چگونه دقت خمش ماشین خمش را افزایش دهیم
دقت خم شدن برای تولید قطعات فلزی با کیفیت بالا حیاتی است تا ابعاد قطعات با مشخصات طراحی سازگار باشند. در صنایعی مانند هوافضا یا تولید دستگاه پزشکی، تحملات محکم به این معناست که حتی انحرافات کوچک میتوانند مشکلاتی را ایجاد کنند.
دقت خم شدن بر روی منافع اقتصادی تأثیر میگذارد. خم شدن نادرست منجر به ضایعات مواد میشود، باعث کار مجدد گرانبرد و تاخیر میگردد، زمان تولید و هزینههای نیروی کار را افزایش میدهد و رضایت مشتری را کاهش میدهد. دقت کم میتواند سلیقه سازه را ضعیف کرده یا جمع آوری را اشتباه تنظیم کند، که منجر به ادعای گارانتی و آسیب به اعتبار میشود.
نگهداری از دقت ثابت در خمش ضروری است در عملکرد ماشین خمش فلز. خمش دقیق منابع را بهینه می کند، زباله را کاهش می دهد و سودآوری را افزایش می دهد، بنابراین تولیدکنندگان باید فرآیندهای خود را کامل کنند.
خطاهایی که منجر به شکست دقت خمش ماشین خمش فلز می شوند دلایل مختلفی دارند، شامل مشکلات مکانیکی ماشین خمش فلز و عوامل خارجی مانند ابزارهای خمش، ضخامت مواد و خطاهای انسانی عملگر.
در این مقاله، ما به بررسی عوامل مختلفی خواهیم پرداخت که بر دقت خمش تأثیر می گذارند و راه حل ها برای برخی از موقعیت های متداولی که مواجه می شویم ارائه خواهیم داد.
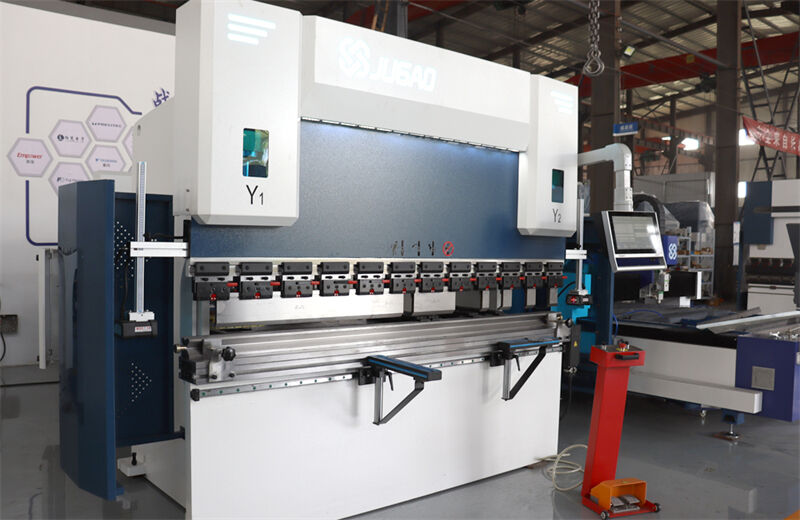
1. عوامل مربوط به ماشین
چندین عامل وجود دارد که بر دقت خمش ماشین خمش فلز تأثیر می گذارند. این عوامل شامل
خط راستی گشوده شدن اسلایدر
گشوده شدن فشرده ساز اسلایدر در هر دو جهت Y و X خط راست است. دقت مجدد قرار گرفتن و دقت موقعیت دلخواه اسلایدرهای چپ و راست است. دقت گشوده شدن اسلایدر در جهات Y و X برای دقت خم شدگی حیاتی است. اگر گشوده شدن اسلایدر خط راست نباشد، این موضوع انحراف در زاویه و موقعیت خم شدگی ایجاد خواهد کرد.
فاصله بین اسلایدر و ردیف چارچوب
فاصله منطقی بین پیستون ماشین خم شدگی و راهنمای خطی چارچوب باید مناسب باشد. فاصله مناسب بین اسلایدر و ردیف چارچوب، ثبات اسلایدر را طی حرکت تضمین می کند و در نتیجه دقت خم شدگی ماشین خم شدگی را بهبود می بخشد.
