मोड़ने वाली मशीन की मोड़ने की सटीकता कैसे बढ़ाएं
मोड़ने की सटीकता उच्च गुणवत्ता के धातु भागों के लिए महत्वपूर्ण है, यह सुनिश्चित करने के लिए कि आयाम डिजाइन की निर्दिष्टियों को मिलाते हैं। विमान उद्योग या चिकित्सा उपकरण निर्माण जैसी उद्योगों में, कठिन सहनशीलता का मतलब है कि छोटी भ्रांतियाँ भी समस्याओं का कारण बन सकती हैं।
मोड़ने की सटीकता आर्थिक लाभ पर प्रभाव डालती है। गलत मोड़ने से सामग्री बर्बाद होती है, महंगी पुनर्मूल्यांकन और देरी होती है, उत्पादन समय और मजदूरी की लागत बढ़ जाती है, और ग्राहक संतुष्टि कम हो जाती है। खराब सटीकता संरचना की अधिकता को कम कर सकती है या सभी को गलत रूप से मिलाने का कारण बन सकती है, जिससे गारंटी के दावे और खराब प्रतिष्ठा हो सकती है।
प्रेस ब्रेक कार्यान्वयन में स्थिर झुकाव एकसामयिकता को बनाए रखना अत्यंत आवश्यक है। सटीक झुकाव संसाधनों को बेहतरीन ढंग से उपयोग करता है, अपशिष्ट को कम करता है और लाभप्रदता को बढ़ाता है, इसलिए निर्माताओं को अपनी प्रक्रियाओं को सही से करना चाहिए।
प्रेस ब्रेक के झुकाव एकसामयिकता को नष्ट करने वाले त्रुटियों के कई कारण होते हैं, जिनमें धातु शीट झुकाव मशीन की यांत्रिक समस्याएं भी शामिल हैं, तथा बाह्य कारक जैसे झुकाव उपकरण, सामग्री की मोटाई और मानव ऑपरेटर की त्रुटि।
इस लेख में, हम विभिन्न कारकों का अध्ययन करेंगे जो सटीक झुकाव पर प्रभाव डालते हैं और कुछ सामान्य परिस्थितियों के लिए समाधान प्रदान करेंगे जो मुकाबला की जाती हैं।
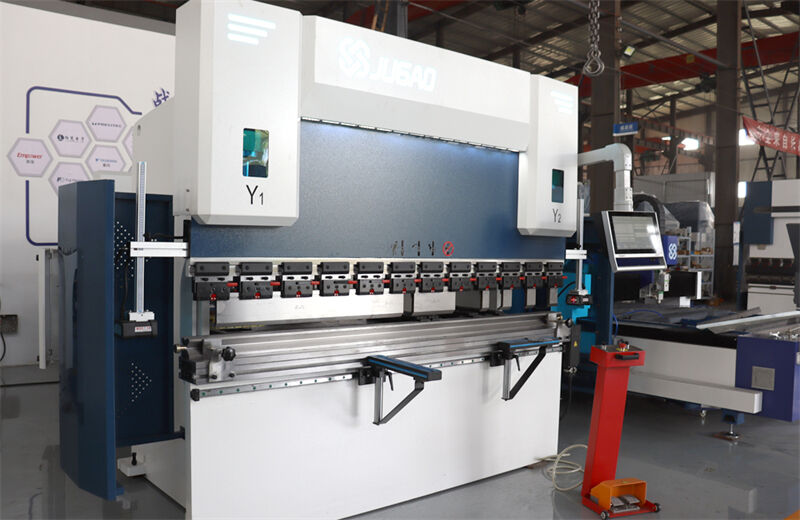
1. मशीन कारक
प्रेस ब्रेक के झुकाव एकसामयिकता पर प्रभाव डालने वाले कई कारक हैं। ये कारक इस प्रकार हैं:
स्लाइडर खोलने की सीधापन
स्लाइडर का क्लैम्पिंग खोलना दोनों Y और X दिशाओं में सीधा है। बाएं और दाएं स्लाइडर की पुनर्व्यवस्थिति और अभिमानिक स्थिति की सटीकता। स्लाइडर की खोलने की सटीकता Y और X दिशाओं में बेंडिंग की सटीकता के लिए महत्वपूर्ण है। यदि स्लाइडर खोलना सीधा नहीं है, तो यह बेंडिंग कोण और स्थिति में विचलन का कारण बन सकता है।
स्लाइडर और फ्रेम रेल के बीच का भाग
बेंडिंग मशीन के प्लंजर और फ्रेम के लीनियर गाइड के बीच का भाग उचित होना चाहिए। स्लाइडर और फ्रेम रेल के बीच का उचित भाग गति के दौरान स्लाइडर की स्थिरता को यकीनन करता है, जिससे बेंडिंग मशीन की बेंडिंग सटीकता में सुधार होता है।
फ्रेम की ऊर्ध्वाधरता और झुकाव
फ्रेम की ऊर्ध्वाधरता और झुकाव। फ्रेम की ऊर्ध्वाधरता और झुकाव झुकाव प्रक्रिया के दौरान अपनी बल के वितरण पर प्रभाव डालते हैं, जिससे समाप्ति उत्पाद की झुकाव सटीकता सुनिश्चित होती है।
