Press Brake Tooling
What is a bending machine die
Definition and main functions
A bending machine is a device used to bend metal sheets, which can transformblanks into parts with specific shapes and sizes under the pressure of thebending machine.
The bending machine die consists of a punch and a lower die, which cooperatewith each other for punching, forming and separation of metal sheets. The diefor forming has a cavity, and the die for separation has a cutting edge.
For beginners, it is necessary to understand that the main purpose of thebending machine die is to enable the machine to bend various metals intodifferent angles. In this process, a piece of metal sheet slides between twotools: the top tool (punch) descends to the bottom tool (die) to bend the metalsheet part.
Bending machine dies are divided into manual bending machine dies, hydraulicbending machine dies and CNC bending machine dies. Hydraulic bending machinedies can be divided into torsion axis synchronization, machine-hydraulicsynchronization and electro-hydraulic synchronization according to thesynchronization method. Hydraulic bending machine dies can be divided intoupward and downward types according to the movement method.
Importance in metal bending
Determine the bending form and dimensional accuracy: The shape and size ofthe mold can directly determine the bending form, such as angle, radius ofcurvature, etc., which is closely related to product quality.
Control the bending process: The tool can fix the metal plate in a specificposition and control its deformation under pressure to maintain the consistencyof the bending.
Improve production efficiency: By quickly changing the mold, the moldswitching of different products can be completed in a few milliseconds, whichgreatly shortens the switching cycle.
Extend service life: The service life of tools made of abrasive materials andsurface treated can be extended several times.
Reduce production costs: The use of precision molds can increase productivityand reduce the scrap rate caused by mold consumption.
Achieve specific requirements: Through CNC technology, the mold can be bentinto any shape to meet the manufacturing requirements of certain specificproducts.
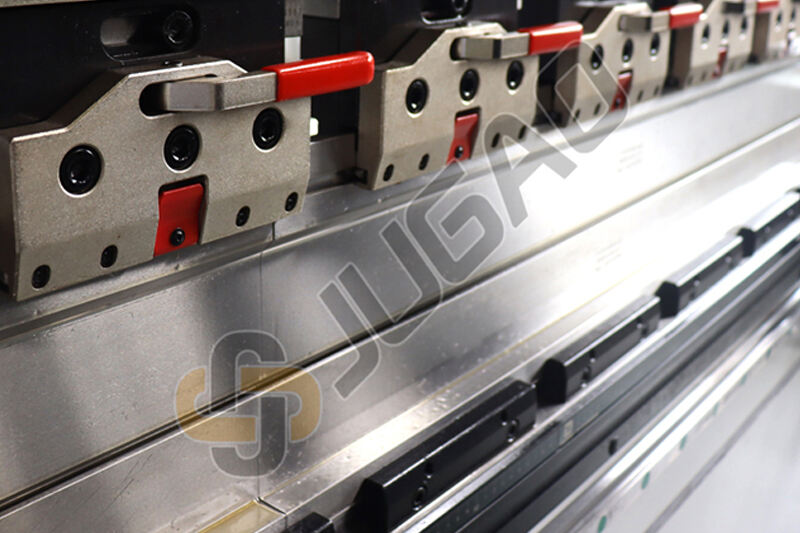
Press Brake Tool Assemblies
Punches and Dies
They are key components that determine the shape of the workpiece being bentand are mounted on the upper and lower pressure rods to control the deformationof the bending area of the metal sheet.
Die Bases
These platforms support and position the top punch and bottom die. They areconnected to the press brake punches to allow for quick tool changeover. Theyare particularly useful in maintaining consistency over multiple productionruns.
Bend Aids
To help operators quickly and easily complete bending tasks, some aids suchas angle measuring tools and locating blocks are sometimes used. These tools arevery important in high-precision applications where even small deviations canaffect the final product.
Quick Change Systems
Many modern press brakes are equipped with quick change systems that allowoperators to quickly change top punches and bottom dies to accommodate differentbending tasks.
This capability is critical for high-mix, low-volume production environmentswhere tools need to be changed frequently to accommodate different bendingtasks. For example, in a job shop environment, a quick change system enablesfast changeover between different projects, improving overall efficiency.
