Analisi Completa della Durata di Vita e del Ciclo di Sostituzione del Piegatrice
Sommario
Fattori Principali che Influenzano la Durata di Vita della Pressa Frezza
1. Progettazione e Qualità della Costruzione
2. Frequenza d'Uso
3. Gestione della Manutenzione Regolare
4. Adattabilità dell'Ambiente Operativo
Segnali Chiave per il Sostituzione
1. Aumento dei Costi di Manutenzione
2. Obsolescenza Tecnologica
3. Declino Continuo delle Prestazioni
Domande frequenti
Q1: Qual è la durata media di una pressa freno?
Q2: Come si può estendere la durata?
Q3: Quando dovrebbe essere sostituita una pressa freno?
Conclusione e Raccomandazioni
Come attrezzatura principale nella lavorazione dei metalli a freddo, la durata e la strategia di sostituzione delle presse freno influenzano direttamente i costi di produzione ed l'efficienza. Questo articolo analizza sistematicamente i fattori che influiscono sulla durata dell'attrezzatura, sul momento della sostituzione e sulle strategie di ottimizzazione, consentendo alle imprese di implementare una gestione del ciclo di vita scientifica.
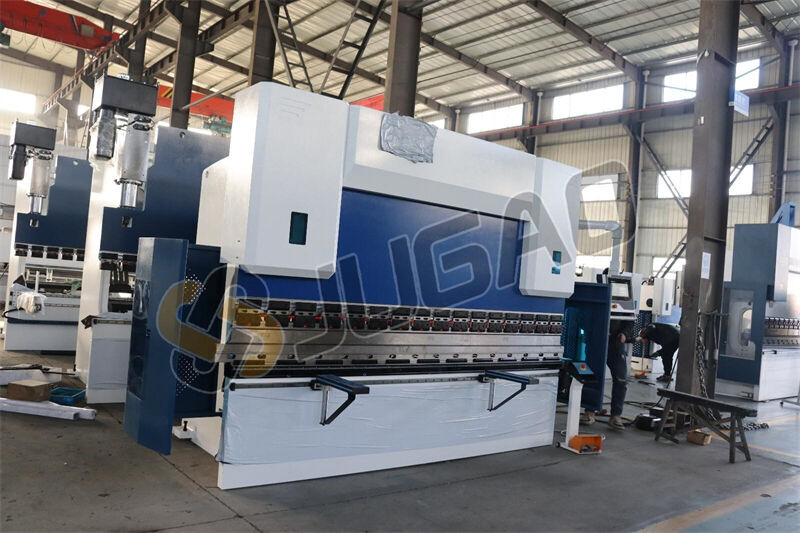
Fattori Principali che Influenzano la Durata di Vita della Pressa Frezza
1. Progettazione e Qualità della Costruzione
La base della longevità degli equipaggiamenti risiede nei processi di progettazione e produzione:
Materiali e Artigianalità: Cornici in ghisa ad alta precisione e guide rafforzate aumentano significativamente la resistenza alla fatica.
Configurazione Tecnica: Tecnologie avanzate come motori a servocomando e sistemi di controllo a ciclo chiuso riducono l'usura a lungo termine.
Selezione del Marchio: Dà priorità ai produttori certificati ISO per garantire affidabilità.
Studio di caso: Una pressa frenatrice con telaio in acciaio completamente saldato ha mantenuto il 90% dell'esattezza dopo 12 anni di uso continuo, mentre un modello di bassa gamma ha richiesto riparazioni maggiori entro l'ottavo anno sotto le stesse condizioni.
2. Frequenza d'Uso
L'intensità d'uso e la durata presentano una relazione non lineare:
Casi di Utilizzo Leggero (<4 ore/giorno): La durata teorica supera i 20 anni.
Produzione Intensa (operazione 24/7): I componenti principali dovrebbero essere valutati ogni 10-15 anni.
Punti Critici di Usura: Concentrarsi sui sigilli idraulici, sulle guide del pistone e sui contatti elettrici.