عمودی بودن و شیب چارچوب
عمودی بودن و شیب قاب. عمودی بودن و شیب قاب تأثیری بر توزیع نیروی خمش در طول فرآیند خمش دارد، که این موضوع دقت خمش محصول نهایی را تضمین میکند.
دادههای آزمایشگاهی (مانند نمایش زیر) نشان میدهند که یک شیب 0.1° در قاب در جهت محور Y باعث کاهش 5% یکنواختی نیروی خمش میشود، که منجر به انحراف حداکثر 0.5° در زاویه خمش میشود. این موضوع به دلیل نامساوی نیرو روی سیلندر اسلایدر است که باعث شیفت در توزیع نیروی خمش میشود.
زاویه شیب قاب (در جهت محور Y) | نیروی خمش به طور مساوی توزیع شده است | انحراف زاویه خمش |
0° | 99.50% | <0.1° |
0.05° | 97.20% | 0.2°- 0.3° |
0.1° | 94.80% | 0.3°- 0.5° |
اتصال بین استوانه و اسلاید
برای تضمین توزیع منظم نیروی خمش در طول خمش در ماشین فرمان، اتصال بین استوانه و اسلاید باید سازگار باشد.
دقت مکانیکی
کالیبرسازی دقیق اسلایدها، مهرهها، هیدرولیکی و پشتسنج ضروری است. کالیبرسازی منظم تضمین میکند که این مولفهها در حدود تحمل مشخص شده کار کنند.
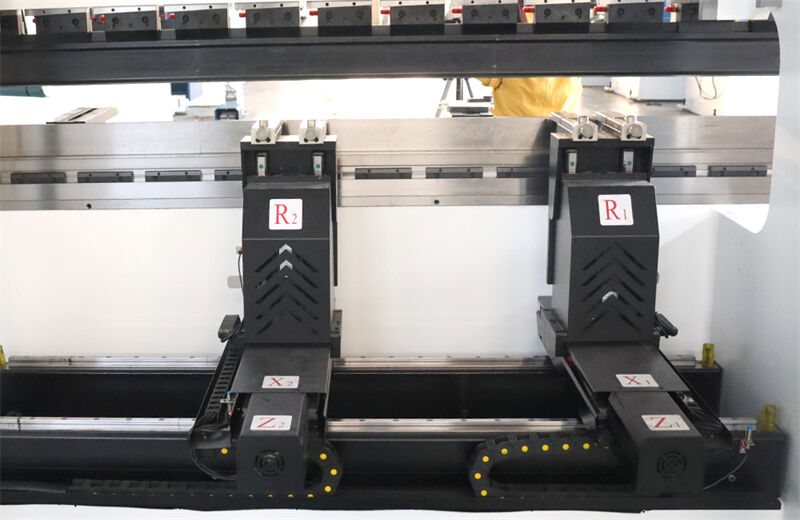
عوامل دیگری نیز وجود دارند که بر روی خمش دقیق فرمانها تأثیر میگذارند، مانند قدرت و دقت چارچوب و اسلاید، دقت مجدد قرار گرفتن سیستم پشتسنج در هر دو جهت X و R، تنظیم صحیح سیستم کامپیوتری، تنظیم سیستم هیدرولیکی و هماهنگی بین سیستم هیدرولیکی و تنظیم کامپیوتری.
2. عوامل ابزار
الف... دقت ماتریسهای بالا و پایین:
دقت ماتریسهای بالا و پایین حیاتی است. تغییر شکل، آسیب، سوزنده شدن و مشکلات دیگر ماتریس بر تمام جنبههای خمش فلز تأثیر میگذارد. هنگامی که این مشکلات شناسایی میشوند، باید به صورت زمانی گزارش داده شوند و اصلاح شوند. بنابراین، بررسی و نگهداری منظم ضروری است.
