Sheet metal seamless bending technology
Sheet metal processing technology is constantly improving, especially in some applications such as precision stainless steel bending, stainless steel decorative parts bending, aluminum alloy bending, aircraft parts bending, copper plate bending, etc., which further puts forward higher requirements on the surface quality of the formed workpiece. The traditional bending process is more likely to cause damage to the surface of the workpiece. The surface in contact with the mold will form an obvious indentation or scratch, which will affect the aesthetics of the final product and reduce the user's value judgment of the product.
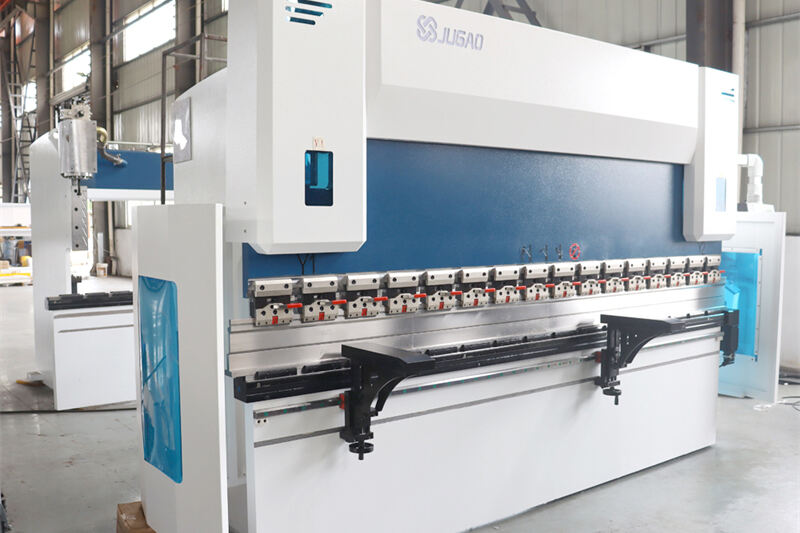
1. Reasons for bending indentation
Take the bending of a V-shaped part as an example. Sheet metal bending is a forming process in which the metal sheet first undergoes elastic deformation and then enters plastic deformation under the pressure of the punch or die of the bending machine. In the initial stage of plastic bending, the sheet is bent freely. As the punch or die presses the sheet, the sheet and the inner surface of the V-shaped groove of the die gradually close together, and the radius of curvature and the bending force arm gradually decrease. Continue to pressurize until the stroke ends, so that the die and the sheet are in full contact at three points, and a V-shaped bend is completed at this time.
During bending, the metal sheet will be squeezed by the bending die and produce elastic deformation, and the contact point between the sheet and the die will slip as the bending process proceeds. During the bending process, the sheet will experience two obvious stages: elastic deformation and plastic deformation. There will also be a pressure holding process during the bending process (three-point contact between the die and the sheet), so three indentation lines will be formed after the bending process is completed. These indentation lines are generally caused by the extrusion and friction between the sheet and the shoulder of the V-groove of the die, so they are called shoulder indentations. The main reasons for the formation of shoulder indentations can be simply classified into the following categories.
