Factors affecting the tonnage of bending machines
Bending methods
Bendingmethods | Influenceon the tonnage of bending machines |
Airbending | Itrequires more tonnage than pneumatic bending because the upper die bottoms outin the die. The material contacts the tip of the upper die and the sidewall ofthe lower die. The tonnage is higher, but not as high as imprinting. |
Bottombending | Itrequires more tonnage than air bending because the upper die bottoms out in thedie. The material contacts the tip of the upper die and the side wall of thedie. The tonnage is higher, but not as high as imprinting. |
Imprinting | Requiresthe highest tonnage. The punch and die are in full contact with the material,compressing and thinning the material. Use very large forces to make thematerial conform to the die angle of the bending machine |
Different metal bending methods require different tonnage. For example, inair bending, the tonnage can be increased or decreased by changing the dieopening width.
The bend radius affects the die opening width. In this case, the methodfactor must be added to the formula. When using bottom bending and imprinting,the required tonnage is higher than air bending.
If you calculate the tonnage for the bottom bend, you need to multiply thetonnage per inch of air bend by at least five. If you use stamping, the tonnagerequired may be even greater than for the bottom bend.
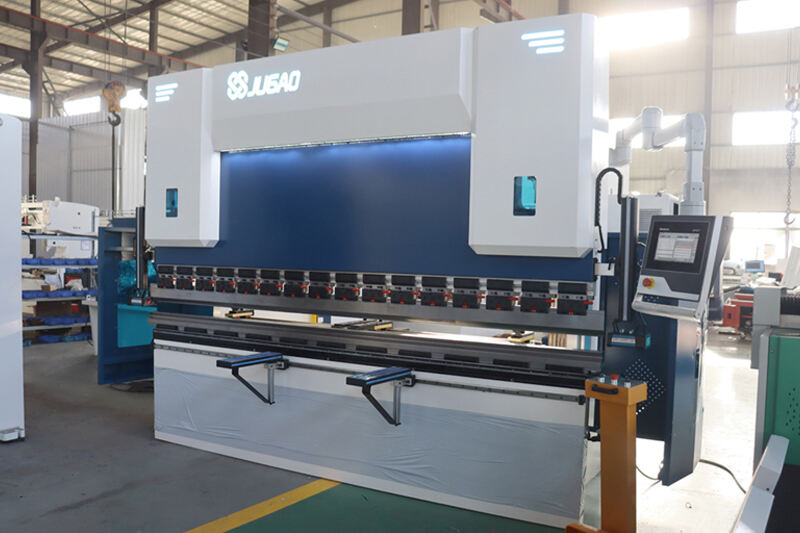
Die Width
We have already learned that in air bending, the tonnage required decreasesas the die opening size increases and increases as the opening sizedecreases.
This is because the width of the die opening determines the inside bendradius, and a smaller die radius requires more tonnage.
In air bending, the die ratio is typically 8:1, meaning the die openingdistance is eight times the material thickness. In this case, the materialthickness is equal to the inside bend radius.
Friction and Speed
In air bending, the punch needs to pass through the bottom die opening tobend the metal sheet. If the metal sheet surface is not lubricated, the frictionbetween the die and the metal sheet increases, requiring more tonnage to bendthe metal sheet and reducing the springback of the material.
Conversely, if the metal sheet surface is smooth and lubricated, the frictionbetween the die and the metal sheet decreases, reducing the tonnage required tobend the metal sheet. However, this will increase the springback of the metalsheet.
Bending speed also affects the required tonnage. As the bending speedincreases, the required tonnage decreases. Increasing the speed also reduces thefriction between the die and the sheet, but this also increases the springbackof the sheet.
Material Properties
Tonnage refers to the force that the press brake applies to the sheet metal.Therefore, the range of bending forces depends on the thickness and tensilestrength of the sheet metal being bent.
Material Type
One factor is the type of material being bent. Materials with higher tensilestrengths, such as stainless steel or high-strength alloys, require more forceto bend than softer metals, such as aluminum or copper. For example
Stainless steel (grade 316): tensile strength ~620 MPa; yield strength ~290MPa.
Copper: tensile strength ~210 MPa; yield strength ~69 MPa.
Softer materials, such as aluminum, exhibit less resistance, which reducestonnage requirements but increases the potential for springback.
Tensile Strength and Yield Strength
Different materials have different tensile strengths, which directly affectsthe force required to bend. For example, stainless steel generally requires moretonnage than mild steel or aluminum.
