Precautions for laser cutting machine layout
With the rapid development of the market economy and the rapid development of science and technology, laser cutting technology has been widely used in the fields of automobiles, machinery, electricity, hardware and electrical appliances. Generally, before using the laser cutting machine, we will import the prepared drawings into the program, and then use the layout team to arrange the graphics on a board, so that the laser cutting machine can batch process the products. Although the layout process is very short, there is a lot of knowledge hidden in it. If the layout is slightly wrong, it will have a great impact on the cutting effect of the entire board.
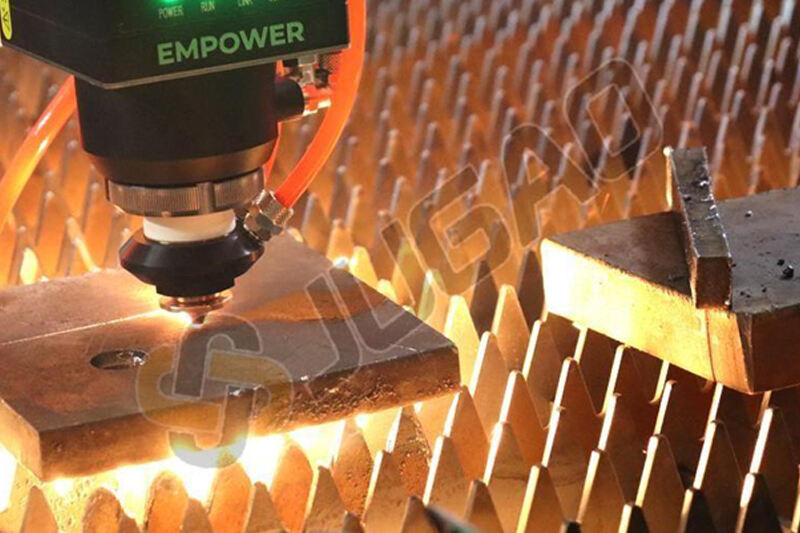
The following matters need to be paid attention to during layout:
1. Corner melting
When slowing down the cutting of the corner of the thin steel plate, the laser will melt the corner due to overheating, and generate a small radius at the corner to maintain the high-speed cutting of the laser, avoid overheating and melting of the steel plate when cutting the corner, so as to obtain good cutting quality, reduce cutting time and improve productivity.
2. Part spacing
In general, when cutting thick plates and hot plates, the spacing between parts should be large, because the heat of thick plates and hot plates has a greater impact. When cutting corners, sharp corners and small graphics, it is easy to burn the edges, affecting the cutting quality.
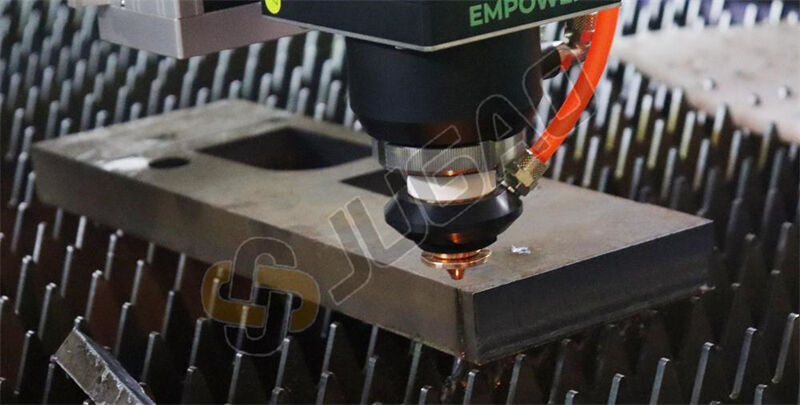
3. Lead setting
In the process of cutting thicker plates, in order to make the cutting seam connect well and prevent burns at the beginning and end, a transition line is often drawn at the beginning and end of the cutting, which are called lead and tail respectively. Lead and tail are useless to the workpiece itself, so they should be arranged outside the workpiece range. At the same time, be careful not to set the lead at sharp corners and other places where heat is not easy to dissipate. The connection between the lead and the cutting seam should be made into a circular arc transition as much as possible to make the machine move smoothly and avoid burns caused by corner pauses.