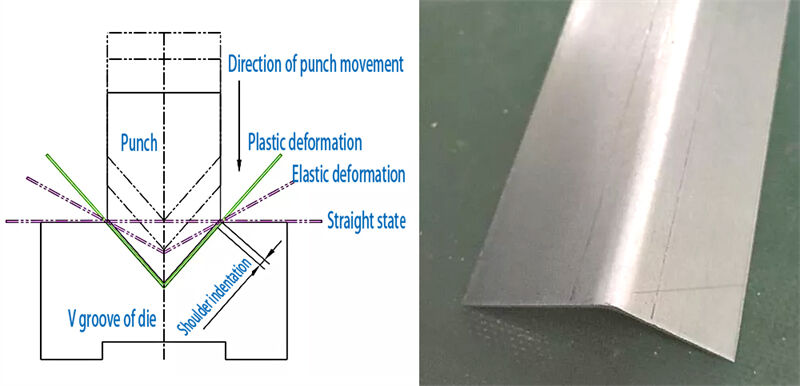
a. Bending method
Since it was mentioned earlier that the generation of shoulder indentation is related to the contact between the sheet and the shoulder of the V-groove of the die, the different gaps between the punch and the die during the bending process affect the compressive stress on the sheet, and the probability and degree of indentation will also be different. Under the same V-groove conditions, the larger the bending angle of the bent workpiece, the greater the tensile deformation of the metal sheet, and the longer the friction distance of the metal sheet on the shoulder of the V-groove; furthermore, the larger the bending angle, the longer the time the punch exerts pressure on the sheet, and the more obvious the indentation caused by these two factors.
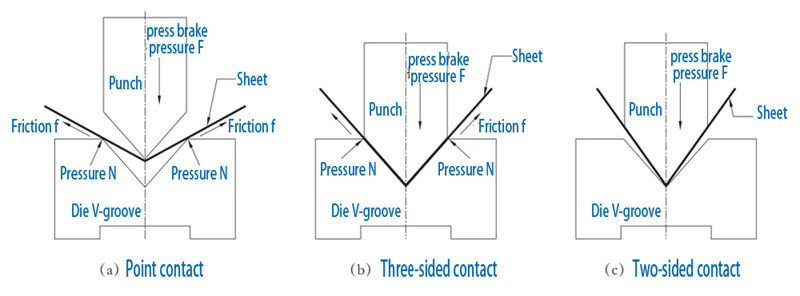
b. Structure of the die V-groove
When bending metal sheets of different thicknesses, the selected V-groove width is also different. Under the same punch conditions, the larger the size of the die V-groove, the larger the size of the indentation width. Correspondingly, the friction between the metal sheet and the shoulder of the die V-groove is smaller, and the depth of the indentation is naturally reduced. On the contrary, the thinner the plate thickness, the narrower the V-groove, and the more obvious the indentation.
Speaking of friction, another factor related to friction that we need to consider is the friction coefficient. The R angle of the shoulder of the die V-groove is different, and the friction caused to the sheet during the sheet bending process is also different. On the other hand, from the perspective of the pressure exerted by the die V-groove on the sheet, the larger the R angle of the die V-groove, the smaller the pressure between the sheet and the shoulder of the die V-groove, and the lighter the indentation, and vice versa.
c. Lubrication degree of die V-groove
As mentioned earlier, the surface of the die V-groove will contact with the sheet and produce friction. When the mold is worn, the contact part between the V-groove and the sheet will become rougher and rougher, and the friction coefficient will become larger and larger. When the sheet slides on the surface of the V-groove, the contact between the V-groove and the sheet is actually the point contact between countless rough convex points and the surface, so the pressure on the surface of the sheet will increase accordingly, and the indentation will be more obvious.
On the other hand, if the die V-groove is not wiped clean before the workpiece is bent, the residual debris on the V-groove will often cause obvious indentations on the sheet. This situation usually occurs when the equipment bends galvanized sheets, carbon steel sheets and other workpieces.
2.Application of Markless Bending Technology
Since we know that the main reason for the bending mark is the friction between the sheet and the V-groove shoulder of the die, we can start from the cause-oriented thinking and use process technology to reduce the friction between the sheet and the V-groove shoulder of the die. According to the friction formula f=μ·N, the factors that affect the friction are the friction coefficient μ and the pressure N, and both are proportional to the friction. Accordingly, the following process plans can be formulated.
a. Use non-metallic materials for the V-groove shoulder of the die
The traditional method of simply increasing the R angle of the V-groove shoulder of the mold is not very effective in improving the bending indentation. From the perspective of reducing the pressure in the friction pair, it is possible to consider changing the V-groove shoulder to a non-metallic material that is softer than the sheet, such as nylon, PU elastomer, etc., while ensuring the original required extrusion effect. Considering that these materials are easy to wear and need to be replaced regularly, there are currently several V-groove structures that use these materials, as shown in the figure.