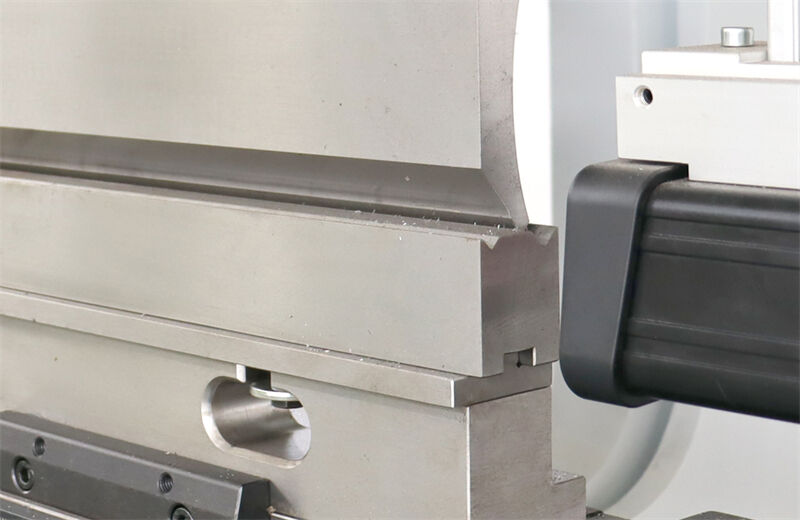
ب... همآرایی ماتریس:
عدم همآرایی بین ماتریسهای بالا و پایین منجر به انحراف در اندازه خمش میشود. باید مطمئن شوید که ابزار به درستی همآرا شده است هنگامی که ابزار را تنظیم میکنید.
پس از جابجایی موقعیت چپ و راست کلید پشتی، فاصله بین ماتریس پایین و کلید پشتی تغییر خواهد کرد. این میتواند با استفاده از خطکش Vernier اندازهگیری و با استفاده از مهره کلید پشتی تنظیم شود.
دقت و سازگاری دستگاه جبران ماتریس پایین باید با طراحی قاب هماهنگ باشد. فیکسچر ماتریس بالا باید به شدت دقیق باشد.
c. اندازه باز شدن ماتریس V:
اندازه باز شدن ماتریس V نسبت معکوسی با فشار خمش دارد. وقتی طول و ضخامت برگ ثابت است، هر چه باز شدن بیشتر باشد، فشار مورد نیاز کمتر است. بنابراین، هنگام پردازش برگهای با ضخامتهای مختلف، باید از اندازه مناسب باز شدن ماتریس V استفاده کرد.
هنگام پردازش با بار یکطرفه، مانند در انتهای ماشین خمش، فشار خمش ممکن است تحت تأثیر قرار گیرد که ممکن است ماشین را آسیب برساند. این کار به شدت ممنوع است. هنگام مونتاژ ماتریس، باید همیشه قسمت مرکزی ماشین تحت فشار قرار گیرد.
انتخاب ابزار:
انتخاب عرض مناسب دی و پروفایل چکش بر اساس ماده و شعاع خمیدگی بسیار حیاتی است. در صنعت شکلدهی و تولید فلزی، استفاده از دیهای نادرست میتواند منجر به انحراف زاویهها و عیوب رویه شود.
انتخاب ابزارهای خم شدن و دیها یک فرآیند دقیق است که نیازمند درک عمیق از همچنین تجهیزات و مواد پردازش شده است.
3. عوامل بلاد فلزی
باید سطح مرجع بلاد فلزی بررسی شود. اطمینان حاصل کنید که بلاد فلزی تحت فشار یکنواخت قرار گرفته است. ضخامت یکسان بلاد فلزی را بررسی کنید.
در طی فرآیند خمش، اگر موازی بودن قطعه کاری با ماتریس پایین ناکافی باشد، این موضوع منجر به بازگشت قطعه کاری پس از فشار دادن مهره بالا خواهد شد که سبب تأثیر بر اندازه خمش میشود.
بازگشت، پدیدهای است که در آن ماده سعی میکند پس از خمش به شکل اصلی خود بازگردد. مقاومت کششی، ضخامت، ابزار و نوع ماشین خمش همه بر بازگشت تأثیر میگذارند. پیشبینی و ارزیابی موثر بازگشت برای مدیریت خمهای تنگ و مصالح ضخیم با مقاومت بالا ضروری است.
ویژگیهای ماده و ضخامت آن بر زاویه خمش تأثیر میگذارد، بنابراین باید هر قطعه کاری قبل از خمش به صورت مناسب بررسی و چک شود.
زیرا ویژگیهای دقیق ماده به شرح زیر است:
مقاومت تسلیم: مقاومت تسلیم، بیشترین استرسی است که ماده میتواند قبل از آنکه شروع به تغییر شکل دائمی کند، تحمل کند. دانستن مقاومت تسلیم کمک میکند تا بیشترین نیروی قابل اعمال در فرآیند خمش تعیین شود تا ماده آسیب نبیند.
