Bükme makinesinin bükme doğruluğunu nasıl geliştirebiliriz
Eğme doğruluğu, boyutların tasarım belirtilerini karşılamasını sağlamak için yüksek kaliteli metal parçaları için kritiktir. Uzay ve tıp cihazı üretimi gibi endüstrilerde, dar toleranslar bile küçük sapmaların sorunlara neden olabileceği anlamına gelir.
Eğme doğruluğu ekonomik faydalara etki eder. Yanlış eğrilme malzemeyi boşa çıkarır, pahalı yeniden işlemeye ve gecikmelere neden olur, üretim süresini ve emek maliyetlerini artırır ve müşteri memnuniyetini azaltır. Düşük doğruluk seviyesi yapının bütünlüğünü zayıflatabilir veya montajı hatalı hizalayabilir, bu da garantili talepler ve zararlı itibar kaybına neden olabilir.
Düzenli bükme doğruluğunu korumak, pres freni işleminde temel bir unsurdur. Doğru bükme, kaynakları optimize eder, atıkları azaltır ve karlılığı artırır; dolayısıyla üreticiler süreçlerini iyileştirmelidir.
Pres frenlerinin bükme doğruluğunu etkileyen hataların birçok nedeni vardır, bunlar metalleri bükme makinesindeki mekanik sorunlarla birlikte, bükme araçları, malzeme kalınlığı ve insan operatör hataları gibi dış faktörler de içerebilir.
Bu makalede, doğru bükmenin etkileyici olan çeşitli faktörleri inceleyeceğiz ve karşılaşılan bazı ortak durumlar için çözümler sunacağız.
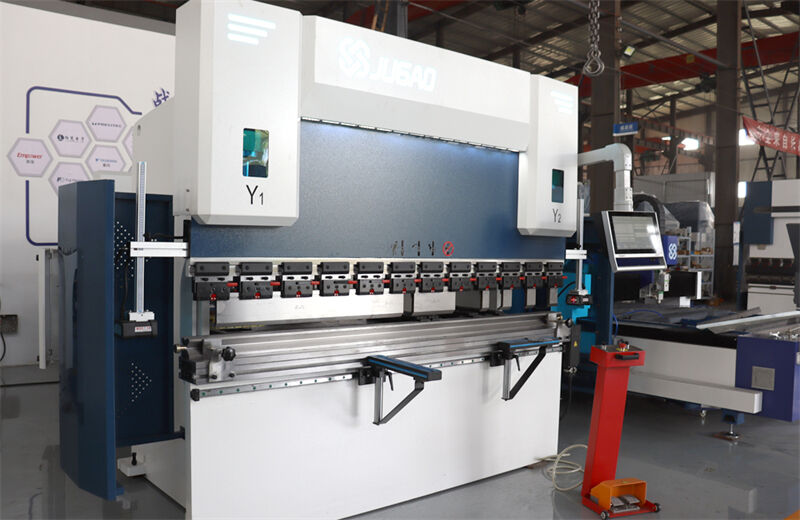
1. Makine faktörleri
Pres frenlerinin bükme doğruluğunu etkileyen birkaç faktör vardır. Bu faktörler arasında
Kaydırıcı açma doğruluğu
Kaydırıcı'nın sıkıştırma açısı Y ve X yönlerinde düzgünür. Sol ve sağ kaydırıcıların yeniden konumlandırma doğruluğu ve isteğe bağlı konumlandırma doğruluğu. Kaydırıcı'nın Y ve X yönlerindeki açma doğruluğu, bükme doğruluğuna kritiktir. Eğer kaydırıcı açısı düzgün değilse, bu bükme açısı ve konumunda sapmalar yol açacaktır.
Kaydırıcı ile çerçeve rayı arasındaki boşluk
Bükme makinesinin pistonu ile çerçevesinin lineer rehberi arasındaki boşluk uygun olmalıdır. Kaydırıcı ile çerçeve rayı arasındaki uygun boşluk, kaydırıcı'nın hareket esnasındaki kararlılığını sağlar ve böylece bükme makinesinin bükme doğruluğunu artırır.
