Paano madali ang paggawa ng pagbabago ng lensa ng laser cutting machine?
Paano madali ang paggawa ng pagbabago ng lensa ng laser cutting machine?
Mukhang huli pa rin ba kayo nag-aalala tungkol sa pagbabago ng lensa ng inyong laser cutting machine? Maling pamamaraan ay madaling magdulot ng mga problema. Mag-aral ng detalyadong guia hakbang-hakbang upang madali ang pagbabago ng lensa at siguruhin na maaaring tumakbo ang kagamitan nang mabuti at walang tigil.
Ang pagsasalba sa lente ng laser cutting machine ay madali. Sundin ang ating malinaw at maikling gabay upang matapos ang pagsasalba nang mabisa. Mula sa paghahanda hanggang sa huling pagsubok, itong gabay ay makakatulong sa iyo na siguruhin na ang iyong kagamitan ay palaging nakikipagtrabaho sa pinakamataas na antas. Malaman kung paano panatilihin ang epektibong paggana ng iyong makina at paniwalaan ang kanyang buhay. Ang sumusunod ay ipapaliwanag ang mga hakbang ng paghahanda, pagtanggal ng lente at proseso ng pagsasanay upang tulungan ka sa pagbabago ng lente nang maayos.
Ang mahalagang halaga ng pag Sundin ng gabay sa pagsasalba ng lens ay upang mapabilis ang serbisyo ng buhay ng laser cutting machine. Pagkatapos ng maayos na paggamit, ang lens ay madaling maaapektuhan ng kontaminasyon o pinsala, na maaaring magdulot ng mga problema tulad ng pinababa na katatagan ng pag-cut, pinababa na katatagan ng pagproseso at tumataas na rate ng pagbagsak ng kagamitan. Ang regular na pagbabago ng lens ay maaaring makaeektibo na maiwasan ang mga sitwasyong ito at tiyakin ang tuloy-tuloy at magkasundulan na katatagan ng pagproseso. Sa parehong oras, ang regular na pamamahala na ito ay maaaring tiyaking malikhain ang maayos na operasyon ng kagamitan, iwasan ang hindi inaasahang pamamaril, at sa dulo ay maaaring maitindak ang mga gastos sa pamamaril at mabawasan ang mga pagkakaapi sa paggawa.
Ang talaksan na ito ay sistematikong nagpapaliwanag ng proseso ng pagbabago ng lens at mga pangunahing hakbang sa pagsustain upang makamit ang pinakamahusay na pagganap ng mga laser cutting machine. Ang kumpletong pagsunod sa mga regular na plano para sa pagsustain at paggamit ng estandang mga paraan ng operasyon ay maaaring hindi lamang pagbutihin ang katumpakan ng pagproseso, kundi pati na ring tiyakin na maaaring magbigay ng mataas na kalidad ng resulta sa pag-cut sa isang haba at maligalig na pamamaraan. Alisin ang mga panganib sa produksyon na dulot ng pagbabaon sa pagsustain o pagtanda ng lens - sunodin ang talaksan na ito at makakatulong ito upang makabuo ng pinakamataas na epektibidad ng operasyon at makaiwas nang epektibo sa mataas na gastos sa pagsasanay.
Bakit mahalaga ang pagbabago ng iyong mga lens?
Ang pribitong pagbabago ng mga lente ay isang pangunahing hakbang sa pamamahala upang siguruhin ang pagganap ng mga laser cutting machine. Ang sobrang gamit ng mga lente ay direktang magiging sanhi ng pagbaba ng pagganap ng equipment, na ipinapakita bilang pagkasira ng kalidad ng pag-cut at pagtaas ng pag-wear ng mga pangunahing bahagi. Ang pag-iwas sa pagsustenta ng mga lente ay hindi lamang magiging sanhi ng mali sa katumpakan ng pagproseso, kundi pati na ding magiging sanhi ng mataas na gastos sa pamamahala.
Ang pribitong pagbabago ng mga lente ay maaaring siguruhin ang kasarian ng katumpakan ng pag-cut, palawakin ang seguridad ng operasyon at pagpahabangin ang buhay ng mga pangunahing bahagi. Ang pangunahing operasyong ito sa pamamahala ay maaaring epektibong maiwasan ang deposito ng kontaminante at pinsala sa lente, siguruhin ang tuloy-tuloy at handa na operasyon ng equipment; ito rin ay isang pangunahing mekanismo upang maiwasan ang di inaasahang pag-iwan at mga gastos sa pamamahala.
