벤딩 머신의 톤수에 영향을 미치는 요인들
굽힘 방법
굽힘방법 | 굽힘 머신의 톤수에 대한 영향 |
공기 구부림 | 압력 구부림보다 더 많은 톤수를 필요로 하며,这是因为上模在凹模中完全压到底。材料接触到上模的尖端和下模的侧壁。吨位较高,但不如压印高。 |
바닥 구부림 | 공기 구부림보다 더 많은 톤수를 필요로 하며,这是因为上模在凹模中完全压到底。材料接触到上模的尖端和凹模的侧壁。吨位较高,但不如压印高。 |
인프린팅 | 최대 톤수를 요구합니다. 팀프와 다이가 재료와 완전히 접촉하여 재료를 압축하고 두께를 줄입니다. 매우 큰 힘을 사용하여 재료를 벤딩 머신의 다이 각도에 맞게 만듭니다. |
다른 금속 구부리기 방법은 다른 톤수를 필요로 합니다. 예를 들어, 공기 구부리기에서는 다이 개구 폭을 변경하여 톤수를 증가시키거나 감소시킬 수 있습니다.
구부림 반경은 다이 개구 폭에 영향을 미칩니다. 이 경우 공식에 메서드 계수를 추가해야 합니다. 바닥 구부리기와 인쇄를 사용할 때 필요한 톤수는 공기 구부리기보다 더 높습니다.
바닥 구부리기의 톤수를 계산할 때 공기 구부리기의 인치당 톤수를 최소 5배로 곱해야 합니다. 스탬핑을 사용하면 바닥 구부리기에 비해 필요한 톤수가 더 클 수 있습니다.
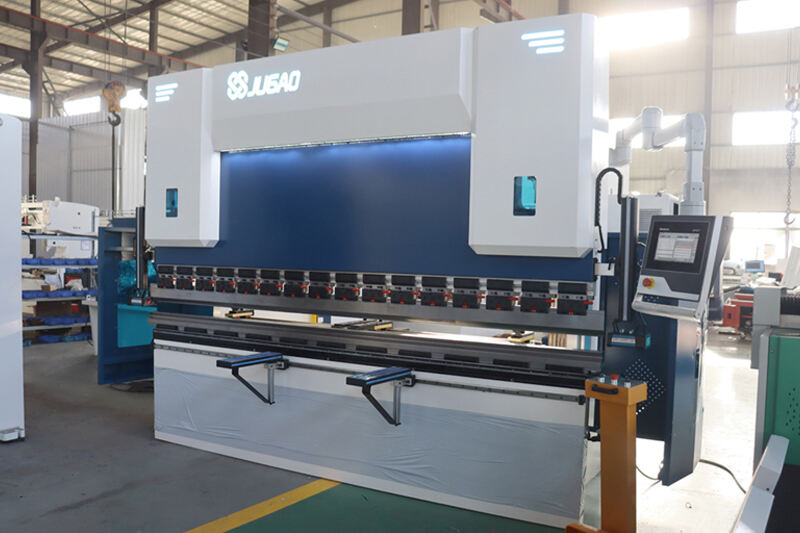
다이 폭
이미 공기 벤딩에서 필요한 톤nage는 다이 개구부의 크기가 커질수록 감소하고, 개구부의 크기가 작아질수록 증가한다는 것을 배웠습니다.
이는 다이 개구부의 너비가 내부 구부림 반경을 결정하며, 더 작은 다이 반경은 더 많은 톤nage를 필요로 하기 때문입니다.
공기 벤딩에서는 다이 비율이 일반적으로 8:1로, 다이 개구부 거리는 재료 두께의 여덟 배입니다. 이 경우 재료 두께는 내부 구부림 반경과 같습니다.
마찰과 속도
공기 벤딩에서는 펀치가 금속 시트를 구부리기 위해 바닥 다이 개구부를 통과해야 합니다. 만약 금속 시트 표면이 윤활되지 않았다면, 다이와 금속 시트 사이의 마찰이 증가하여 더 많은 톤nage가 필요하며, 재료의 스프링백이 줄어듭니다.
