Paano ma-extend ang service life ng laser cutting machine?
Gusto mong makaeektibo na mapalawig ang serbisyo ng buhay ng iyong laser cutting machine? Narito ka nang tama. Ang pagpapalawig sa buhay ng makina ay hindi lamang nakakatipid sa mga gastos, kundi pati ring nag-iinspeksyon ng katuturan ng pag-cut, nakakabawas ng hindi inaasahang paghinto, at nagpapatuloy na produktibo sa malalim na produksyon. Ang praktikal na mga estratehiya sa pagsasawi at ang pinagkakasyang payo na ibinibigay sa pamamagitan ng gabay na ito ay makakatulong upang matakbo ang iyong kagamitan nang matatag at matagal. Maaaring gamitin ang mga paraan na ito sa mga maliit na workshop at malalaking fabrica.
Mga Tip sa Pagsasawi sa Araw-araw at Linggo-linggo
Ilininis ang optika nang regulado
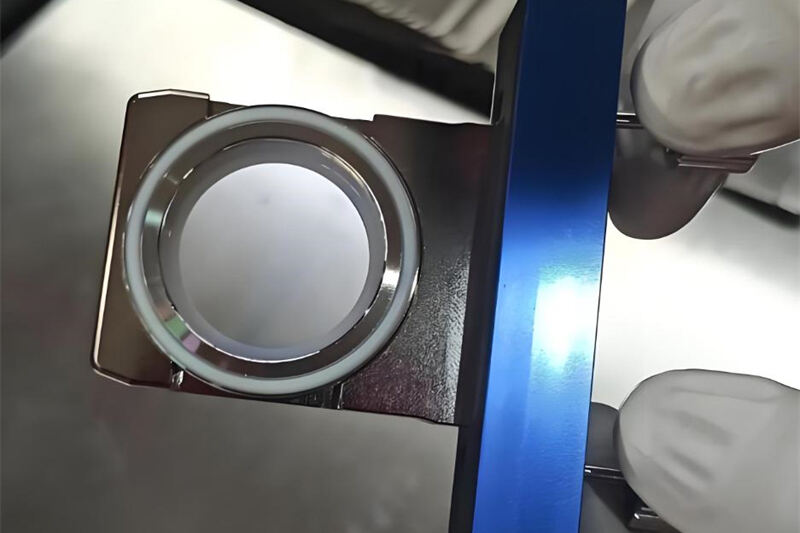
Ang pagsisiguradong malinis ang mga optical components ay isang pangunahing hakbang upang mapalawak ang buhay ng laser cutting machine. Ang alikabok at basura sa lens o reflector ay magiging sanhi ng pagkawala ng enerhiya ng beam at abnormal na pagtaas ng temperatura. Kinakailangan ang espesyal na kagamitan para sa pagsisilbing-linis - itinatanggol na gamitin ang karaniwang kain o madirektang ilapag sa kamay. Ang malinis na optical components ay hindi lamang makakapag-ensayo ng katumpakan ng pag-cut, bagkus epektibong bababaan ang presyon sa laser source at mapapalawak ang kanyang buhay.
Surian at palitan ang mga nozzle
Madalas hinahangaan ang bilis ng pagwawasak ng mga nozzle. Ang sugat o tinitig na nozzle ay maaaring magiging sanhi ng hindi makatarungan na pag-cut, splashing ng material, o kaya naman kahihiyan sa pag-cut head. Inirerekomenda na suriin ang kondisyon ng mga nozzle bawa't linggo at palitan sila nang maaga ayon sa mga kondisyon ng trabaho. Ang modestong investment na ito ay maaaring epektibong maiwasan ang mahal na mga sumusunod na pagdama.
Paglilimos ng mga gumagalaw na bahagi
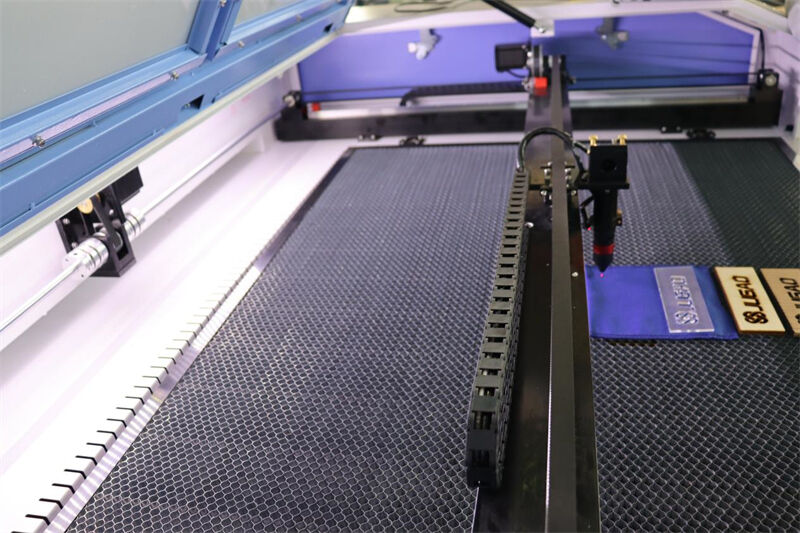
Ang regular na paglubog ng mga guide, linear bearings at mga parte na nagagalaw ay mahalaga upang maiwasan ang siklo ng pagkakaputol at pagkaubos. Iyong rekomendado na magdagdag ng lubrikante bawat 200-300 oras ng paggamit o mas mababa (tulad ng kondisyon ng maangin). Siguruhing sundin nang mabuti ang mga patakaran ng tagagawa, gamitin ang tinukoy na modelo at ipagawa ang pamamahala sa lubrikasyon ayon sa inirerekumendang tsiklo.
