การเพิ่มประสิทธิภาพของเครื่องพับโลหะ: กรอบการประเมินผลการทำงาน
ในสภาพแวดล้อมการผลิตโลหะที่มีการแข่งขันสูงในปัจจุบัน ประสิทธิภาพของเครื่องพับโลหะส่งผลกระทบโดยตรงต่อผลกำไรในการดำเนินงานและความสามารถในการตอบสนองต่อตลาด การวิเคราะห์อย่างลึกซึ้งนี้นำเสนอแนวทางเชิงระบบในการประเมินและปรับปรุงประสิทธิภาพของเครื่องพับโลหะ โดยรวมเอาตัวชี้วัดทางเทคนิคกับแนวปฏิบัติที่ดีที่สุดในการดำเนินงานเพื่อสร้างการปรับปรุงที่วัดได้ในกระบวนการผลิตของคุณ
ปัจจัยสำคัญที่กำหนดประสิทธิภาพสำหรับการดำเนินงานของเครื่องพับโลหะ
1. ตัวชี้วัดประสิทธิภาพในการดำเนินงาน
การประเมินประสิทธิภาพของเครื่องพับโลหะสมัยใหม่จำเป็นต้องติดตามตัวชี้วัดหลักสามประการ:
การวิเคราะห์เวลารอบการผลิต: ติดตามรอบการงอจริงเทียบกับความจุของเครื่องตามทฤษฎี
อัตราผลผลิตคุณภาพ: วัดผลผลิตครั้งแรกเทียบกับเปอร์เซ็นต์งานที่ต้องแก้ไขใหม่
รูปแบบการใช้พลังงาน: ตรวจสอบการใช้พลังงานต่อหน่วยการผลิต
โมเดล CNC ขั้นสูงในปัจจุบันมีแดชบอร์ดวิเคราะห์ในตัวที่ให้คะแนน OEE (Overall Equipment Effectiveness) ในเวลาจริง ซึ่งช่วยในการตัดสินใจบนพื้นฐานของข้อมูล
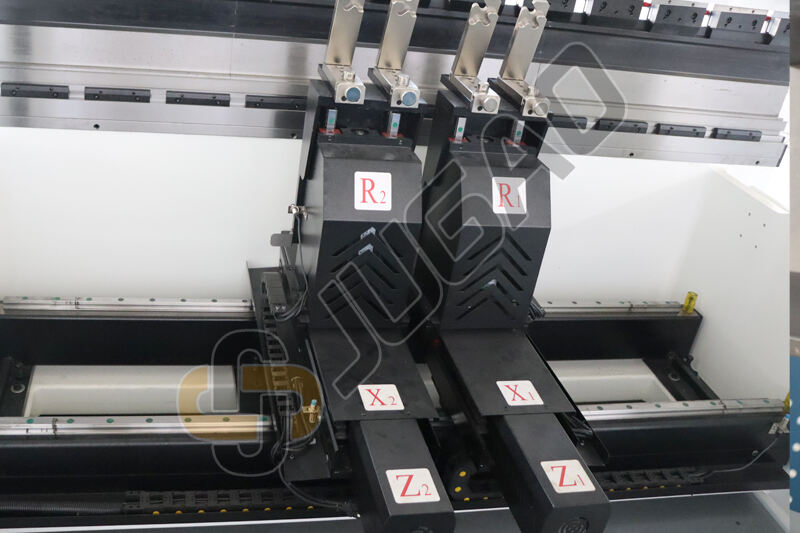
2. กลยุทธ์การเพิ่มประสิทธิภาพกระบวนการทำงาน
การปรับปรุงกระบวนการทำงาน
