Future Evolution Paths of Press Brake Technological Innovation
Table of Contents
Automation Revolution: Reshaping Production Paradigms
○ Intelligent Production Line Integration
○ Breakthroughs in Adaptive Control Systems
Digital Ecosystem: Software-Defined Manufacturing
○ End-to-End Digital Twin Technology
○ Deep Integration of Industrial IoT
Green Transformation: Sustainable Manufacturing Practices
○ Closed-Loop Energy Management Systems
○ Innovations in Environmental Compliance Design
Technological Convergence: Outlook for Next-Gen Solutions
Core Technical Analysis
Automation Revolution: Reshaping Production Paradigms
Intelligent Production Line Integration
Modern press brake automation has evolved from single-machine upgrades tofull-line collaboration. By integrating six-axis collaborative robots, AGVmaterial handling systems, and intelligent warehousing modules, manufacturersachieve unmanned operations spanning from raw material loading to finishedproduct sorting. Such systems improve overall efficiency by over 40%, whilevision positioning technology ensures bending repeatability within ±0.05mm,significantly reducing quality fluctuations caused by manual intervention.
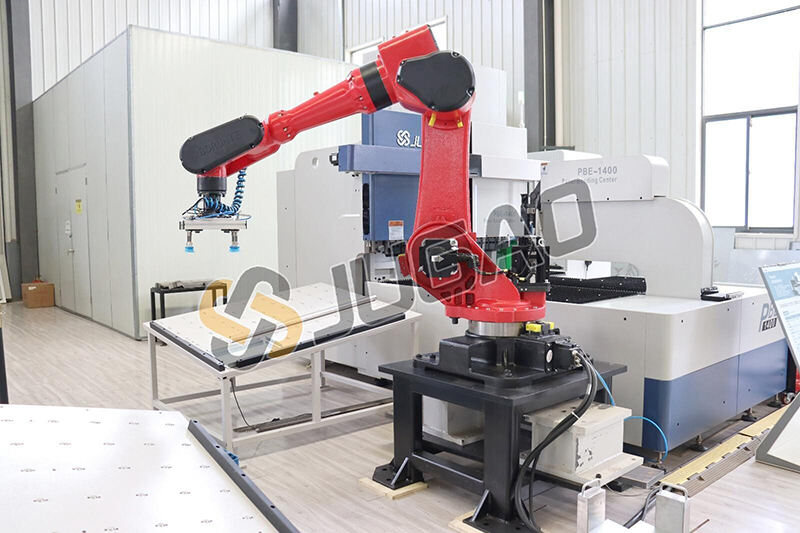
Breakthroughs in Adaptive Control Systems
Adaptive control systems driven by deep learning algorithms are becomingindustry benchmarks. By real-time data acquisition from pressure sensors, laserrangefinders, and other multi-source inputs, these systems dynamically optimizeangle compensation algorithms. For instance, when processing high-strength steelwith significant springback effects, the system automatically adjusts dieopenings, enhancing compensation accuracy from ±0.3° (traditional empiricalvalues) to ±0.1°. This self-evolving logic enables equipment to adapt toincreasingly complex multi-material processing demands.
Digital Ecosystem: Software-Defined Manufacturing
End-to-End Digital Twin Technology
The deep integration of CAD/CAM software with physical equipment has givenrise to digital twin platforms. Engineers can complete full-processvalidations—from 3D modeling and process simulation to stress analysis—invirtual environments, accurately predicting sheet metal deformation duringbending. Case studies show that this technology reduced trial molding cycles foran automotive parts manufacturer from 15 days to 72 hours, with material wastedecreasing by 22%.
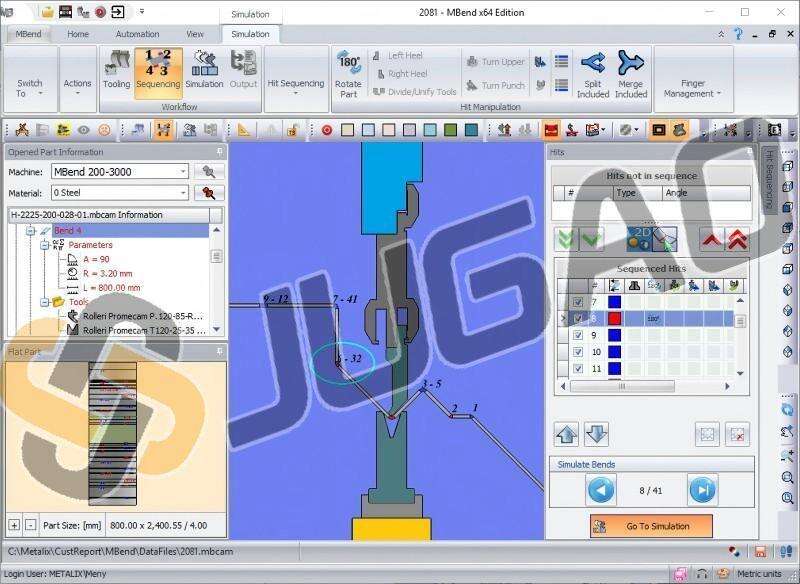
Deep Integration of Industrial IoT
Remote monitoring systems supported by 5G and edge computing architecturesachieve millisecond-level responsiveness. By deploying vibration analysissensors and hydraulic oil condition monitoring modules, equipment can predictcritical component failures (e.g., servo motor bearings) 14 days in advance.Additionally, blockchain-based process data certification systems are addressingstringent traceability requirements in aerospace manufacturing.
Green Transformation: Sustainable Manufacturing Practices
Closed-Loop Energy Management Systems
Next-gen electric servo press brakes employ bidirectional inverter technologyto feed braking energy back into the grid, reducing energy consumption by 65%compared to traditional hydraulic models. Experimental data indicate that hybridsystems with supercapacitors recover 32% of inertial energy during continuousprocessing of 2mm stainless steel plates, achieving an annual carbon reductionof 8.6 tons per machine.
Innovations in Environmental Compliance Design
Low-noise hydraulic systems compliant with ISO 50001 standards utilizevariable pumps and accumulator synergy to reduce idle noise from 85dB(A) to72dB(A). Meanwhile, replacing mineral oil with bio-based hydraulic fluids cutsVOC emissions by 46% over the equipment lifecycle, aligning with EU EcoDesign2025 regulations.
Technological Convergence: Outlook for Next-Gen Solutions
Electro-hydraulic hybrid drive systems are breaking traditional boundaries:Hydraulic systems enable rapid feed during roughing, while electric servo modesensure precision in finishing, achieving an industry-leadingefficiency-to-energy ratio of 1:0.78. Furthermore, quantum computing-drivenprocess optimization algorithms are projected to compress programming time forcomplex curved bends to minutes by 2025.
Core Technical Analysis
Technical Dimension | Innovative Value |
Automation | Enables 24/7 continuous production, reduces labor costs by 57%, and boosts OEE (Overall Equipment Effectiveness) to 89% |
Digitalization | Shortens product development cycles by 40%; process databases enhance new employee training efficiency by 300% |
Sustainability | Reduces total energy consumption by 52%, carbon footprint by 38%, and compliance costs by 65% |
Conclusion
The innovation wave in press brake technology is advancing along three axes:intelligence, digitalization, and sustainability. Over the next five years,cognitive press brakes with self-diagnostic capabilities, cloud-basedcollaborative manufacturing platforms, and zero-carbon hydrogen-poweredsolutions may redefine competition in metal forming industries. Formanufacturers, embracing these trends is not only critical for enhancingcompetitiveness but also an essential pathway toward Industry 4.0transformation.