مسیرهای آینده اولویت گذاری نوآوری فنی در ماشین فرمان
فهرست مطالب
انقلاب خودکارسازی: بازسازی Paradigm تولید
○ یکپارچه سازی خط تولید هوشمند
○ پیشرفت در سیستم های کنترل تطبیقی
اکوسیستم دیجیتال: تولید تعریفشده با نرمافزار
○ فناوری دوبلر دیجیتال از ابتدا تا انتها
○ ادغام عمیق IoT صنعتی
تبدیل سبز: روشهای پایدار تولید
○ سیستمهای مدیریت انرژی حلقه بسته
○ نوآوریها در طراحی مطابقت با محیط زیست
همگرایی فناورانه: بیننده برای راهکارهای نسل بعدی
تحلیل فنی اصلی
انقلاب خودکارسازی: بازسازی Paradigm تولید
ادغام خط تولید هوشمند
اتوماسیون فشاربر نوین از بهبود ماشینهای تکی به همکاری خط کامل تکامل یافته است. با ادغام رباتهای همکار ششمحور، سیستمهای حمل و نقل متریال AGV و ماژولهای انبارداری هوشمند، تولیدکنندگان عملیات بدون نظارتی از بارگذاری مواد خام تا مرتبسازی محصول نهایی را دستیاب میسازند. این سیستمها کارایی کلی را بیش از ۴۰٪ بهبود میبخشند، در حالی که فناوری موقعیتیابی تصویر تکرارپذیری خمش را در حد ±۰٫۰۵ میلیمتر تضمین میکند و نوسانات کیفیت ناشی از مداخله دستی را به طور قابل ملاحظه کاهش میدهد.
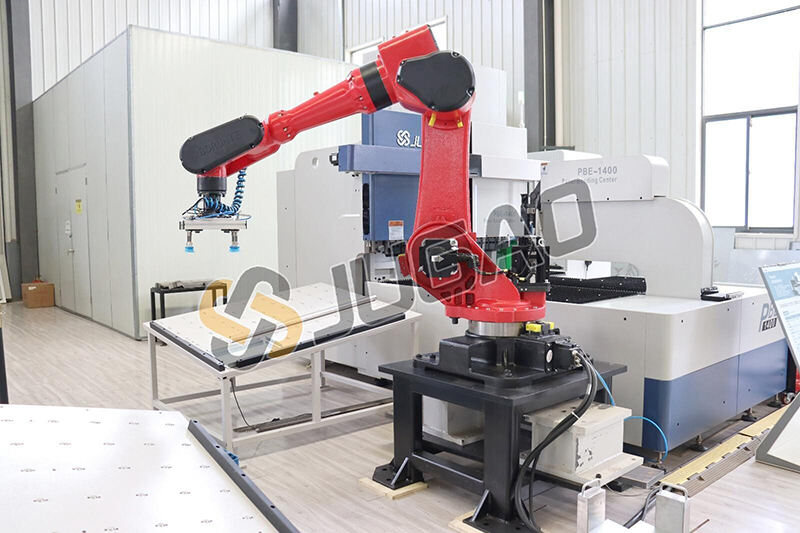
پیشرفتها در سیستمهای کنترل تطبیقی
سیستمهای کنترل تطبیقی محرک توسط الگوریتمهای یادگیری عمیق به نمونههای صنعتی تبدیل شدهاند. با جمعآوری دادههای زمان واقعی از حسگرهای فشار، لیزر رینجفایندرها و ورودیهای چندمنبعه دیگر، این سیستمها الگوریتمهای تعوض زاویه را به طور پویا بهینه میکنند. برای نمونه، هنگام پردازش فولاد مقاوم با اثرات قابل توجه بازگشتی، سیستم به طور خودکار بازشدن قالبها را تنظیم میکند، که دقت تعوض را از ±0.3° (مقادیر تجربی سنتی) به ±0.1° افزایش میدهد. این منطق خودتوسعهای، به تجهیزات اجازه میدهد تا به نیازهای پردازش چندمادهای پیچیدهتر بپاسخ دهد.
اکوسیستم دیجیتال: تولید تعریفشده با نرمافزار
فناوری توأم دیجیتال از ابتدا تا انتها
یکپارچهسازی عمیق نرمافزارهای CAD/CAM با تجهیزات فیزیکی منجر به پلتفرمهای دوقلوی رقمی شده است. مهندسان میتوانند اعتبارسنجی کامل فرآیند—از مدلسازی سه بعدی و شبیهسازی فرآیند تا تحلیل تنش—در محیطهای مجازی انجام دهند و به طور دقیق از تشکیل جابهجایی فلز در فرآیند خمش پیشبینی کنند. مطالعات موردی نشان میدهد که این فناوری دورههای آزمایشی قالبسازی یک تولیدکننده قطعات خودرو را از ۱۵ روز به ۷۲ ساعت کاهش داده است، همراه با کاهش ۲۲٪ در ضایعات مواد.