प्रयोगशाला डेटा (नीचे दिखाए गए) यह दर्शाते हैं कि फ्रेम का Y अक्ष के साथ 0.1° झुकाव बल के वितरण में 5% की कमी पैदा करता है, जिससे झुकाव कोण में 0.5° का अधिकतम विचलन होता है। यह स्लाइडर सिलिंडर पर असमान बल के कारण होता है, जिससे झुकाव बल वितरण का परिवर्तन होता है।
फ्रेम झुकाव कोण (Y अक्ष दिशा) | झुकाव बल समान रूप से वितरित है | झुकाव कोण विचलन |
0° | 99.50% | <0.1° |
0.05° | 97.20% | 0.2°- 0.3° |
0.1° | 94.80% | 0.3°- 0.5° |
बेलन और स्लाइड के बीच कनेक्शन
प्रेस ब्रेक में झुकाव के दौरान झुकाव बल के समान वितरण को यकीनन होने के लिए बेलन और स्लाइड के बीच कनेक्शन सही रूप से बना हुआ होना चाहिए।
यांत्रिक सटीकता
स्लाइड, डाइस, हाइड्रॉलिक्स और बैकगेज की सटीक कैलिब्रेशन आवश्यक है। नियमित कैलिब्रेशन यह सुनिश्चित करती है कि ये घटक निर्दिष्ट सहनशीलता के भीतर काम करते हैं।
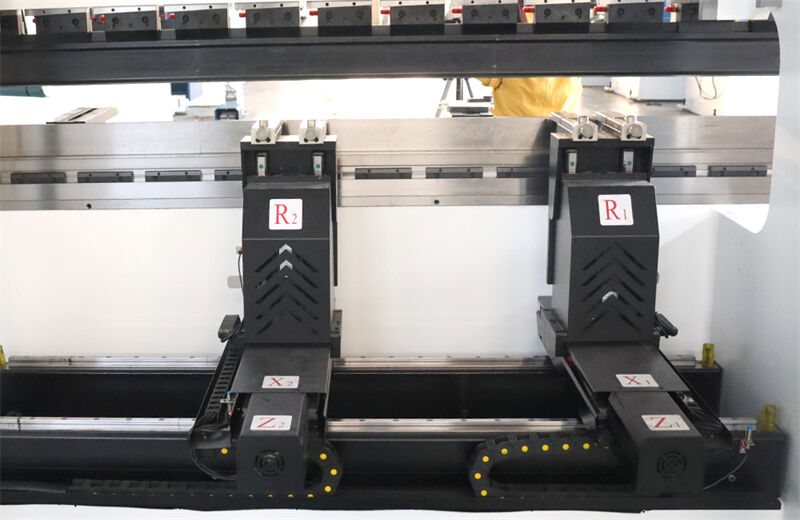
प्रेस ब्रेक के झुकाव को प्रभावित करने वाले अन्य कारक हैं, जैसे कि फ्रेम और स्लाइड की शक्ति और सटीकता, X और R दिशाओं में बैकगेज प्रणाली की पुन: स्थिति की सटीकता, कंप्यूटर प्रणाली की सही समायोजन, हाइड्रॉलिक प्रणाली की समायोजन, और हाइड्रॉलिक प्रणाली और कंप्यूटर समायोजन के बीच मेल खापाना।
2. उपकरण कारक
a.. ऊपरी और निचली मर्मर की सटीकता:
ऊपरी और निचली मर्मर की सटीकता बहुत महत्वपूर्ण है। मर्मर के विकृति, क्षति, पहन और अन्य समस्याएं मेटल बेंडिंग के सभी पहलुओं पर प्रभाव डालेंगी। जब तक पता चलता है, उन्हें समय पर रिपोर्ट किया जाना चाहिए और सुधारा जाना चाहिए। इसलिए, नियमित जाँच और रखरखाव की आवश्यकता है।
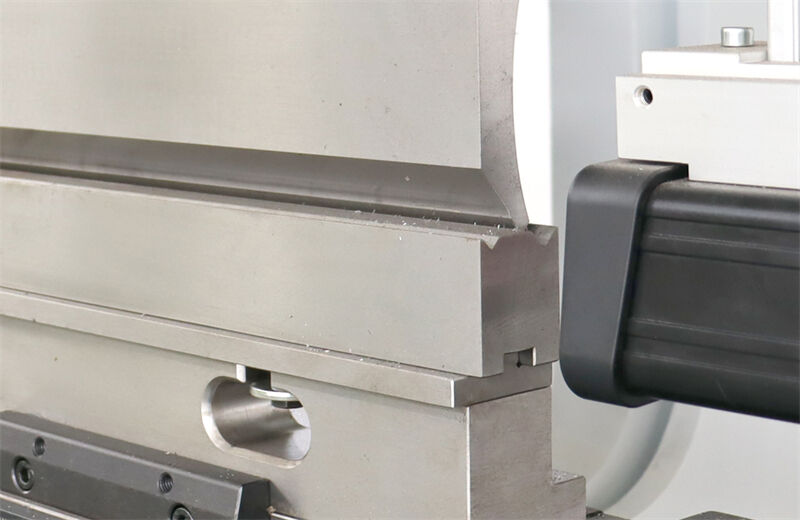
b. मर्मर की सजामति:
ऊपरी और निचली मर्मर के बीच ग़लत सजामति बेंडिंग आकार में विचलन का कारण बनेगी। जब टूल सेट करते हैं, तो यह सुनिश्चित करें कि टूल को ठीक से सजामति किया गया है।
जब पीछे के स्केल की बाएं और दाएं स्थिति बदलती है, तो निचले मर्मर और पीछे के स्केल के बीच की दूरी बदल जाती है। इसे एक वर्नियर कैलिपर से मापा जा सकता है और पीछे के स्केल के स्क्रू का उपयोग करके समायोजित किया जा सकता है।
निचले डाय प्रतिकरण उपकरण की सटीकता और संगतता को फ़्रेम के डिजाइन के अनुसार मैच करना चाहिए। ऊपरी डाय फिक्सचर को अत्यधिक सटीक होना चाहिए।
c. V-डाय खोलने का आकार:
