Analyse Complète de la Durée de Vie et du Cycle de Remplacement d'un Frein à Presse
Table des matières
Facteurs principaux affectant la durée de vie d'un frein à presse
1. Conception et qualité de fabrication
2. Fréquence d'utilisation
3. Gestion du Maintenance Régulière
4. Adaptabilité de l'Environnement Opérationnel
Signaux Clés pour le Remplacement
1. Augmentation des Coûts de Maintenance
2. Obsolescence Technologique
3. Déclin Continu des Performances
Questions fréquemment posées
Q1 : Quelle est la durée de vie moyenne d'un plieuse à métaux ?
Q2 : Comment prolonger la durée de vie ?
Q3 : Quand faut-il remplacer une presse-plieuse ?
Conclusion et recommandations
En tant qu'équipement central dans la fabrication de tôles, la durée de vie et la stratégie de remplacement des presses-plieuses influencent directement les coûts de production et l'efficacité. Cet article analyse systématiquement les facteurs affectant la durée de vie de l'équipement, le moment du remplacement et les stratégies d'optimisation, permettant aux entreprises de mettre en œuvre une gestion scientifique du cycle de vie.
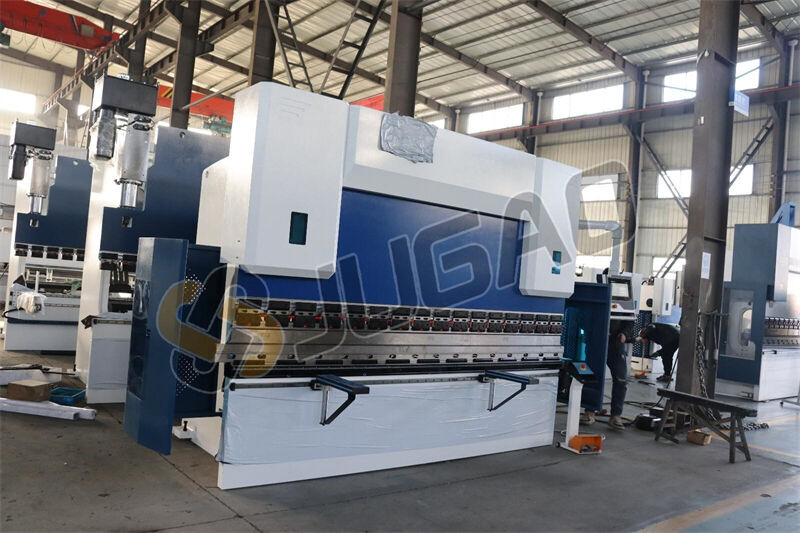
Facteurs principaux affectant la durée de vie d'un frein à presse
1. Conception et qualité de fabrication
Le fondement de la longévité des équipements réside dans les processus de conception et de fabrication :
Matériaux et savoir-faire : Des cadres moulés à haute précision et des rails guides trempés améliorent considérablement la résistance à la fatigue.
Configuration technique : Des technologies avancées telles que les moteurs à entraînement par servocommande et les systèmes de contrôle en boucle fermée réduisent l'usure à long terme.
Sélection de marque : Privilégiez les fabricants certifiés ISO pour garantir la fiabilité.
Étude de cas : Une presse plieuse à cadre en acier soudé entièrement a maintenu 90 % de sa précision après 12 ans d'utilisation continue, tandis qu'un modèle bas de gamme nécessitait des réparations majeures dès la 8e année sous des conditions identiques.
2. Fréquence d'utilisation
L'intensité d'utilisation et la durée de vie présentent une relation non linéaire :
Scénarios à faible charge (<4 heures/jour) : La durée de vie théorique dépasse 20 ans.
Production intensive (fonctionnement 24/7) : Les composants principaux doivent être évalués tous les 10-15 ans.
Points critiques d'usure : Concentrez-vous sur les joints hydrauliques, les guides de poussoir et les contacts électriques.