Surian at linisin ang sistemang pagsisilaw
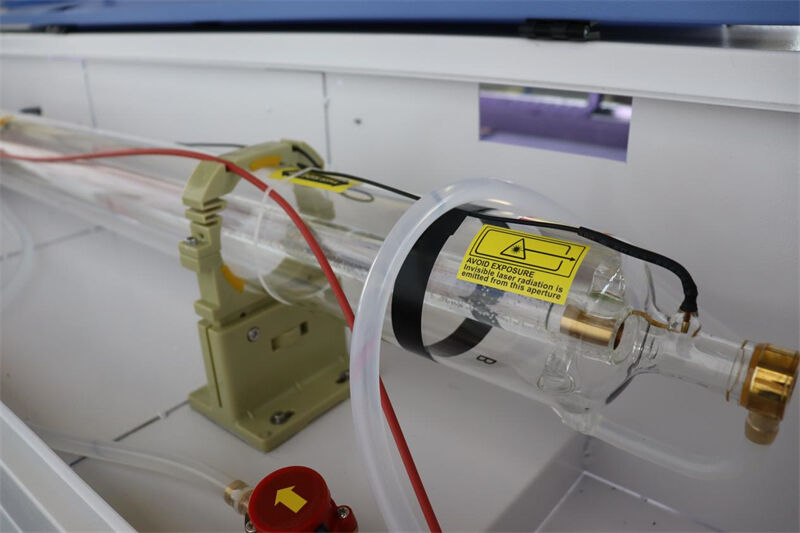
Mga laser cutting machine ay nakakaugnay sa pangunahing water cooling system upang makapagpatibay ng temperatura ng laser source. Dapat suriin regula ang antas ng coolant, sirkulasyon at kontaminasyon. Kung ang coolant ay naging kulog o nabago ang kulay, ito ay dapat palitan agad. Sa parehong panahon, regular na paglilinis ng water tank at filter ay maaaring makabawas sa pagkatagal ng buhay ng kagamitan dahil sa sobrang init.
Mga Update sa Software at Firmware
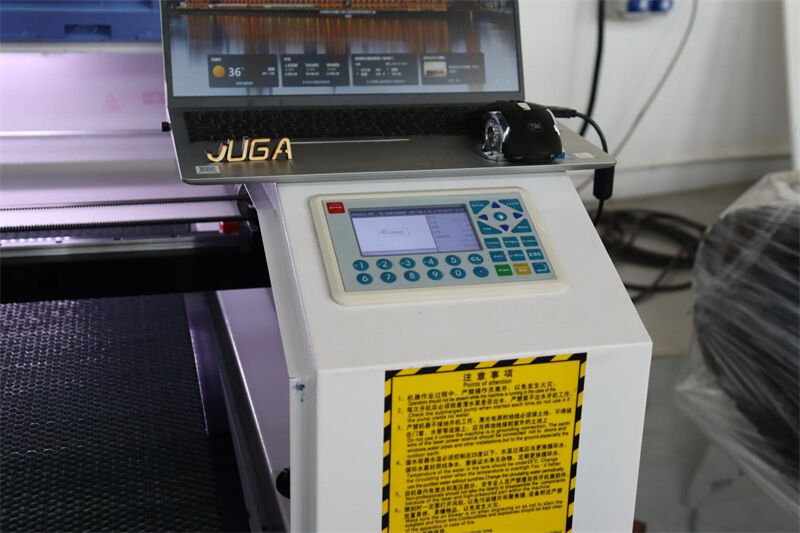
Iniiyakay na lagi mong i-update ang kontrol na software at firmware. Ang mga manufacturer ay regulaong naglalabas ng mga update upang mapabuti ang katumpakan sa pag-machining, ang kagandahan ng sistema at siguradong ligtas. Ang maaga mong pagsunod sa mga update ay hindi lamang nagpapatakbo nang mabuti ang equipment, kundi pati na din bumabawas sa paglabag ng loob na bahagi at nagpapahaba ng buhay ng serbisyo.
Mga Dakilang Gampanin upang Maiwasan ang Paglabag at Pagtitiim
Gumamit ng tamang cutting parameters
Ang maling bilis ng pag-cut o setting ng kapangyarihan ay maaaring sanhiin ang sobrang-bubuhos at paglabag ng pangunahing bahagi. Matatag na inirerekomenda na subukin at optimisahin ang mga parameter ng pagproseso para sa iba't ibang uri ng material. Halimbawa, pag-cut ng makapal na stainless steel sa pinakamataas na kapangyarihan para sa mahabang panahon kasama ang maling parameter ng gas ay madaling sanhiin ang malaking pinsala sa optikong bahagi at cutting beds, na sigarilyo ay napakaliit ang buhay ng equipment.
Iwasan ang sobrang-bubuhos sa iyong workbench
Ang sobrang timbang o maliit na posisyon ng mga trabaho ay maaaring sanhiin ang pagkabulok o kahit ang pagka-iba ng alinman sa makina. Siguraduhing maayos at patas na ibahagi ang presyo ng mga materyales at sundin nang mabuti na patas ang ibabaw ng lamesa bago mag-load ng mga plato (lalo na ang mga matinding materyales tulad ng carbon steel) upang maiwasan ang pinsala sa estraktura.