Çerçeve dikeyliği ve eğimi
Çerçevenin dikeyliği ve eğimi. Çerçevenin dikeyliği ve eğimi, bükme süreci sırasında bükme kuvvetinin dağılımını etkiler ve bu da bitmiş ürünün bükme doğruluğunu sağlar.
Deney verileri (aşağıda gösterildiği gibi) göstermektedir ki, çerçeveyin Y ekseni boyunca 0.1° eğimi, bükme kuvvetinin均匀liğini %5 azaltır ve maksimum bükme açısı sapması 0.5° olur. Bu, kaydırma silindirindeki kuvvetin dengesiz olması nedeniyledir ve bu da bükme kuvveti dağılımını kaydırmaktadır.
Çerçeve eğim açısı (Y eksen yönünde) | Bükme kuvveti eşit şekilde dağılmıştır | Bükme açısı sapması |
0° | 99.50% | <0,1° |
0,05° | 97.20% | 0.2°- 0.3° |
0.1° | 94.80% | 0.3°- 0.5° |
Silindir ve kaydırma arasındaki bağlantı
Silindir ve kaydırma arasındaki bağlantı, basıncı uygularken bükme kuvvetinin dengeli dağılmamasını sağlamak için tutarlı olmalıdır.
Mekanik Kesinlik
Kaydırıcılar, kalıplar, hidrolikler ve arkaölçü sistemlerininpreciz bir şekilde kalibrasyonu esastır. Düzenli kalibrasyon, bu bileşenlerinbelirlenen toleranslar içinde çalışmasını sağlar.
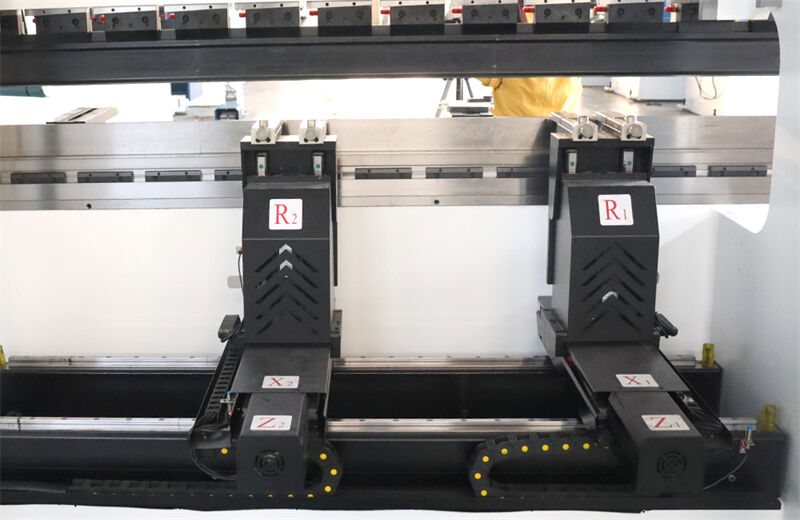
Basınç makinelerinin preciz bükme işlemlerinde etkili olan diğer faktörlerde var; bunlar, makine çatısının ve kaydırmanın dayanımı ve doğruluğu, X ve R yönleri açısından arkaölçü sisteminin yeniden konumlandırma doğruluğu, bilgisayar sisteminin doğru ayarlanması, hidrolik sisteminin ayarlanması ve hidrolik sistemi ile bilgisayar ayarları arasında uyum sağlanmasıdır.
2. Alet faktörleri
a.. Üst ve alt kalıpların doğruluğu:
Üst ve alt matrislerin doğruluğu kritik importance. Matrisin bozulması, hasarı, aşınması ve diğer sorunları metal bükme işleminin tüm yönlerini etkileyecektir. Bunlar tespit edildiğinde, zamanında bildirilip düzeltilmelidir. Bu nedenle, düzenli denetim ve bakım gereklidir.
