How to choose the right bending machine for small batch production?
In the field of metal processing, bending machines are key equipment for
sheet metal forming. For small batch production needs, how to choose a machine
that can meet the requirements of precise processing and has efficient and
flexible characteristics is a problem faced by many companies. This article will
deeply analyze the key points of purchase to help you find the solution that
best matches your production needs.
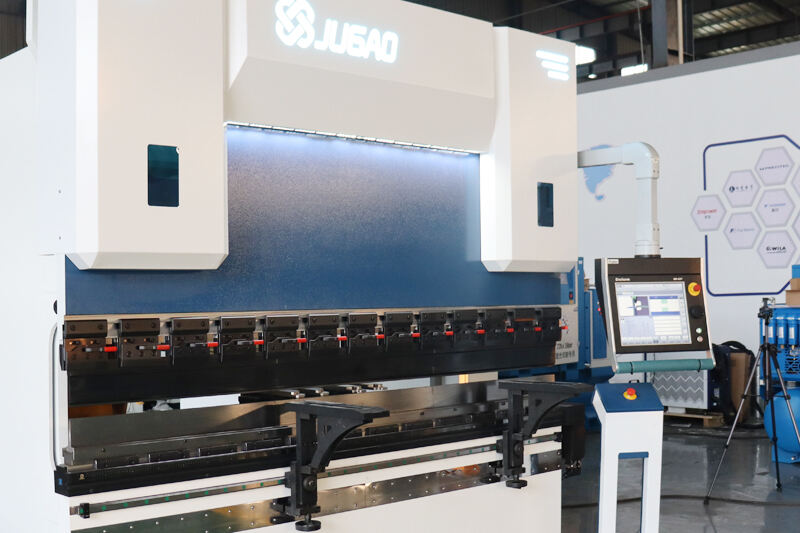
Basics of bending machines for small batch production
Modern bending machines have developed from traditional mechanical types to precision equipment that integrates CNC technology, hydraulic transmission and intelligent control. In view of the characteristics of small-batch production, the ideal equipment should have three core characteristics: fast mold change capability (complete mold change within 15 minutes), ±0.1° angle repeatability, and processing adaptability to support a variety of materials (such as stainless steel, aluminum alloy, carbon steel). This type of equipment is usually equipped with a modular mold system, which can greatly reduce the unit cost of small-batch production.
Key factors for selecting small-batch bending machines
Equipment size and processing capacity
It is recommended to select small and medium-sized equipment with a workbench length of 4-6 meters and a nominal pressure of 100-250 tons. For example, when processing stainless steel plates below 2mm, a 160-ton press model can meet the needs and save 30% of the floor space. Key parameter matching formula: Required pressure (tons) = (8×tensile strength×plate thickness²×expanded length)/(lower die opening×1.33)
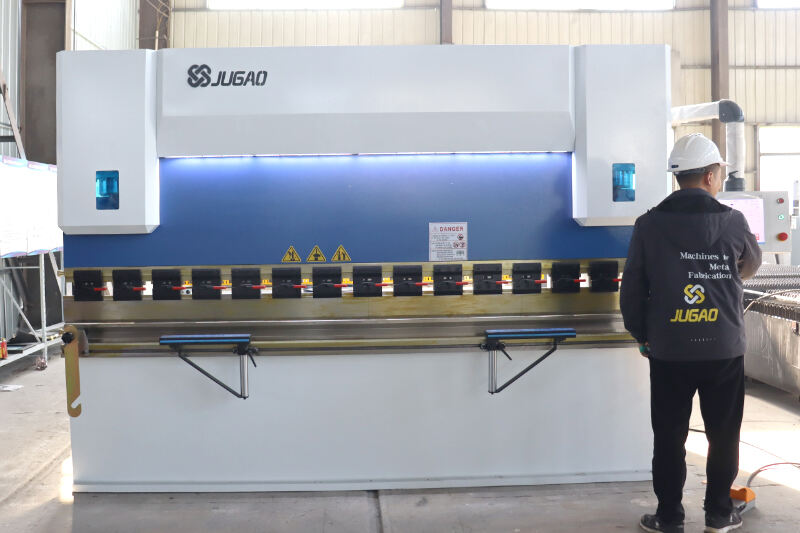
Accuracy and repeatability
The new generation of electro-hydraulic servo system with laser real-time detection device can control the angle error within ±0.05°. It is recommended to choose a model equipped with a high-precision control system such as DELEM DA-69T or ESA S640, which has an automatic deflection compensation function and is particularly suitable for precision parts processing with high consistency requirements.