반대로, 금속 시트 표면이 매끄럽고 윤활되어 있으면 다이와 금속 시트 사이의 마찰이 줄어들어 금속 시트를 구부리기 위해 필요한 톤수도 감소합니다. 그러나 이는 금속 시트의 스프링백을 증가시킵니다.
구부리는 속도도 필요한 톤수에 영향을 미칩니다. 구부리는 속도가 빨라질수록 필요한 톤수가 감소합니다. 속도를 올리면 다이와 시트 사이의 마찰이 줄어들지만, 이는 시트의 스프링백을 증가시킵니다.
재료 특성
톤수란 프레스 브레이크가 시트 금속에 가하는 힘을 의미합니다. 따라서 구부리는 힘의 범위는 구부려지는 시트 금속의 두께와 인장 강도에 따라 달라집니다.
재료 유형
한 가지 요인은 구부려지는 재료의 종류입니다. 더 높은 인장 강도를 가진 재료, 예를 들어 스테인레스 또는 고강도 합금은 알루미늄이나 구리 같은 부드러운 금속보다 더 큰 힘이 필요합니다. 예를 들어
스테인레스 스틸 (등급 316): 인장 강도 약 620 MPa; 항복 강도 약 290 MPa.
구리: 인장 강도 ~210 MPa; 항복 강도 ~69 MPa.
알루미늄과 같은 더 부드러운 재료는 저항이 적어 톤수 요구사항을 줄이지만 스프링백 가능성을 증가시킵니다.
인장 강도와 항복 강도
다양한 재료는 서로 다른 인장 강도를 가지고 있어 굽힘에 필요한 힘에 직접적인 영향을 미칩니다. 예를 들어, 스테인레스는 일반 철강이나 알루미늄보다 더 많은 톤수를 필요로 합니다.
인장 강도는 물질이 지속적인 하중 아래에서 견딜 수 있는 최대 스트레스입니다. 이 스트레스가 가해지고 유지되면 물질은 결국 부서집니다. 반면, 항복 강도는 물질이 플라스틱 변형을 시작하는 스트레스를 의미합니다.
일부 재료의 일반적인 인장 강도
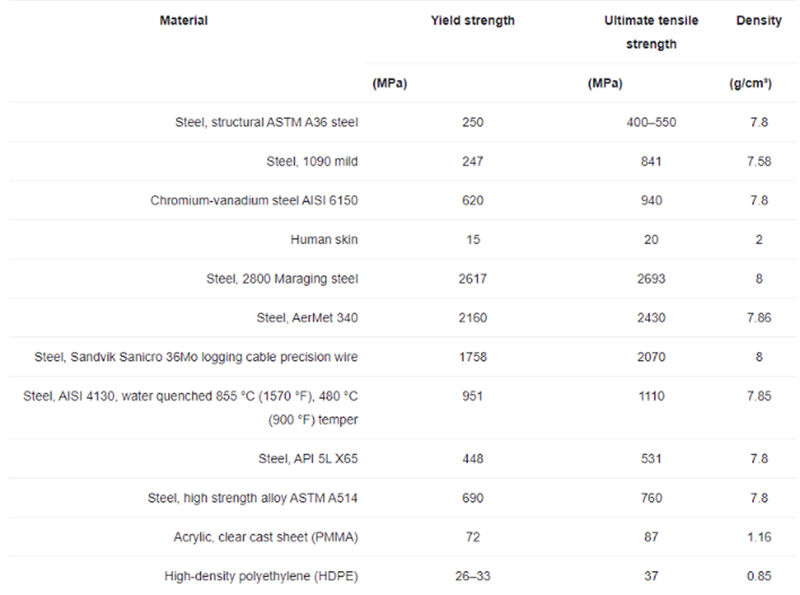
재료 두께
또 다른 중요한 요소는 시트 금속의 두께입니다. 재료가 더 두꺼울수록 더 많은 톤이 필요하며, 그 반대도 마찬가지입니다. 더 두꺼운 재료는 변형에 대한 저항이 크기 때문에 여러 배의 톤이 필요합니다.
예를 들어, 시트 금속의 두께를 두 배로 늘리면 필요한 힘도 두 배가 됩니다. 일반적으로 재료가 더 두꺼울수록 성형하기 위해 더 많은 톤 또는 힘이 필요합니다.
