Uitgebreide Analyse van de Levensduur en Vervangingscyclus van een Drukbom
Inhoud
Kernfactoren die invloed hebben op de levensduur van een persschaar
1. Ontwerp en productiekwaliteit
2. Gebruiksfrekwentie
3. Regulier Onderhoudsbeheer
4. Operationele Omgevingsadaptabiliteit
Sleutelsignalen voor Vervanging
1. Stijgende Onderhoudskosten
2. Technologische Veroudering
3. Continu Verlies van Prestaties
Veelgestelde Vragen
V1: Wat is de gemiddelde levensduur van een persbrander?
V2: Hoe kan de levensduur verlengd worden?
V3: Wanneer moet een persbrander vervangen worden?
Conclusie en aanbevelingen
Als kernapparatuur in blaadsmetaalfabrikatie, heeft de levensduur en vervangingsstrategie van persbrekers een directe invloed op productiekosten en efficiëntie. Dit artikel analyseert systematisch de factoren die de levensduur beïnvloeden, het vervangingsmoment en optimalisatiestrategieën, waarmee bedrijven in staat worden gesteld wetenschappelijke levenscyclusbeheer uit te voeren.
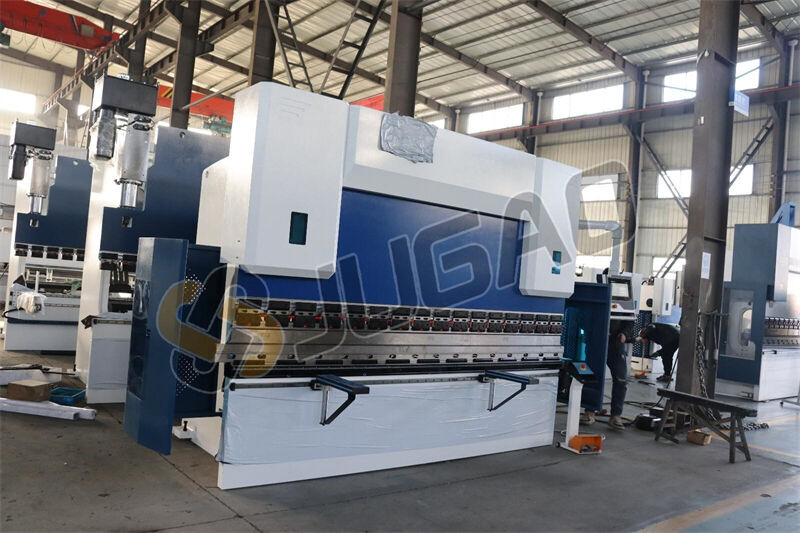
Kernfactoren die invloed hebben op de levensduur van een persschaar
1. Ontwerp en productiekwaliteit
De basis voor de levensduur van apparatuur ligt in de ontwerpprocessen en productie:
Materialen en vakmanschap: Hoog-nauwkeurige gegoten frames en verhardte leidingsassen verbeteren de vermoeimingsweerstand aanzienlijk.
Technische configuratie: Geavanceerde technologieën zoals servomotoren en gesloten-lus besturingssystemen verminderen langdurige slijtage.
Merkselectie: Geef de voorkeur aan ISO-gecertificeerde fabrikanten om betrouwbaarheid te waarborgen.
Casestudy: Een volledig gelaste staalfundering drukpers behield na 12 jaar continu gebruik 90% van zijn nauwkeurigheid, terwijl een laagwaardig model al in het 8e jaar grote reparaties nodig had onder identieke omstandigheden.
2. Gebruiksfrekwentie
Gebruiksintensiteit en levensduur tonen een niet-lineaire relatie:
Lichte Belasting Scenario's (<4 uur/dag): Theoretische levensduur overschrijdt 20 jaar.
Zware Belasting Productie (24/7 bedrijfsvoering): Kernonderdelen dienen elke 10-15 jaar geëvalueerd te worden.
Kritieke Slijtpunten: Focuste op hydraulische sluitingen, persgidsen en elektrische contacten.
