What impact does a laser cutting machine have on the environment?
While many manufacturers are concerned about sustainability and eco-efficiency, they also have questions about the environmental impact of laser cutting machines. This article will take a deep dive into the ecological footprint of this type of equipment, covering key issues such as noise pollution, exhaust emissions, and waste disposal. Whether you are preparing to introduce new equipment or want to optimize the environmental performance of an existing workshop, this guide will provide you with valuable decision-making reference.
Understanding the Environmental Footprint of Laser Cutting
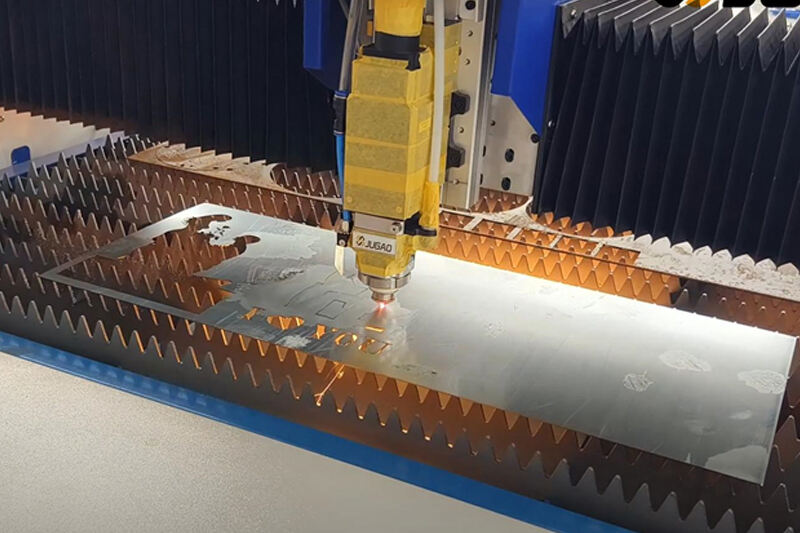
Laser cutting technology occupies an important position in the manufacturing industry due to its excellent processing accuracy and excellent production efficiency. However, this advanced processing method is also accompanied by environmental impacts that cannot be ignored. The following will systematically analyze these environmental impact factors.
Noise pollution from laser cutting machines
While laser cutting is generally quieter than mechanical cutting methods, it still produces noticeable noise—especially when operating at high power or cutting thicker materials.
Major noise sources: Exhaust fans, gas delivery systems, air compressors, and movement of the cutting head all contribute to overall noise levels.
Typical noise levels: Between 65–85 dB, depending on material and machine type.
Solutions: Installing soundproofing, regularly maintaining equipment, and isolating laser cutting areas can help reduce noise pollution in the workplace.
Laser cutting machine exhaust and fume emissions
One of the most concerning aspects of the environmental impact of laser cutting machines is the emission of fumes and gases during the cutting process.
What causes fumes? Cutting certain materials, especially plastics or coated metals, can release toxic gases such as formaldehyde, hydrogen chloride and fine particulate matter.
Health risks: Poor fume extraction can cause respiratory problems for operators and contribute to indoor air pollution.
Exhaust solutions:
Use high-efficiency particulate air (HEPA) filters and activated carbon filters.
Clean and inspect extraction systems regularly.
Avoid cutting materials that are harmful or not suitable for the laser.
Waste management in laser cutting processes
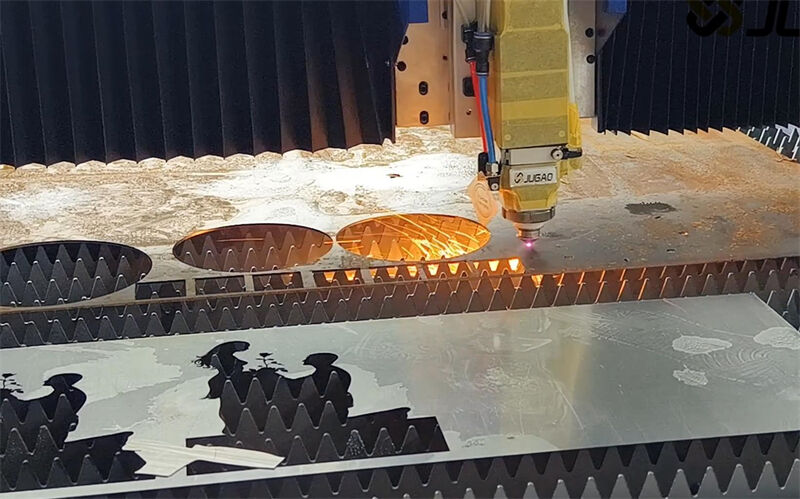
Laser cutting produces relatively little physical waste compared to traditional methods, but there are still by-products that need to be properly managed.
Waste Types:
Metal scrap from paper cutting
Spatter and residue buildup on the cutting bed
Filter exhaust system waste
Best Practices:
Recycle metal scrap through a certified metal recycling facility.
Clean the machine’s cutting bed and ventilation filters regularly.
Use digital nesting software to minimize material use and reduce scrap.
How to reduce the impact of laser cutting machines on the environment
Implement proper ventilation and air filtration systems
Optimize cutting layout to reduce material waste
Using nesting software, you can fit as many parts as possible onto one sheet, minimizing leftover scrap and saving costs.