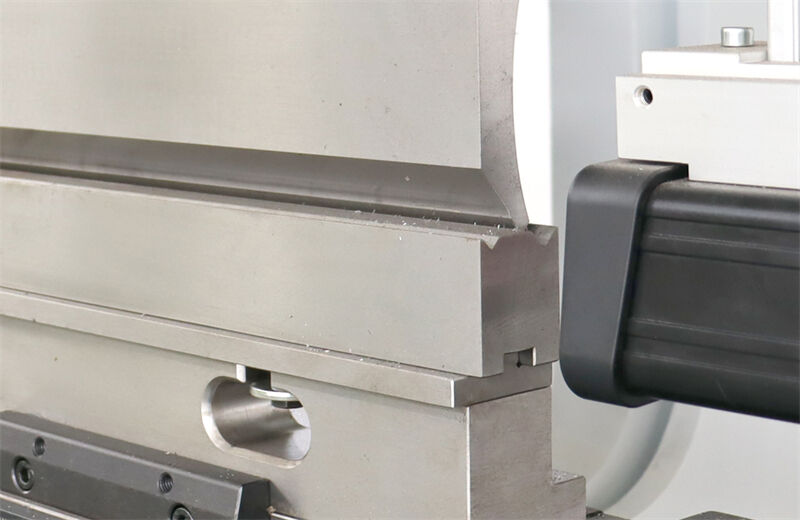
b. Matris hizalama:
Üst ve alt matrisler arasındaki hizasızlık, bükme boyutunda sapmalar yaratabilir. Araç kurulurken aracı doğru bir şekilde hizalamak gerektiğini unutmayın.
Arka kalibrasyonun sol ve sağ konumu hareket ettikten sonra, alt matris ile arka kalibrasyon arasındaki mesafe değişecektir. Bu, bir çentiklik ile ölçülerek arka kalibrasyon torneti kullanılarak ayarlanabilir.
Alt matris kompansasyon cihazının doğruluğu ve uyumluluğu, çerçeveye göre tasarlanmalıdır. Üst matris tutamacı ise yüksek derecede doğru olmalıdır.
c. V-ölçü açılımı:
V-ölçü açılımı, bükme basıncıyla ters orantılıdır. Plaka uzunluğu ve kalınlığı sabitken, açılım越大 ise gerekli olan basınç daha azdır. Bu nedenle, farklı kalınlıklardaki plakaları işlerken uygun V-ölçü açılımı kullanılmalıdır.
Tek taraflı bir yükle işlem yaparken, örneğin bükme makinesinin bir ucunda, bükme basıncı etkilenmesi makineye zarar verebilir. Bu kesinlikle yasaktır. Ölçüyü monte ederken, makinenin orta kısmı her zaman gerilim altına alınmalıdır.
d. Alet seçimi:
Malzeme ve bükme yarıçapına göre uygun ölçü açılımı ve darbelen profili seçmek çok önemlidir. Metal şekillendirme ve üretim endüstrisinde yanlış ölçü açılımları açı sapmalarına ve yüzey kusurlarına neden olabilir.
Uygun bükme araçlarını ve matraçları seçmek, hem ekipmanı hem de işlenen malzemeleri derinlemesine anlamak gerektiren dikkatli bir süreçtir.
3. Plaka faktörleri
Metal plakanın referans yüzeyinin düz olduğunu kontrol etmek gerekir. Metal plakanın eşit şekilde gerildiğinden emin olun. Plakanın sabit kalınlığa sahip olduğunu kontrol edin.
Bükme işlemi sırasında, montaj parçası ile alt matraç arasındaki paralellik yeterli değilse, üst matraç bastırıldıktan sonra montaj parçasının geri dönmesine neden olur ve bu da bükme boyutunu etkiler.
Geri dönüşüm, malzemenin büküldükten sonra orijinal şekline dönmeye çalıştığı fenomen olarak tanımlanır. Çekme dayanımı, kalınlık, aletler ve pres türü geri dönüşümü etkiler. Geri dönüşümü etkili bir şekilde tahmin etmek ve değerlendirmek, sık bükülere ve kalın, yüksek dayanımlı malzemelere uyum sağlayabilmek için esastır.
Malzeme özellikleri ve kalınlığı bükme açısı üzerinde etki eder, bu nedenle her bir parçanın bükülmeden önce uygun şekilde denetlenmesi ve nokta kontrollerine tabi tutulması gerekir.
Aşağıda malzemenin ayrıntılı özellikleridir:
Elastik Sınır Gücü: Elastik sınır gücü, malzemenin kalıcı olarak deformasyon yaşamasından önce dayanabileceği maksimum stres seviyesidir. Elastik sınır gücünü bilmek, malzemeyi hasar görmesini önlemek için bükme sürecinde uygulanabilecek maksimum kuvveti belirlemeye yardımcı olur.