Locating Pins
They are used to accurately position and secure the workpiece in the dieduring the bending process. This is critical for repetitive work where the samebend must be replicated accurately.
Die Protectors
Die protectors are installed on the edge of the die to protect the sharpcorners of the workpiece and extend the life of the die. They are especiallyimportant when processing fragile or high-value materials.
Die Sockets
Connecting the die socket to the punch interface facilitates quickinstallation and removal of the die. This feature is beneficial in environmentswhere dies need to be changed quickly to maintain production efficiency.
Lubrication System
Evenly distribute lubricant into the radius of the die to reduce workpiecewear and burn.
Die Pads/Modules
They are used to support the tenon and help build the tool set. Rigidity isvery important.
Shims
Control the depth of the bend by keeping the distance between the bend facesconsistent.
Die Drifts
They are used to remove the bent part and can also be used for setup.
Tool Holders
Tool holders mount the die to the press brake. Modern tool holders often havequick-change mechanisms that increase productivity by reducing setup time. Forexample, in a high-mix production environment, quick-change tool holders allowoperators to quickly switch between different tools, minimizing downtime.
Clamping systems
Clamping systems typically use clamps, clamping blocks and adjusting nuts tohold punches and dies in the correct position. Secure clamping is essential toprevent the tool from moving during the bending process, which can cause errors.For example, when bending high-strength steel, a strong clamping system ensuresthat the die remains stable under high pressure.
Types of Press Brake Tooling
Punches Profiles
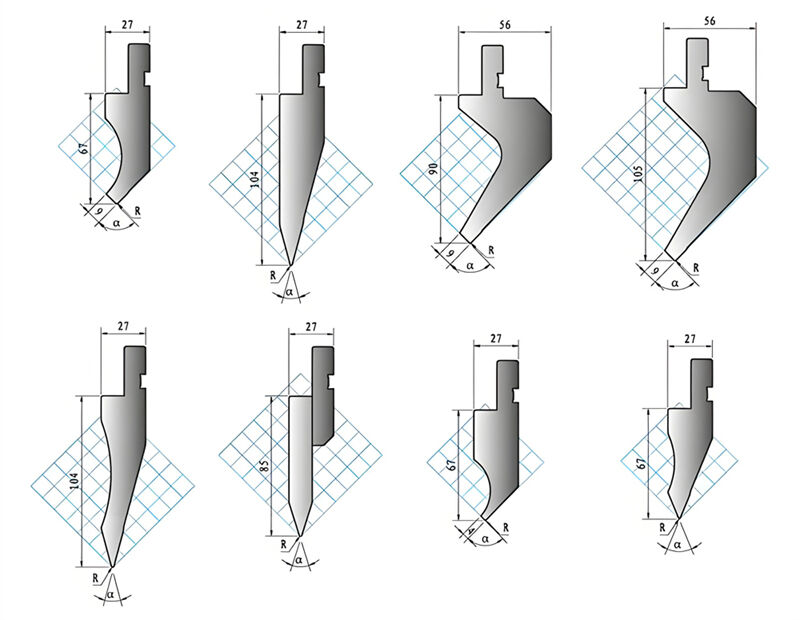
The punch is the upper tool in the press brake tooling and is mounted on theslide of the press brake. It applies force to the workpiece to bend it in theshape of the punch. Punches are available in various designs to suit differentsheet metal bending requirements and material types.
Standard Punches
Standard punches feature a thick body and narrow tip and are versatile andare often used for general bending tasks and high tonnage applications. They aresuitable for making standard bends such as 90-degree angles on a variety ofmaterials. For example, a standard punch can be used to make a right-angle bendon mild steel sheet, ensuring consistent results on multiple workpieces.
Sharp Angle Upper Die
The sharp angle punch is used for angles between 30-60 degrees and has aheavy body and a sharp tip. It is usually used for bends less than 30 degreesand can handle angles up to 89 degrees. The angle of the punch tip is usuallybetween 28° and 34°.