مدول الاستیسیته: مدول الاستیسیته نشاندهنده سختی ماده است و مقدار تغییر شکل تحت استرس معین را تعیین میکند. دانستن مدول الاستیسیته کمک میکند تا مقدار بازگشت پس از خمش پیشبینی شود.
ضخامت مواد: ضخامت ماده تأثیر زیادی بر فرآیند خمش دارد. مواد ضخیمتر نیاز به نیروی بیشتری برای خمش دارند و نیاز به شعاع خمش بزرگتری دارند تا جلوی شکست یا تغییر شکل قرار دهند.
چالاکی: چالاکی به توانایی ماده در تجربه تغییر شکل پلاستیکی بدون شکستن اشاره دارد. مواد با چالاکی بالا راحتتر خمش میشوند و احتمال شکست یا جدایی در فرآیند خمش کمتر است.
حالت سطح: حالت سطح فلزی (شامل پوشش یا تیمار) بر روی اثر خم شدن تأثیر خواهد گذاشت. تمیز کردن کامل برای حذف ناخالصیها همچنین کلید جلوگیری از عیوب است.
4. عوامل عملیات خم شدن
الف. هماهنگی اعمال عملگر:
بررسی کنید که آیا نیروهای چپ و راست زمانی که عملگر ماشین خم شدن ماده را برای خم شدن به حرکت میگذارد یکسان است یا خیر. عدم هماهنگی در نیروی خم شدن انحرافاتی در اندازه خم شدن ایجاد خواهد کرد.
ب. تنظیم دادههای سیستم:
هنگام استفاده از سیستم، مطمئن شوید که خطای دادههای سیستم را به درستی تنظیم کردهاید. زاویه کم بودن در یکباره تأثیر خواهد گذاشت بر اندازه خمش دوم. خطاهاي تجمعی خمش، خطای اندازه محيط قطعه را افزایش خواهد داد.
فشار مورد نیاز برای خمش با طول و ضخامت قطعه کار تغییر میکند و طول و ضخامت صفحه نسبت مستقیم با فشار مورد نیاز دارد.
هنگامی که طول و ضخامت قطعه کار تغییر میکند، مهم است که ظرفیت خمش را به طور مناسب تنظیم کنید.
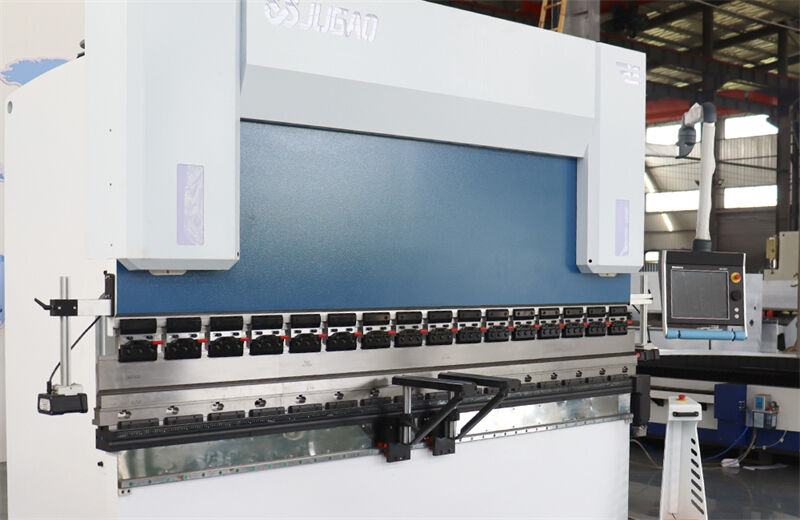
5. عوامل محیطی
به غیر از تجهیزات، قالبها و پارامترهای فرآیند، عوامل محیطی نیز تأثیری معین بر دقت خمش خواهند گذاشت. در میان آنها، تأثیر دما و رطوبت بیشترین اهمیت را دارد.
دمای
تغییرات دمایی بر خواص مواد مانند مقاومت تسلیم و مدول الاستیسیته تأثیر خواهد گذاشت. افزایش دما منجر به کاهش مقاومت تسلیم و مدول الاستیسیته و افزایش بازگشت فنری خواهد شد. دمای نامنظم علت گسترش حرارتی و در نتیجه، تغییر شکل قطعه کار خواهد شد. برای دستیابی به خمش دقیق، دماي کارگاه باید ثابت نگه داشته شود یا طبق تغییرات تنظیم شود.