Elastisite Modülü: Elastik modül, malzemenin sertliğini gösterir ve belirli bir gerilim altındaki deformasyon miktarını belirler. Elastik modülün bilinmesi, bükme işleminden sonra geri dönüş miktarını tahmin etmede yardımcı olur.
Malzeme Kalınlığı: Malzemenin kalınlığı bükme işleminde büyük bir etkiye sahiptir. Daha kalın malzemeler daha fazla kuvvet gerektirir ve çatlama veya deformasyonu önlemek için daha büyük bir bükme yarıçapı gerekir.
Oyalanma: Oyalanma, bir malzemenin kırılmadan plastik deformasyon geçebilme yeteneğidir. Yüksek oyalanma özellikine sahip malzemeler daha kolay bükülür ve bükme sırasında çatlamaya veya yırtılmasına daha az meyillidir.
Yüzey durumu: Metal yüzeyinin durumu (katmanlama veya tedavi dahil) bükme etkisini etkileyecektir. Yabancı maddeleri kaldırmak için yapılan derin temizlik, defoları önlemekte de anahtar bir faktördür.
4. Bükme işlemi faktörleri
a. İşletmenin eylemlerinin tutarlılığı:
Kıvırma makinesi işletmenin malzemeyi kıvırmak için uyguladığı sol ve sağ güçlerin tutarlı olup olmadığını kontrol edin. Tutarlı olmayan kıvırma gücü, kıvırma boyutunda sapmalara neden olacaktır.
b. Sistem verilerini ayarlama:
Sistemi kullanırken, sistem veri hatasını doğru şekilde ayarladığınızdan emin olun. Bir kereki yetersiz kıvırma açısı, ikinci kıvırma boyutunu etkileyebilir. Yığınlanan kıvırma hataları, iş parçası konturu boyutundaki hatayı artırabilir.
Kıvırma için gereken basınç, iş parçasının uzunluğu ve kalınlığına göre değişir ve plakanın uzunluğu ve kalınlığı, gerekli olan basıncıyla orantılıdır.
Çalışma parçasının uzunluğu ve kalınlığı değiştiğinde, bükme kapasitesini uygun şekilde ayarlamak önemlidir.
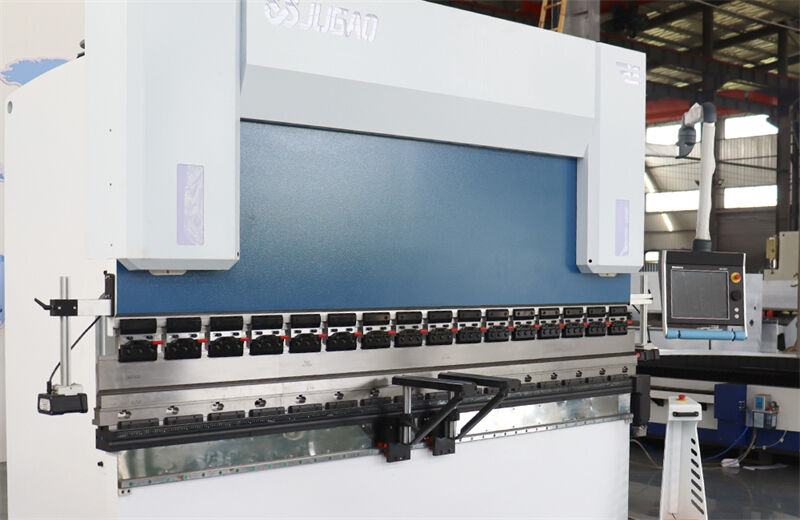
5. Çevresel faktörler
Ekipman, kalıplar ve süreç parametreleri dışında çevresel faktörler de bükme doğruluğuna belirli bir etki edecektir. Bunların arasında sıcaklık ve nemin etkisi en belirgidir.