4. Common edge cutting
Combining two or more parts into a common edge, large quantities of regular graphics should be used as much as possible. Common edge cutting can greatly shorten the cutting time and save raw materials.
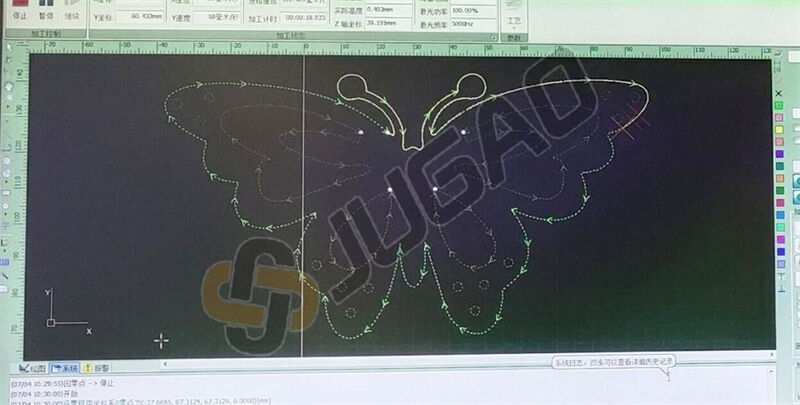
5. Parts collision
In order to maximize production efficiency, many laser cutting equipment are operated continuously for 24 hours and use unmanned automation/unloading devices. They may damage the cutting head and interrupt production when they hit the overturned parts after cutting, resulting in great losses. This requires that you should pay attention to choosing the appropriate cutting path when sorting, detour the parts that have been cut, reduce collisions, choose the best cutting route, reduce cutting time, and automatically or manually combine multiple small parts with tiny connections. After cutting, the unloaded parts can easily disconnect the tiny connections.
6. Residual material processing
After cutting the parts, the skeleton-like residual material on the workbench of the laser cutting equipment needs to be removed as soon as possible to facilitate subsequent cutting operations. For laser cutting equipment without automatic unloading devices, the skeleton-like residual material can be cut into small pieces for quick removal, thereby avoiding personal injury to the operator caused by moving heavy and sharp-edged residual materials.
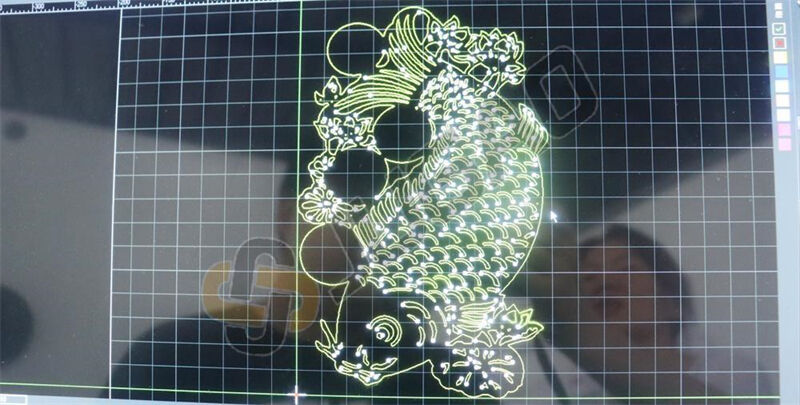
The above are some precautions when typesetting with laser cutting machines. JUGAO CNC MACHINE's main products include laser cutting machines, CNC hydraulic bending machines, laser welding machines, shearing machines and pipe bending machines, etc., which are used in sheet metal processing, chassis cabinets, lighting, mobile phones, 3C, kitchenware, bathroom, auto parts machining and hardware industries.Welcome to consult online to learn more about the machine information.