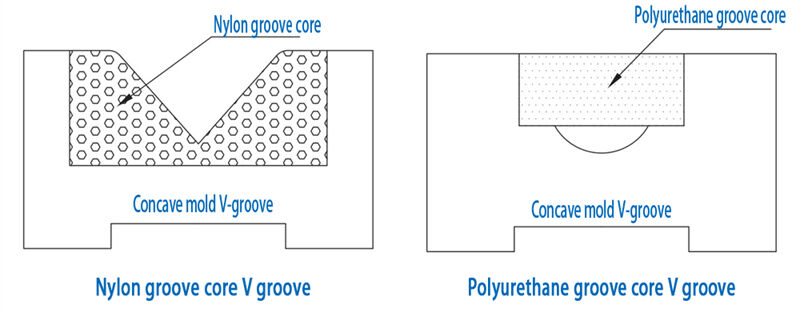
b. Changing the shoulder of the V-groove of the die to a ball and roller structure
Also based on the principle of reducing the friction coefficient of the friction pair between the sheet and the V-groove of the die, the sliding friction pair of the sheet and the shoulder of the V-groove of the die can be transformed into a rolling friction pair, thereby greatly reducing the friction force on the sheet and effectively avoiding the occurrence of bending indentations. At present, this process has been widely used in the mold industry, and the ball-free bending mold is a typical application example.
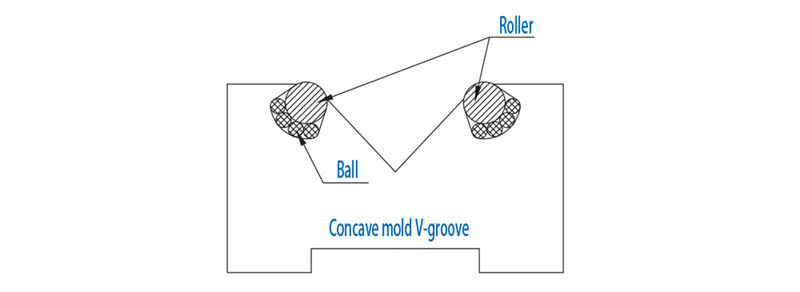
In order to avoid rigid friction between the roller and the V-groove of the ball-bearing seamless bending mold, and also to make the roller easier to rotate and lubricate, balls are added, thereby achieving the effect of reducing pressure and friction coefficient at the same time. Therefore, the parts processed by the ball-bearing seamless bending mold can basically achieve no visible indentation, but the seamless bending effect on soft plates such as aluminum and copper is not good. From an economic perspective, since the structure of the ball-bearing seamless bending mold is more complex than the several mold structures mentioned above, the processing cost is high and the maintenance is difficult, this is also a factor that enterprise managers need to consider when selecting.
c. The V-groove shoulder of the die is changed to a flip structure
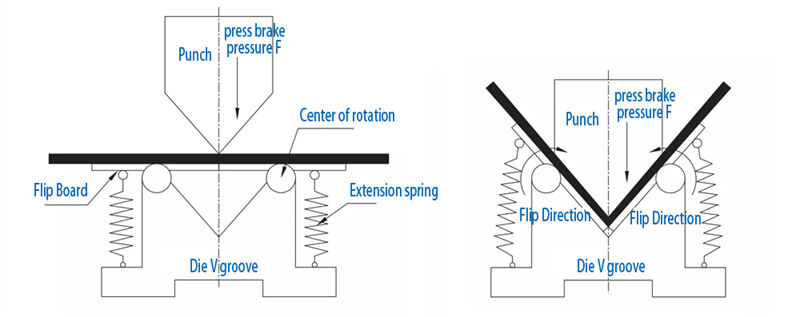
There is another type of mold in the industry that uses the principle of fulcrum rotation to achieve part bending by flipping the shoulder of the die. This mold changes the traditional V-groove structure of the stereotyped die and sets the inclined surfaces on both sides of the V-groove into a flip mechanism. When the punch presses the sheet, the flip mechanism on both sides of the die is flipped inward from the apex of the punch with the help of the pressure of the punch, so that the sheet is bent and formed. Under this working condition, the sheet and the die do not produce obvious local sliding friction, but are close to the flip plane and close to the apex of the punch to avoid indentation on the parts. The structure of this mold is more complicated than the previous structures, with a tension spring and a flip plate structure, and the maintenance and processing costs are higher.
