Análise Abrangente do Ciclo de Vida e Substituição de Freios de Prensa
Índice
Fatores Principais que Afetam a Longevidade do Freio de Prensa
1. Design e Qualidade de Fabricação
2. Frequência de Uso
3. Gestão de Manutenção Regular
4. Adaptabilidade do Ambiente Operacional
Sinais Chave para Substituição
1. Aumento dos Custos de Manutenção
2. Obsolescência Tecnológica
3. Declínio Contínuo no Desempenho
Perguntas Frequentes
P1: Qual é a vida útil média de um freio de prensa?
P2: Como aumentar a vida útil?
P3: Quando um freio de prensa deve ser substituído?
Conclusão e recomendações
Como equipamento central na fabricação de chapas metálicas, a vida útil e a estratégia de substituição dos freios de prensa impactam diretamente os custos de produção e a eficiência. Este artigo analisa sistematicamente os fatores que influenciam a vida útil do equipamento, o momento da substituição e as estratégias de otimização, capacitando as empresas a implementarem uma gestão de ciclo de vida científica.
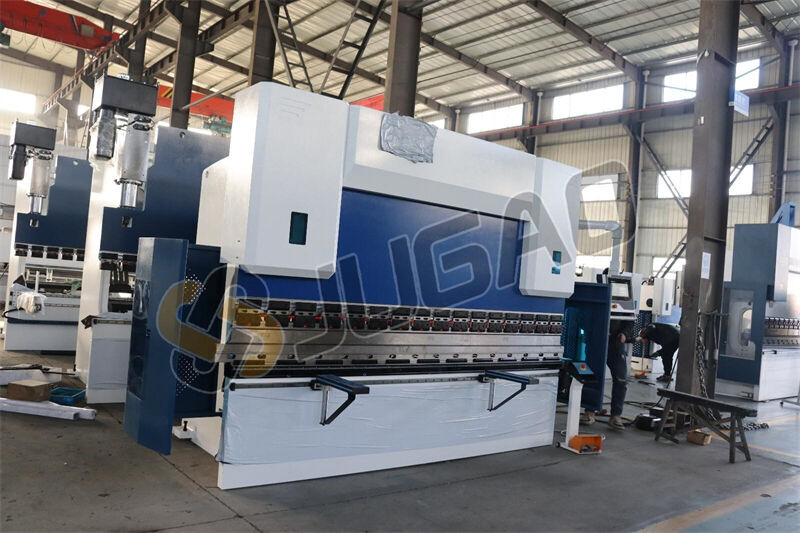
Fatores Principais que Afetam a Longevidade do Freio de Prensa
1. Design e Qualidade de Fabricação
A base da longevidade dos equipamentos está nos processos de design e fabricação:
Materiais e Artesanato: Molduras fundidas de alta precisão e trilhos guias endurecidos melhoram significativamente a resistência à fadiga.
Configuração Técnica: Tecnologias avançadas como motores de servomecanismo e sistemas de controle em malha fechada reduzem o desgaste a longo prazo.
Seleção de Marca: Priorize fabricantes certificados ISO para garantir confiabilidade.
Estudo de Caso: Uma prensa freadora de aço com moldura totalmente soldada manteve 90% de precisão após 12 anos de uso contínuo, enquanto um modelo de baixa qualidade exigiu reparos maiores no oitavo ano sob condições idênticas.
2. Frequência de Uso
A intensidade de uso e o tempo de vida útil exibem uma relação não linear:
Cenários de Uso Leve (<4 horas/dia): O tempo de vida teórico excede 20 anos.
Produção Intensa (operação 24/7): Componentes principais devem ser avaliados a cada 10-15 anos.
Pontos Críticos de Desgaste: Foque em selos hidráulicos, guias de pistão e contatos elétricos.
Referência de Dados: Uma fábrica de peças automotivas relatou que equipamentos processando mais de 500.000 ciclos anualmente experimentaram três vezes mais a taxa de falha do sistema hidráulico em comparação com condições padrão.
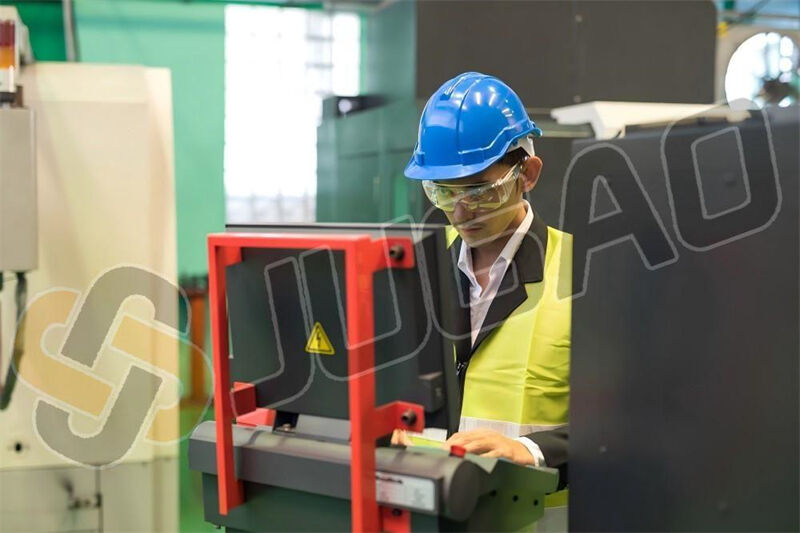
3. Gestão de Manutenção Regular
A manutenção científica aumenta o tempo de vida útil em 30%-50%:
Manutenção Diária: Limpar os detritos da guia; verificar os níveis de óleo hidráulico semanalmente.