Typical Dimensions
Clearance Width: Varies from 1" to 1.5"
Working Height: Typically about 3.75"
Tip Radius: Varies from 1/32" to 1/8"
Gooseneck Punches
Gooseneck punches have a recessed profile that allows for complex bendswithout disturbing the workpiece. Designed for U-profiles, these punches areideal for deep boxes and other complex shapes. Gooseneck punches have anelongated body with a recessed area to prevent the legs of the workpiece fromcolliding. For example, when making a deep U-shaped groove in sheet metal, agooseneck punch provides the necessary clearance to avoid damaging thematerial.
Window Frame Punches
Window frame punches feature a narrow body and an angled tip that allows forbending and working around corners. The tip curves inwards of the bender. It canbe angled on both sides of the bend and is often used to make door frames andwindow sashes, and can effectively process sheet metal for window framemanufacturing.
Narrow/Sword Punches
With uniform thickness throughout the length, the geometry of narrow punchesis straight with no corners, making them suitable for situations where clearanceis tight, ideal for final bends in box closures, and suitable for operations inlimited spaces.
Radius Top Punches
The top radius punch has a rounded tip rather than a sharp edge, so it isdesigned to make rounded bends and can be used with standard V-dies for markingoperations and to make smooth curved profiles. The body is usually thicker towithstand the required bending forces.
Joggle Punches (Z Tools)
The Joggle punch has a specialized shape that produces offset bends and isused in special applications to produce S-shaped profiles. It is a special tool,usually used for specific custom work, designed to make two bends at the sametime. It has a thinner profile than a standard punch.
Lower Die
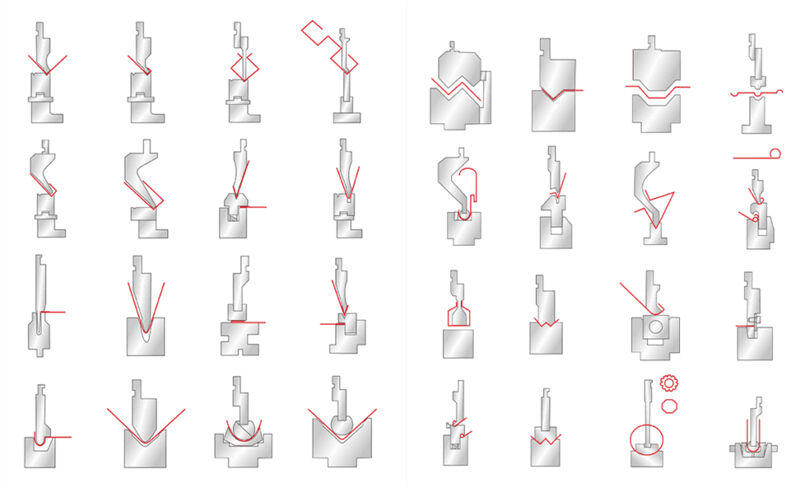
The lower die is the lower tool in the press brake die and is installed onthe bed of the press brake. When the punch is pressed down, it provides thereaction force required to form the metal. Dies come in various shapes and sizesto make different types of bends.
V-die
The V-die is the most common type of die and is available in single V, doubleV and multi-V shapes. It features a shaped groove. It is used to make V-shapedbends in workpieces. The width and depth of the V-groove determine the finalbend angle and arc. It is available as part of a four-way module for easyreplacement
U-die
U" dies are used to make channels and deeper bends and are ideal foroperations that require more complex shapes. Designed for making U- or C-shapedbends, this die can make bends from 90° to 180°. For example, to form deepgrooves in metal sheets for structural parts, "U" dies ensure uniformity andstrength.
Flattening dies
Flattening dies are used to flatten the bent material to ensure a smooth andpolished finish. These dies are essential to achieving a professional look forthe final product, such as flat metal sheets used to produce automotive bodyparts.
Offset dies
Offset dies are used to make Z shaped or offset bends and produce two anglesin one stroke. They improve accuracy by keeping the bends parallel.
Radius Dies
Radius dies are used in conjunction with round punches to form radius bends,resulting in a smooth, curved profile.
Gooseneck Dies
The gooseneck die is designed to avoid workpiece interference, allowing bendsto be made in tight spaces or around existing bends. It is primarily used toremove protruding edges or flanges on the workpiece and is ideal for bendingdeep box or high flange profiles.
