Optimisation de la productivité du plieuse : Un cadre d'évaluation des performances
Dans le paysage actuel de la fabrication métallique compétitive, la productivité des plieuses à came influence directement la rentabilité opérationnelle et la réactivité du marché. Cette analyse approfondie présente une approche systématique pour évaluer et améliorer les performances des plieuses à came, combinant des métriques techniques avec les meilleures pratiques opérationnelles pour obtenir des améliorations mesurables dans vos processus de fabrication.
Déterminants critiques de la productivité pour les opérations de plieuse à came
1. Indicateurs d'efficacité opérationnelle
L'évaluation des performances modernes des plieuses à came nécessite de surveiller trois indicateurs clés :
Analyse du temps de cycle : suivre les cycles réels de pliage par rapport à la capacité théorique de la machine
Taux de rendement qualité : mesurer le rendement du premier passage par rapport aux pourcentages de reprise
Schémas de consommation d'énergie : surveiller l'utilisation de l'énergie par unité de production
Les modèles CNC avancés intègrent désormais des tableaux de bord analytiques embarqués qui fournissent des scores OEE (Overall Equipment Effectiveness) en temps réel, permettant une prise de décision basée sur les données.
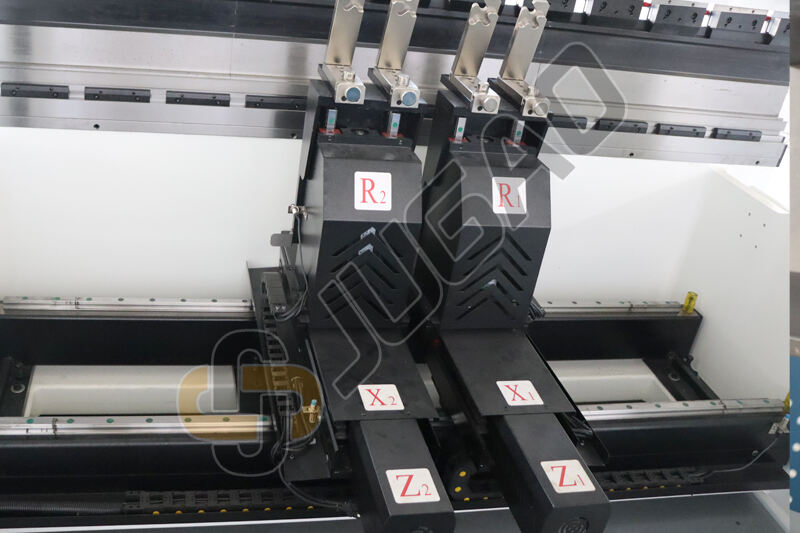
2. Stratégies d'optimisation des flux de travail
Optimisation du flux de travail
Mettre en œuvre les principes de fabrication lean pour éliminer les activités ne créant aucune valeur :
Techniques SMED (Échange de moule en une minute) : Réduire les changements d'outils à moins de 10 minutes
Cartographie du flux de matériaux : Réorganiser les agencements du shop floor pour minimiser les distances de manutention
Suivi numérique des tâches : Mettre en place des systèmes MES pour une surveillance de production en temps réel
Ces méthodes réalisent généralement des améliorations de 25 à 40 % dans le débit opérationnel.
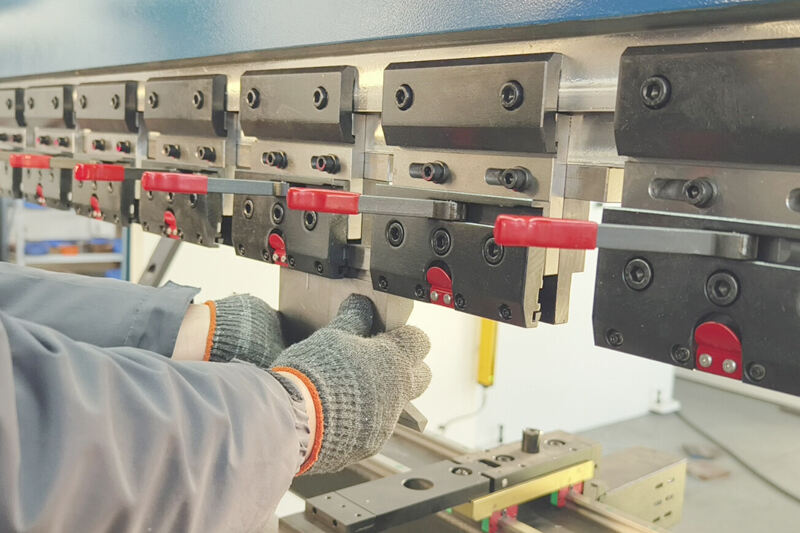
3. Développement du capital humain
Formation des opérateurs
Développer un programme de certification de compétences en plusieurs niveaux couvrant :
Opération de base des machines (Niveau 1)
Dépannage avancé (Niveau 2)
Optimisation des processus (Niveau 3)
Former les opérateurs de cross-training sur plusieurs machines crée une flexibilité de la main-d'œuvre qui peut réduire les temps d'arrêt jusqu'à 30 % lors des changements d'équipe ou des absences.
Techniques avancées pour l'amélioration des performances
1. Systèmes de maintenance prédictive
Passer de la maintenance planifiée au suivi basé sur l'état :
Analyse des vibrations pour l'alignement du pilon
Capteurs de qualité du fluide hydraulique
Imagerie thermique des composants électriques
Ces technologies peuvent prédire 85 % des pannes potentielles avant qu'elles ne provoquent des arrêts non planifiés.