Data Referentie: Een autodelenfabriek rapporteerde dat apparatuur die meer dan 500.000 cycli per jaar verwerkt driemaal zo vaak hydraulische systeemstoringen ondervindt vergeleken met standaardomstandigheden.
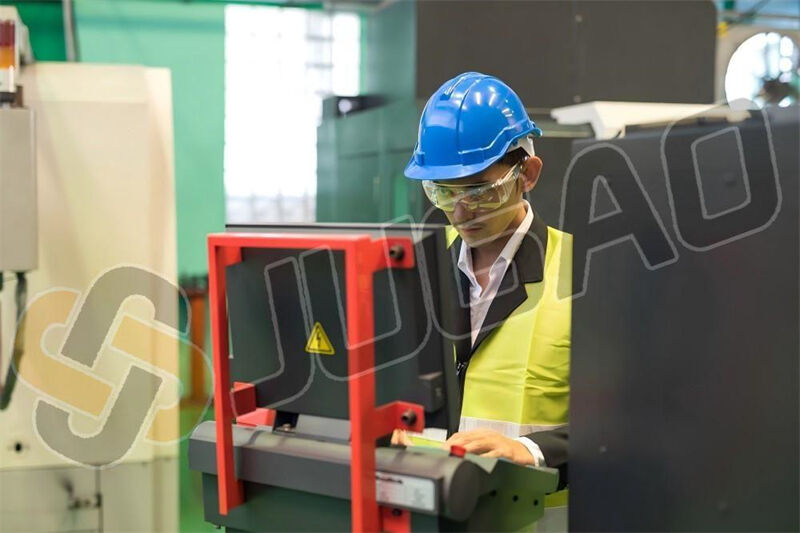
3. Regulier Onderhoudsbeheer
Wetenschappelijke onderhoud verlengt de levensduur met 30%-50%:
Dagelijks onderhoud: Verwijder vuil van de gidsrail; controleer wekelijks het hydraulische oliveau.
Kwartaal onderhoud: Kalibreer de nauwkeurigheid van de achterste gauge; inspecteer de stabiliteit van de gratingschaal.
Jaarlijkse herstelling: Vervang hydraulische oliefilters; test de synchronisatiesysteem koppelingsafwijking.
Onderhoudsvalkuil: Bedrijven die uitsluitend afhankelijk zijn van reparaties na uitval bereiken <60% totaal apparatuur-effectiviteit, terwijl preventief onderhoud programma's >85% opleveren.
4. Operationele Omgevingsadaptabiliteit
Milieueffecten worden vaak onderschat:
Temperatuur/Vochtigheidscontrole: Ideaalere condities: 10-35°C, vochtigheid<70%.
Stofpreventie: Installeer positiedruk-luchtgordijnen om elektrische kastcontaminatie te verminderen.
Funderingsstabiliteit: Gebruik trilling-dempende platforms in omgevingen met hoge trillingen om de vervorming van de constructie te voorkomen.
Extreem geval: Een kustgebouw zonder anti-zoutspuitsbehandeling ondervond ernstige printplaatcorroding binnen 3 jaar.
Sleutelsignalen voor Vervanging
1. Stijgende Onderhoudskosten
Start een kosten-batenanalyse als de jaarlijkse reparatiekosten 30% van de restwaarde overschrijden of als enkele grote reparatiekosten 15% van de prijs van nieuw materiaal overtreffen.
Beslissingsmodel:
Vervangingsdrempel = (Jaarlijkse onderhoudskosten + stilstandverliezen) / Jaarlijkse afwikkelingskosten van nieuw uitrusting > 1.2
2. Technologische Veroudering
Oudere apparatuur staat voor drie uitdagingen:
Nauwkeurigheidsverschil: Traditionele mechanische stopmodellen: ±0,1mm herhaalbaarheid versus CNC-modellen: ±0,02mm.
Lage Energieëfficiëntie: Nieuwe servo drukpersen verminderen de energieverbruik met 40%-60%.
