A nyomósztály termelékenységének optimalizálása: Egy teljesítményértékelési keretrendszer
A mai versengő fémművészet szakterületén a nyomósáv termelékenysége közvetlenül befolyásolja a műveleti haszonszerzést és piaci reakciós képességet. Ez a részletes elemzés rendszerezett megközelítést mutat be a nyomósáv teljesítményének értékeléséhez és javításához, amely technikai mértékezéseket kombinál a műveleti legjobb gyakorlatokkal annak érdekében, hogy mérhető fejlesztéseket hozzon létre a gyártási folyamataidban.
Kritikus termelékenységi tényezők a nyomósáv műveletekhez
1. Műveleti hatékonysági mértékek
A modern nyomósáv teljesítményének értékelése három kulcsfontosságú mutató figyelmét igényli:
Ciklusidő elemzés: Követheti a valós hajlítási ciklusokat a théoretiacus gépképességhez képest
Minőségi százalékos arány: Mérje az első áthaladási arányt a újragyártás százalékos arányával szemben
Energiafogyasztási mintázatok: Monitorozza a teljesítmény-használatot egyes termelési egységekönként
A fejlett CNC modellje mostantól beépített elemzési irányítópultokkal rendelkeznek, amelyek valós idejű OEE (Összes Egyesített Felszerelési Hatékonyság) pontszámokat biztosítanak, lehetővé téve az adatvezérelt döntéshozást.
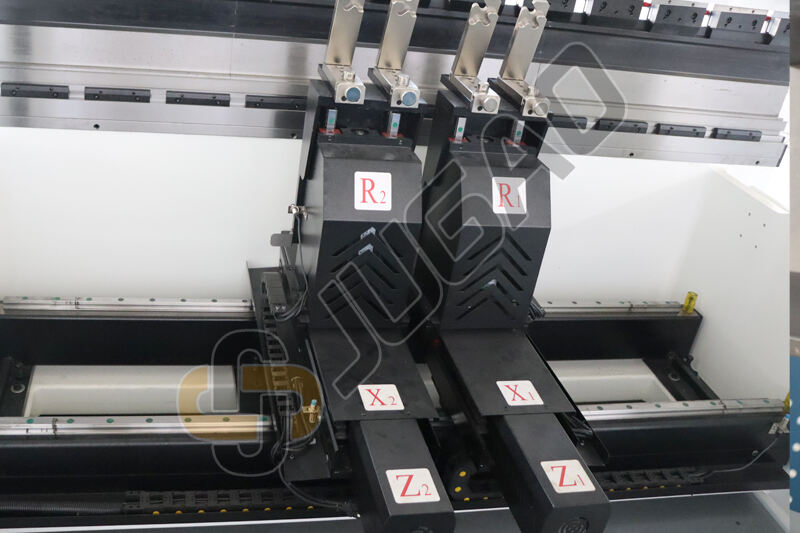
2. Munkafolyamat Optimalizálási Stratégiák
Munkafolyamat optimalizálása
Végrehajtsa a szárnyas gyártási elveket az érték nélküli tevékenységek megszüntetésére:
SMED (Egypérces Áramberendezés Váltás) Technikák: Csökkentse az eszközváltásokat 10 perc alá
Anyagfolyamat Tervezés: Állítson át a termelxő elrendezését a kezelési távolságok minimalizálására
Digitális Munka Nyomonkövetése: Állítsa be az MES rendszereket valós idejű gyártási figyeléshez
Ezek a módszerek általában 25-40%-os javulást eredményeznek a műveleti átviteli sebességben.