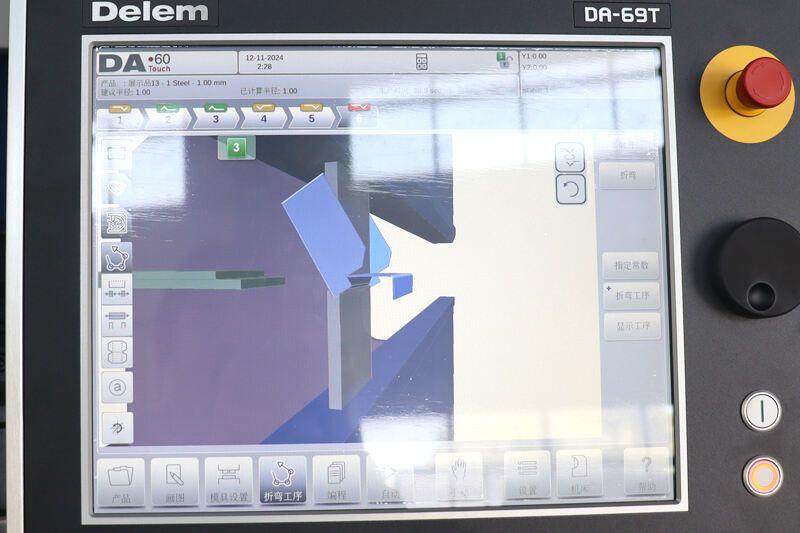
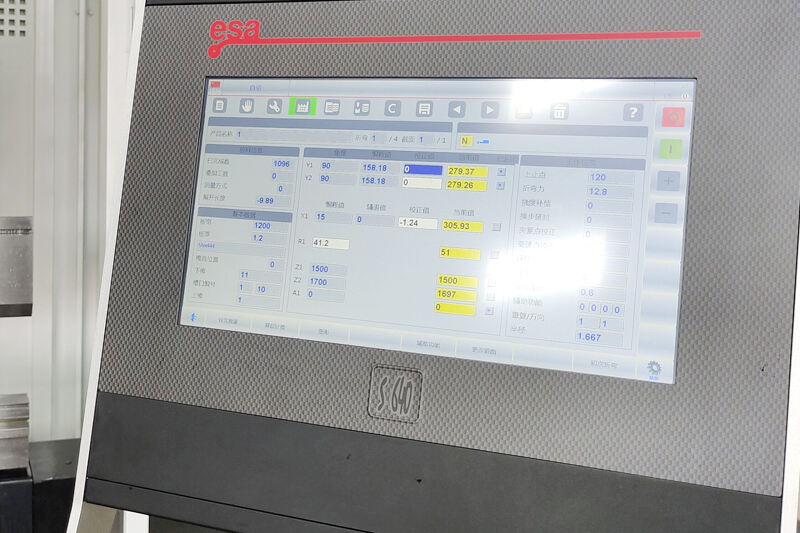
Operational convenience and debugging efficiency
Equipment with the following features can improve efficiency by more than 40%:
- Touch-screen human-machine interface (HMI)
- Mold automatic recognition system
- 3D graphical programming
- Process parameter database
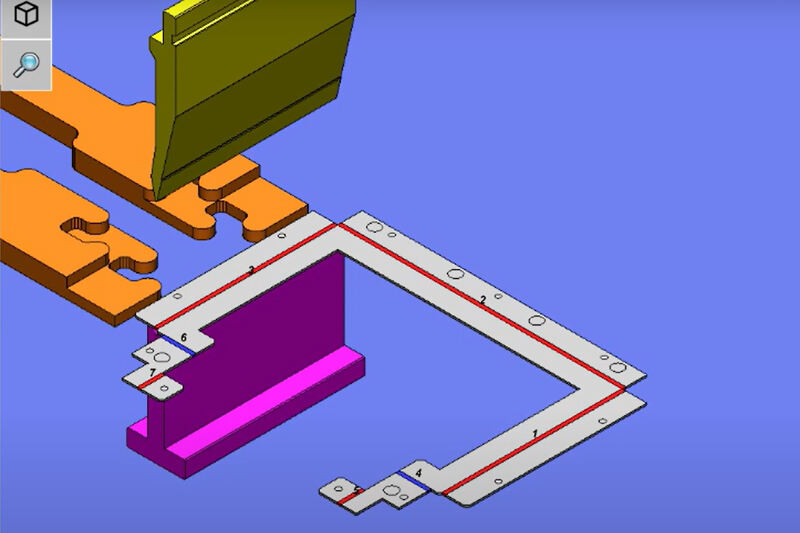
Customization and versatility
Multi-axis backgauge system (at least X1/X2/R three axes) with adjustable segmented upper mold can realize the processing of complex special-shaped parts. Some high-end models also support:
- Automatic mold library management
- Bending sequence optimization algorithm
- Remote diagnosis function
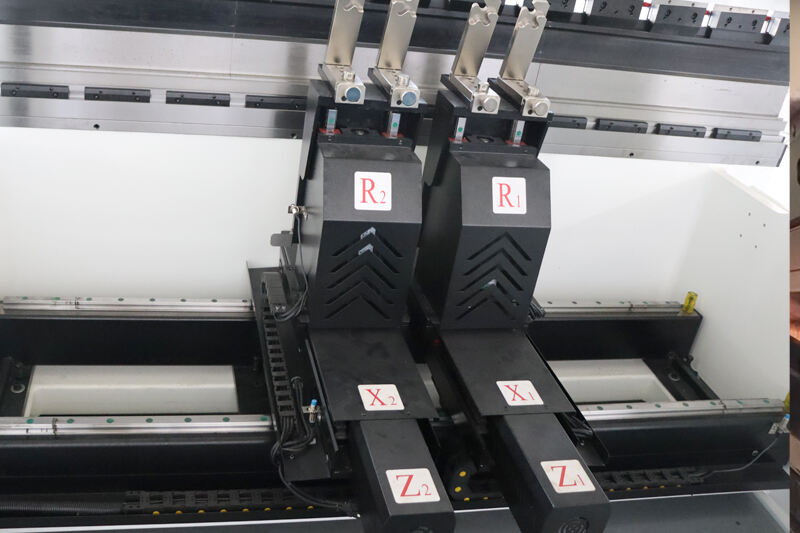