Ang pagsasalita ng lensa nang regulasyon ay mayroong dual na halaga na pagpapabuti sa katuturan ng pag-cut at pagiging sikat sa pagpigil ng mga high-cost na pagsasakay na dulot ng akumulasyon ng micro-damage. Pagsunod sa estandang proseso ng pamamahala ay maaaring tiyakin na patuloy ang laser cutting machine sa kanyang pinakamainit na pagganap at sistematis na kontrolin ang panganib ng hindi inaasahang pag-iwan.
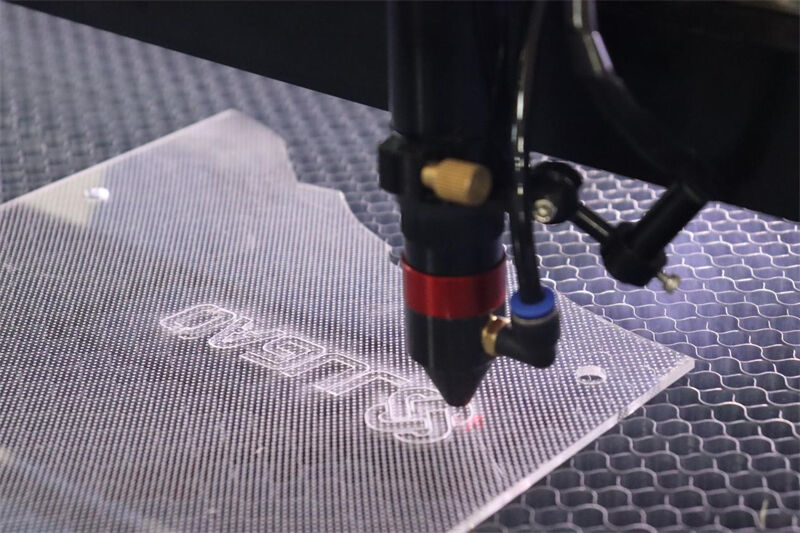
Paano i-replace ang proteksyon na lensa ng laser cutting machine?
Naglalaro ang proteksyon na lensa ng isang pangunahing papel sa pampagprotektahan ng laser cutting head at direktang nagpapasiya sa katutusan ng pag-cut. Habang tumatagal ang paggana ng equipment, maaaring makuha ng lensa ang kontaminasyon, scratch o pagwawasak, na nagreresulta sa pagbaba ng kalidad ng pag-cut at pagbagsak ng pagganap ng equipment.
Upang i-replace ang proteksyon na lensa, unang siguraduhin na maubos ang enerhiya ng makina at nasakop na temperatura. Meticulously alisin ang dating lensa at linisin ang lens housing bago mag-install ng bagong lensa. Lagyan ng gloves ang lahat upang pigilan ang langis o dumi mula sa kamay na magdudulot ng dumi sa lensa.
Ang pagsasalungat ng mga protuktibong lente ay isang disisyun na kailangan upang panatilihin ang kalidad ng pagkakita. Gumamit ng microfiber cloth sa pagsisilip ng lugar sa paligid ng lente habang gumagana. Ang optikong komponenteng ito ay ang pangunahing garanteng tungkol sa katumpakan ng pagpokus ng laser beam at direktang nakakaapekto sa katumpakan ng pagproseso. Habang nag-aakumula ang oras ng operasyon, maaaring magkaroon ng mga sugat, kontaminadong depósito o pisikal na pinsala sa lente, na may direktang relasyon sa kalidad ng pagkakita. Ang mga nabigong lente ay dadalhin sa serye ng pagkabigo tulad ng distorsyon ng profile ng pagkakita, pagbaba ng enerhiya at pag-uwersa ng equipment. Kaya't, ang pagsisimula ng regular na inspeksyon at pagsalungat ng lente ay isang mahalagang bahagi ng estratehiya ng preventive maintenance, na hindi maaalis upang siguruhin na patuloy ang laser cutting system na lumabas ng pinakamahusay na katumpakan ng pagproseso.