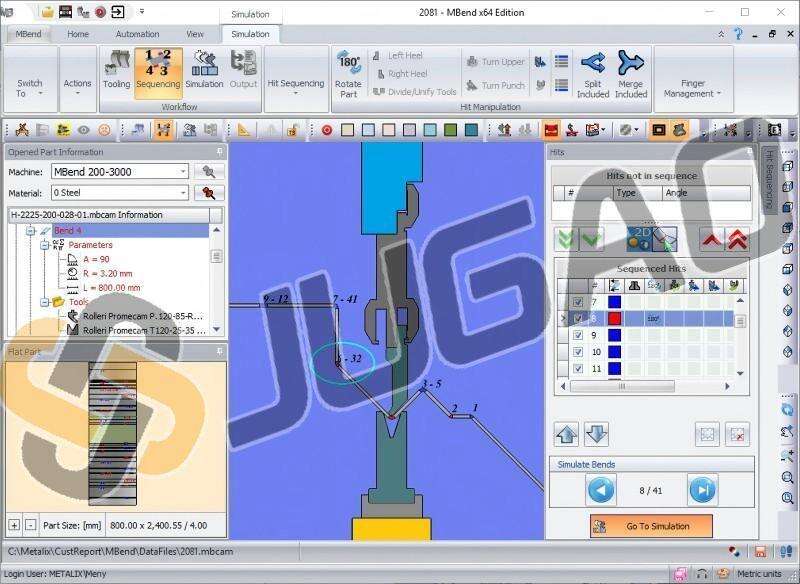
یکپارچهسازی عمقی IoT صنعتی
سیستمهای نظارت از راه دور پشتیبانی شده توسط فناوری ۵G و معماریهای محاسبات لبهای واکنشپذیری سطح میلی ثانیهای را دست میدهند. با نصب حسگرهای تحلیل ارتعاش و ماژولهای نظارت بر وضعیت روغن هیدرولیک، تجهیزات میتوانند شکستهای مؤلفههای بحرانی (مانند برشهای موتورهای سرو) ۱۴ روز قبل پیشبینی کنند. علاوه بر این، سیستمهای گواهی داده فرآیند مبتنی بر بلاکچین نیازهای مشخصه ردپایی در تولید فضایی را پوشش میدهند.
تبدیل سبز: روشهای پایدار تولید
سیستمهای مدیریت انرژی حلقه بسته
ماشینهای فرمان الکتریکی نسل بعدی از تکنولوژی وارونگی دوطرفه برای بازگرداندن انرژی ترمز به شبکه استفاده میکنند، که مصرف انرژی را نسبت به مدلهای هیدرولیک سنتی به میزان 65٪ کاهش میدهد. دادههای آزمایشی نشان میدهند که سیستمهای ترکیبی با سوپرکاپاسیتورها در طی پردازش مداوم صفحات فولادی ریز 2 میلیمتری، 32٪ از انرژیเฉانهای را بازیابی میکنند و کاهش کربن سالانه 8.6 تن در هر ماشین را دستیابی میکند.
نوآوریها در طراحی مطابقت زیستمحیطی
سیستمهای هیدرولیک کمصدا مطابق با استانداردهای ISO 50001 از همکاری پمپهای متغیر و اکومیولاژر برای کاهش صدای خاموشبودن از 85dB(A) به 72dB(A) استفاده میکنند. در حالی که جایگزینی روغن معدنی با مایعات هیدرولیک مبتنیبر زیست محصولات، گازهای آلودهکننده عضوی (VOC) را طی دوره عمر تجهیزات به میزان 46٪ کاهش میدهد، که با مقررات طراحی زیستمحیطی اتحادیه اروپا تا سال 2025 هماهنگ است.
همگرایی فناورانه: بیننده برای راهکارهای نسل بعدی
سیستمهای محرک الکترو-هیدرولیک ترکیبی مرزهای سنتی را شکستهاند: سیستمهای هیدرولیکی اجازه تغذیه سریع در حین خامکاری را میدهند، در حالی که حالتهای سرو الکتریکی دقت نهایی را در فرآیند پایانی تضمین میکنند و به نسبت کارایی به انرژی صنعتی رهبری با 1:0.78 دست مییابند. علاوه بر این، الگوریتمهای بهینهسازی فرآیند مبتنی بر محاسبات کوانتومی برای کاهش زمان برنامهریزی برای خمهای منحنی پیچیده تا دقیقهها در سال 2025 پیشبینی شده است.
تحلیل فنی اصلی
بعد فنی | ارزش نوآورانه |
اتوماسیون | فعال سازی تولید پیوسته 24/7، کاهش هزینههای نیروی کار به میزان 57٪ و افزایش OEE (کارایی کل تجهیزات) به 89٪ |
رقمیسازی | کوتاه کردن چرخه توسعه محصولات تا 40٪؛ پایگاه دادههای فرآیندی کارایی آموزش کارمندان جدید را تا 300٪ افزایش میدهد |
پایداری | کاهش مصرف کلی انرژی تا 52٪، اثر کربنی تا 38٪ و هزینههای رعایت قوانین تا 65٪ |
نتیجهگیری
موج نوآوری در فناوری ماشین تراش قاب قرار گرفتن در حال پیشرفت بر سه محور است: هوشمندی، دیجیتال شدن و پایداری. در پنج سال آینده، ماشینهای تراش هوشمند با توانایی تشخیص خودکار،-platform های ابری برای تولید مشارکتی و راهحلهای تغذیه شده از هیدروژن صفر کربن ممکن است رقابت در صنایع شکلدهی فلز را بازتعریف کنند. برای تولیدکنندگان، پذیرش این روندها تنها کلیدی برای افزایش رقابتپذیری است بلکه همچنین راهی ضروری برای تبدیل به صنعت 4.0 نیز محسوب میشود.