V-डाय के खोलने का आकार झुकाव दबाव के विपरीत समानुपाती होता है। जब शीट की लंबाई और मोटाई निर्धारित होती है, तो बड़ा खोलना होता है, तो कम दबाव की आवश्यकता होती है। इसलिए, जब विभिन्न मोटाइयों की शीटें प्रसंस्करण की जाती हैं, तो उपयुक्त V-डाय खोलने का आकार का उपयोग किया जाना चाहिए।
जब एक ओर के बोझ के साथ प्रसंस्करण किया जाता है, जैसे झुकाव यंत्र के एक सिरे पर, तो झुकाव दबाव प्रभावित हो सकता है, जो यंत्र को क्षति पहुंचा सकती है। यह कठोरता से प्रतिबंधित है। जब डाय को संयोजित किया जाता है, तो यंत्र का मध्य भाग हमेशा दबाव पर होना चाहिए।
d. उपकरण का चयन:
सामग्री और मोड़ने की त्रिज्या के अनुसार सही डाइ पेंच चौड़ाई और पंच प्रोफाइल का चयन करना बहुत महत्वपूर्ण है। धातु रूपांतरण और उत्पादन उद्योग में, गलत डाइज़ कोण विचलन और सतही खराबी का कारण बन सकते हैं।
उपयुक्त मोड़ने वाले उपकरणों और डाइज़ का चयन उपकरणों और प्रसंस्कृत सामग्रियों की गहरी समझ की आवश्यकता वाली एक विस्तृत प्रक्रिया है।
3. शीट मेटल कारक
धातु की शीट संदर्भ सतह की सीधाई की जांच की जानी चाहिए। यह सुनिश्चित करें कि धातु की शीट को समान रूप से तनाव लगता है। शीट मेटल की समान मोटाई की जांच करें।
मोड़ने की प्रक्रिया के दौरान, यदि कार्यपट्टी और निचली डाइ के बीच समानांतरता पर्याप्त नहीं है, तो ऊपरी डाइ को दबाने के बाद कार्यपट्टी पीछे फिर आएगी, जिससे मोड़ का आकार प्रभावित होगा।
स्प्रिंगबैक वह परिकल्पना है कि सामग्री को मुड़ने के बाद अपने मूल आकार में वापस आने का प्रयास करती है। तनाव क्षमता, मोटाई, उपकरण और प्रेस ब्रेक का प्रकार सभी स्प्रिंगबैक पर प्रभाव डालते हैं। तने हुए मोड़ और मोटी, उच्च-शक्ति की सामग्री को संभालने के लिए स्प्रिंगबैक को पूर्वानुमान लगाना और मूल्यांकन करना आवश्यक है।
सामग्री के गुण और मोटाई मोड़ कोण पर प्रभाव डालती हैं, इसलिए प्रत्येक कार्य खण्ड को मुड़ने से पहले उचित रूप से जाँचा और स्थानीय जाँच की जानी चाहिए।
नीचे सामग्री के विस्तृत गुण दिए गए हैं:
प्रदान क्षमता: प्रदान क्षमता वह अधिकतम तनाव है जिससे सामग्री प्रारंभिक रूप से स्थायी रूप से विकृत नहीं होती है। प्रदान क्षमता को जानने से यह निर्धारित करने में मदद मिलती है कि मुड़ाने की प्रक्रिया के दौरान कितना अधिकतम बल लागू किया जा सकता है ताकि सामग्री को क्षति न पहुँचे।
एलास्टिसिटी का मॉडुलस: एलास्टिसिटी का मॉडुलस सामग्री की कड़ाई को इंगित करता है और दिए गए तनाव के अंतर्गत परिवर्तन की मात्रा निर्धारित करता है। एलास्टिसिटी के मॉडुलस को जानने से घुमाव के बाद प्रतिगमन की मात्रा का अनुमान लगाने में मदद मिलती है।