رطوبت
رطوبت بر روی سطح ماده تأثیر خواهد گذاشت. در محیطی با رطوبت بالا، فلز رطوبت جذب خواهد کرد، صدف زنی خواهد شد و این موضوع اصطکاک و دقت خمش را تحت تأثیر قرار خواهد داد. این موضوع برای موادی که نیازمند معیارهای کیفیت سطحی بالا هستند مانند آلیاژهای آلویوم و فولاد راستنیس بسیار حساس است.
6. روشهای دستیابی به دقت خمش بالا
برای دستیابی به دقت بالا در عملیات خمش فشاری، لازم است تجهیزات پیشرفته، ابزار دقیق، مدیریت مناسب مواد و پارامترهای فرآیند بهینه را ترکیب کنید. هر عنصر نقش مهمی در تضمین اینکه خمشها دقیق، مطابق و برگونه طراحی باشند، ایفا میکند.
الف. از ماشین خمش با دقت بالا استفاده کنید
ماشینهای خمش مدرن با سیستمهای کنترل پیشرفته مانند فناوری CNC (کنترل عددی کامپیوتری) مجهز شدهاند که با کاهش خطای انسانی و خودکارسازی محاسبات پیچیده، دقت عالی در خمش را به دست میآورند. ویژگیهایی مانند سیستمهای اندازهگیری زاویه در حالت واقعی و تنظیم خودکار زاویه بالا، انحرافات موجود در قالب یا قطعه کار را جبران میکنند و عملکرد ثابت خمش را تضمین میکنند.
ماشینهای خمش هیدرولیک و الکتریک به ویژه ویژگیهایی دارند که دقت را افزایش میدهد، شامل موقعیتگذاری قابل برنامهریزی لغزش و کنترل سرعت. این ویژگیها امکان تنظیم دقیق عملیات را فراهم میکند تا خمش دقیق روی چندین قطعه تضمین شود. علاوه بر این، ماشینهای مجهز به موتورهای سرو-الکتریک میتوانند تکرارپذیری عالی ارائه دهند به دلیل کنترل دقیق حرکت لغزش.
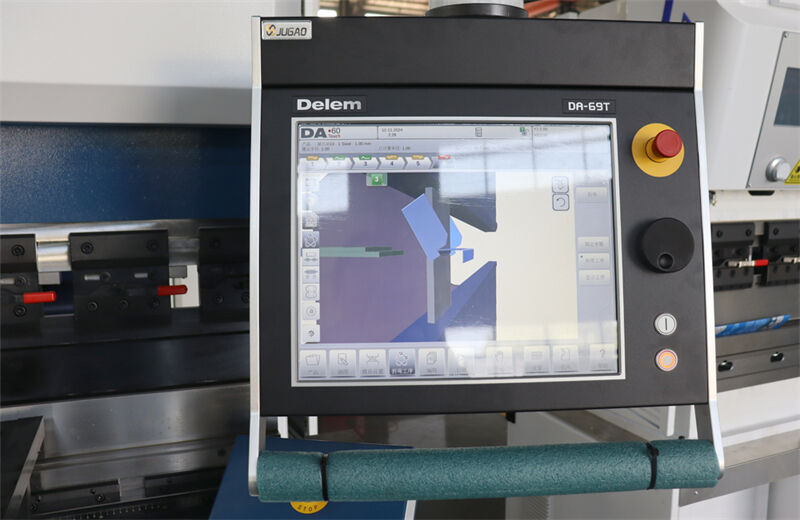
ب. انتخاب و نگهداری ابزار
انتخاب و وضعیت ابزارهای ماشین خمش مستقیماً بر کیفیت خمش تأثیر میگذارد. نظرات کلیدی عبارتند از
هندسه ابزار: انتخاب صفحات و ضربهزنهایی با شعاع و زاویه مناسب با نوع مواد، توزیع نیروی بهینه را در طول فرآیند خمش تضمین میکند. استفاده از صفحات نادرست میتواند منجر به تغییر شکل غیرمنتظره یا زوایا نادرست شود.