Riferimento Dati: Un'officina per componenti automobilistici ha riferito che l'attrezzatura che elabora più di 500.000 cicli all'anno presenta un tasso di guasto del sistema idraulico triplo rispetto alle condizioni standard.
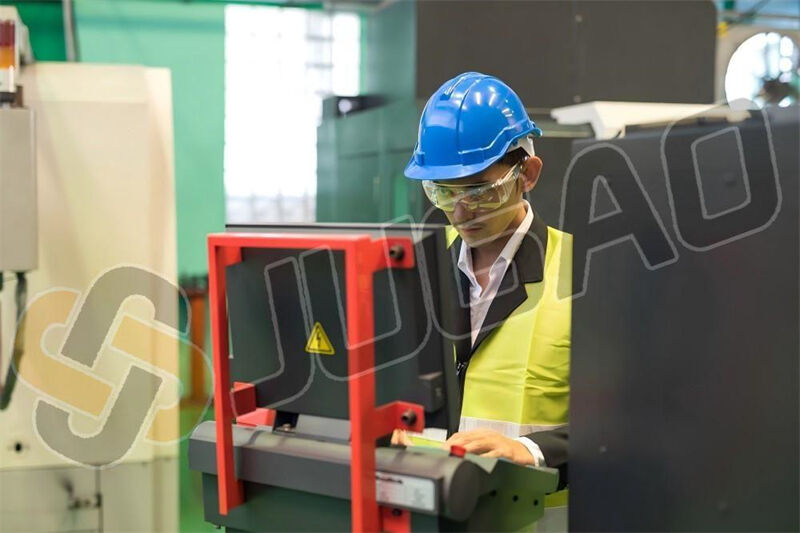
3. Gestione della Manutenzione Regolare
La manutenzione scientifica estende la durata del 30%-50%:
Manutenzione quotidiana: Pulire i residui dalla guida; controllare i livelli dell'olio idraulico settimanalmente.
Revisione trimestrale: Calibrare l'accuratezza del rilevatore posteriore; ispezionare la stabilità della scala a griglia.
Riparazione annuale: Sostituire i filtri dell'olio idraulico; testare la deviazione di coppia del sistema di sincronizzazione.
Fossa di manutenzione: Le aziende che si affidano esclusivamente alle riparazioni post-fallimento raggiungono<60% di efficacia complessiva="" delle="" attrezzature="",="" mentre="" i="" programmi="" di="" manutenzione="" preventiva="" producono="">85%.
4. Adattabilità dell'Ambiente Operativo
Gli impatti ambientali vengono spesso sottovalutati:
Controllo della temperatura/umidità: Condizioni ideali: 10-35°C, umidità<70%.
Prevenzione della Polvere: Installare tende aeree a pressione positiva per ridurre la contaminazione degli armadi elettrici.
Stabilità della Fondazione: Utilizzare piattaforme antivibrazione in ambienti ad alta vibrazione per prevenire la deformazione del telaio.
Caso Estremo: Un impianto costiero senza trattamento antispruzzo salino ha subito una grave corrosione delle schede elettroniche entro 3 anni.
Segnali Chiave per il Sostituzione
1. Aumento dei Costi di Manutenzione
Avvia l'analisi costo-beneficio se i costi di riparazione annuali superano il 30% del valore residuo o i costi di un singolo riparto maggiore superano il 15% del prezzo di un nuovo macchinario.
Modello Decisionale:
Soglia di Sostituzione = (Costo di Manutenzione Annua + Perdite per Downtime) / Costo di Deprezzamento Annuo del Nuovo Macchinario > 1.2
2. Obsolescenza Tecnologica
Gli impianti ereditari si confrontano con tre sfide:
Gap di Precisione: Modelli meccanici tradizionali a fermata: ripetibilità ±0.1mm vs. modelli CNC: ±0.02mm.
Bassa Efficienza Energetica: Le nuove presse a freddo servo riducono il consumo di energia del 40%-60%.