द्रव्य का गाढ़ापन: सामग्री की मोटाई का घुमाव प्रक्रिया पर बहुत बड़ा प्रभाव पड़ता है। मोटी सामग्रियाँ घुमाने के लिए अधिक बल चाहिए और फटने या विकृति से बचने के लिए बड़ा घुमाव त्रिज्या आवश्यक होता है।
प्लास्टिसिटी: प्लास्टिसिटी एक सामग्री की क्षमता को संदर्भित करती है कि वह फटने के बिना प्लास्टिक विकृति के माध्यम से गुजर सकती है। उच्च प्लास्टिसिटी वाली सामग्रियाँ घुमाने में आसान होती हैं और घुमाव प्रक्रिया के दौरान फटने या फटने की संभावना कम होती है।
सतह की स्थिति: धातु सतह की स्थिति (जिसमें कोटिंग या उपचार शामिल है) घुमाव प्रभाव पर प्रभाव डालेगी। अशुद्धियों को हटाने के लिए ठीक से सफाई भी खराबियों से बचने के लिए महत्वपूर्ण है।
4. मोड़ने की संचालन कारक
a. संचालक कार्यों की नियमितता:
जाँचें कि मोड़ने की मशीन के संचालक जब सामग्री को मोड़ने के लिए धकेलते हैं, तो उनके बाएँ और दाएँ बल संगत हैं या नहीं। असंगत मोड़ने वाला बल मोड़ की लंबाई में विचलन का कारण बन सकता है।
b. प्रणाली डेटा समायोजन:
प्रणाली का उपयोग करते समय, सुनिश्चित करें कि प्रणाली डेटा त्रुटि को सही ढंग से समायोजित किया जाए। एक समय पर कम मोड़ने का कोण दूसरे मोड़ की आकृति पर प्रभाव डाल सकता है। उच्च मोड़ने वाली त्रुटियाँ कार्यक्रम की रूपरेखा आकार त्रुटि को बढ़ा सकती हैं।
मोड़ने के लिए आवश्यक दबाव कार्यपट्टी की लंबाई और मोटाई पर निर्भर करता है, और प्लेट की लंबाई और मोटाई आवश्यक दबाव के साथ समानुपातिक होती है।
जब कार्यपट्टी की लंबाई और मोटाई बदलती है, तो उसके अनुसार मोड़ने की क्षमता को समायोजित करना महत्वपूर्ण है।
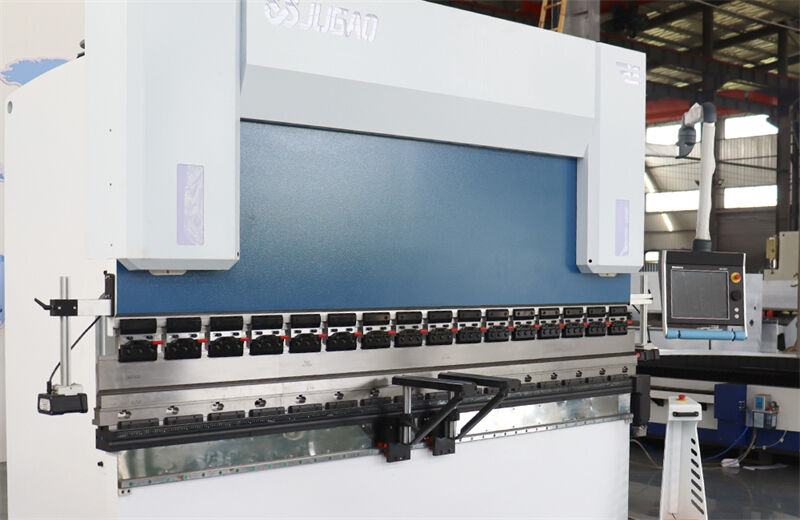
5. पर्यावरणीय कारक
उपकरण, मोल्ड और प्रक्रिया पैरामीटर के अलावा, पर्यावरणीय कारक भी मोड़ने की सटीकता पर कुछ प्रभाव डालते हैं। उनमें से, तापमान और आर्द्रता का प्रभाव सबसे अधिक महत्वपूर्ण है।
तापमान
तापमान के परिवर्तन वस्तु के गुण, जैसे वाइअल्ड स्ट्रेंग्थ और ईलास्टिक मॉडुलस पर प्रभाव डालते हैं। बढ़े हुए तापमान वाइअल्ड स्ट्रेंग्थ और ईलास्टिक मॉडुलस को कम करते हैं और स्प्रिंगबैक को बढ़ाते हैं। असमान तापमान थर्मल विस्तार का कारण बनता है, जिससे कार्यपट्टी का विकृत हो जाना होता है। सटीक मोड़ने को प्राप्त करने के लिए, कार्यशाला के तापमान को स्थिर रखा जाना चाहिए या परिवर्तनों के अनुसार समायोजित किया जाना चाहिए।
आर्द्रता
आर्द्रता सामग्री के सतह पर प्रभाव डालेगी। एक उच्च आर्द्रता के पर्यावरण में, धातु नमी सोखेगी, जंग बनाएगी, और घर्षण और मोड़ने की सटीकता पर प्रभाव डालेगी। यह ऐसी सामग्रियों के लिए महत्वपूर्ण है जिनकी उच्च सतह गुणवत्ता की मांग है, जैसे एल्यूमिनियम एल्युमिनियम और स्टेनलेस स्टील।