Mga spesipikasyon sa paglilinis ng lens: Bago ang pagsasalungat, kinakailangang buksan ang anumang alikabok, langis at iba pang kontaminante sa paligid gamit ang microfiber cloth. Ang materyales na ito, kasama ang mga katangian nito na hindi makakapinsala, maaaring magamit upang maiwasan ang mga sugat sa mga optikal na permisyong precise. Iwanag ang isang galaw ng pagsisikid na malambot upangalisin ang mga partikula, at ipapatupad ang operasyon ng paghawak na walang pakikipagkuwentuhan sa buong proseso upang maiwasan ang kontaminasyon ng pisang deddal. Ang standard na proseso ng paglilinis ay hindi lamang nagpapahiwatig ng maayos na pag-install ng bagong lens, kundi pati na rin ang pundasyon ng pagpapanatili ng integridad ng optikal na sistema ng equipo, na direktang may ugnayan sa katumpakan ng laser cutting at sa kalidad ng surface treatment.
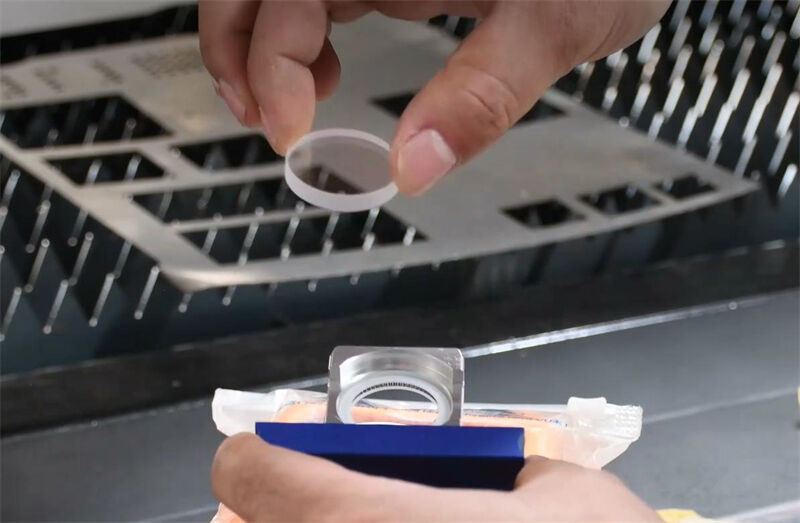
Paghuhusay at pamamahala ng laser cutting machine
Bukod sa pagsasalba ng mga lente, kailangan rin ang regular na paglilinis ng cutting head at iba pang bahagi ng iyong laser cutting machine upang panatilihin ang optimal na pagganap. Ang alikabok, dumi, at basura ay maaaring magdulot ng epekto sa proseso ng pag-cut at bumaba sa kasikatan.
Gumamit ng malambot na siklot upangalis ang basura mula sa cutting head at iba pang bahagi. Linisin nang regula ang nozzle at mga lente upang siguraduhin ang malinaw na daan ng laser beam.
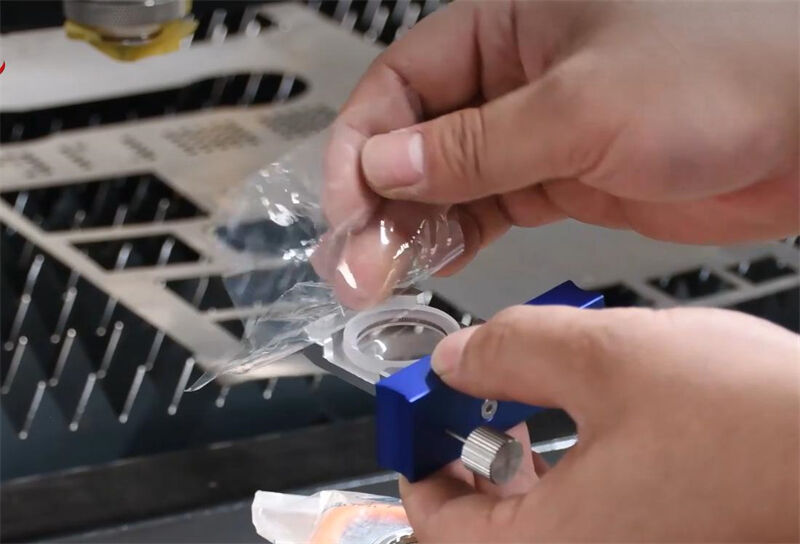
Gaano kadikit dapat maintindihan ang isang laser cutting machine?
Kinakailangan ang regular na pagsusuri at pamamahala sa mga laser cutting machine upang makapanatili silang tumatakbo nang maayos. Siguradong nagaganap ang makina nang mabuti, maiiwasan ang mahal na pagsasara, at siguraduhin ang mataas na kalidad ng mga cut. Kung hindi ito isinisiyasat nang regula, ang pagbagsak at pagputol sa mga pangunahing komponente ay maaaring magdulot ng mga isyu sa pagganap.