Tensile strength is the maximum stress a material can withstand under asteady load. If this stress is applied and maintained, the material willeventually break. Yield strength, on the other hand, is the stress at which amaterial begins to deform plastically.
Typical tensile strengths of some materials
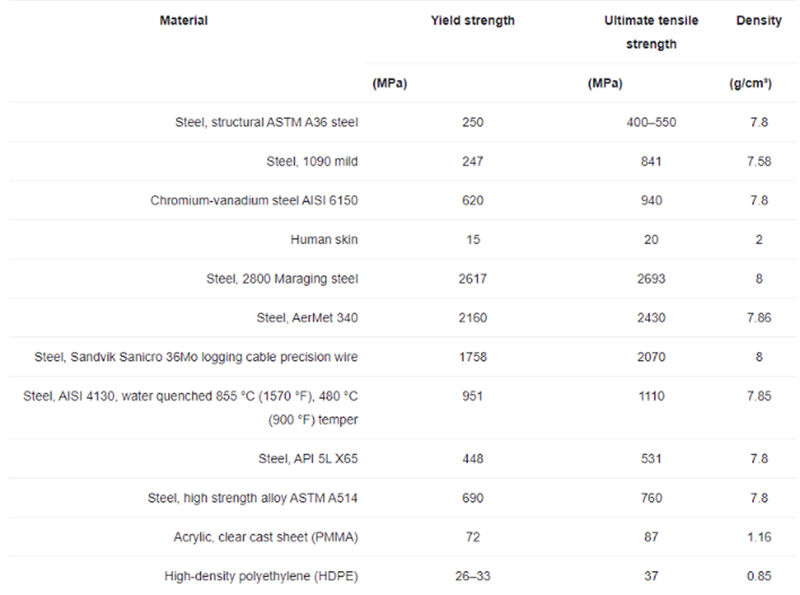
Material thickness
Another important factor is the thickness of the sheet metal. The thicker thematerial, the more tonnage is required, and vice versa. Thicker materialsrequire multiple times more tonnage due to their greater resistance todeformation.
For example, doubling the thickness of the sheet metal will double the forcerequired. Generally speaking, the thicker the material, the more tonnage orforce is required to form it.
Materials | Thickness (mm) | Bending radius (mm) | Tonnage multiplier | Required tonnage (tons/meter) |
Mild steel | 1 | 1 | 1 | 10 |
Mild steel | 2 | 2 | 1 | 40 |
Mild steel | 3 | 3 | 1 | 90 |
Aluminum (5052-H32) | 1 | 1 | 0.45 | 4.5 |
Aluminum (5052-H32) | 2 | 2 | 0.45 | 18 |
Aluminum (5052-H32) | 3 | 3 | 0.45 | 40.5 |
Stainless steel (304) | 1 | 1 | 1.45 | 14.5 |
Stainless steel (304) | 2 | 2 | 1.45 | 58 |
Stainless steel (304) | 3 | 3 | 1.45 | 130.5 |
Mild steel | 2 | 1 | 1 | 60 |
Mild steel | 2 | 3 | 1 | 30 |
Stainless steel (304) | 2 | 1 | 1.45 | 87 |
Stainless steel (304) | 2 | 3 | 1.45 | 43.5 |
The table shows that
1. As the thickness of the material increases, the tonnage required for allmaterials increases significantly. Doubling the thickness from 1 mm to 2 mmincreases the tonnage fourfold.
2. Aluminum requires about 45% more tonnage than mild steel of the samethickness, and stainless steel requires about 45% more tonnage than mildsteel.
3. Reducing the inside bend radius while keeping the thickness constantincreases the tonnage required. Halving the radius from 2 mm to 1 mm increasesthe tonnage by 50%.
4. The tonnage multiplier varies by material type and tensile strength. Inthis example, it is 1.0 for mild steel, 0.45 for 5052-H32 aluminum, and 1.45 for304 stainless steel.
Springback
After bending, materials tend to spring back slightly toward their originalshape. High-strength materials will have more springback, so tonnage and toolingneed to be adjusted to achieve precise angles.
Bend Length and Angle
Bend Length
The bend length of the press brake table is the maximum length that a sheetof metal can be bent. The bend length of the press brake should be slightlylonger than the material being bent.
If the table length is incorrect, damage to the die or other components mayoccur. A bend load calculator can help determine the required tonnage based onmaterial thickness and other factors such as bend length and V-openingwidth.
