Optimizing Press Brake Productivity: A Performance Assessment Framework
In today's competitive metal fabrication landscape, press brake productivity directly impacts operational profitability and market responsiveness. This in-depth analysis presents a systematic approach to evaluating and enhancing press brake performance, combining technical metrics with operational best practices to drive measurable improvements in your manufacturing processes.
Critical Productivity Determinants for Press Brake Operations
1. Operational Efficiency Metrics
Modern press brake performance assessment requires monitoring three key indicators:
Cycle Time Analysis: Track actual bending cycles against theoretical machine capacity
Quality Yield Rates: Measure first-pass yield versus rework percentages
Energy Consumption Patterns: Monitor power usage per production unit
Advanced CNC models now incorporate built-in analytics dashboards that provide real-time OEE (Overall Equipment Effectiveness) scores, enabling data-driven decision making.
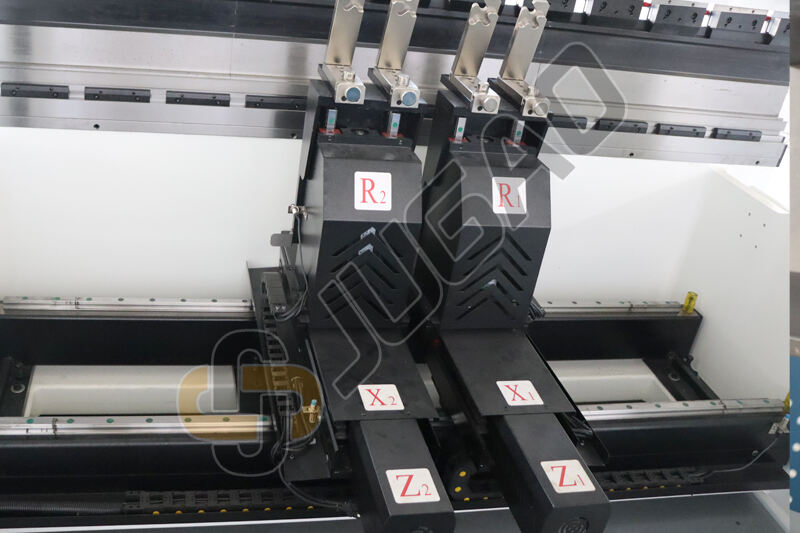
2. Workflow Optimization Strategies
Workflow Optimization
Implement lean manufacturing principles to eliminate non-value-added activities:
SMED (Single-Minute Exchange of Die) Techniques: Reduce tooling changeovers to under 10 minutes
Material Flow Mapping: Reorganize shop floor layouts to minimize handling distances
Digital Job Tracking: Implement MES systems for real-time production monitoring
These methods typically achieve 25-40% improvements in operational throughput.
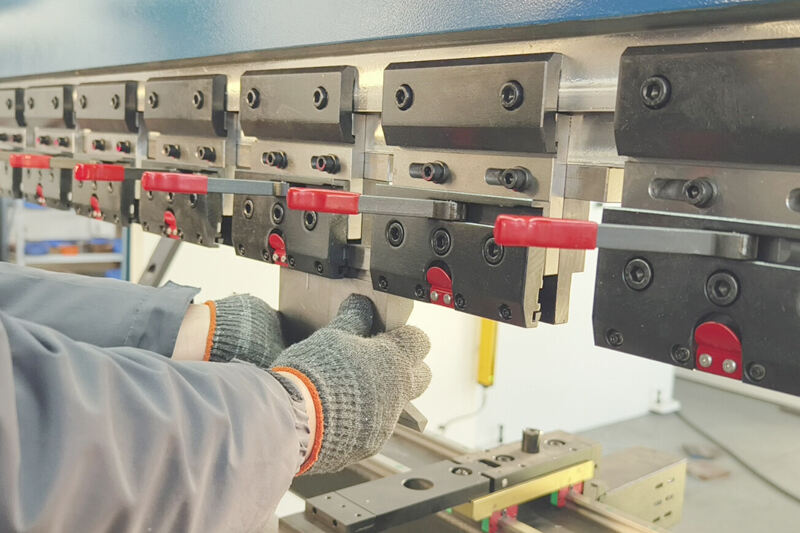
3. Human Capital Development
Operator Training
Develop a tiered skills certification program covering:
Basic machine operation (Level 1)
Advanced troubleshooting (Level 2)
Process optimization (Level 3)
Cross-training operators on multiple machines creates workforce flexibility that can reduce downtime by up to 30% during shift changes or absences.
Advanced Techniques for Performance Enhancement
1. Predictive Maintenance Systems
Transition from scheduled maintenance to condition-based monitoring:
Vibration analysis for ram alignment
Hydraulic fluid quality sensors
Thermal imaging of electrical components
These technologies can predict 85% of potential failures before they cause unscheduled downtime.