کیفیت ماده: مواد ابزار مقاوم با قدرت بالا، مانند فولاد ابزار سخت شده، ضد سرپوشی هستند و عملکرد پایداری در بلندمدت حفظ میکنند.
نگهداری مداوم: اطمینان حاصل کردن از اینکه سطوح ابزار از آسیب، استفاده بیش از حد یا آلودگی خالی باشند، اشتباهات را در طول فرآیند خم شدن جلوگیری میکند. بررسی منظم ابزارها حتی برای عیوب کوچک و جایگزینی قسمتهای استفادهشده برای نگهداری از دقت در بلندمدت ضروری است.
ج. تهیه دقیق مواد
یکنواختی تغذیه تأثیر زیادی بر نتیجه خم شدن دارد. نامنظم بودن ها مثل ضخامت نامساوی مواد، نقصهای سطحی یا ویژگیهای مکانیکی ناسازگار میتوانند تغییراتی در زاویه خمیده مورد نظر ایجاد کنند. برای تضمین ثبات
ضخامت و سختی مواد را قبل از خم شدن تأیید کنید. اگر ضخامت نامساوی باشد یا سختی بیش از حد باشد، فرآیند باید تنظیم شود.
سطح فلزی را پاک کرده و از آلودگیهایی که ممکن است باعث اختلال در ابزار یا عدم ثبات شوند، خالی کنید.
استاندارد کردن دستههای ماده به منظور کاهش تغییرپذیری و ترویج رفتار قابل پیشبینی در خم شدن.
د. جبران بازگشت ماده
بازگشت، یعنی میل فلز به بازگشت بخشی از شکل اصلی خود پس از خم شدن، یک چالش متداول در دستیابی به دقت زاویهای دقیق است. تدابیر برای مقابله با بازگشت شامل موارد زیر است:
خم شدن بیش از حد: خم شدن نامتعادل طی عملیات به منظور در نظر گرفتن بازیابی الاستیک.
خم شدن پایین یا سکهزنی: در این روشها، نیروی کافی به قطعه کاری اعمال میشود تا آن را فراتر از حد الاستیک تغییر شکل دهد، بنابراین بازگشت کاهش مییابد.
تنظیمات برای مواد خاص: فلزات مختلف ویژگیهای بازگشت پیچیده متفاوتی دارند. ماشینهای فشاری پیشرفته مجهز به کتابخانه مصالح، میتوانند زاویه جبران مناسب را بر اساس مateriaل انتخابی به طور خودکار محاسبه کنند.
ه. اجرای گاوهای دقیق
گاوهای عقب، بخشهای مهمی برای کنترل موقعیت قطعه کار هستند، به ویژه در تولید انبوه که ثبات حیاتی است. گاوهای عقب با دقت بالا، معمولاً توسط سیستمهای CNC کنترل میشوند و کمک میکنند:
محاذا قطعه کار با صفحه و ضربه با دقت.
قرار دادن مداوم مواد طی خمشهای تکراری.
در عملیات خم شدن چند مرحله ای، تنظیمات سریع برای هندسههای مختلف قطعه کار امکانپذیر است.
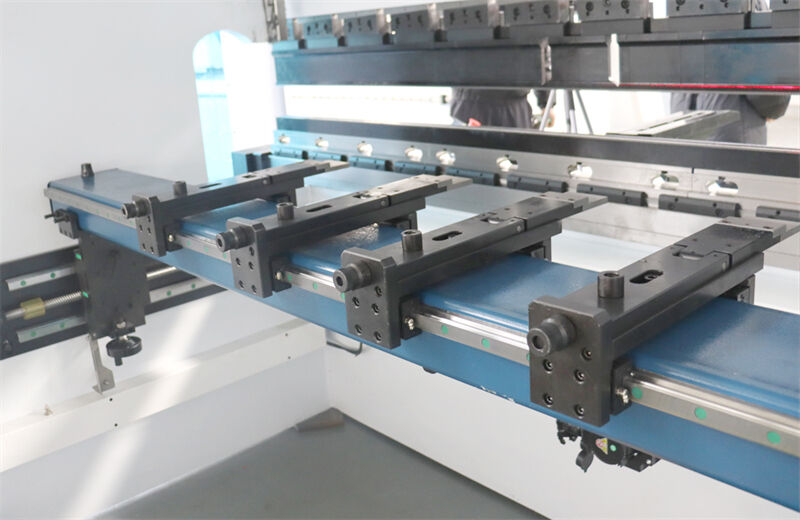
ف. بهینهسازی پیکربندی فرآیند
تنظیم صحیح پارامترهای فرآیند برای دستیابی به خمهای دقیق بسیار حیاتی است. عوامل کلیدی که باید در نظر گرفته شوند شامل
نیروی خم شدن: تنظیم تنبندی بر اساس نوع ماده، ضخامت و ویژگیهای ابزار برای تضمین اعمال نیروی ثابت ضروری است.