Sıcaklık
Sıcaklık değişiklikleri, teslim güç ve elastik modül gibi malzeme özelliklerini etkileyecektir. Artan sıcaklık teslim gücünü ve elastik modülü azaltır ve geri dönüşü artırır. Düzgün olmayan sıcaklık termal genleşmeye neden olur ve bu da çalışma parçasının deformasyonuna yol açabilir. Kesin bükme yapmak için atölye sıcaklığı sabit tutulmalı veya değişimlere göre ayarlanmalıdır.
Nem
Nem, malzemenin yüzeyini etkileyecektir. Yüksek nem ortamında, metal buharı emecek, çürümeye başlayacak ve bu da sürtünme ve bükme doğruluğunu etkileyecektir. Bu, alüminyum aleysleri ve çelik gibi yüksek yüzey kalitesi gereksinimine sahip malzemeler için kritiktir.
6. Yüksek bükme doğruluğuna ulaşmak için yöntemler
Basınçlı bükme işlemlerinde yüksek bükme doğruluğuna ulaşmak için, ileri düzeyde ekipman, hassas araçlar, uygun malzeme işleme ve optimize edilmiş süreç parametrelerinin birleşimi gerekir. Her öğe, bükümlerin doğru, tutarlı ve tasarım belirtimlerini karşılaması konusunda hayati bir rol oynar.
a. Yüksek hassasiyetli bir bükme makinesi kullanın
Modern burma makineleri, insan hatasını minimize ederek karmaşık hesaplamaları otomatikleştiren CNC (bilgisayar numerik kontrol) teknolojisi gibi ileri kontrol sistemleriyle donatılmıştır ve bu sayede mükemmel burma doğruluğu sağlanır. Gerçek zamanlı açı ölçme sistemleri ve otomatik üst açı ayarı gibi özellikler, kalıbın veya iş parçasının sapmalarını telafi eder ve tutarlı bir burma performansı sağlar.
Hidrolik ve elektrikli burma makineleri özellikle doğruluğu artıran, programlanabilir kaydırma konumlandırması ve hız kontrollü gibi özelliklere sahiptir. Bu özellikler, birden fazla parçada doğru burmaları sağlamak için işlemi ince ayarlamaya izin verir. Ayrıca, servoelektrik sürücülerle donatılan makineler, kaydırma hareketinin kesin kontrolleri nedeniyle harika bir tekrarlanabilirlik sağlayabilir.
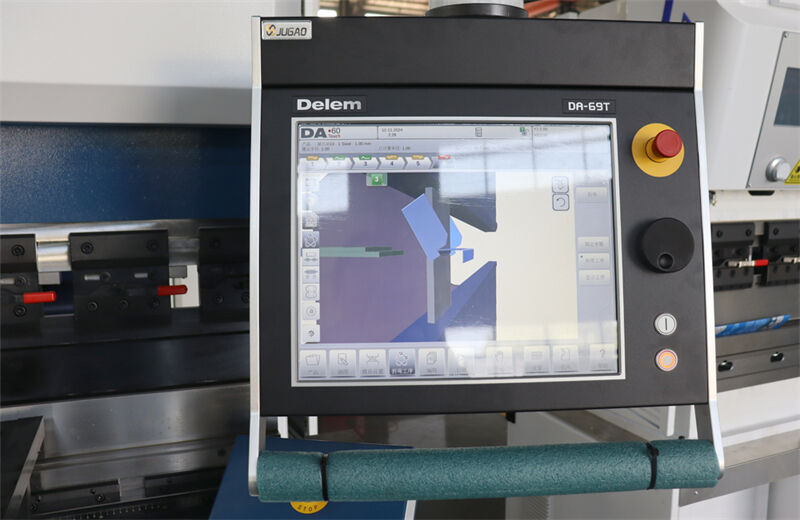
b. Alet seçimi ve bakımı
Burmalı makine aletlerinin seçimi ve durumu, burmanın kalitesini doğrudan etkiler. Ana noktalar şunlardır:
Araç geometrisi: Malzeme türüne uygun yarıçap ve açılarla donatılmış matris ve kalıp seçimi, bükme işleminde optimal kuvvet dağılımını sağlar. Yanlış matrislerin kullanımı beklenmedik deformasyonlara veya yanlış açılarına neden olabilir.
Malzeme kalitesi: Sertleştirilmiş araç çeliği gibi yüksek dayanımlı araç malzemeleri, uzun vadede aşınmayı direnir ve istikrarlı bir performans sergiler.