นำหลักการ lean manufacturing มาใช้เพื่อกำจัดกิจกรรมที่ไม่สร้างมูลค่า:
เทคนิค SMED (Single-Minute Exchange of Die): ลดเวลาในการเปลี่ยนเครื่องมือให้เหลือน้อยกว่า 10 นาที
การแผนที่การไหลของวัสดุ: ปรับโครงสร้างพื้นที่การผลิตเพื่อลดระยะทางในการเคลื่อนย้าย
การติดตามงานดิจิทัล: ใช้ระบบ MES เพื่อตรวจสอบการผลิตแบบเรียลไทม์
วิธีการเหล่านี้มักจะทำให้ประสิทธิภาพของการดำเนินงานเพิ่มขึ้น 25-40%
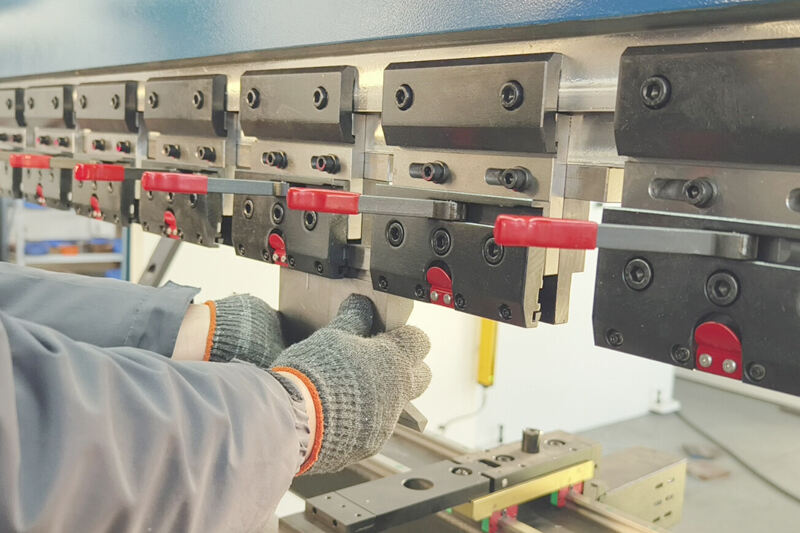
3. การพัฒนาทรัพยากรมนุษย์
การฝึกอบรมผู้ใช้
พัฒนาโปรแกรมรับรองทักษะแบบชั้นเชิงครอบคลุม:
การใช้งานเครื่องจักรพื้นฐาน (ระดับ 1)
การแก้ปัญหาขั้นสูง (ระดับ 2)
การเพิ่มประสิทธิภาพกระบวนการ (ระดับ 3)
การฝึกอบรมผู้ปฏิบัติงานให้สามารถใช้งานเครื่องจักรหลายประเภทสร้างความยืดหยุ่นในแรงงาน ซึ่งสามารถลดเวลาหยุดทำงานได้ถึง 30% ในช่วงเปลี่ยนกะหรือเมื่อมีการขาดงาน
เทคนิคขั้นสูงสำหรับการเพิ่มประสิทธิภาพ
1. ระบบการบำรุงรักษาแบบคาดการณ์
เปลี่ยนจากการบำรุงรักษาตามกำหนดเวลาไปสู่การตรวจสอบตามสภาพการทำงาน:
การวิเคราะห์การสั่นสะเทือนสำหรับการจัดเรียงแรม
เซ็นเซอร์คุณภาพของของเหลวไฮดรอลิก
การถ่ายภาพความร้อนของชิ้นส่วนไฟฟ้า
เทคโนโลยีเหล่านี้สามารถทำนายความล้มเหลวที่อาจเกิดขึ้นได้ 85% ก่อนที่จะก่อให้เกิดการหยุดทำงานที่ไม่ได้วางแผนไว้