Flanging Dies
Flanging dies are used to create hems or hems that improve aesthetics andstrengthen the edges of sheet metal parts.
Groove Forming Dies
Channeling dies form U-shaped channels in one stroke, which is more efficientthan forming U-shaped channels with traditional V-shaped dies.
Flattening Dies
Flattening dies are used to completely flatten sharp angled bends and areoften used in conjunction with hemming operations.
Four-Way Dies
Four-Way dies feature a V-shaped channel with different sizes on each side ofa single die. Multiple bend dies are used to produce two or more bends in oneoperation and include special types such as offset dies.
Types of bending machine molds
Tooltype |
Features |
Application |
Advantage |
Americantools |
-With 30 degree acute angles on both the punch and the die. |
-Suitable for bending operations on a variety of material thicknesses andprofiles. |
-Durable and reliable, it can be used for various tasks. |
Europeanprecision tools |
-Known as the "Promecam" tool. |
-Suitable for high-precision bending applications with high accuracyrequirements. |
-Reduce the rebound caused by acute angles, improve bending accuracy. |
NewStandard Tool |
-Combines the characteristics of both the United States and Europe. - The punchand die have a 45-degree sharp angle. - Compatible with bending machines in theUnited States and Europe. |
-Suitable for various bending requirements. - Popular in production environmentsthat require precision and flexibility. |
-Rapid tool changes enhance operational efficiency. -Balancing versatility and precision, suitable for a variety of projects withoutthe need for extensive modifications to the machine. |
VelatonRapid Tooling |
-Typically used for TruPunch systems - High precision, smalltolerance |
-Primarily used for high-precision stamping tasks, such as processing precisioncomponents. -Suitable for production needs that require precise and frequent toolchanges. |
-High precision, high degree of standardization, rapid tool change. -Longer tool life, higher precision. -Strong tool compatibility, suitable for various types of machinetools. |
In conclusion
The Wila quick-change tooling system is mainly used in situations thatrequire high precision and frequent tool changes, allowing for rapid toolreplacement and is suitable for the machining of precision components.
The characteristics of American molds are low cost and large productionscale, suitable for mass production with lower precision requirements.
European molds emphasize precision and stability, suitable for industrieswith high precision requirements such as automobiles, electronics, andaerospace.
The new standard tools possess strong compatibility and adaptability,enabling rapid adjustments and improvements in production efficiency acrossvarious environments.
Material Selection for Press Brake Dies
The efficiency and lifespan of bending dies are intrinsically linked to thestrength and material of the die. Due to the significant pressure and abrasivesgenerated during the bending process, the composition and treatment of the dieare crucial.
The importance of high strength and wear resistance
Bending machine tools can withstand strict pressure during operation. Highstrength ensures that the tools will not deform or break when providingpressure.
Furthermore, wear resistance is crucial as it determines the service life ofthe user. Wear-resistant tools can maintain their shape and function over thelong term, ensuring consistent bending effects and reducing the need for regularreplacements.
Hardened tools
One method to improve the rigidity and durability of a bending machine isthrough hardening the dies. Specific materials for bending machine dies arepopular due to their initial rigidity and the ability to further hardenthem.
For example
Chromium-Molybdenum Steel: This alloy is renowned for its toughness andwear resistance, achieving a balance between the strength and durability of thebending machine, ensuring that the tool can withstand heavy bending operationswithout premature wear.
Yasuki steel: yasuki steel is a high-grade steel commonly used forspecialized tools, renowned for its exceptional hardness and abrasiveness. Itscomposition maintains sharp edges, making it the ideal choice for precision andbending tasks.
Hot refining tools
Tempering or heat treatment is a process that enhances the properties ofmetal tools. By subjecting metal to controlled heating and cooling cycles, itchanges its molecular structure, thereby improving its performance.
For example
After heat treatment, the strength and wear resistance of carbon steel areimproved. The heat treatment process refines the grain structure of the steel,making it more solid and durable. Carbon steel tools, after tempering treatment,are less prone to cracking and deformation, ensuring a longer tool life andconsistent bending effect.