6. उच्च मोड़ने की सटीकता प्राप्त करने के लिए तरीके
प्रेस ब्रेक संचालन में उच्च मोड़ने की सटीकता प्राप्त करने के लिए, अग्रणी उपकरणों का उपयोग, दक्ष उपकरण, सही सामग्री संचालन और विकसित प्रक्रिया पैरामीटर को मिलाना आवश्यक है। प्रत्येक तत्व यह सुनिश्चित करने में महत्वपूर्ण भूमिका निभाता है कि मोड़ सटीक, संगत और डिजाइन विनिर्देशों को पूरा करते हैं।
a. उच्च-सटीकता के मोड़ने की मशीन का उपयोग करें
आधुनिक बेंडिंग मशीनों को प्रॉग्राम करने वाले सिस्टम जैसे CNC (कंप्यूटर न्यूमेरिकल कंट्रोल) तकनीक से तयार किया गया है, जो मानवीय त्रुटियों को कम करके और जटिल गणनाओं को स्वचालित करके उत्कृष्ट बेंडिंग सटीकता प्राप्त करता है। वास्तव-में-कोण मापन सिस्टम और स्वचालित शीर्ष कोण समायोजन जैसी विशेषताएँ मोल्ड या कार्य खंड में विचलन की पुर्ति करती हैं, जो संगत बेंडिंग कार्यक्षमता को यकीनन करती है।
विशेष रूप से हाइड्रॉलिक और विद्युत बेंडिंग मशीनों में सटीकता में सुधार करने वाली विशेषताएँ होती हैं, जिनमें प्रोग्राम करने योग्य स्लाइड स्थिति और गति नियंत्रण शामिल है। ये विशेषताएँ कार्य को सटीक बेंडिंग के लिए अनेक भागों पर फाइन-ट्यून करने की अनुमति देती हैं। इसके अलावा, सर्वो-इलेक्ट्रिक ड्राइव्स से तयार मशीनें स्लाइड गति के सटीक नियंत्रण के कारण उत्कृष्ट पुनरावृत्ति प्रदान कर सकती हैं।
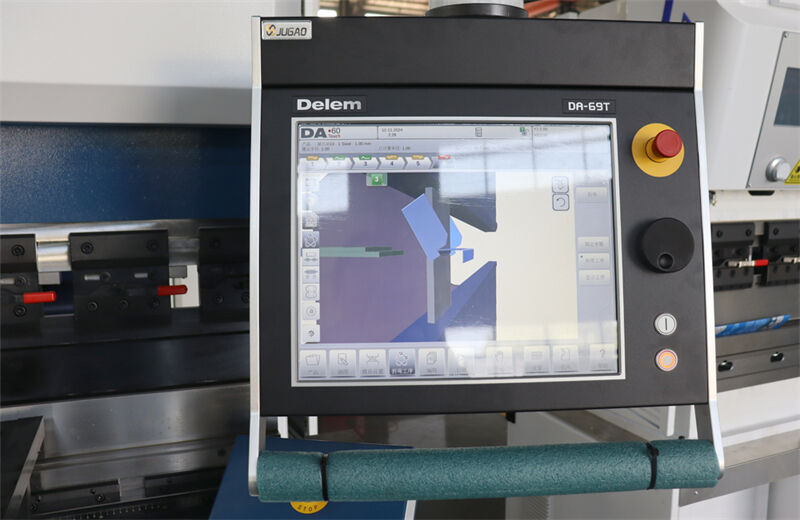
b. उपकरण का चयन और रखरखाव
बेंडिंग मशीन उपकरण का चयन और स्थिति बेंड की गुणवत्ता पर सीधे प्रभाव डालता है। मुख्य विचारों में शामिल हैं
टूल ज्यामिति: सामग्री प्रकार के अनुसार त्रिज्या और कोणों वाले डाइज़ और पंच का चयन बेंडिंग प्रक्रिया के दौरान बल के आदर्श वितरण को गारंटी देता है। गलत डाइज़ का उपयोग अप्रत्याशित विकृति या गलत कोणों का कारण बन सकता है।
सामग्री की गुणवत्ता: कठिन टूल स्टील जैसी उच्च-शक्ति टूल सामग्रियाँ सहनशीलता से निपटती हैं और लम्बे समय तक स्थिर प्रदर्शन बनाए रखती हैं।
नियमित रखरखाव: टूल सतहों को क्षति, सहनशीलता या प्रदूषण से मुक्त रखना बेंडिंग प्रक्रिया के दौरान त्रुटियों से बचाता है। छोटी खराबियों की जांच करना और खराब हिस्सों को बदलना लम्बे समय तक सटीकता बनाए रखने के लिए आवश्यक है।
c. सटीक सामग्री तैयारी
फीड की एकसमानता बेंडिंग परिणाम पर बहुत बड़ा प्रभाव डालती है। अनियमितताएँ जैसे कि भिन्न सामग्री मोटाई, सतह की खराबियाँ, या असंगत यांत्रिक गुण अपेक्षित बेंड कोण में भिन्नताओं का कारण बन सकती हैं। एकसमानता को बनाए रखने के लिए यह आवश्यक है।