2. Smart Automation Integration
Automation Solutions
Evaluate automation opportunities across three levels:
Basic Automation: Automatic tool changers
Intermediate Systems: Robotic material handling
Advanced Solutions: AI-driven adaptive bending
ROI analysis typically shows payback periods of 12-18 months for comprehensive automation packages.
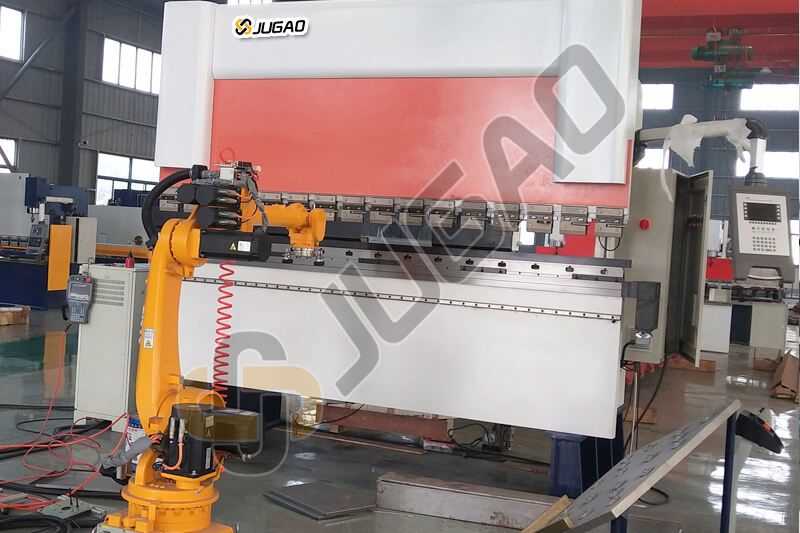
3. CNC Programming Optimization
Implement advanced programming techniques:
Nesting Algorithms: Maximize material utilization
Collision Simulation: Virtual testing of bending sequences
Cloud-Based Libraries: Centralized program storage and version control
These methods typically reduce programming time by 40% while improving process reliability.
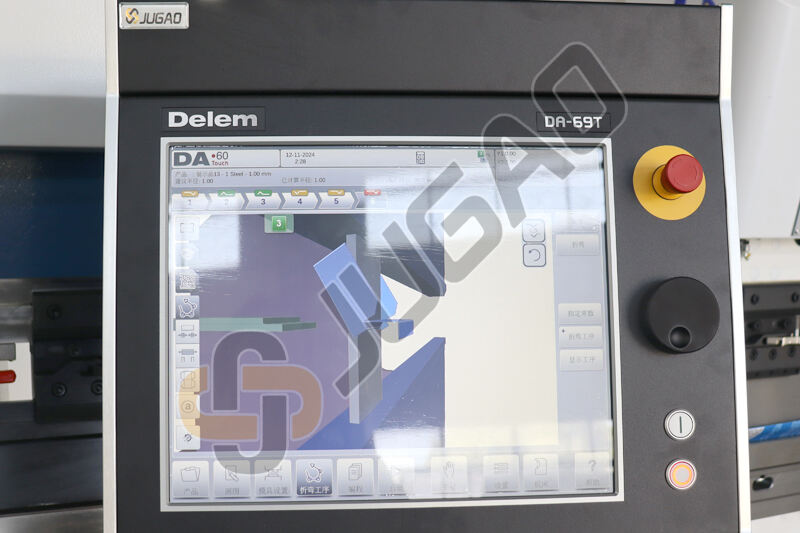
Expert Q&A: Solving Press Brake Productivity Challenges
Q: What's the most impactful first step to improve press brake productivity?
A: Conduct a comprehensive time-motion study to identify your largest productivity bottlenecks before implementing solutions.
Q: How frequently should we benchmark our press brake performance?
A: Perform quarterly productivity audits with monthly KPI tracking to maintain continuous improvement momentum.
Q: What automation investments provide the fastest returns?
A: Automatic tool changing systems typically deliver the most immediate productivity gains with relatively low implementation complexity.
Strategic Roadmap for Continuous Improvement
Develop a 12-month productivity enhancement plan:
Months 1-3: Baseline assessment and bottleneck identification
Months 4-6: Operator training and basic automation implementation
Months 7-9: Advanced process optimization and predictive maintenance
Months 10-12: Full system integration and performance validation
Leading manufacturers who follow this structured approach typically achieve:
35-50% improvement in throughput
25% reduction in material waste
20% decrease in energy costs per unit
For organizations ready to transform their press brake operations, partnering with technology providers JUGAO CNC MACHINE who offer comprehensive productivity assessment services can accelerate results while minimizing implementation risks. The most progressive manufacturers are now combining these mechanical improvements with digital twin technology to simulate and optimize processes before physical implementation.