Percorsi di Evoluzione Futura dell'Innovazione Tecnologica delle Frese
Indice
Automation Revolution: Ricostruzione dei Paradigmi di Produzione
○ Integrazione della Linea di Produzione Intelligente
○ Progressi nei Sistemi di Controllo Adattivo
Ecosistema Digitale: Manifattura Definita da Software
○ Tecnologia di Gemello Digitale End-to-End
○ Integrazione Profonda dell'Internet delle Cose Industriale
Trasformazione Verde: Pratiche di Produzione Sostenibili
○ Sistemi di Gestione Energetica a Ciclo Chiuso
○ Innovazioni nel Design di Conformità Ambientale
Convergenza Tecnologica: Prospettive per Soluzioni di Nuova Generazione
Analisi Tecnica Fondamentale
Automation Revolution: Ricostruzione dei Paradigmi di Produzione
Integrazione della Linea di Produzione Intelligente
L'automazione delle stampiature a freddo moderne è evoluta dall'aggiornamento di singole macchine alla collaborazione su tutta la linea. Integrando robot collaborativi a sei assi, sistemi di gestione dei materiali AGV e moduli di magazzino intelligente, i produttori raggiungono operazioni completely senza intervento umano, dal caricamento del materiale grezzo fino alla classificazione del prodotto finito. Tali sistemi migliorano l'efficienza complessiva del 40% circa, mentre la tecnologia di posizionamento visivo garantisce una ripetibilità del piegamento entro ±0,05mm, riducendo notevolmente le variazioni di qualità causate dall'intervento manuale.
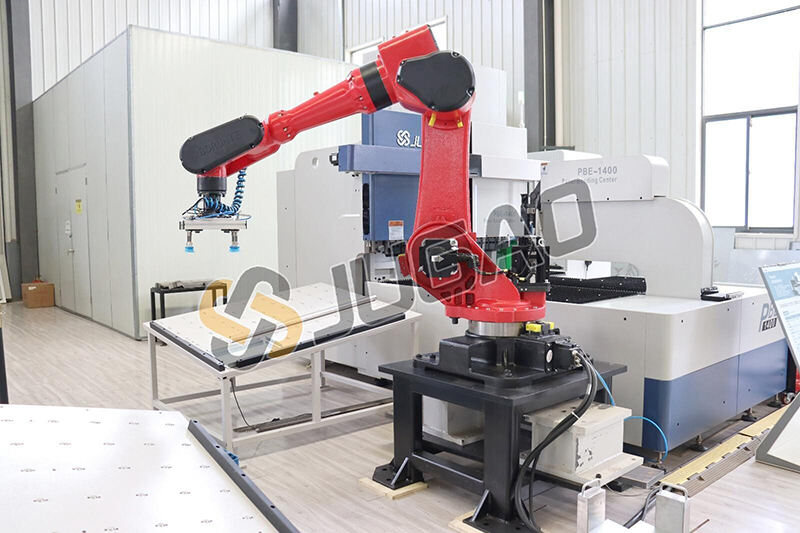
Progressi nei Sistemi di Controllo Adattivo
I sistemi di controllo adattivo guidati da algoritmi di deep learning stanno diventando benchmark dell'industria. Attraverso l'acquisizione di dati in tempo reale da sensori di pressione, rilevatori laser e altre fonti multimediali, questi sistemi ottimizzano dinamicamente gli algoritmi di compensazione angolare. Per esempio, quando si lavora con acciai ad alta resistenza che presentano effetti di respringsignificativi, il sistema regola automaticamente le aperture dei morsetti, migliorando la precisione della compensazione da ±0.3° (valori empirici tradizionali) a ±0.1°. Questa logica autoevolutiva consente alle attrezzature di adattarsi sempre più complesse richieste di lavorazione di materiali multipli.
Ecosistema Digitale: Manifattura Definita da Software
Tecnologia Digital Twin End-to-End
L'integrazione profonda del software CAD/CAM con l'attrezzatura fisica ha dato origine a piattaforme di gemelli digitali. Gli ingegneri possono completare validazioni di tutto il processo—dalla modellazione 3D e la simulazione del processo all'analisi dello stress—in ambienti virtuali, prevedendo in modo accurato la deformazione del metallo durante il piegamento. Studi di caso mostrano che questa tecnologia ha ridotto i cicli di prova per un produttore di componenti automobilistici da 15 giorni a 72 ore, con una riduzione del 22% dei rifiuti di materiale.