मटरियल की मोटाई और कठोरता को झुकाने से पहले पुष्टि करें। यदि मोटाई असमान है या कठोरता बहुत अधिक है, तो प्रक्रिया को समायोजित करना होगा।
प्रदूषणों को टूलिंग या अनुसंधान के कारण असंगतियों से बचने के लिए धातु सतहों को चिपचिपा करने और सफ़ाई करें।
वैरिएबिलिटी को कम करने और भविष्यवाणी योग्य झुकाव व्यवहार को बढ़ावा देने के लिए मटरियल बैचेस को मानक बनाएं।
d. मटरियल स्प्रिंगबैक की गुणवत्ता
स्प्रिंगबैक, धातु की झुकाने के बाद अपनी मूल आकृति को आंशिक रूप से पुन: प्राप्त करने की प्रवृत्ति, ठीक कोणीय सटीकता प्राप्त करने में एक सामान्य चुनौती है। स्प्रिंगबैक को रोकने के लिए उपाय निम्नलिखित हैं:
ओवरबेंडिंग: कार्यकालानुसार जानबूझकर अधिक मात्रा में बेंडिंग करना, जिससे प्रत्यास्थ पुनर्वापसी (elastic recovery) का प्रभाव दूर हो।
निचला बेंडिंग या कॉइनिंग: इन विधियों में, कार्यपट्टी पर पर्याप्त बल लगाया जाता है ताकि वह प्रत्यास्थ सीमा से आगे विकृत हो जाए, जिससे प्रत्यास्थ पुनर्वापसी (springback) कम हो जाए।
विशिष्ट सामग्रियों के लिए समायोजन: विभिन्न धातुओं की प्रत्यास्थ पुनर्वापसी (springback) विशेषताएँ अलग-अलग होती हैं। एडवांस प्रेस ब्रेक्स में सामग्री पुस्तकालय फिट की जाती है, जिससे चयनित सामग्री के आधार पर उपयुक्त प्रतिकारण कोण स्वचालित रूप से गणना की जा सके।
e. सटीक बैकगेज का उपयोग करना
बैकगेज कार्यपट्टी स्थिति को नियंत्रित करने के लिए महत्वपूर्ण घटक हैं, विशेष रूप से जहां तदनुसारता महत्वपूर्ण है, जैसे मास प्रोडक्शन में। CNC प्रणालियों द्वारा नियंत्रित उच्च सटीकता वाले बैकगेज यह सहायता करते हैं:
कार्य पiece को डाइ और पंच के साथ सटीक संरेखण।
दोहराए गए झुकाव के दौरान सामग्री का स्थिर रखना।
बहु-स्टेज झुकाव संचालन में, अलग-अलग कार्य piece ज्यामितियों के लिए तेजी से समायोजन किए जा सकते हैं।
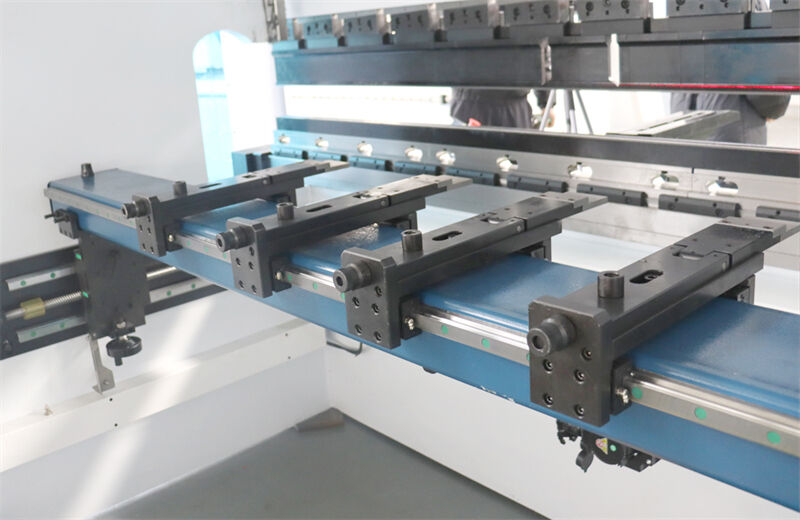
f. प्रक्रिया विन्यास का बेहतरीन उपयोग
सटीक झुकाव प्राप्त करने के लिए प्रक्रिया पैरामीटर का उचित विन्यास कritical है। मुख्य कारकों में शामिल हैं
मोड़ने का बल: सामग्री के प्रकार, मोटाई और उपकरण के गुणों पर आधारित टनnage को समायोजित करें ताकि सही बल लगाया जा सके।
मोड़ने की गति: मोटी या मजबूत सामग्री के लिए, अधिक सटीकता बनाए रखने के लिए धीमी मोड़ने की गति बेहतर होती है, जबकि तेज गति असंगतताओं का कारण बन सकती है।