2. Intégration de l'Automatisation Intelligente
Solutions d'automatisation
Évaluer les opportunités d'automatisation sur trois niveaux :
Automatisation de base : changeurs d'outils automatiques
Systèmes Intermédiaires : manutention robotisée de matériaux
Solutions Avancées : flexion adaptative pilotée par l'IA
L'analyse du ROI montre généralement des périodes de retour sur investissement de 12 à 18 mois pour des packages d'automatisation complets.
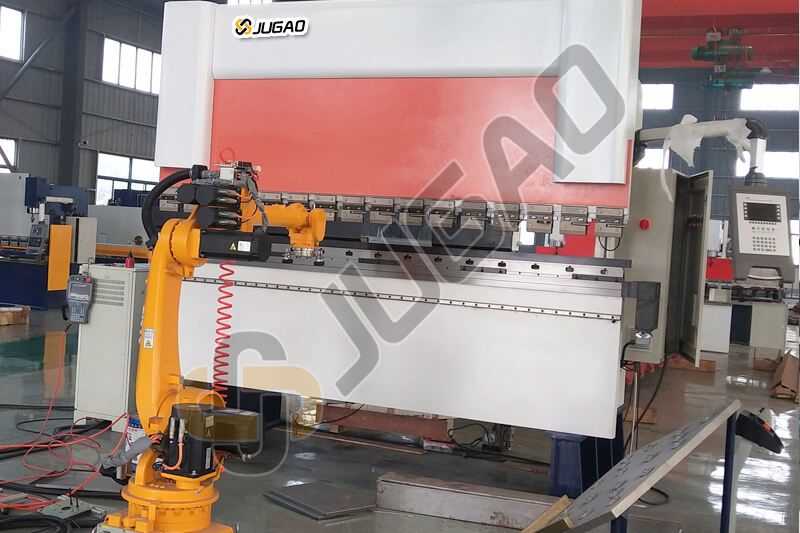
3. Optimisation de la programmation CNC
Implémentez des techniques de programmation avancées :
Algorithmes de nidification : Maximiser l'utilisation des matériaux
Simulation de collision : Test virtuel des séquences de pliage
Bibliothèques basées sur le cloud : Stockage centralisé des programmes et contrôle de version
Ces méthodes réduisent généralement le temps de programmation de 40 % tout en améliorant la fiabilité du processus.
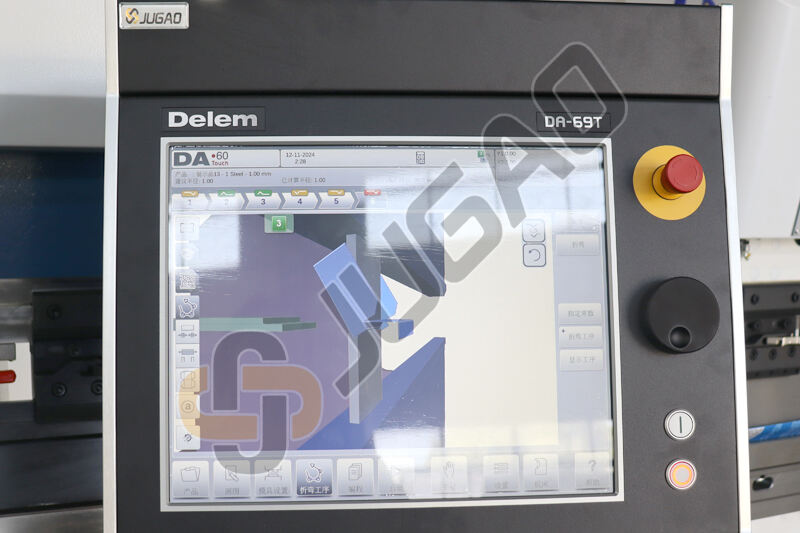
Questions-réponses avec un expert : Résolution des défis de productivité des presse-pliages
Q : Quel est le pas le plus impactant pour améliorer la productivité du plieuse à froid ?
R : Réalisez une étude complète du temps-mouvement pour identifier vos plus grands goulets d'étranglement en matière de productivité avant de mettre en œuvre des solutions.
Q : À quelle fréquence devrions-nous évaluer les performances de notre plieuse à froid ?
R : Effectuez des audits de productivité trimestriels avec un suivi mensuel des indicateurs clés de performance pour maintenir une dynamique d'amélioration continue.
Q : Quels investissements en automatisation offrent les retours les plus rapides ?
R : Les systèmes de changement d'outils automatiques offrent généralement les gains de productivité les plus immédiats avec une complexité de mise en œuvre relativement faible.
Feuille de route stratégique pour l'amélioration continue
Élaborer un plan d'amélioration de la productivité sur 12 mois :
Mois 1-3 : Évaluation de base et identification des goulets d'étranglement
Mois 4-6 : Formation des opérateurs et mise en œuvre de l'automatisation de base
Mois 7-9 : Optimisation avancée du processus et maintenance prédictive
Mois 10-12 : Intégration complète du système et validation des performances
Les principaux fabricants qui suivent cette approche structurée réalisent généralement :
amélioration de 35-50 % du débit
réduction de 25 % des déchets de matériaux
diminution de 20 % des coûts énergétiques par unité
Pour les organisations prêtes à transformer leurs opérations de plieuse hydraulique, collaborer avec des fournisseurs de technologies comme JUGAO CNC MACHINE qui offrent des services complets d'évaluation de la productivité peut accélérer les résultats tout en minimisant les risques de mise en œuvre. Les fabricants les plus innovants combinent désormais ces améliorations mécaniques avec la technologie du jumeau numérique pour simuler et optimiser les processus avant leur mise en œuvre physique.