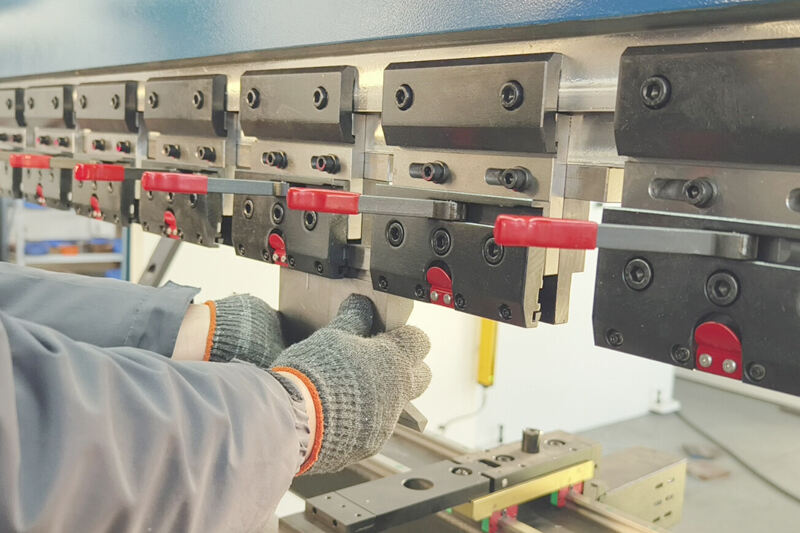
3. Emberi Erőforrás Fejlesztés
Szállítói képzés
Fejlesztesd ki a szintezett képesség-vizsgálati programot, amely fedettséget biztosít a következőkre:
Alapértelmezett gépoperáció (1. szint)
Haladó hibaelhárítás (2. szint)
Folyamatoptimalizálás (3. szint)
Több gépen való keresztszkálázás növeli a munkaerő rugalmasságát, amely lehetővé teszi a hátravetelt legfeljebb 30%-kal csökkenteni váltások vagy hiányosságok közben.
Haladó Technikák a Teljesítmény Növeléséhez
1. Előrejelzéses Karbantartási Rendszerek
Áttérés ütemezett karbantartástól állapotfigyelésre:
Reper igazításra vonatkozó rezgésanalízis
Hidraulikus folyadék minőségi érzékelők
Elektrikus komponensek infravörös képészése
Ezek a technológiák 85%-ot lehetővé tesznek a potenciális hibákból, mielőtt nem tervezett leállást okoznak.
2. Okos Automatizmus Integráció
Automatizációs megoldások
Értékelje ki az automatizációs lehetőségeket három szinten:
Alapvető Automatizmus: Automatikus eszkövcserélő
Középhosszúságú rendszerek: Robotikai anyagkezelés
Haladó megoldások: Mesterséges intelligenciára alapozott adaptív hajtás
Az ROI elemzés általában 12-18 hónapos visszatérési időt mutat comprehensieve automatizációs csomagok esetén.
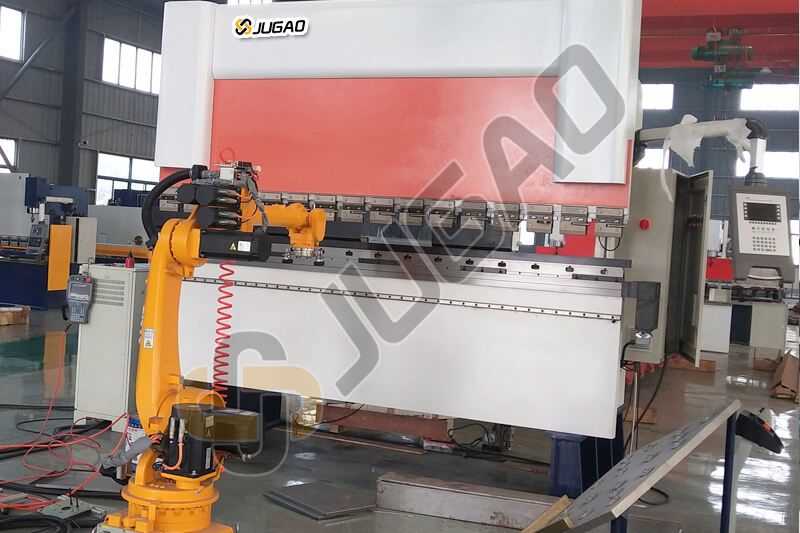
3. CNC Programozási Optimalizálás
Alkalmazza a haladó programozási technikákat:
Beágyazási algoritmusok: anyaghasznosítás maximalizálása
Ütközés szimuláció: virtuális tesztelés a hajlítási sorrendekben
Felhőalapú könyvtárak: központi programtár és verziókezelés
Ezek a módszerek általában 40%-kal csökkentik a programozási időt, miközben növelik a folyamat megbízhatóságát.