अनुक्रम योजना: बहुत सारे मोड़ों वाले जटिल भागों को बनाने के लिए प्रत्येक चरण में बाधा न होने और संरेखण बनाए रखने के लिए एक विस्तृत अनुक्रम की आवश्यकता होती है।
g. संचालक प्रशिक्षण और कौशल विकास
उन्नत उपकरणों के साथ भी, संचालक की विशेषता मोड़ने की उच्च सटीकता प्राप्त करने में महत्वपूर्ण होती है। नियमित प्रशिक्षण प्राप्त करने वाले संचालक बेहतर तरीके से काम कर पाते हैं।
गलती के संभावित स्रोतों की पहचान करें, जैसे मिलाने में भूल या सामग्री के सेटअप में अनुपयुक्तता।
प्रेस ब्रेक सेटिंग्स को अवलोकित विचलनों पर आधारित रूप से डायनमिक रूप से समायोजित करें।
उत्पादन के दौरान और बाद में जाँच की प्रक्रिया में समानता बनाए रखें ताकि भाग की गुणवत्ता की जाँच हो।
नवीन तकनीकों और चुनौतियों को संबल देने में ऑपरेटरों की शिक्षा में निरंतर निवेश करना, सटीक बेंडिंग मानकों को बनाए रखने वाली कौशलपूर्ण श्रम शक्ति को सुनिश्चित करता है।
h. गुणवत्ता नियंत्रण और पर्यवेक्षण
मोड़ने की प्रक्रिया के दौरान सख्त गुणवत्ता नियंत्रण उपाय मदद करते हैं ताकि शुरू में ही त्रुटियों का पता चले और उन्हें सही किया जा सके। ये उपाय इस प्रकार हैं,
आँकड़ा-बद्ध प्रक्रिया नियंत्रण (SPC): लंबे समय तक के उत्पादन डेटा का विश्लेषण करने से प्रवृत्तियों और विचलनों की पहचान की जा सकती है जिससे प्रक्रियाओं को बेहतर बनाया जा सके और असंगति के कारणों को खत्म किया जा सके।
ऑनलाइन कोण मापन प्रणाली: मोड़ने की मशीन पर स्थापित वास्तव-काल में निगरानी करने वाले उपकरण सुनिश्चित करते हैं कि मोड़ निर्दिष्ट कोण तक पहुँच जाए फिर भी कार्यपट्टी छोड़ी जाए।
आयामी जाँच: सटीक उपकरणों का उपयोग करें, जैसे कि कैलिपर्स, निर्देशांक मापन मशीनें या लेजर मापन प्रणाली, आयाम और कोणों की पुष्टि के लिए।
7. अक्सर पूछे जाने वाले प्रश्न
a. अपने प्रेस ब्रेक को अधिकतम सटीकता के लिए कितनी बार रखरखाव करना चाहिए?
अपने प्रेस ब्रेक की सटीकता को एक नियमित रखरखाव की योजना के साथ बनाए रखें।
दैनिक: सफाई करें और ढीले या क्षतिग्रस्त हिस्सों की जाँच करें।
साप्ताहिक: स滑रण करें और रिसाव की जाँच करें।
मासिक: हाइड्रोलिक घटकों को सफ़ाई करें और हवा के फ़िल्टर की जाँच करें।
पहले 2,000 घंटों के बाद, 4,000-6,000 घंटों के अंतराल पर हाइड्रॉलिक तेल बदलें। सभी प्रणालियों की जाँच हर छह महीने से एक साल के बाद करें। नियमित कैलिब्रेशन सटीक झुकाव को यकीनन करती है। यह कार्यवाही डाउनटाइम को रोकती है और मशीन की आयु को बढ़ाती है।
ब. प्रेस ब्रेक की सटीकता पर प्रभाव डालने वाले सामान्य समस्याएँ क्या हैं?