Recommended bending machine models suitable for small batch production
Intelligent CNC bending machine
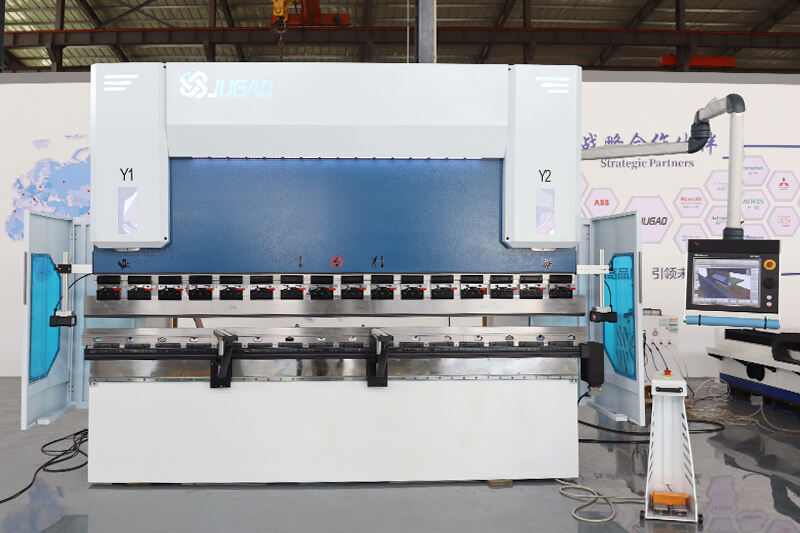
Core advantages:
Equipped with AI process optimization system
Support offline programming (compatible with SolidWorks files)
Servo drive technology with 25% energy consumption reduction
Standard safety light curtain and two-hand operation protection
Hydraulic bending machine
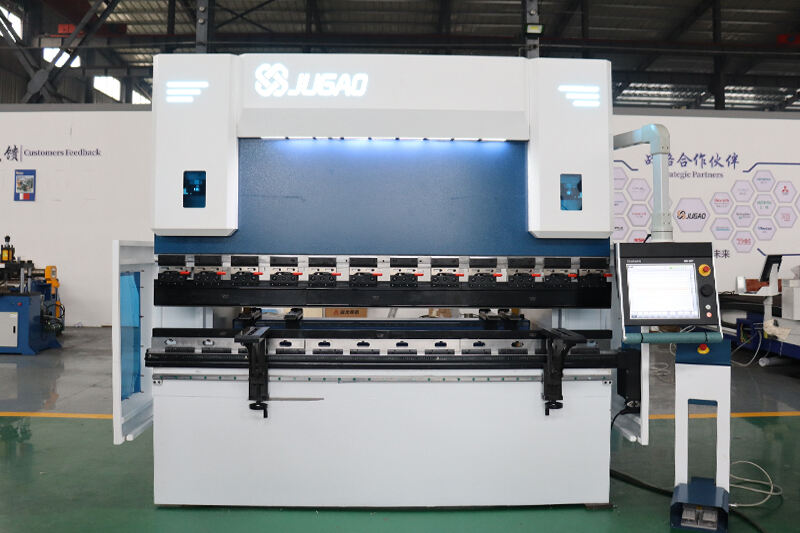
Outstanding features:
Dual cylinder synchronization accuracy of 0.02mm
Optional automatic mold change device
Economical solution (price is about 60% of CNC models)
Low maintenance cost
FAQ
Which bending machine is most suitable for small batch production?