Référence des données : Une usine de pièces automobiles a rapporté que les équipements effectuant plus de 500 000 cycles annuellement présentaient un taux de défaillance du système hydraulique triplé par rapport aux conditions standard.
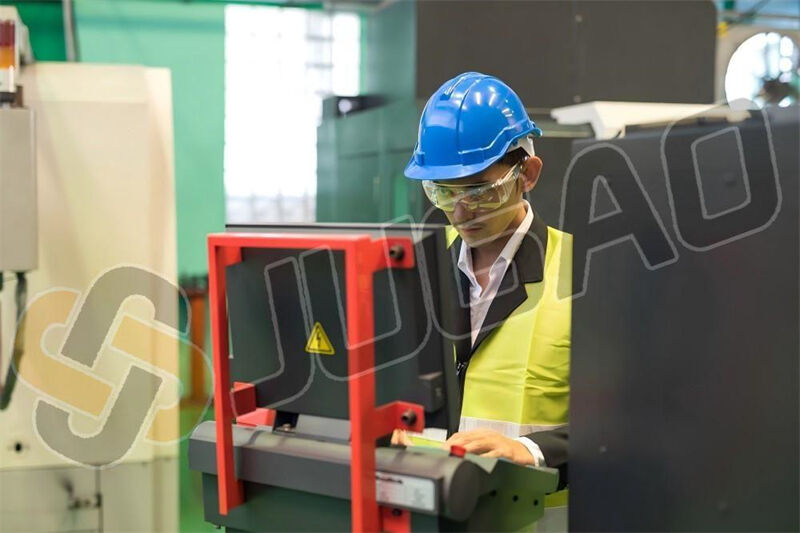
3. Gestion du Maintenance Régulière
L'entretien scientifique prolonge la durée de vie de 30 % à 50 % :
Entretien quotidien : Nettoyer les débris de la voie directrice ; vérifier le niveau d'huile hydraulique hebdomadairement.
Entretien trimestriel : Calibrer la précision du gabarit arrière ; vérifier la stabilité de l'échelle à grille.
Révision annuelle : Remplacer les filtres à huile hydraulique ; tester l'écart de couple du système de synchronisation.
Piège d'entretien : Les entreprises qui comptent uniquement sur les réparations après panne atteignent <60 % d'efficacité globale des équipements, tandis que les programmes d'entretien préventif produisent >85 %.
4. Adaptabilité de l'Environnement Opérationnel
Les impacts environnementaux sont souvent sous-estimés :
Contrôle de la température/humidité : Conditions idéales : 10-35°C, humidité <70 %.
Prévention de la Poussière : Installez des rideaux d'air à surpression pour réduire la contamination des armoires électriques.
Stabilité de la Fondation : Utilisez des plates-formes anti-vibrations dans les environnements à fortes vibrations pour éviter la déformation du cadre.
Cas Extrême : Une installation côtière sans traitement anti-projection de sel a connu une corrosion sévère des cartes électroniques en l'espace de 3 ans.
Signaux Clés pour le Remplacement
1. Augmentation des Coûts de Maintenance
Lancer une analyse coûts-avantages si les coûts de réparation annuels dépassent 30 % de la valeur résiduelle ou si les coûts d'une réparation majeure unique dépassent 15 % du prix d'un nouvel équipement.
Modèle de décision :
Seuil de remplacement = (Coût de maintenance annuel + Pertes liées aux temps d'arrêt) / Coût annuel d'amortissement d'un nouvel équipement > 1,2
2. Obsolescence Technologique
Les équipements anciens rencontrent trois défis :
Écart de précision : Modèles mécaniques traditionnels à arrêt : ±0,1 mm de reproductibilité contre modèles CNC : ±0,02 mm.
Faible efficacité énergétique : Les nouveaux presses plieuses à servocommande réduisent la consommation d'énergie de 40 % à 60 %.