سرعت خم شدن: برای مواد ضخیمتر یا مقاومتر، سرعتهای خم شدن کندتر برای حفظ دقت مناسبتر است، در حالی که سرعتهای بالاتر ممکن است ناسازگاریها ایجاد کنند.
برنامهریزی توالی: قطعات پیچیده با چندین خم نیاز به یک توالی دقیق دارند تا در هر مرحله از جانبداری و حفظ هماهنگی جلوگیری شود.
ج. آموزش عملیاتی و توسعه مهارت
حتی با تجهیزات پیشرفته، تخصص عملیاتی نقش کلیدی در دستیابی به دقت بالای خمش دارد. عملیاتی که آموزش منظم میبینند بهتر میتوانند
منابع پتانسیل نادرستی را شناسایی کنند، مانند ابزارهای غیرهمخط یا تنظیمات نادرست مواد.
تنظیمات فشار برکه را بر اساس انحرافات مشاهدهشده به طور دینامیکی تنظیم کنند.
ثبات در روال بررسیها طی تولید و پس از آن را حفظ کنید تا کیفیت قطعات را تأیید کنید.
سرمایهگذاری در آموزش مداوم عملکرد اپراتوران، به ویژه در زمینه چگونگی مقابله با فناوریهای جدید و چالشها، نیروی کار متخصصی را تضمین میکند که میتواند استانداردهای دقیق خمش را حفظ کند.
ه. کنترل کیفیت و نظارت
اندازهگیریهای قوی کنترل کیفیت در طول فرآیند خمش، کشف و اصلاح خطاهای اولیه را تسهیل میکند. این اندازهگیریها شامل
کنترل فرآیند آماری (SPC): تحلیل دادههای تولید بلندمدت برای شناسایی الگوها و انحرافات، کمک میکند تا فرآیندها بهینه شوند و منابع ناسازگاری حذف شوند.
سیستم اندازهگیری زاویه اینترنتی: ابزارهای نظارت در حین انجام کار که بر روی دستگاه خمش نصب میشوند، تضمین میکنند که زاویه خمش به زاویه مشخص شده برسد قبل از آزاد سازی قطعه کاری.
بررسی ابعاد: از ابزارهای دقیق مانند فاصلسنجها، ماشینهای اندازهگیری مختصات یا سیستمهای اندازهگیری لیزری برای تأیید ابعاد و زوایا استفاده کنید.
7. پرسشهای متداول
الف. چقدر باید از یک ماشین خمش فشاری برای دقت بهینه نگهداری شود؟
دقت ماشین خمش فشاری خود را با برنامهریزی نگهداری سیستماتیک حفظ کنید.
روزانه: تمیز کردن و بررسی قطعات آسونده یا повیرده.
هفتگی: روغن کردن و بررسی فیلترها برای جلوگیری از رشح.
ماهانه: تمیز کردن مولفههای هیدرولیکی و بررسی فیلتر هوا.
پس از اولین ۲,۰۰۰ ساعت، روغن هیدرولیک را هر ۴,۰۰۰ تا ۶,۰۰۰ ساعت جایگزین کنید. همه سیستمها را هر شش ماه تا یک سال یکبار بررسی کنید. کالیبراسیون منظم دقت خمش را تضمین میکند. این روال مانع از تعویق در کار و طول عمر ماشین را افزایش میدهد.
ب. مشکلات متداولی که دقت فشاربر نیروی خمش را تحت تأثیر قرار میدهد چیست؟
مشکلات دقت فشاربر ناهمگونی مواد، ابزارهای سرخ شده، هممرکزی نادرست، کالیبراسیون نامناسب، خطاها در ماشین، عدم دقت در باکگیج و روشهای غیرمناسب پیچش است.