It is recommended to give priority to CNC models equipped with servo motor drive. Taking the 304 stainless steel chassis with a processing capacity of 500 pieces/month as an example, the recommended configuration is:
200 tons of pressure
6-axis rear positioning
With mold compensation function
Programming storage capacity ≥ 500 groups
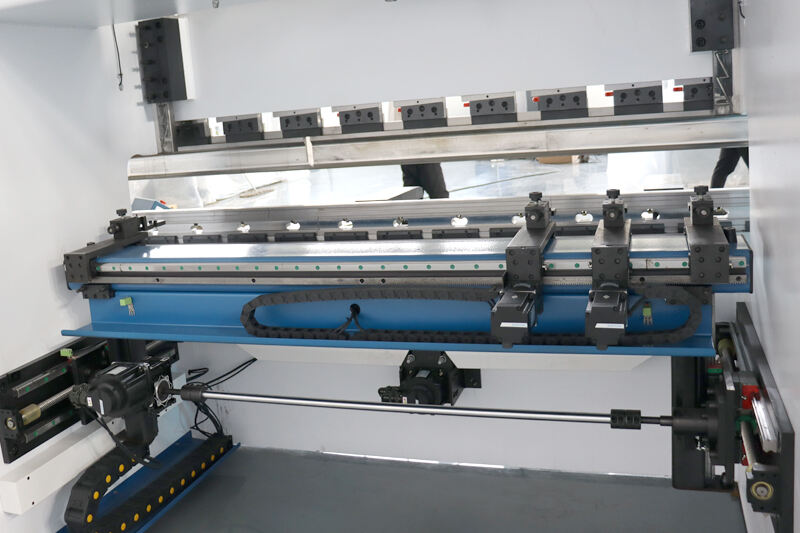
How to ensure accurate debugging of the bending machine?
Implement the "5-step calibration method":
Use a 0.02mm/m level to adjust the machine body
Laser detection of slider parallelism (error ≤ 0.05mm)
Repeated positioning test of the back stop (3 measurement deviations < 0.03mm)
Trial folding verification (at least 5 key dimensions must be measured for the first piece inspection)
Parameter archiving (establish a process card system)
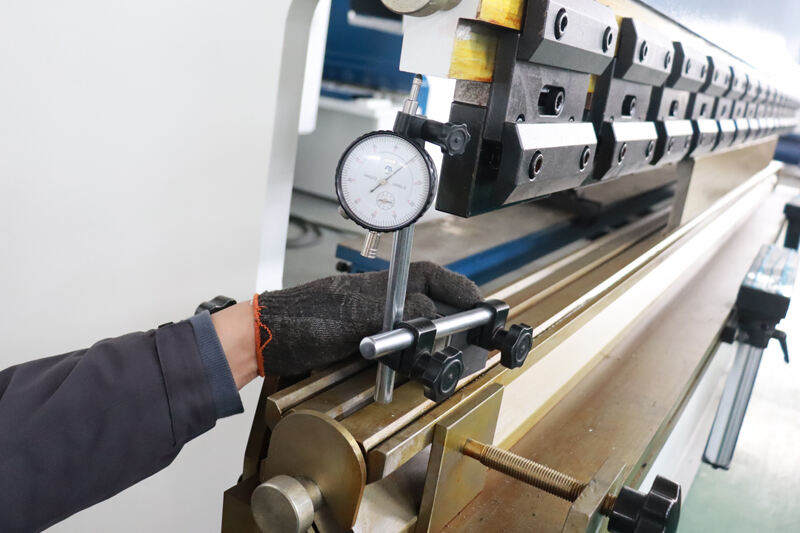
Maintenance frequency of small batch production bending machines?
The following maintenance plan is recommended:
Daily: Guide rail lubrication check + air line drainage
Monthly: Hydraulic oil contamination detection (NAS level 9 or less)
Quarterly: Servo motor encoder calibration
Every 2000 hours: Comprehensive preventive maintenance (including seal replacement)
Summary
When selecting a bending machine for small-batch production, it is recommended to adopt the "3+2" evaluation method: focus on the three core indicators of accuracy level, changeover efficiency, and expansion capability, while taking into account the two auxiliary dimensions of energy consumption level and after-sales service. Modern bending equipment has developed many functions optimized for small-batch production, such as adaptive bending technology, virtual mold trial system, etc. These innovations can significantly improve the comprehensive benefits of small-batch production. When actually purchasing, it is recommended to arrange on-site trial processing to verify whether the actual performance of the equipment meets specific process requirements.