Düzenli bakım: Araç yüzeylerinin hasar, aşınma veya kirlerden arındırılması, bükme işleminde hataları önler. Araçların hatta küçük деfects için düzenli olarak denetlenmesi ve aşınmış parçaların değiştirilmesi, uzun vadede doğruluğu korumak için temeldir.
c. Doğru malzeme hazırlığı
Besleme eşitliğinin bükme sonucu üzerinde büyük bir etkisi vardır. Değişken malzeme kalınlığı, yüzey eksiklikleri veya tutarsız mekanik özellikler gibi düzensizlikler, istenen bükme açısında değişikliklere neden olabilir. Eşgüdümün sağlanması için tutarlılık sağlanmalıdır.
İskambil etmeden önce malzeme kalınlığını ve sertliğini doğrulayın. Eğer kalınlık düzensizse veya sertlik çok yüksekse, işlem ayarlanması gerekir.
Araç takımıyla ilgili sorunlara neden olabilecek veya tutarsızlıklara neden olabilecek kirlilikleri kaldırmak için metal yüzeylerini kenarlarını düzeltin ve temizleyin.
Değişkenliği minimize etmek ve tahmin edilebilir bir bükme davranışı sağlamak için malzeme partilerini standartlaştırın.
d. Malzeme Geri Dönmeye Karşı Tazminat
Geri dönüş, metalin büküldükten sonra orijinal şeklinin kısmen geri kazanma eğilimi, kesin açı doğruluğunu elde etmedeki yaygın bir zorluktur. Geri dönüşle mücadele için alınacak önlemler şunlardır:
Aşırı bükme: Çalışma sırasında elastik geri dönüşü dengellemek için kasıtlı olarak aşırı bükme uygulanması.
Alt bükme veya parmaklık: Bu yöntemlerde, malzemeye elastik sınırın ötesinde deformasyon yaratacak yeterli kuvvet uygulanır, böylece geri dönüş minimize edilir.
Belirli malzemeler için ayarlama: Farklı metaller farklı geri dönüş özelliklere sahiptir. Malzeme kütüphanesi bulunan gelişmiş pres bükücüleri, seçilen malzemeye göre uygun kompansasyon açısını otomatik olarak hesaplayabilir.
e. Hassas arka jeneratörler uygulama
Arka jeneratörler, özellikle tutarlılık kritik olan seri ürettirmede iş parçası konumlandırmasını kontrol etmek için önemli bileşenlerdir. Yüksek hassasiyetli arka jeneratörler, genellikle CNC sistemleri tarafından kontrol edilir ve şunları sağlar:
Çalışma parçasının kalıbıyla ve dövme aletiyle tam hizalanması.
Malzemenin tekrarlanan bükme işlemlerinde tutarlı yerleştirme.
Çok aşamalı bükme işlemlerinde, farklı çalışma parça geometrilerine hızlı ayarlamalar yapılabilir.
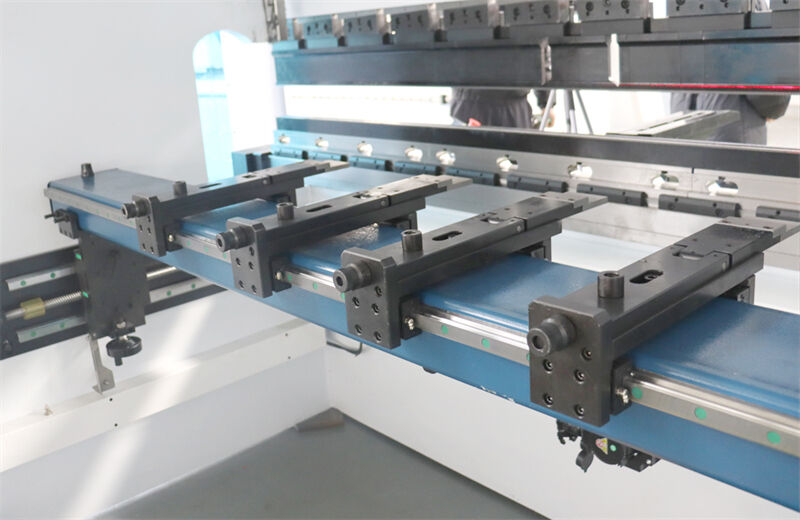
f. Süreç yapılandırmasının iyileştirilmesi
Süreç parametrelerinin doğru yapılandırılması, hassas bükülere ulaşmak için kritik öneme sahiptir. Dikkate alınması gereken ana faktörler arasında
Eğme kuvveti: Malzeme türü, kalınlığı ve araç özellikleri temelinde tonajı ayarlayarak sürekli bir kuvvetin uygulanmasını sağlayın.