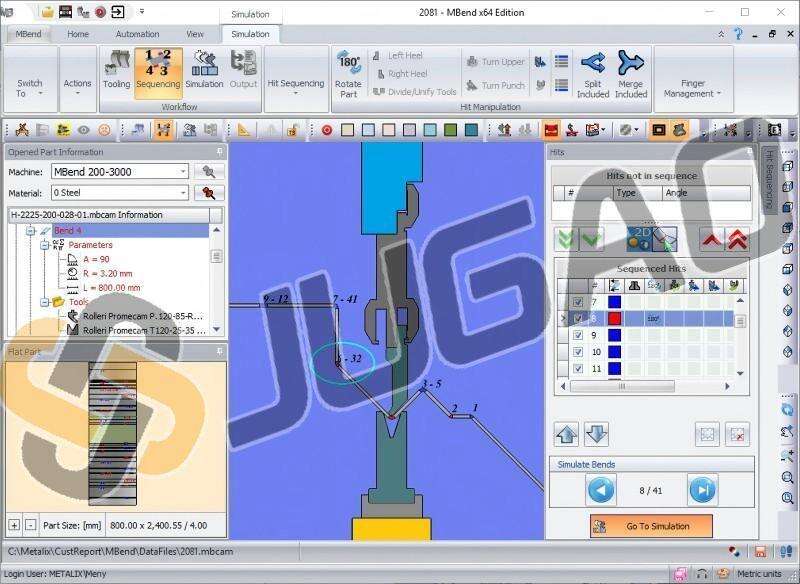
Integrazione Profonda dell'IoT Industriale
I sistemi di monitoraggio remoto supportati da architetture 5G e di calcolo sul bordo raggiungono tempi di risposta a livello di millisecondi. Dipingendo sensori di analisi delle vibrazioni e moduli di monitoraggio della condizione dell'olio idraulico, l'attrezzatura può prevedere guasti di componenti critici (ad esempio, i cuscinetti dei motori a servocomando) fino a 14 giorni prima. Inoltre, i sistemi di certificazione dei dati del processo basati su blockchain stanno soddisfacendo i requisiti rigorosi di tracciabilità nella produzione aerospaziale.
Trasformazione Verde: Pratiche di Produzione Sostenibili
Sistemi di Gestione dell'Energia in Ciclo Chiuso
Le presse a servocomando elettriche di ultima generazione utilizzano la tecnologia di inverter bidirezionale per restituire l'energia dei freni alla rete, riducendo il consumo di energia del 65% rispetto ai modelli idraulici tradizionali. I dati sperimentali indicano che i sistemi ibridi con supercondensatori recuperano il 32% dell'energia inerziale durante l'elaborazione continua di lastre di acciaio inossidabile spesse 2mm, raggiungendo una riduzione annua di carbonio di 8,6 tonnellate per macchina.
Innovazioni nel Design di Conformità Ambientale
I sistemi idraulici a basso rumore conformi agli standard ISO 50001 utilizzano la sinergia tra pompe variabili e accumulatori per ridurre il rumore inattivo da 85dB(A) a 72dB(A). Nello stesso tempo, sostituendo l'olio minerale con fluidi idraulici a base biologica si riducono le emissioni di VOC del 46% durante il ciclo di vita dell'attrezzatura, allineandosi alle normative EU EcoDesign del 2025.
Convergenza Tecnologica: Prospettive per Soluzioni di Nuova Generazione
I sistemi ibridi elettro-idraulici stanno superando i limiti tradizionali: i sistemi idraulici consentono un'alta velocità di avanzamento durante l'abbattimento grezzo, mentre le modalità servo-elettriche garantiscono precisione nel finitura, raggiungendo un rapporto di efficienza-energia leader nel settore di 1:0.78. Inoltre, gli algoritmi di ottimizzazione dei processi basati sul calcolo quantistico sono destinati a ridurre il tempo di programmazione per piegature curve complesse a pochi minuti entro il 2025.
Analisi Tecnica Fondamentale
Dimensione Tecnica | Valore Innovativo |
Automatizzazione | Consente una produzione continua 24/7, riduce i costi del lavoro del 57% e aumenta l'OEE (Overall Equipment Effectiveness) al 89% |
Digitalizzazione | Riduce i cicli di sviluppo prodotto del 40%; le basi di dati dei processi migliorano l'efficienza dell'addestramento dei nuovi dipendenti del 300% |
Sostenibilità | Riduce il consumo totale di energia del 52%, l'impronta di carbonio del 38% e i costi di conformità del 65% |
Conclusione
L'onda di innovazione nella tecnologia delle frese per metalli sta avanzando lungo tre assi: intelligenza, digitalizzazione e sostenibilità. Negli próssimi cinque anni, frese cognitive con capacità di auto-diagnosi, piattaforme collaborative basate sul cloud e soluzioni a idrogeno ad anidride carbonica zero potrebbero ridisegnare la competizione nelle industrie della lavorazione dei metalli. Per i produttori, abbracciare queste tendenze è non solo fondamentale per migliorare la competitività, ma anche un percorso essenziale verso la trasformazione dell'Industria 4.0.