Lacune di Funzionalità: Le funzioni intelligenti (ad esempio, simulazione 3D, cambio automatico degli strumenti) non sono raggiungibili tramite retrofit.
Consiglio di Aggiornamento: Dedicare priorità al retrofit CNC per modelli idraulici con più di 10 anni di età.
3. Declino Continuo delle Prestazioni
Includere queste metriche nelle valutazioni della salute dell'attrezzatura:
Deviazione dell'Angolo di Flessione: Supera la tolleranza per 2 volte per tre mesi consecutivi.
Ritardo di Risposta Idraulica: >0,5 secondi dal comando al movimento del pistone.
Errore di Sincronizzazione: deviazione asse Y1/Y2 >0,05mm.
Strumenti di Diagnosi: Usare analizzatori di vibrazione e camere termiche per ispezioni approfondite.
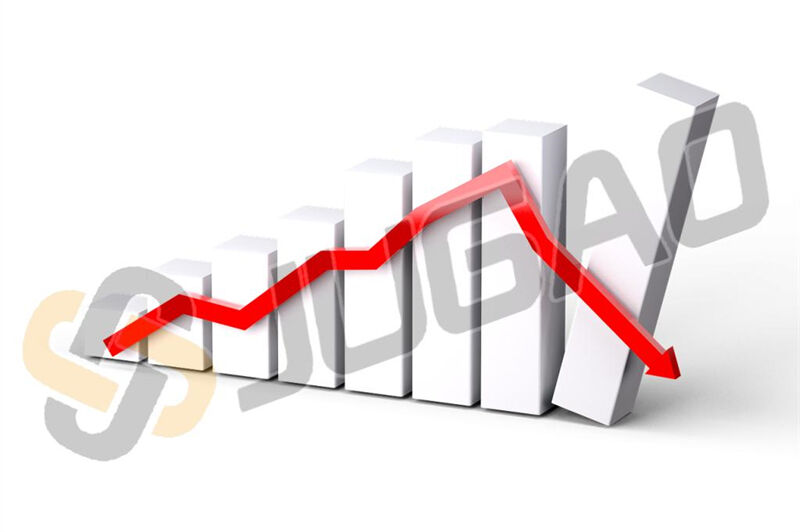
Domande frequenti
Q1: Qual è la durata media di una pressa freno?
Sotto utilizzo e manutenzione standardizzati:
Modelli Economici: 8-12 anni
Modelli CNC di gamma media: 12-18 anni
Modelli a Servo di alta gamma: 15-25 anni
Q2: Come si può estendere la durata?
Implementare una strategia di manutenzione a tre livelli:
1. Livello Operatore: Controlli di lubrificazione prima del turno; pulizia dell'area di lavoro dopo il turno.
2. Livello Tecnico: Test mensili della curva di pressione idraulica e degli test di isolamento elettrico.
3. Livello Esperto: Analisi dello stress strutturale annuale e aggiornamenti del firmware CNC.
Q3: Quando dovrebbe essere sostituita una pressa freno?
Avviare la valutazione di sostituzione se:
Componenti critici (ad esempio, cilindri principali) vengono discontinuati senza alternative.
L'efficienza del processo scende del 30% rispetto ai benchmark dell'industria.
I sistemi di sicurezza non rispettano gli ultimi standard CE/OSHA.
Conclusione e Raccomandazioni
La gestione del ciclo di vita del press brake richiede un sistema di valutazione quantificato:
1. Gestisci i record dell'attrezzatura: Registra la cronologia della manutenzione, i codici di errore e i retrofit.
2. Adotta il monitoraggio IoT: Monitoraggio in tempo reale della pressione, temperatura e vibrazione.
3. Sviluppa piani rotolanti a 5 anni: Allinea le linee temporali dei sostituzioni con la pianificazione della capacità e le tendenze tecnologiche.
Guida all'azione: Ispezioni annuali da parte di terze parti per generare Rapporti sulla Salute dell'Attrezzatura per decisioni basate sui dati.