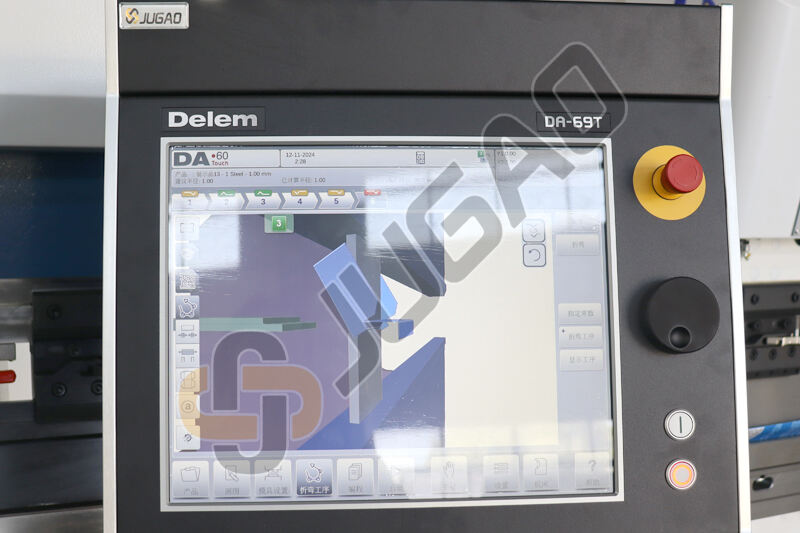
Szakértő Kérdés-Válasz: Nyomócsav termelékenység kihívásainak megoldása
K: Mi a legnagyobb hatású első lépés a nyomósztály termelékenységének javításához?
V: Végezzen átösszefoglaló idő-mozgás tanulmányt az egyik legnagyobb termelékenységi bottleneck azonosítására megoldások kivitelezése előtt.
K: Milyen gyakran kell mérnünk a nyomósztály teljesítményét?
V: Hajtsa végre negyedéves termelékenységi vizsgálatokat havi KPI-követéssel folyamatos fejlődés érdekében.
K: Melyik automatizálási beruházások adják a legrövidebb visszaesést?
A: Az automatikus eszközcsere-rendszerek általában a legnagyobb termelékenységi nyereséget hozzák viszonylag alacsony implementációs bonyolultsággal.
Stratégiai útmutató a folyamatos fejlesztéshez
Készítsünk el egy 12-hónapos termelékenységi növelési tervet:
1-3. hónap: Alapértelmezett kiértékelés és bottleneck azonosítása
4-6. hónap: Operátorok képzése és alapvető automatizmus bevezetése
7-9. hónap: Haladó folyamatoptimalizálás és előrejelzéses karbantartás
10-12. hónap: Rendszer teljes integrációja és teljesítmény érvényesítése
A strukturált megközelítést alkalmazó vezető gyártók általában elérik:
35-50%-os növekedést a feldolgozásban
25%-os csökkentést anyagi hulladékban
20%-os csökkenés az energiaállomány költségeiben egységenként
Azoknak a szervezeteknek, amelyek készen állnak arra, hogy átalakítják nyomókitermék műveleteit, egy technológiai szolgáltatóval való együttműködés, mint például a JUGAO CNC MACHINE, amely komprehenszív termelékenységi értékelési szolgáltatásokat kínál, gyorsíthatja az eredmények elérését, miközben minimalizálja a megvalósítási kockázatokat. A leghaladottságamba járó gyártók mostantól kombinálják ezeket a mechanikai fejlesztéseket digitális ikrek technológiájával, hogy szimulálják és optimalizálják a folyamatokat a fizikai megvalósítás előtt.