d. V-groove of the die is isolated from the sheet metal
The above mentioned methods are all about achieving seamless bending by changing the bending mold. For enterprise managers, it is not advisable to develop and purchase a new set of molds to achieve seamless bending of individual parts. From the perspective of friction contact, as long as the mold and the sheet are separated, friction does not exist. Therefore, without changing the bending mold, seamless bending can be achieved by using a soft film to prevent contact between the V groove of the die and the sheet. This soft film is also called a bending seamless pressure film, and the materials are generally rubber, PVC (polyvinyl chloride), PE (polyethylene), PU (polyurethane), etc. The advantages of rubber and PVC are low raw material costs, and the disadvantages are that they are not pressure-resistant, have poor protection performance, and have a short life; PE and PU are excellent engineering materials, and the seamless bending pressure film produced with them as the base material has good tear resistance, so it has a long life and good protection.
The bending protection film mainly plays a buffering role between the workpiece and the shoulder of the die, offsetting the pressure between the mold and the sheet, thereby preventing the workpiece from producing indentations when bending. When using it, just put the bending film on the die, which has the advantages of low cost and easy use. The thickness of the bending-free stamping film currently on the market is generally 0.5mm, and the size can be customized according to needs. The bending-free stamping film can generally reach a service life of about 200 bends under a pressure of 2t, and has strong wear resistance, strong tear resistance, excellent bending performance, high tensile strength and elongation at break, and resistance to lubricating oils and aliphatic hydrocarbon solvents.
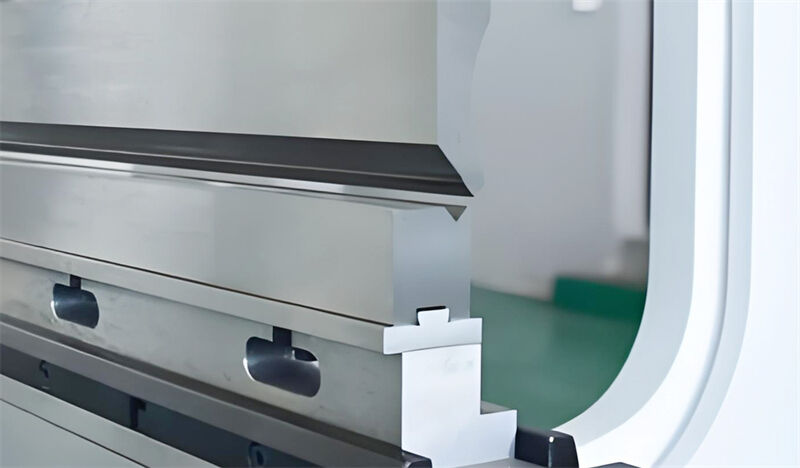
The market competition in the sheet metal processing industry is very fierce. If companies want to gain a foothold in the market, they need to continuously improve their processing technology. Not only should the functionality of the product be achieved, but also the processability and aesthetics of the product should be considered, as well as the economic efficiency of the processing. By applying more efficient and economical process methods, the product can be made easier to process, more economical, and more beautiful.