재료 | 두께 (mm) | 굴곡 반경 (mm) | 톤 수 증가율 | 필요한 톤 수 (톤/미터) |
연강 | 1 | 1 | 1 | 10 |
연강 | 2 | 2 | 1 | 40 |
연강 | 3 | 3 | 1 | 90 |
알루미늄 (5052-H32) | 1 | 1 | 0.45 | 4.5 |
알루미늄 (5052-H32) | 2 | 2 | 0.45 | 18 |
알루미늄 (5052-H32) | 3 | 3 | 0.45 | 40.5 |
스테인레스 스틸 (304) | 1 | 1 | 1.45 | 14.5 |
스테인레스 스틸 (304) | 2 | 2 | 1.45 | 58 |
스테인레스 스틸 (304) | 3 | 3 | 1.45 | 130.5 |
연강 | 2 | 1 | 1 | 60 |
연강 | 2 | 3 | 1 | 30 |
스테인레스 스틸 (304) | 2 | 1 | 1.45 | 87 |
스테인레스 스틸 (304) | 2 | 3 | 1.45 | 43.5 |
표는 다음을 보여줍니다
1. 재료의 두께가 증가할수록 모든 재료에 필요한 톤nage이 크게 증가합니다. 두께를 1mm에서 2mm로 두 배로 늘리면 톤nage이 네 배로 증가합니다.
2. 알루미늄은 같은 두께의 저탄소 강철보다 약 45% 더 많은 톤nage이 필요하고, 스테인레스 스틸은 저탄소 강철보다 약 45% 더 많은 톤nage이 필요합니다.
3. 두께를 일정하게 유지하면서 내부 구부림 반경을 줄이면 필요한 톤수는 증가합니다. 반경을 2mm에서 1mm로 절반으로 줄이면 톤수가 50% 증가합니다.
4. 톤수 배수는 재료 유형과 인장 강도에 따라 다릅니다. 이 예시에서는 경도금속은 1.0, 5052-H32 알루미늄은 0.45, 304 스테인레스 스틸은 1.45입니다.
탄성 복귀
구부린 후 재료는 원래 형태로 약간 돌아가는 경향이 있습니다. 고강도 재료일수록 더 많은 탄성 복귀가 발생하므로 정확한 각도를 얻기 위해 톤수와 공구를 조정해야 합니다.
구부림 길이 및 각도
굽힘 길이
プレ스 브레이크 테이블의 굽힘 길이는 금속 시트를 굽힐 수 있는 최대 길이입니다. 프레스 브레이크의 굽힘 길이는 굽히는 재료보다 약간 더 길어야 합니다.
테이블 길이가 부정확하면 다이 또는 기타 구성 요소에 손상이 발생할 수 있습니다. 굽힘 하중 계산기는 재료 두께 및 굽힘 길이와 V-개구부 폭과 같은 기타 요인에 기반한 필요한 톤수를 결정하는 데 도움을 줄 수 있습니다.
굽힘 각도
각도가 클수록 굽힘점에서의 재료 압축이 증가하므로 필요한 톤수가 늘어납니다. 반대로, 큰 각도는 적은 힘이 필요하지만 덜 정확한 굽힘을 초래할 수 있습니다.
공구 요소
브레이크 프레스 펀치도 고려해야 할 요소입니다. 이러한 펀치에도 굽힘 하중 제한이 있습니다. 직각 V자형 펀치는 더 큰 톤nage의 하중을 견딜 수 있습니다.
예각 다이의 경우 각도가 작고 재료가 적게 사용되며, 예를 들어 거위목(Gooseneck) 다이와 같이 무거운 하중을 견디기 어렵습니다.
다양한 다이를 사용할 때 그들의 최대 굽힘 힘을 초과해서는 안 됩니다. 또한 다이 반경과 굽힘 반경도 톤nage 요구 사항에 영향을 미칩니다.
더 큰 다이 반경은 필요한 굽힘 힘의 증가로 이어질 수 있습니다. 마찬가지로 굽힘 반경이 클수록 더 높은 톤nage가 필요합니다.
다이 개구부 폭과 재료 두께 간의 비율도 고려해야 할 또 다른 요소입니다. 더 얇은 재료의 경우 6:1과 같은 낮은 다이 비율이 권장됩니다.