प्रेस ब्रेक सटीकता समस्याओं में असंगत सामग्री, स्थिर उपकरण, गलत संरेखण, अनुपयुक्त कैलिब्रेशन, मशीन त्रुटियाँ, गलत बैकगेज और अनुपयुक्त झुकाव विधियाँ शामिल हैं।
इन समस्याओं को हल करने के लिए सामग्री के गुणों की संगति सुनिश्चित करें, उपकरणों की रखरखाव करें, मशीन कैलिब्रेशन करें, CNC बैकगेज का उपयोग करें और उपयुक्त झुकाव विधियों का चयन करें। CNC प्रणाली में वास्तविक समय में समायोजन करें और समस्याओं के होने को कम करने के लिए उपयुक्त अनुसूची बनाएँ।
स. प्रेस ब्रेक के झुकाव की सटीकता के लिए आदर्श टॉलरेंस स्तर क्या है?
एक प्रेस ब्रेक का सहनशीलता स्तर एप्लिकेशन और उद्योग की मांग पर निर्भर करता है। सामान्य रूप से, अधिकांश सटीक परियोजनाओं के लिए ±0.5° का कोणीय विचलन और ±0.1 मिमी का आयामिक विचलन स्वीकार्य है। विमान या चिकित्सा उपकरण निर्माण में, सहनशीलताएँ आम तौर पर कम होती हैं, ±0.25° से कम।
इन लक्ष्यों को प्राप्त करने के लिए, अग्रणी CNC प्रणाली, सटीक टूलिंग और गुणवत्ता निश्चित करने की आवश्यकता होती है। निर्माताओं को विनिर्देशों, सामग्री के गुण, और प्रतिबंधों का मूल्यांकन करना चाहिए ताकि उपयुक्त सहनशीलताएँ निर्धारित की जा सकें।
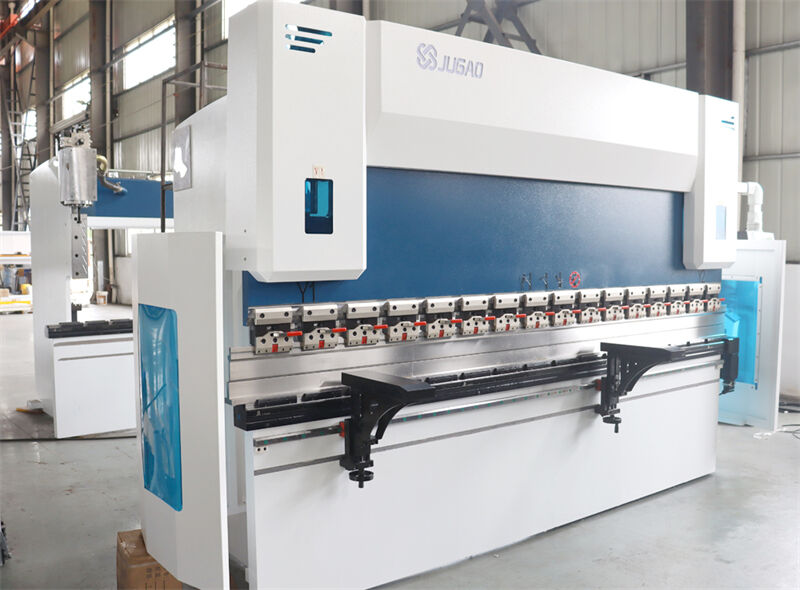
प्रेस ब्रेक की मोड़ने की सटीकता में सुधार करने के लिए, कई कारकों को ध्यान में रखा जाना चाहिए। प्रेस ब्रेक के घटकों को समायोजित करने के अलावा, डाइ पर सटीकता और पुनरावृत्ति को सुनिश्चित करना, सही मोड़ने की प्रतिक्रिया करना, और प्रेस ब्रेक की दैनिक रखरखाव और देखभाल पर ध्यान देना चाहिए।
यह इसकी सेवा जीवन को बढ़ाने में मदद करेगा और कुशल और सटीक झुकाव बनाए रखने में मदद करेगा। चादर धातु के झुकाव के लिए चार झुकाव प्रौद्योगिकियाँ हैं: हवा झुकाव, निचला झुकाव, कॉइन झुकाव, और तीन-बिंदु झुकाव।
धातु निर्माण में एक उत्पादक झुकाव संचालन को सुनिश्चित करने के लिए एक उच्च-गुणवत्ता की प्रेस ब्रेक में निवेश करना एक अन्य प्रभावी तरीका है। JUGAO CNC MACHINE एक विश्वसनीय झुकाव मशीन निर्माता है जिसमें चादर धातु उद्योग में दो दशकों से अधिक विशेषज्ञता है।
हाइड्रोलिक झुकाव मशीनों और CNC झुकाव मशीनों जैसी आधुनिक झुकाव मशीनों के अलावा, हम अन्य मशीनों की पेशकश भी करते हैं जैसे कि लेजर कटिंग मशीनें, प्लेट झुकाव मशीनें, ट्यूब झुकाव मशीनें और अधिक।
अधिक जानकारी के लिए हमारे झुकाव मशीन उत्पाद पेज पर जाएं या विस्तृत उत्पाद और कीमत जानकारी के लिए हमारे संपर्क करें पेज पर जाएं।