Eğme hızı: Daha kalın veya güçlü malzemeler için, doğruluğu korumak için daha yavaş eğme hızları daha iyi olabilirken, daha hızlı hızlar tutarsızlıklara neden olabilir.
Sıra planlama: Birden fazla büküm içeren karmaşık parçalar için her adımda müdahaleyi önlemek ve hizalamaéstını korumak amacıyla dikkatlice planlanmış bir sıra gerekir.
g. İşletıcı eğitimi ve beceri geliştirme
Hatta gelişmiş ekipmanlara sahip olsa bile, işletici uzmanlığı yüksek eğme doğruluğuna ulaşmak için kritik importance taşır. Düzenli eğitim alan işleticiler daha iyi şekilde...
Yanılgı kaynaklarını tespit edin, örneğin hizalanmamış araçlar veya yanlış malzeme kurulumu gibi durumları.
Gözlemlenen sapmalara göre pres bükme ayarlarını dinamik olarak ayarlayın.
Üretim sırasında ve sonrası boyunca denetim prosedürlerini tutarlı bir şekilde uygulayarak parçanın kalitesini doğrulayın.
Yeni teknolojiler ve zorluklarla başa çıkmayı öğrenmek için sürekli operatör eğitimi yapmak, hassas bükme standartlarını koruyabilecek becerili bir işgücüne sahip olmayı sağlar.
h. Kalite kontrolü ve izleme
Kıvrım süreci boyunca uygulanan güçlü kalite kontrol önlemleri, hataları erken tespit etmeyi ve düzeltmeyi sağlar. Bu önlemler şunları içerir:
İstatistiksel süreç kontrolü (SPC): Uzun vadeli üretim verilerini analiz ederek eğilimleri ve sapmaları tespit etmek süreçleri optimize etmeye ve tutarsızlığın kaynaklarını ortadan kaldırmaya yardımcı olur.
Çevrimiçi açı ölçme sistemi: Kıvrım makinesine monte edilen gerçekte zamanlı izleme araçları, iş parçasını serbest bırakmadan önce belirlenen açıyı ulaşmasını sağlar.
Boyutsal denetim: Kalıplar, koordinat ölçüm makineleri veya lazer ölçüm sistemleri gibi hassas aletler kullanarak boyutları ve açıları doğrulayın.
7. Sık Sorulan Sorular
a. Basınç koparıcısının optimal doğruluk için ne sıklıkta bakımlı olması gerekir?
Basınç koparıcınızın doğruluğunu sistemli bir bakım takvimiyle koruyun.
Günlük: Temizleyin ve gevşek veya hasarlı parçaları kontrol edin.
Haftalık: Yağlama yapın ve sızıntıları kontrol edin.
Aylık: Hidrolik bileşenleri temizleyin ve hava filtrelerini kontrol edin.
İlk 2.000 saatten sonra, hidrolik yağını her 4.000-6.000 saatte bir değiştirin. Tüm sistemleri altı aylık ila yılda bir denetleyin. Düzenli kalibrasyon, doğru bükümü sağlar. Bu rutin, iş sürekliliğini önler ve makinenin ömürünü uzatır.
b. Basınçlı bükme işleminin doğruluğuna etki eden yaygın sorunlar nelerdir?
Basınçlı bükme doğruluğu sorunları, tutarsız malzemeler, aşınma araçları, hizalanmamış hizalama, yanlış kalibrasyon, makine hataları, yanlış arkaölçüler ve uygun olmayan bükme yöntemleri içerir.