این مشکلات را با تضمین خواص یکسان مواد، نگهداری ابزارها، انجام کالیبراسیون ماشین، استفاده از باکگیج CNC و انتخاب روشهای مناسب پیچش حل کنید. تنظیمات واقعی-زمانی در سیستم CNC را انجام دهید و برنامهریزی مناسبی برای کاهش رخداد مشکلات انجام دهید.
c. چه سطح تحمل ایدهآلی برای دقت پیچش فشاربر وجود دارد؟
سطح تحمل فشاربر بستگی به کاربرد و الزامات صنعتی دارد. به طور کلی، برای اکثر پروژههای دقیق، انحراف زاویهای ±0.5° و انحراف ابعادی ±0.1 میلیمتر قابل قبول است. در تولید دستگاههای هوافضا یا پزشکی، تحملات معمولاً محکمتر هستند و کمتر از ±0.25°.
برای دستیابی به این اهداف، نیاز به سیستمهای CNC پیشرفته، ابزار دقیق و تضمین کیفیت است. تولیدکنندگان باید مشخصات، خواص مواد و محدودیتها را ارزیابی کرده و تحملات مناسب را تعیین کنند.
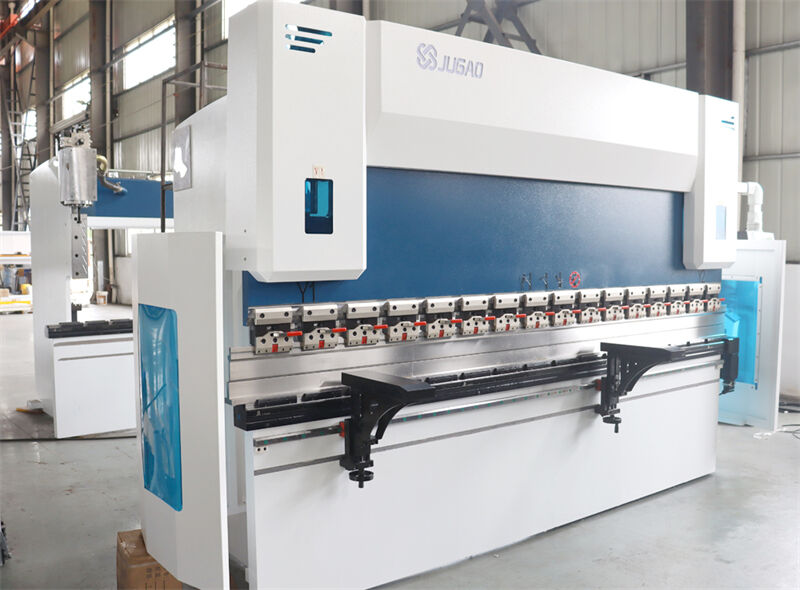
برای بهبود دقت انحنای یک فشاربر، باید به بسیاری از عوامل توجه کرد. علاوه بر تنظیم قطعات فشاربر، تضمین دقت و تکرارپذیری قالب و انجام جبران انحنا به درستی، باید به نگهداری روزانه و مراقبت از فشاربر نیز توجه کرد.
این کار به طول عمر آن کمک میکند و انحناهای کارآمد و دقیق را حفظ میکند. چهار فناوری انحنا برای انحناهای فلز بلند وجود دارد: انحنا هوایی، انحنا پایین، انحنا سکهای و انحنا سه نقطهای.
سرمایهگذاری در یک فشاربر کیفیت بالا راه دیگری مؤثر برای تضمین عملیات خم شدن تولیدی موثر در صنعت ساخت فلز است. JUGAO CNC MACHINE یک تولیدکننده مورد اعتماد ماشین خم شدن با بیش از دو دهه تجربه در صنعت فلز صفحه ای است.
علاوه بر ماشینهای خم شدن مدرن مانند ماشینهای خم شدن هیدرولیک و ماشینهای خم شدن CNC، ما نیز دیگر ماشینها مانند ماشینهای برش لیزر، ماشینهای خم شدن صفحه، ماشینهای خم شدن لوله و بیشتر آنها را پیشنهاد میکنیم.
جهت دریافت اطلاعات بیشتر، لطفاً به صفحه محصولات ماشین خم شدن مراجعه کنید یا برای اطلاعات دقیق محصول و قیمت، به صفحه تماس با ما مراجعه کنید.