Functionaliteitsgaten: Slimme functies (bijv., 3D simulatie, automatische wisseling van gereedschap) zijn niet haalbaar door retrofitting.
Upgrade Aanbeveling: Geef prioriteit aan CNC retrofitting voor hydraulische modellen ouder dan 10 jaar.
3. Continu Verlies van Prestaties
Neem deze metrieken op in apparaatgezondheidsbeoordelingen:
Booghoekafwijking: Overschrijdt tolerantie met 2x voor drie opeenvolgende maanden.
Hydraulische responsvertraging: >0,5 seconden vanaf commando tot beweging van de stoot.
Synchronisatiefout: afwijking as Y1/Y2 >0,05mm.
Diagnosetools: Gebruik vibratieanalyseapparatuur en thermografische camera's voor diepgaande inspecties.
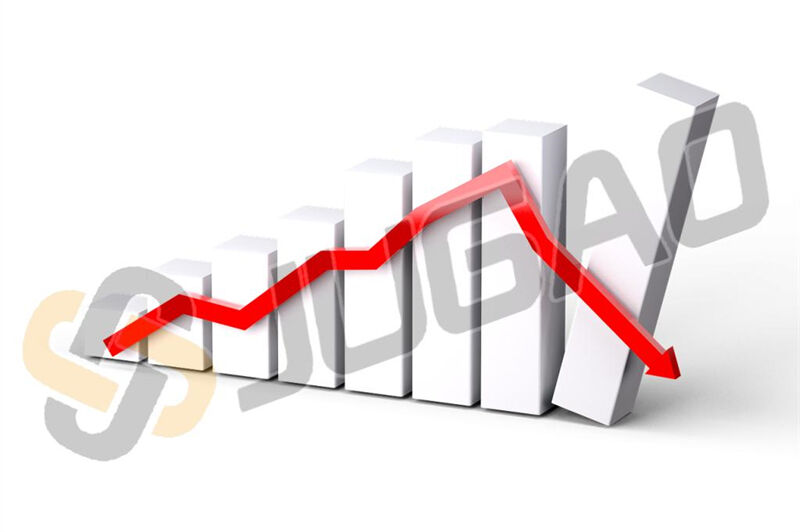
Veelgestelde Vragen
V1: Wat is de gemiddelde levensduur van een persbrander?
Onder gestandaardiseerd gebruik en onderhoud:
Economie modellen: 8-12 jaar
Middenklasse CNC-modellen: 12-18 jaar
Hoogwaardige servo-modellen: 15-25 jaar
V2: Hoe kan de levensduur verlengd worden?
Implementeer een drievoudige onderhoudsstrategie:
1. Operator niveau: Voorafgaande smeervoorzieningscontroles; na-afsluiting werkplek schoonmaken.
2. Technicus niveau: Maandelijkse hydraulische drukcurve en elektrische isolatietesten.
3. Expertniveau: Jaarlijkse frame-stressanalyse en CNC-firmwareupdates.
V3: Wanneer moet een persbrander vervangen worden?
Start vervangingsevaluatie als:
Kritieke onderdelen (bijv., hoofdcilinders) worden stopgezet zonder alternatieven.
De verwerkingsefficiëntie 30% onder de branche-normen komt te liggen.
Veiligheidssystemen voldoen niet aan de nieuwste CE/OSHA-standaarden.
Conclusie en aanbevelingen
Levenscyclusbeheer van een press brake vereist een gekwantificeerd evaluatiesysteem:
1. Houd apparaatrecords bij: Noteer onderhouds geschiedenis, foutcodes en retrofitting.
2. Implementeer IoT-bewaking: Real-time volgen van druk, temperatuur en trilling.
3. Ontwikkel 5-jarige rolplannen: Pas vervangingskalenders aan op capaciteitsplanning en technologietrends.
Actiehandleiding: Jaarlijks derde-partij onderzoek om Apparaatgezondheidsrapporten te genereren voor data-gestuurde beslissingen.