Bu sorunları, malzeme özelliklerinin tutarlılığını sağlamak, araçları bakımını yapmak, makine kalibrasyonlarını gerçekleştirmek, CNC arkaölçüleri kullanmak ve uygun bükme yöntemlerini seçerek çözebilirsiniz. Sorunların oluşmasını azaltmak için CNC sistemine anlık ayarlamalar yapın ve uygun bir bakım programı oluşturun.
c. Basınçlı bükme işleminin bükme doğruluğu için ideal tolerans seviyesi nedir?
Bir pres bükme cihazının tolerans seviyesi, uygulamaya ve sektör gereksinimlerine bağlıdır. Genel olarak, çoğu hassas proje için ±0.5° açısal sapma ve ±0.1 mm boyutsal sapma kabul edilebilir. Havacılık veya tıp cihazı üretimi gibi alanlarda toleranslar genellikle daha dar olup, ±0.25°'den azdır.
Bu hedefleri gerçekleştirmek için gelişmiş CNC sistemleri, hassas araçlık ve kalite güvencesi gerekir. Üreticiler, uygun toleransları belirlemek için özelliklerini, malzeme özelliklerini ve kısıtlamalarını değerlendirmelidir.
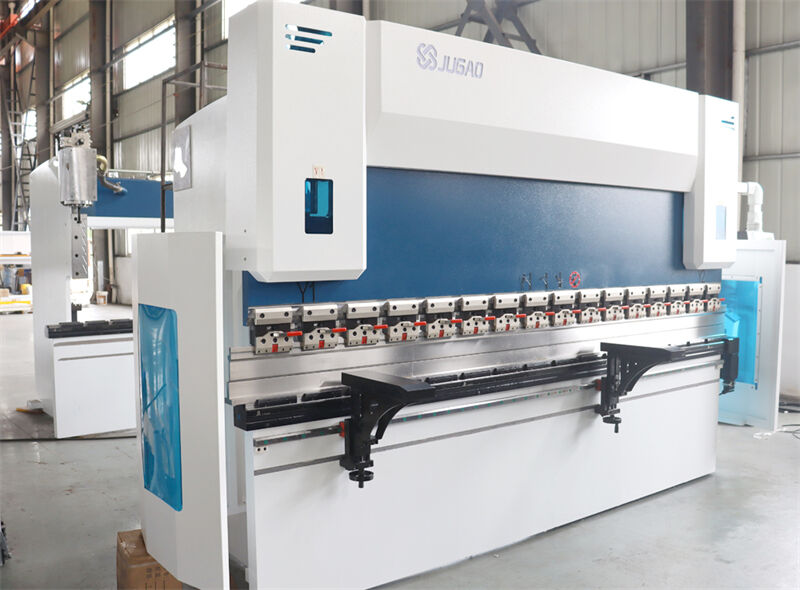
Bir pres bükme cihazının bükme doğruluğunu artırmak için birçok faktör dikkate alınmalıdır. Pres bükme bileşenlerini ayarlamanın yanı sıra, kalıbın doğruluğunu ve tekrarlanabilirliğini sağlamak, doğru bükme kompensasyonu yapmak ve pres bükmenin günlük bakımı ve bakımına dikkat etmek gerekir.
Bu, hizmet ömrünü uzatmasına ve verimli ve doğru bükme işlemi sürdürmesine yardımcı olacaktır. Plaka metali bükme için dört farklı bükme teknolojisi vardır: havada bükme (air bending), alttan bükme (bottom bending), madeni para bükme (coin bending) ve üç nokta bükme.
Metal imalatında üretken bir bükme işlemi sağlamak için yüksek kaliteli bir pres frezi yatırımı yapmak başka bir etkili yöntemdir. JUGAO CNC MACHINE, plaka metali sektöründe iki dekaden fazla uzmanlıkla güvenilir bir bükme makinesi üreticisidir.
Hidrolik bükme makineleri, CNC bükme makineleri gibi modern bükme makinelerinin yanı sıra, lazer kesim makineleri, plaka bükme makineleri, boru bükme makineleri ve daha fazlası gibi diğer makineleri de sunmaktayız.
Daha fazla bilgi için bükme makine ürün sayfamızı ziyaret edebilir veya detaylı ürün ve fiyat bilgisi için bizimle iletişime geçebilirsiniz.