Core Differences Between Electric and Hydraulic Press Brakes
Table of Contents
Introduction
Technical Principles Overview
Working Mechanism of Electric Press Brakes
Working Mechanism of Hydraulic Press Brakes
Core Performance Comparison
Energy Consumption & Operational Costs
Processing Precision & Efficiency
Power Output & Applicable Scenarios
Maintenance Requirements & Long-Term Costs
Application Recommendations
Conclusion
Introduction
In metal forming industries, the selection of press brakes directly impactsproduction efficiency and process accuracy. Electric and hydraulic press brakes,as mainstream technologies, dominate distinct application scenarios due to theirdifferentiated technical characteristics. This article systematically comparestheir working principles, performance metrics, and suitability to provideactionable insights for industrial users.
Technical Principles Overview
Working Mechanism of Electric Press Brakes
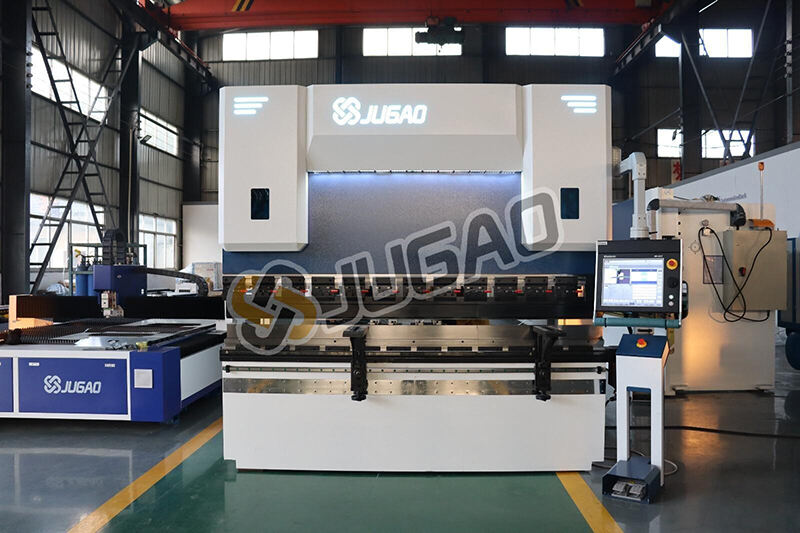
Driven by servo motors and controlled via precision CNC modules, electricpress brakes achieve dynamic torque regulation. Their core advantages includehigh energy conversion efficiency (exceeding 90%) and minimized mechanicaltransmission errors through direct programmatic motion control. These machinesexcel in high-precision, low-noise processing of lightweight materials, such aselectronic enclosures or medical device components.
Working Mechanism of Hydraulic Press Brakes
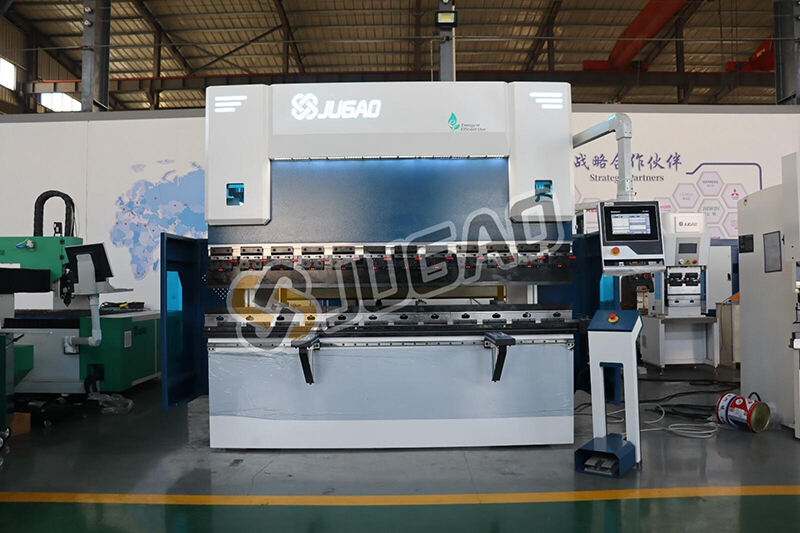
Hydraulic systems utilize pump assemblies to drive pistons, generating linearpressure through hydraulic fluid circulation. This design ensures stable andscalable force output, adaptable to thick plates (up to 50+ mm) via adjustablecylinder configurations. Typical applications include shipbuilding componentsand heavy machinery chassis for large-scale industrial production.
Core Performance Comparison
Energy Consumption & Operational Costs
Electric Press Brakes: Servo motors consume energy only during operation,with near-zero standby power, reducing overall energy usage by 40%-60% comparedto hydraulic models.
Hydraulic Press Brakes: Hydraulic pumps require continuous operation tomaintain system pressure, leading to baseline energy consumption even duringidle states, significantly increasing long-term operational costs.
Processing Precision & Efficiency
Electric Press Brakes: Achieve repeat positioning accuracy of ±0.01 mm,with high-speed servo systems enabling over 25 cycles per minute, ideal fortight-tolerance precision bending.
Hydraulic Press Brakes: Maintain accuracy of ±0.1 mm, with cycle speedslimited by hydraulic response. Multi-cylinder synchronization technologyenhances stability for batch production with moderate precisionrequirements.
Power Output & Applicable Scenarios
Electric Press Brakes: Maximum force ranges from 100-600 tons, suitable forcomplex shaping of thin stainless steel (0.5-6 mm) or aluminum alloys.
Hydraulic Press Brakes: Deliver forces exceeding 3,000 tons, capable offorming thick carbon steel plates (6-50 mm) and high-strength alloys.
Maintenance Requirements & Long-Term Costs
Electric Press Brakes: Simplified mechanics eliminate hydraulic fluidleakage risks. Routine tasks include rail lubrication and servo systemdiagnostics, reducing annual maintenance costs by 30%-50%.
Hydraulic Press Brakes: Require periodic hydraulic fluid replacement (every2,000 operating hours) and monitoring of seals/filters, resulting in highermaintenance frequency and costs.
Application Recommendations
Equipment Type | Recommended Scenarios |
Electric Press Brakes | Medium-small batch precision processing, rapid mold changes, clean room environments, 24/7 automated production lines |
Hydraulic Press Brakes | Large-scale standardized production, ultra-thick plate forming, high-tonnage demands, space-constrained workshops |
Conclusion
The divergence between electric and hydraulic press brakes reflects theindustrial demand for "precision efficiency" versus "robust power." Users mustevaluate material properties, production scale, and technical requirements:
Electric models prioritize zero-defect rates and energy efficiency forlightweight applications.
Hydraulic systems remain indispensable for heavy-duty materials and massproduction.
Emerging hybrid press brakes (electro-hydraulic synergy) may bridgeperformance gaps, offering next-generation solutions as intelligent controltechnologies evolve.