Serviços Trimestrais: Calibrar a precisão do retorno traseiro; inspecionar a estabilidade da escala de grade.
Revisão Anual: Substituir filtros de óleo hidráulico; testar a diferença de torque do sistema de sincronização.
Ponto Cego na Manutenção: Empresas que dependem exclusivamente de reparos pós-falha atingem<60% de eficácia geral="" do="" equipamento="", enquanto="" programas="" de="" manutenção="" preventiva="" geram="">85%.
4. Adaptabilidade do Ambiente Operacional
Os impactos ambientais são frequentemente subestimados:
Controle de Temperatura/Umidade: Condições ideais: 10-35°C, umidade<70%.
Prevenção contra Poeira: Instale cortinas de ar de pressão positiva para reduzir a contaminação do armário elétrico.
Estabilidade da Fundação: Use plataformas com amortecedores de vibração em ambientes de alta vibração para evitar a deformação da estrutura.
Caso Extremo: Uma instalação costeira sem tratamento anti-salitre experimentou uma corrosão severa nos circuitos impressos dentro de 3 anos.
Sinais Chave para Substituição
1. Aumento dos Custos de Manutenção
Inicie a análise de custo-benefício se os custos anuais de reparo excederem 30% do valor residual ou se os custos de um único reparo maior ultrapassarem 15% do preço de equipamento novo.
Modelo de Decisão:
Limite de Substituição = (Custo Anual de Manutenção + Perdas por Parada) / Custo Anual de Depreciação de Equipamento Novo > 1.2
2. Obsolescência Tecnológica
Equipamentos antigos enfrentam três desafios:
Gap de Precisão: Modelos mecânicos tradicionais com parada: repetibilidade ±0,1mm vs. modelos CNC: ±0,02mm.
Baixa Eficiência Energética: Novos freios de chapa servo reduzem o consumo de energia em 40%-60%.
Gaps de Funcionalidade: Recursos inteligentes (ex., simulação 3D, troca automática de ferramentas) são inatingíveis por meio de retrofit.
Recomendação de Atualização: Priorize o retrofit CNC para modelos hidráulicos com mais de 10 anos.
3. Declínio Contínuo no Desempenho
Inclua essas métricas nas avaliações de saúde do equipamento:
Desvio do Ângulo de Dobragem: Excede a tolerância em 2x por três meses consecutivos.
Atraso na Resposta Hidráulica: >0,5 segundos do comando até o movimento do êmbolo.
Erro de Sincronização: Desvio do eixo Y1/Y2 >0,05mm.
Ferramentas de Diagnóstico: Use analisadores de vibração e câmeras térmicas para inspeções aprofundadas.
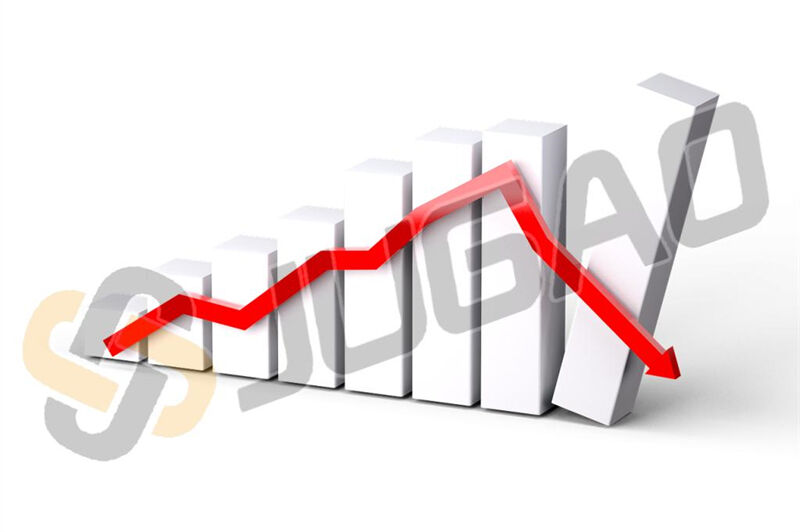
Perguntas Frequentes
P1: Qual é a vida útil média de um freio de prensa?
Sob uso e manutenção padronizados:
Modelos Econômicos: 8-12 anos
Modelos CNC de Médio Alcance: 12-18 anos
Modelos de Servo de Alta Gama: 15-25 anos
P2: Como aumentar a vida útil?
Implemente uma estratégia de manutenção em três níveis:
1. Nível do Operador: Verificação de lubrificação antes do turno; limpeza do espaço de trabalho após o turno.
2. Nível do Técnico: Testes mensais da curva de pressão hidráulica e da resistência elétrica.
3. Nível Especialista: Análise anual de tensão do quadro e atualizações de firmware CNC.
P3: Quando um freio de prensa deve ser substituído?
Iniciar avaliação de substituição se:
Componentes críticos (por exemplo, cilindros principais) são descontinuados sem alternativas.
A eficiência de processamento cai 30% abaixo dos benchmarks da indústria.
Os sistemas de segurança não atendem aos mais recentes padrões CE/OSHA.
Conclusão e recomendações
A gestão do ciclo de vida de freios de prensa requer um sistema de avaliação quantificado:
1. Manter Registros de Equipamentos: Registrar histórico de manutenção, códigos de falha e retrofit.
2. Adotar Monitoramento IoT: Rastreamento em tempo real de pressão, temperatura e vibração.
3. Desenvolver Planos Rotativos de 5 Anos: Alinhar prazos de substituição com planejamento de capacidade e tendências tecnológicas.
Guia de Ação: Inspeções anuais de terceiros para gerar Relatórios de Saúde do Equipamento para decisões baseadas em dados.