Tool handling and installation
The operating efficiency of a press brake depends on the quality of the tool,but also on how the tool is handled and installed. Proper handling andinstallation can maintain optimal performance, reduce wear and extend the lifeof the tool. Here are the nuances of tool handling and installation:
The importance of mold geometry
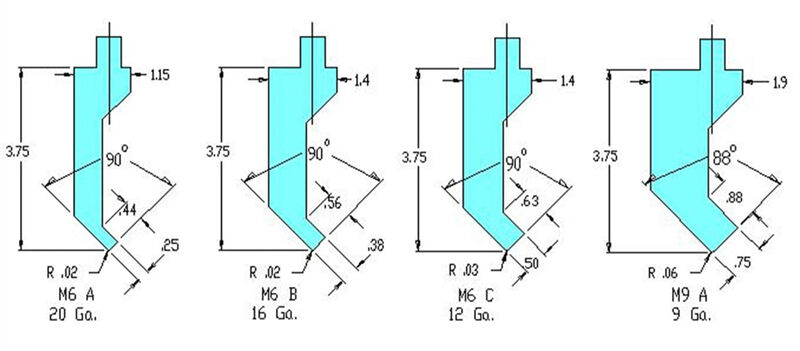
To achieve the bending effect, complex designs are typically made for thegeometry of the bending dies. The shape, angle, and dimensions of each die arecrucial for ensuring the accuracy of the bending process. When handling andinstalling these tools,
Ensure that the geometry of the tool is consistent with the expectedbending operation. Using a tool with incorrect geometry may result in inaccuratebending results and can damage the machine tool and workpiece.
Regularly inspect the mold for wear or damage. Over time, the geometricshape of the mold will change due to wear, thereby affecting the bendingquality.
Proper storage is crucial. When storing tools, their geometric shape shouldbe maintained, avoiding stacking or placing them in positions that could causedeformation.
Segmented molds and their advantages
Segmented tools are tools that are divided into many parts or sections.Rather than just long tools, segmented tools allow press brake operators to usea combination of shorter tool segments to achieve the desired length or setup.The advantages are as follows:
Flexibility: Segmented tools have stronger versatility, operators can matchsegments according to the specific requirements of the program.
Easy to operate: Compared with longer tools, shorter tools are easier tooperate, install, and repair.
Reduce wear: If specific components of the mold are worn or damaged, thesecomponents should be replaced instead of the entire mold.
Cost-effectiveness: Operators can invest in a segmented group rather thanmultiple long tools for different operations, thereby reducing long-termcosts.
Optimized work procedures: Segmental tools can be quickly reset, therebyreducing setup time and increasing productivity.
The Importance of Tool Tolerances
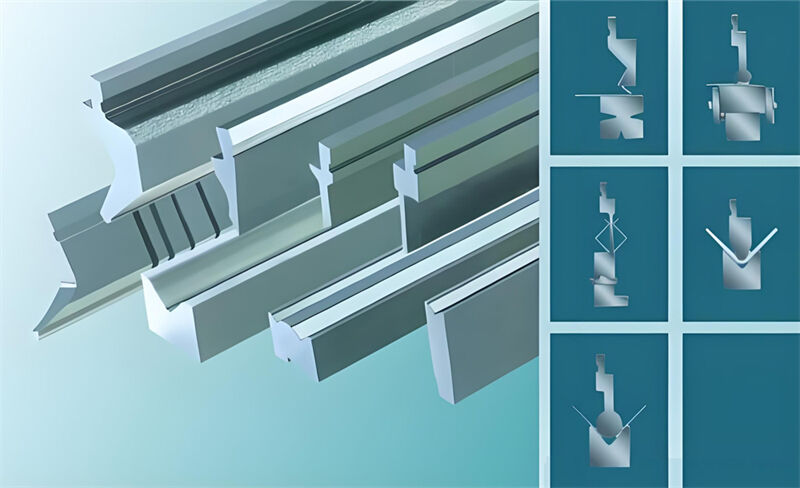
Mold tolerances are crucial in production as they determine the normaloperation of the product, the measurement range of aesthetic containers, orother physical characteristics. The main reasons for their importance are asfollows:
Improved component fit and function: This tolerance ensures that parts fitwith other parts, avoiding functional issues and incompatibilities.