Ang bilis ng pamamahala ay nakakasalalay sa kung gaano kadikit ang paggamit ng makina at sa kapaligiran na nasaan ito. Ang mga makina na madalas gamitin o tumatahak sa mga kapaligiran na maangin at mainit ay kailangan ng mas madalas na pamamahala para sa laser cutting machine kaysa sa mga makina na tumatahak sa malinis, mas di-maangkin na mga kapaligiran.
Pamantayan na proseso ng pamamahala sa laser cutting equipment: Iyiniyakda na ipagawa ang buong inspeksyon at pagsisilbing malalim pagkatapos magtrabaho ng 200-500 oras ang aparato. Kumakatawan ang saklaw ng pamamahala sa mga pangunahing bahagi ng subsistem tulad ng yunit ng pagpapalaser, grupo ng lensa ng pagfokus, modul ng transmisyon ng beam at nozel ng auxilliary gas. Ang pagtutulak ng regular na pang-preventibong pamamahala ay maaaring epektibo na maabot ang maagang diagnoog ng mga problema at blokehin ang pagbabago ng mga potensyal na mode ng pagkabigo sa functional na pagkabigo.
Ang log ng pagsusustenta sa equipamento ay ang pangunahing instrumento sa pamamahala upang matiyak ang tunay na pagsubaybay sa oras ng operasyon at mabigyang-katwiran ang siklo ng pagsusustenta. Sa pamamagitan ng pagtatayo ng digital na mga file para sa pagsusustenta, maaaring iprograma nang sistematiko ang schedule ng pagsususustenta upang tiyakin ang kawalan ng oras ng pagsusustenta sa buong siklo ng buhay ng laser cutting equipment. Naroroon itong pangunahing papel sa pagpapahaba ng buhay ng serbisyo ng equipamento.
Buod
Ang pagsasagawa ng pamamahala sa laser cutting equipment sa buong siklo ng kanyang buhay ay ang pangunahing estratehiya upang siguruhin na matahimon ang mataas na pagganap ng equipment at iwasan ang hindi inaasahang pamamahala. Ang pagsisimula ng regular na pamamahala ay maaaring maabot ang tatlong teknikal na obhektibo: panatilihin ang katatagan ng operasyon ng equipment, kontrolin ang panganib ng pagsira ng sistemiko, at siguruhin ang tuloy-tuloy na katuturan ng pagproseso ayon sa mga estandar ng ISO 9013. Ang equipment na pinapatnubayan nang may wastong paraan ay matatagpuan sa taas na pagganap sa loob ng kanyang service life, nagbibigay sa mga kumpanya ng mga garanteng mabilis na ritmo ng produksyon at kontrol sa katutaran ng proseso.
Mga direksyon sa pamamahala ng optical system
Bilang pangunahing optikong elemento para sa pamamahala ng kalidad ng laser beam, ang regular na pagbabago/paglilinis/pag-inspeksyon ng grupo ng focusing lens ay bumubuo ng pangunahing nodong pang-maintenanceng sistema ng kagamitan. Ang depósito ng mga kontaminante at mikro-damay na ipinapakita ng lensa habang nagdurusa ng tuloy-tuloy na operasyon ay direktang magiging sanhi ng pagbaba ng katangian ng pagsasailalim ng beam. Ang pagtatatag ng isang sistema ng pagbabago ng lensa batay sa oras ng operasyon at ng isang proseso ng paglilinis na antas ng cleanroom ay ang unang teknikal na hakbang upang blokahan ang serye ng pagbaba ng kinakailangan ng kagamitan.
Mehanismo ng kolaboratibong maintenancesa maraming sistema
Habaan ang sakop ng pamamahala sa mga pangunahing subsystem tulad ng laser generators, thermal management systems, at beam conduction modules upang tiyakin na gumagana ang lahat ng mga yunit ng ayos sa loob ng disenyo parameter range. Ang pag-iwas sa pangunahing mga item ng pamamahala ay magiging sanhi ng pagsusumikad ng mga problema at maaaring malaking dagdagan ang gastos sa pamamahala ng buong siklo ng buhay. Ang pagsisimula ng isang preventive maintenance plan ay hindi lamang makakapagpahaba ng MTBF (mean time between failures) ng mga kagamitan, kundi pati ring tiyakin ang kontinuidad ng produksyon sa pamamagitan ng pagbibigay-buong panahon sa pagbukas at makasulong ng kabuuan ng equipment effectiveness (OEE).