Zukünftige Entwicklungswege der technologischen Innovation bei Pressbremsen
Inhaltsverzeichnis
Automatisierungsrevolution: Neugestaltung der Produktionsparadigmen
○ Integrierung intelligenter Produktionslinien
○ Durchbrüche in adaptiven Steuerungssystemen
Digitales Ökosystem: Software-Definierte Fertigung
○ End-to-End Digitale Zwillingstechnologie
○ Tiefgreifende Integration des Industriellen IoT
Grüne Transformation: Nachhaltige Fertigungspraktiken
○ Closed-Loop Energiemanagementsysteme
○ Innovationen im Umweltkonformitätsdesign
Technologische Konvergenz: Ausblick auf Next-Gen-Lösungen
Kern technische Analyse
Automatisierungsrevolution: Neugestaltung der Produktionsparadigmen
Intelligente Produktionslinienintegration
Die moderne Pressbremsautomatisierung ist von Einzelmaschinen-Aufwertungen zu vollständiger Linienkooperation gewachsen. Durch die Integration von sechsachsigen kollaborativen Robotern, AGV-Materialflusssystemen und intelligenten Lagermodulen erreichen Hersteller unbesetzte Operationen vom Rohstoffladen bis zur Fertigprodukt-Sortierung. Solche Systeme steigern die Gesamteffizienz um über 40 %, während visuelle Positionierungstechnologie die Wiederholgenauigkeit des Biegens innerhalb von ±0,05 mm sicherstellt und so qualitative Schwankungen durch manuelle Eingriffe erheblich reduziert.
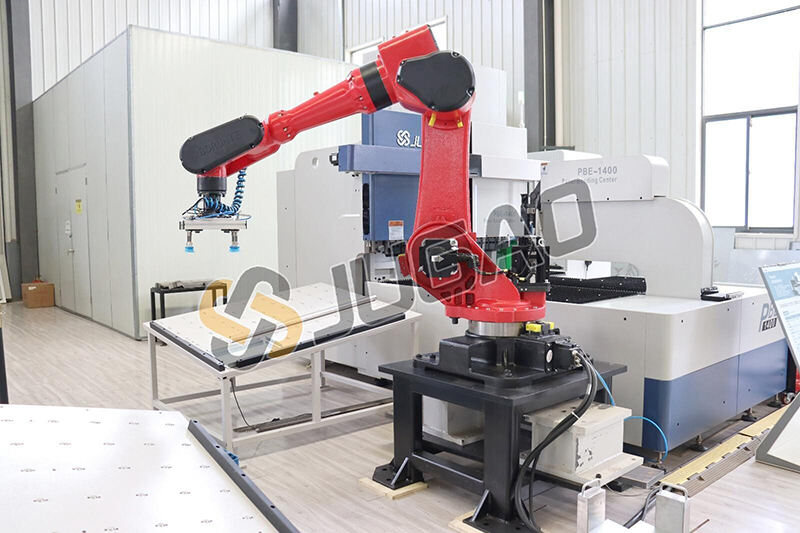
Durchbrüche in adaptiven Steuerungssystemen
Durch deep learning-algorithmen gesteuerte adaptive Steuerungssysteme werden zu Branchenstandards. Durch Echtzeiterfassung von Daten aus Drucksensoren, Lasertiefenmessern und anderen multiquelligen Eingaben optimieren diese Systeme dynamisch Winkelkompensationsalgorithmen. Zum Beispiel, wenn hochfestes Stahl mit erheblichen Rückfedereffekten verarbeitet wird, passt das System die Pressenöffnungen automatisch an, was die Kompensationsgenauigkeit von ±0,3° (traditionelle empirische Werte) auf ±0,1° verbessert. Diese selbstentwicklende Logik ermöglicht es dem Equipment, sich den wachsenden Anforderungen an komplexe Mehr-Material-Verarbeitungen anzupassen.
Digitales Ökosystem: Software-Definierte Fertigung
End-to-End Digital Twin Technologie
Die tiefe Integration von CAD/CAM-Software mit physikalischem Equipment hat zur Entstehung von Digital-Twin-Plattformen geführt. Ingenieure können vollständige Prozessvalidierungen – von der 3D-Modellierung und Prozesssimulation bis hin zur Spannungsanalyse – in virtuellen Umgebungen durchführen und Metallverformungen während des Biegevorgangs genau vorhersagen. Fallstudien zeigen, dass diese Technologie die Anzahl der Probendurchläufe bei einem Automobilzulieferer von 15 Tagen auf 72 Stunden reduzierte, wobei sich der Materialverbrauch um 22 % verringerte.