더 두꺼운 재료는 변형력을 줄이고 변형 기계의 성능 범위 내에서 작업을 유지하기 위해 더 높은 다이 비율(예: 10대 1 또는 12대 1)이 필요할 수 있습니다.
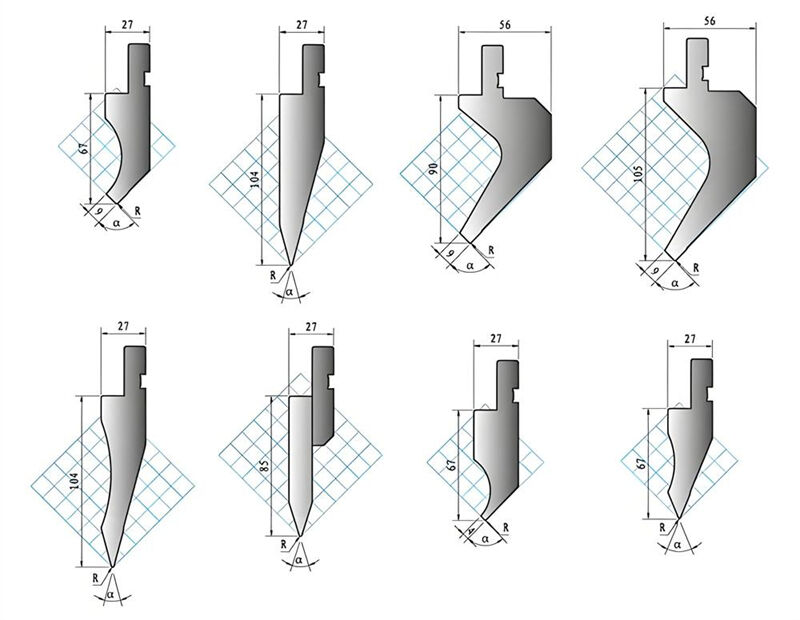
장기적인 도구摩耗
점진적인 마모:
시간이 지남에 따라 반복적인 고압 작동으로 인해 도구가 그 날카로움과 구조적 안정성을 잃게 됩니다. 이를 해결하지 않으면 이 마모로 인해 일관성 없는 굽힘과 부품 품질 저하가 발생할 수 있습니다.
도구 수명에 미치는 영향:
공구를 그 등급 용량 이상으로 사용하는 것(예: 좁은 다이로 두꺼운 판을 가공)은 작동 중 미세한 균열이나 심각한 고장이 발생할 수 있습니다. 예기치 않은 작업 정지나 안전 사고를 방지하기 위해 정기적인 점검이 필수적입니다.
유지 보수 요구 사항:
과부하가 걸린 공구는 더 자주 유지보수를 필요로 하거나 교체되어야 해서 운영 비용이 증가합니다. 모니터링 시스템이나 예측적 유지보수 소프트웨어는 마모 패턴을 조기에 식별하고 공구 사용을 최적화하는 데 도움을 줄 수 있습니다.
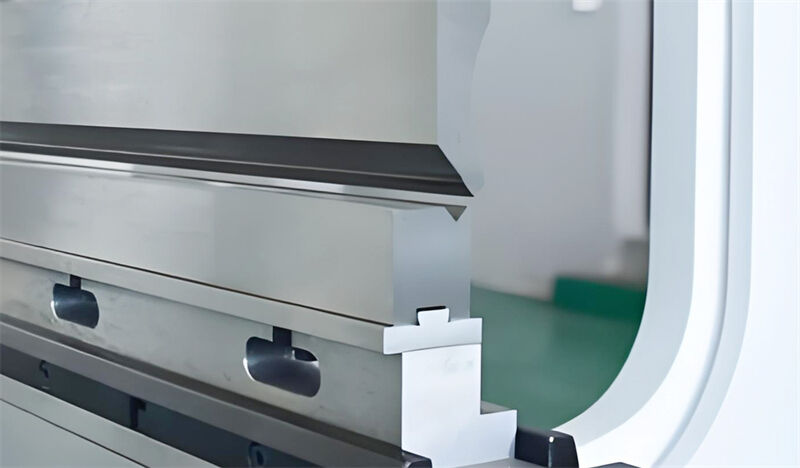