Bend Angle
The larger the angle, the higher the tonnage required due to the increasedmaterial compression at the bend point. Conversely, larger angles require lessforce but may result in less accurate bends.
Tooling Factors
Press brake punches are also a factor to consider. These punches also havebending load limitations. Right-angle V-shaped punches can handle larger tonnageloads.
Since sharp-angle dies have a smaller angle and are made with less material,such as gooseneck dies, they are not as inclined to handle heavy loads.
When using different dies, their maximum bending force must not be exceeded.In addition, the die radius and bend radius also affect tonnagerequirements.
A larger die radius may result in an increase in the required bending force.Likewise, the larger the bend radius, the higher the required tonnage.
The ratio between the die opening width and the material thickness is anotherfactor to consider. For thinner materials, a lower die ratio (such as 6 to 1) isrecommended.
Thicker materials may require a higher die ratio (such as 10 to 1 or 12 to 1)to reduce the bending force and keep the application within the capabilities ofthe bending machine.
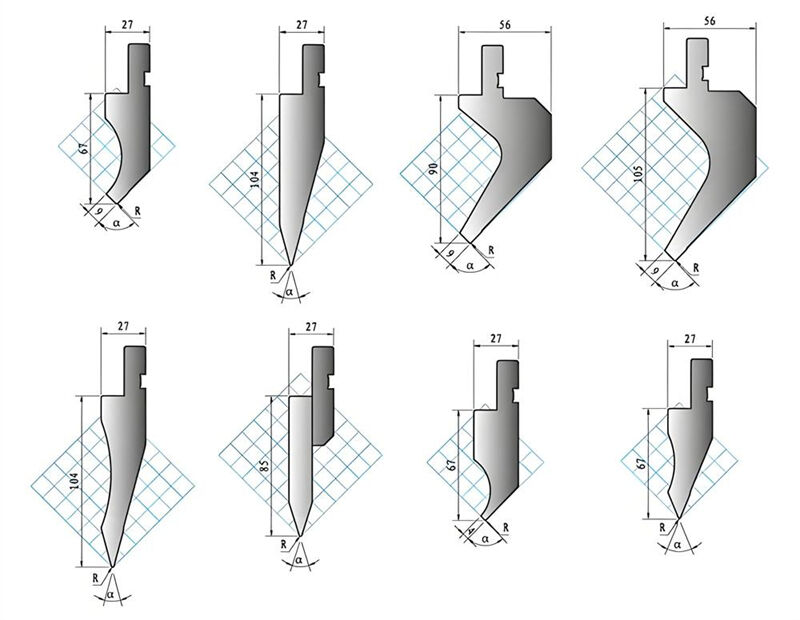
Long-term tool wear
Gradual wear:
Over time, repeated high-pressure operations cause tools to lose theirsharpness and structural integrity. If not addressed, this wear can lead toinconsistent bends and reduced part quality.
Impact on tool life:
Overloading a tool beyond its rated capacity (e.g., machining thick platewith a narrow die) can cause micro cracks or catastrophic failure duringoperation. Regular inspections are essential to prevent unexpected downtime orsafety hazards.
Maintenance requirements:
Tools that are overloaded require more frequent maintenance or replacement,increasing operating costs. Monitoring systems or predictive maintenancesoftware can help identify wear patterns early and optimize tool use.
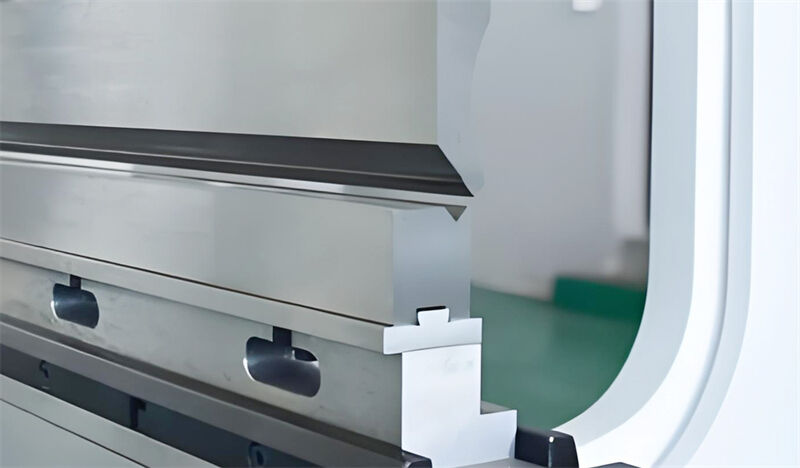