Influencing Factors and Performance Evaluation of Laser Cutting
In the laser processing equipment market, laser cutting stands out as a pivotal application technology. In 2024, approximately 3,000 laser cutting machines were sold in China, demonstrating a growing trend of replacing traditional tools like shearers and punch presses. Following the widespread adoption of laser marking, the market for high-power laser cutting machines—characterized by high cutting speeds, precision, thick-plate capability, and large cutting formats—is poised for significant expansion.
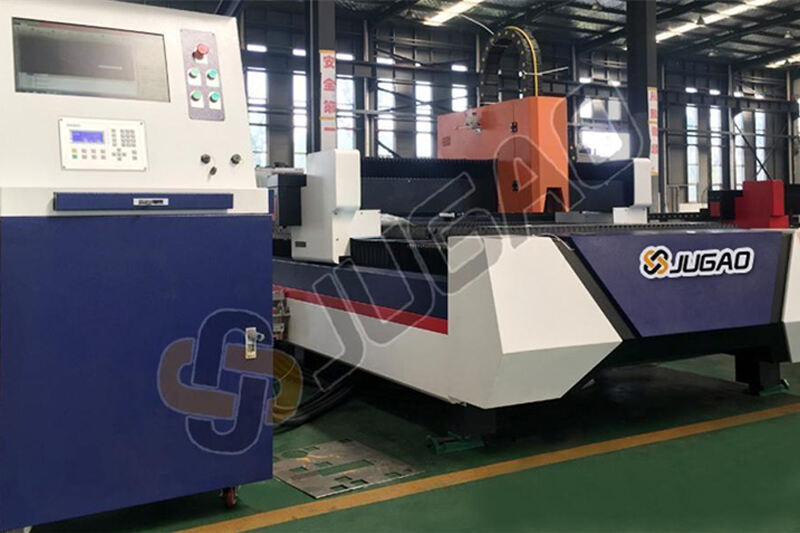
Key Factors Influencing Laser Cutting
During laser cutting, the laser beam emitted by the laser source is collimated and focused into a fine point (focal spot) by the cutting head's lens system. Operators must ensure the laser beam is precisely aligned with the nozzle and adjust the nozzle-to-material distance based on the material thickness. High-pressure gas is ejected from the nozzle, working in tandem with the laser beam to complete the cutting process. The primary influencing factors include:
1.Focal Spot Diameter
A smaller diameter results in a narrower cut but limits cutting thickness.
A larger diameter allows for thicker cuts but produces a wider kerf.
2.Focal Position
Determines the spot size on the material surface and the shape of the cut.
The optimal position depends on the material type and thickness.
3.Laser Power
Affects the maximum thickness of the material that can be cut.
Influences processing efficiency and the degree of thermal deformation.
4.Cutting Speed
Must be balanced with power and gas flow rate.
Too slow: incomplete cuts or excessive burrs.
Too fast: reduced cut quality or failure to penetrate.
5.Nozzle Diameter
Smaller nozzles are ideal for thin materials.
Larger nozzles are better suited for thick materials.
6.Assist Gas
Gas purity impacts burr formation and oxidation of the cut surface.
Thinner materials require higher gas pressure for effective cutting.
7.Beam Mode
Single-mode beams (below 1,500W) excel in thin-plate cutting.
Multi-mode beams (above 1,500W) offer a larger spot size and uniform energy distribution, making them suitable for thick-plate cutting.
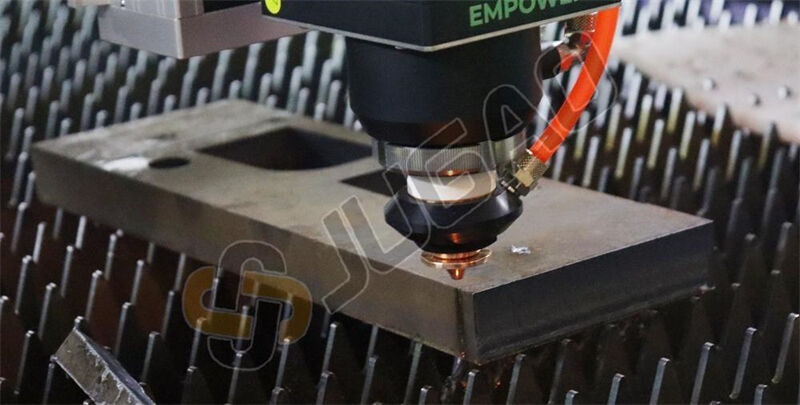
Performance Metrics for Laser Cutting
Laser cutting equipment meets the complex demands of industries such as automotive, aerospace, healthcare, plastics, electronics, and textiles by delivering high speed, precision, and quality. The effectiveness of laser cutting can be evaluated based on the following criteria:
1.Surface Roughness
The cut edge exhibits striations; shallower striations indicate lower roughness and a smoother surface.
Thinner materials generally yield lower roughness.
Nitrogen or argon gas produces smoother cuts compared to oxygen.
2.Cutting Perpendicularity
The focused beam's divergence causes variations in spot size along the material thickness, leading to deviations from a perfect 90° angle.
Thinner materials and higher beam quality improve perpendicularity.
The focal position relative to the material thickness also plays a critical role.
3.Burr Formation
High-quality cuts should be burr-free to minimize post-processing.
Burrs are influenced by process parameters, material type, and beam quality.
4.Thermal Deformation
As a thermal process, laser cutting inevitably induces material deformation.
Minimizing deformation is crucial, especially for thin materials.
Faster cutting speeds, narrower kerfs, and higher gas flow rates reduce deformation.
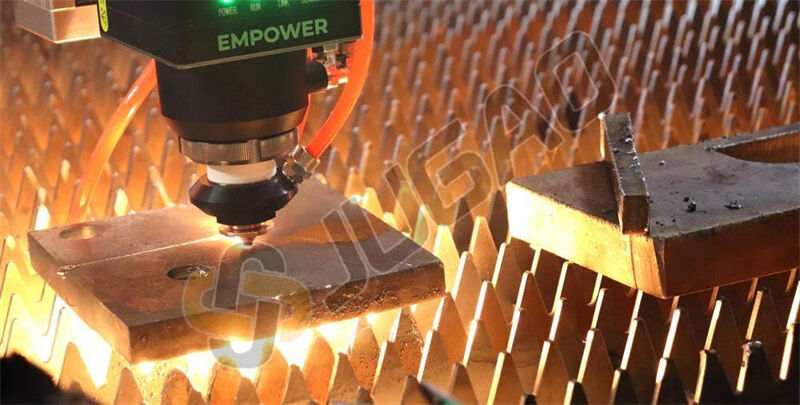
Applications and Equipment
Laser cutting is widely used for precision tasks such as:
Fine cutting of brass.
Cutting 304 stainless steel.
Carbon steel processing.
For example, JUGAO Laser's 500W–3000W single-mode continuous fiber lasers feature water cooling, high power, excellent beam quality, maintenance-free operation, and high electro-optical efficiency. These lasers are ideal for cutting, welding, and drilling metals like stainless steel, carbon steel, aluminum, and copper, with applications spanning sheet metal fabrication, hardware processing, appliance manufacturing, and automotive production.
JUGAO CNC MACHINE's main products include laser cutting machines, CNC hydraulic bending machines, laser welding machines, shearing machines and pipe bending machines, etc., which are used in sheet metal processing, chassis cabinets, lighting, mobile phones, 3C, kitchenware, bathroom, auto parts machining and hardware industries.Welcome to consult online to learn more about the machine information.