Gaps fonctionnels : Les fonctions intelligentes (par ex., simulation 3D, changement automatique d'outils) ne peuvent pas être obtenues par rénovation.
Recommandation de mise à niveau : Accordez la priorité à la rénovation CNC pour les modèles hydrauliques âgés de plus de 10 ans.
3. Déclin Continu des Performances
Incluez ces métriques dans les évaluations de l'état des équipements :
Déviation de l'angle de pliage : Dépasse la tolérance par 2 fois pendant trois mois consécutifs.
Délai de Réponse Hydraulique : >0,5 seconde entre la commande et le mouvement du vérin.
Erreur de Synchronisation : écart d'axe Y1/Y2 >0,05mm.
Outils de Diagnostic : Utilisez des analyseurs de vibrations et des caméras thermiques pour des inspections approfondies.
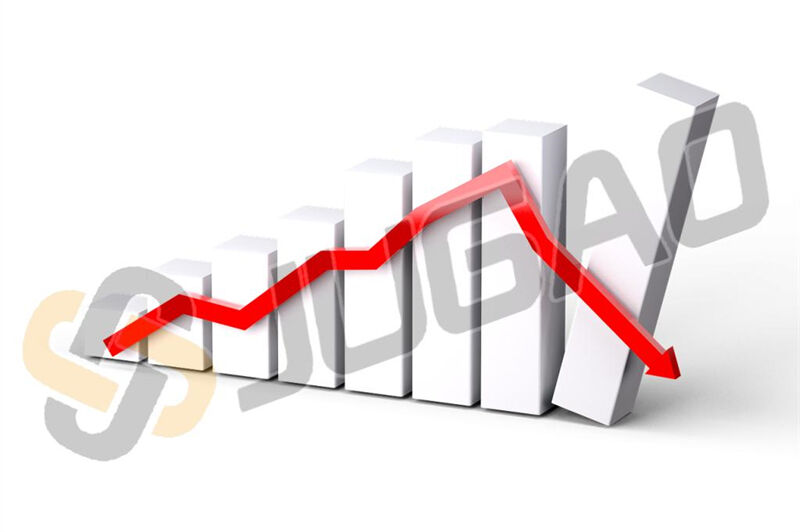
Questions fréquemment posées
Q1 : Quelle est la durée de vie moyenne d'un plieuse à métaux ?
Sous réserve d'une utilisation et d'une maintenance standardisées :
Modèles Économiques : 8-12 ans
Modèles CNC de gamme intermédiaire : 12-18 ans
Modèles à servomoteurs haut de gamme : 15-25 ans
Q2 : Comment prolonger la durée de vie ?
Mettre en place une stratégie de maintenance en trois niveaux :
1. Niveau opérateur : Vérifications de lubrification avant le service ; nettoyage de l'espace de travail après le service.
2. Niveau technicien : Tests mensuels de la courbe de pression hydraulique et des tests d'isolation électrique.
3. Niveau Expert : Analyse annuelle du stress de la structure et mises à jour du firmware CNC.
Q3 : Quand faut-il remplacer une presse-plieuse ?
Initier une évaluation de remplacement si :
Les composants critiques (par exemple, les cylindres principaux) sont discontinués sans alternatives.
L'efficacité de traitement diminue de 30 % par rapport aux références de l'industrie.
Les systèmes de sécurité ne répondent pas aux dernières normes CE/OSHA.
Conclusion et recommandations
La gestion du cycle de vie d'un plieuse à came nécessite un système d'évaluation quantifié :
1. Tenir des dossiers d'équipement : Enregistrer l'historique d'entretien, les codes de panne et les rétrofit.
2. Adopter la surveillance IoT : Suivi en temps réel de la pression, de la température et des vibrations.
3. Élaborer des plans roulants sur 5 ans : Aligner les calendriers de remplacement avec la planification de la capacité et les tendances technologiques.
Guide d'action : Inspections annuelles par un tiers pour générer des rapports de santé des équipements permettant des décisions basées sur des données.