Enhance the final product outlook Tolerances: Tolerances contribute to theaesthetics of the product, such as ensuring parts are level without noticeablegaps.
Consider reasonable latitude Tool tolerances: Tool tolerances can be allowedwhile maintaining their functionality.
Part interchangeability: Tolerances allow for replacement of a single part,facilitating maintenance and repair.
Definition of tolerances for consistency, accuracy and precision: Thedefinition of tolerances allows for better control of the consistency, accuracyand precision of the product.
Reduce costs: By defining tolerances upfront, manufacturers can minimizecostly manufacturing errors and rework.
Frequently Asked Questions
1. What is the main difference between precision ground and non-precisionground tools?
Precision ground dies are manufactured to extremely tight tolerances,ensuring high accuracy and consistency across the entire set of dies. This levelof accuracy is critical for applications that require precise angles andrepeatability, such as industries such as aerospace or medical devicemanufacturing.
Non-precision ground tools, while less expensive, have smaller tolerances andare generally suitable for applications where accuracy is not as critical.Choosing between these options depends on production requirements, withprecision ground tools being more desirable for high-precision tasks thatrequire consistency.
2. How often should press brake tools be calibrated?
The frequency of calibration depends on production volume, material type, andaccuracy requirements. For high-precision applications or continuous productionenvironments, calibration should be performed weekly or even daily, as thisensures consistent bending accuracy and minimizes potential deviations.
In less intensive operations, monthly or quarterly calibrations may besufficient. Establishing a regular calibration program that aligns withproduction needs can help maintain accuracy and reduce rework or waste.
3. What factors affect the life of press brake tools?
Many factors affect tool life, including material quality, intensity of use,workpiece material hardness, and maintenance methods. Press brake tools that usehigh-grade tool steels or are treated with special coatings generally lastlonger, especially in high-volume production environments.
Regular cleaning, lubrication, and inspection can also prevent prematurewear, which can greatly extend the life of the tool. In addition, avoidingexcessive tonnage and following recommended operating guidelines can protect thetool from excessive stress and extend its service life.
4. Can press brake tools be used for all types of metals?
Although press brake tools are widely used, different metals require specifictool characteristics to ensure optimal performance. For example, harder metalssuch as stainless steel or titanium exert more force on the die, sohigh-strength or carbide-coated dies are ideal for these applications.
Softer metals, such as aluminum, require less die strength, but softer diesor punches can be used to prevent surface damage. Matching the die to thematerial type optimizes die life and bend quality, improving the overallefficiency of the press brake operation.
5. How do I choose the right press brake tool for my project?
First, consider the material's characteristics, including type, tensilestrength, and yield strength, as these will determine the specific toolingneeds. Different materials, such as aluminum, carbon steel, and stainless steel,have unique properties that require different adjustments.
Then, evaluate the material's thickness and length. The die opening shouldgenerally be 8 times the material's thickness. The length of the material willdetermine the required die length. Bend angle and shape are critical. Specificbend shapes, such as V-bends or hemming, require corresponding tooling. Knowingthe required bend shape can help you select the correct die.
Tool profile and load limit are also critical. Match the tool profile to thetype of work, whether it's an air bend, bottom bend, or coin bend, and ensurethe load limit does not exceed the press brake's capabilities to avoiddamage.
Die selection should be consistent with the thickness of the metal involved.Use the "8×2 rule" and multiply the thinnest metal by 8 to find the smallestV-shaped die required. Adjustable dies are useful for projects with multiplebends.
When selecting a punch, choose based on the requirements of the job. Considerthe punch type, such as standard, gooseneck, or sharp-angle, and make sure thenose radius matches the pneumatic forming radius value.
Precision and compatibility are important to achieve part accuracy. Choosetools with high precision and features such as segmented and self-retainingmounting for convenience and safety. Consider tool options and customization.While standard tools are suitable for common bends, custom tools may be requiredto meet unique specifications to improve forming efficiency.
Finally, pay attention to setup and operation. Tools that allow front loadingcan reduce setup time. For projects that require frequent tool changes,equipping each press brake with a dedicated tool library can improveefficiency.