Caminhos Futuros de Evolução da Inovação Tecnológica em Freios de Prensa
Sumário
Automation Revolution: Redefinindo Paradigmas de Produção
○ Integração da Linha de Produção Inteligente
○ Avanços nos Sistemas de Controle Adaptativo
Ecossistema Digital: Manufatura Definida por Software
○ Tecnologia de Gêmeo Digital de Extremidade a Extremidade
○ Integração Profunda do IoT Industrial
Transformação Verde: Práticas Sustentáveis de Manufatura
○ Sistemas de Gestão de Energia em Loop Fechado
○ Inovações no Design de Conformidade Ambiental
Convergência Tecnológica: Perspectiva para Soluções de Próxima Geração
Análise Técnica Central
Automation Revolution: Redefinindo Paradigmas de Produção
Integração da Linha de Produção Inteligente
A automação moderna de freios de prensa evoluiu das atualizações de máquinas individuais para uma colaboração em toda a linha. Ao integrar robôs colaborativos de seis eixos, sistemas de manuseio de materiais AGV e módulos de armazenamento inteligente, os fabricantes conseguem operações não tripuladas desde o carregamento de matérias-primas até a classificação do produto final. Esses sistemas aumentam a eficiência geral em mais de 40%, enquanto a tecnologia de posicionamento por visão garante repetibilidade no dobra dentro de ±0,05mm, reduzindo significativamente as flutuações de qualidade causadas pela intervenção manual.
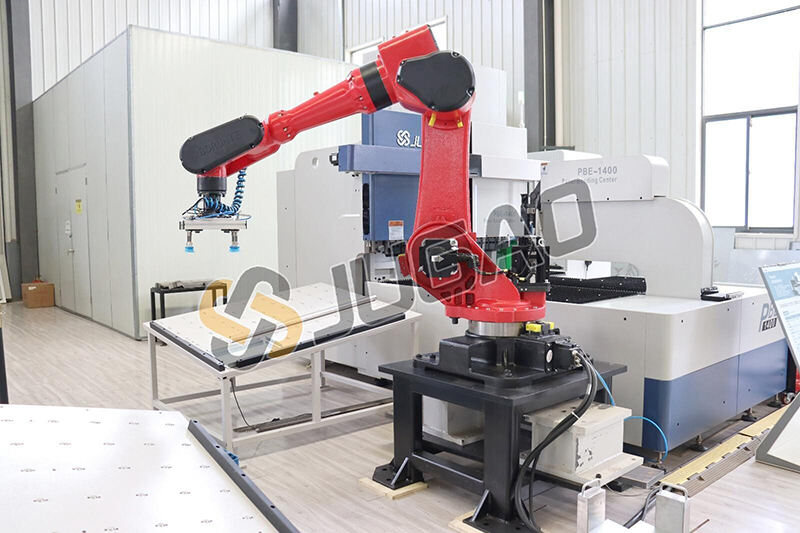
Avanços nos Sistemas de Controle Adaptativo
Sistemas de controle adaptativo impulsionados por algoritmos de aprendizado profundo estão se tornando referências no setor. Por meio da aquisição de dados em tempo real de sensores de pressão, medidores a laser e outras entradas multisource, esses sistemas otimizam dinamicamente algoritmos de compensação de ângulo. Por exemplo, ao processar aço de alta resistência com efeitos significativos de ressurgimento, o sistema ajusta automaticamente as aberturas dos moldes, melhorando a precisão de compensação de ±0,3° (valores empíricos tradicionais) para ±0,1°. Essa lógica auto-evolutiva permite que o equipamento se adapte a demandas cada vez mais complexas de processamento multimatéria.
Ecossistema Digital: Manufatura Definida por Software
Tecnologia de Gêmeo Digital de Ponta a Ponta
A integração profunda de softwares CAD/CAM com equipamentos físicos deu origem a plataformas de gêmeos digitais. Engenheiros podem realizar validações de processo completas — desde modelagem 3D e simulação de processos até análise de tensão — em ambientes virtuais, prevendo com precisão a deformação de chapas metálicas durante o dobramento. Estudos de caso mostram que essa tecnologia reduziu os ciclos de moldagem experimental de um fabricante de peças automotivas de 15 dias para 72 horas, com uma redução de 22% no desperdício de material.