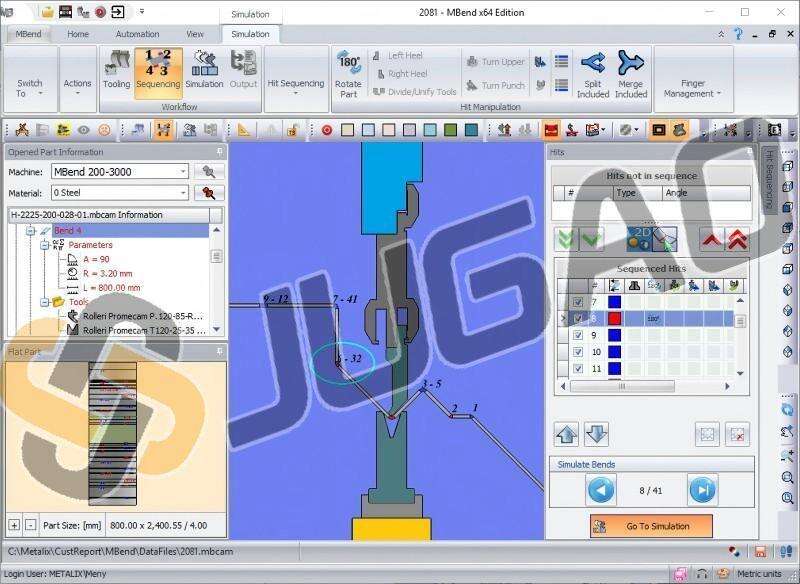
Tiefe Integration des Industrie-IoT
Durch Fernüberwachungssysteme, die von 5G und Edge-Computing-Architekturen unterstützt werden, wird eine Reaktionsfähigkeit auf Millisekundenebene erreicht. Durch den Einsatz von Schwingungsanalysesensoren und Überwachungsmodulen für die Hydraulikoilqualität kann das Equipment kritische Bauteilkomponentenversagen (z. B. Servomotorschwellenlager) 14 Tage im Voraus vorhersagen. Zudem erfüllen blockchainbasierte Prozessdaten-Zertifizierungssysteme die strengen Nachvollziehbarkeitsanforderungen in der Luftfahrtfertigung.
Grüne Transformation: Nachhaltige Fertigungspraktiken
Geschlossene Energie-Managementsysteme
Nächste-Generation elektrische Servo Pressbremsen verwenden bidirektionale Inverter-Technologie, um Bremsenergie zurück ins Netz zu speisen und so den Energieverbrauch um 65 % im Vergleich zu traditionellen hydraulischen Modellen zu reduzieren. Experimentelle Daten zeigen, dass Hybridsysteme mit Supercapazitoren 32 % der Trägheitsenergie während der kontinuierlichen Verarbeitung von 2-mm Edelstahlplatten wiedererhalten, was eine jährliche Kohlenstoffreduzierung von 8,6 Tonnen pro Maschine erreicht.
Innovationen im Umweltkonformitätsdesign
Niedrigschalige hydraulische Systeme, die den ISO 50001 Standards entsprechen, nutzen Variable-Pumpen und Akkumulator-Synergie, um Leerlaufgeräusche von 85 dB(A) auf 72 dB(A) zu senken. Gleichzeitig verringert der Austausch von Mineralöl gegen biobasierte Hydraulikflüssigkeiten VOC-Emissionen um 46 % über die Lebensdauer des Geräts, in Übereinstimmung mit den EU EcoDesign Vorschriften von 2025.
Technologische Konvergenz: Ausblick auf Next-Gen-Lösungen
Elektro-hybride Antriebssysteme durchbrechen traditionelle Grenzen: Hydraulische Systeme ermöglichen eine schnelle Vorfütterung während des Raufliegens, während elektrische Servomodi die Präzision beim Fertigliegen sicherstellen und ein branchenführendes Effizienz-zu-Energie-Verhältnis von 1:0,78 erreichen. Darüber hinaus werden durch quantencomputergetriebene Prozessoptimierungsalgorithmen bis 2025 Kompressionszeiten für komplexe gekrümmte Biegevorgänge auf Minuten reduziert.
Kern technische Analyse
Technische Dimension | Innovativer Wert |
Automatisierung | Ermöglicht 24/7 kontinuierliche Produktion, senkt Personalkosten um 57 % und steigert die GESA (Gesamtausrüstungseffektivität) auf 89 % |
Digitalisierung | Kürzt Produktentwicklungszyklen um 40 %; Prozessdatenbanken erhöhen die Trainings-effizienz für neue Mitarbeiter um 300 % |
Nachhaltigkeit | Senkt den Gesamtenergieverbrauch um 52 %, den Kohlenstofffußabdruck um 38 % und die Konformitätskosten um 65 % |
Fazit
Die Innovationswelle in der Pressbrementechnologie macht Fortschritte entlang dreier Achsen: Intelligenz, Digitalisierung und Nachhaltigkeit. In den nächsten fünf Jahren könnten kognitive Pressbremse mit selbst-diagnosefähigen Funktionen, cloudbasierte kollaborative Produktionsplattformen und auf null-Emissions-Wasserstoff basierende Lösungen die Konkurrenz in den Metallformungsindustrien neu definieren. Für Hersteller ist das Einbinden dieser Trends nicht nur entscheidend für die Steigerung der Wettbewerbsfähigkeit, sondern auch ein wesentlicher Weg zur Transformation in Richtung Industry 4.0.