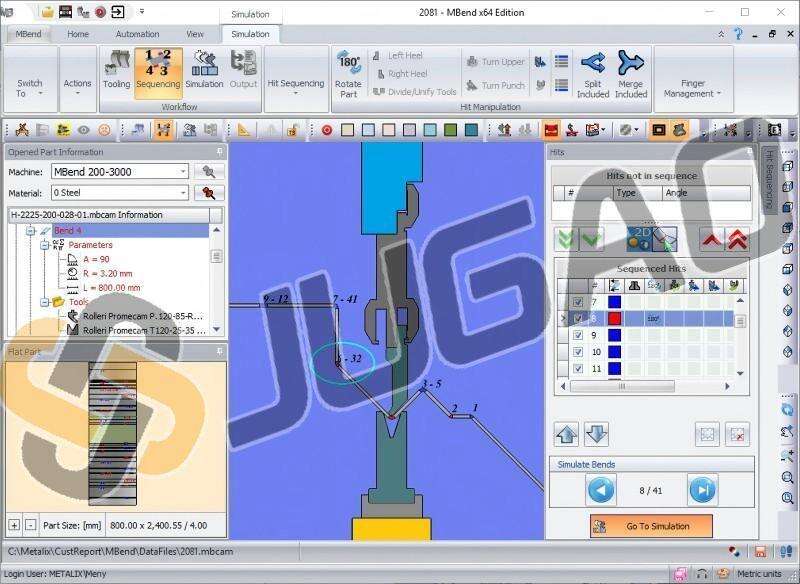
Integração Profunda do IoT Industrial
Sistemas de monitoramento remoto suportados por arquiteturas 5G e computação na borda alcançam resposta em nível de milissegundos. Ao implantar sensores de análise de vibração e módulos de monitoramento da condição do óleo hidráulico, o equipamento pode prever falhas de componentes críticos (por exemplo, rolamentos de motores de servos) com 14 dias de antecedência. Além disso, sistemas de certificação de dados de processo baseados em blockchain estão atendendo aos rigorosos requisitos de rastreabilidade na fabricação aeroespacial.
Transformação Verde: Práticas Sustentáveis de Manufatura
Sistemas de Gestão de Energia em Loop Fechado
Freadores elétricos de servo com tecnologia de inversor bidirecional devolvem a energia de frenagem para a rede, reduzindo o consumo de energia em 65% em comparação com modelos hidráulicos tradicionais. Dados experimentais indicam que sistemas híbridos com supercapacitores recuperam 32% da energia inercial durante o processamento contínuo de chapas de aço inoxidável de 2mm, alcançando uma redução anual de carbono de 8,6 toneladas por máquina.
Inovações no Design de Conformidade Ambiental
Sistemas hidráulicos de baixo ruído compatíveis com os padrões ISO 50001 utilizam sinergia de bombas variáveis e acumuladores para reduzir o ruído em standby de 85dB(A) para 72dB(A). Enquanto isso, substituir óleo mineral por fluidos hidráulicos à base de biomassa reduz as emissões de VOC em 46% ao longo do ciclo de vida do equipamento, alinhando-se às regulamentações EU EcoDesign 2025.
Convergência Tecnológica: Perspectiva para Soluções de Próxima Geração
Sistemas de direção eletro-hidráulicos híbridos estão quebrando limites tradicionais: sistemas hidráulicos permitem alimentação rápida durante o esboço, enquanto modos elétricos de servo garantem precisão no acabamento, alcançando uma relação de eficiência-energia líder na indústria de 1:0,78. Além disso, algoritmos de otimização de processos impulsionados por computação quântica devem reduzir o tempo de programação para dobras curvas complexas a minutos até 2025.
Análise Técnica Central
Dimensão Técnica | Valor Inovador |
Automação | Permite produção contínua 24/7, reduz os custos de mão-de-obra em 57% e aumenta a OEE (Eficiência Global do Equipamento) para 89% |
Digitalização | Reduz ciclos de desenvolvimento de produtos em 40%; bancos de dados de processos aumentam a eficiência no treinamento de novos funcionários em 300% |
Sustentabilidade | Reduz o consumo total de energia em 52%, a pegada de carbono em 38% e os custos de conformidade em 65% |
Conclusão
A onda de inovação na tecnologia de freios de prensa está avançando ao longo de três eixos: inteligência, digitalização e sustentabilidade. Nos próximos cinco anos, freios de prensa cognitivos com capacidades de autodiagnóstico, plataformas colaborativas baseadas em nuvem e soluções movidas a hidrogênio de carbono zero podem redefinir a competição nas indústrias de formação de metais. Para os fabricantes, abraçar essas tendências é não apenas crucial para aumentar a competitividade, mas também um caminho essencial rumo à transformação da Indústria 4.0.