2. การบูรณาการอัตโนมัติแบบอัจฉริยะ
โซลูชันการอัตโนมัติ
ประเมินโอกาสในการใช้อัตโนมัติในสามระดับ:
อัตโนมัติพื้นฐาน: เครื่องเปลี่ยนเครื่องมืออัตโนมัติ
ระบบกลาง: การจัดการวัสดุด้วยหุ่นยนต์
วิธีการขั้นสูง: การงอแบบปรับตัวด้วยปัญญาประดิษฐ์
การวิเคราะห์ ROI มักแสดงช่วงเวลาคืนทุนภายใน 12-18 เดือนสำหรับแพ็กเกจการอัตโนมัติแบบครบวงจร
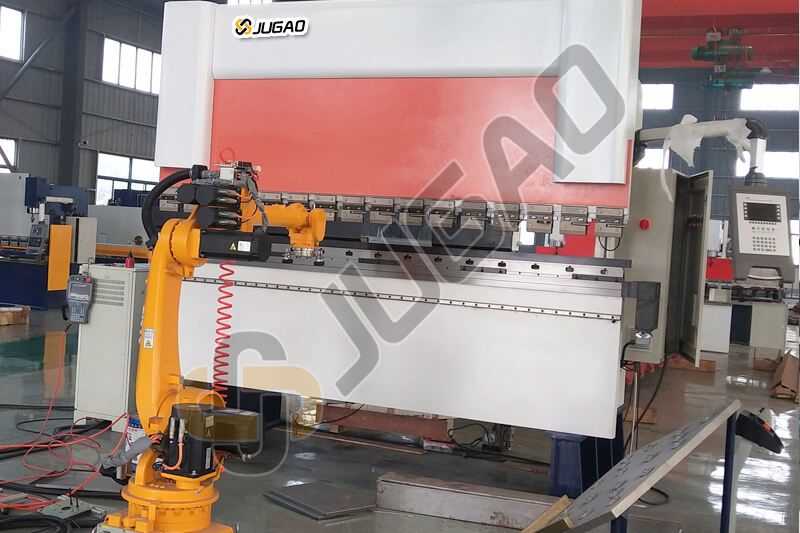
3. การเพิ่มประสิทธิภาพการเขียนโปรแกรม CNC
ใช้เทคนิคการเขียนโปรแกรมขั้นสูง:
อัลกอริทึมการซ้อน: ใช้วัสดุให้เต็มประสิทธิภาพสูงสุด
การจำลองการชน: การทดสอบเสมือนของลำดับการงอ
ไลบรารีบนคลาวด์: การเก็บโปรแกรมแบบศูนย์กลางและการควบคุมเวอร์ชัน
วิธีการเหล่านี้มักจะลดเวลาในการเขียนโปรแกรมลง 40% ในขณะที่เพิ่มความน่าเชื่อถือของกระบวนการ
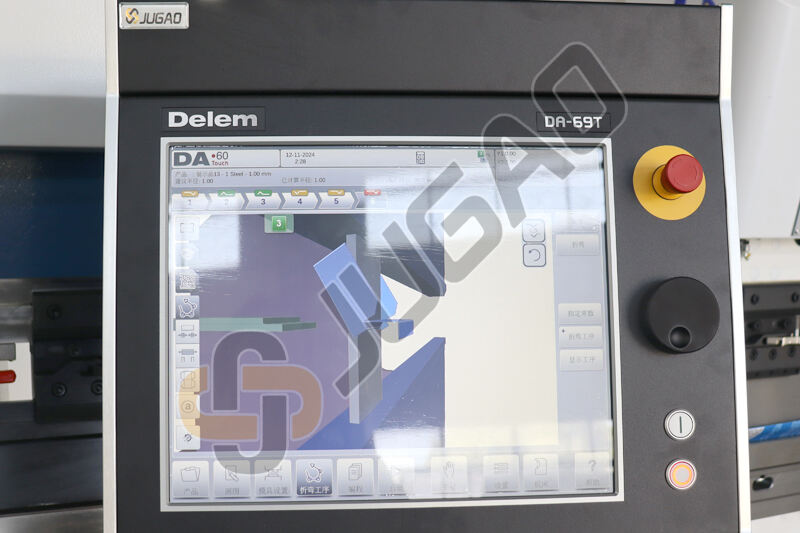
ถาม-ตอบกับผู้เชี่ยวชาญ: แก้ปัญหาความท้าทายในการผลิตของเครื่องพับโลหะ
คำถาม: ขั้นตอนแรกที่มีผลกระทบมากที่สุดในการเพิ่มประสิทธิภาพของเครื่องพับโลหะคืออะไร?
คำตอบ: ทำการศึกษาเวลาและแรงงานอย่างครอบคลุมเพื่อระบุจุดคอขวดด้านประสิทธิภาพที่ใหญ่ที่สุดก่อนการใช้โซลูชัน
คำถาม: เราควรตรวจสอบประสิทธิภาพของเครื่องพับโลหะของเราบ่อยแค่ไหน?
คำตอบ: ดำเนินการตรวจสอบประสิทธิภาพรายไตรมาสพร้อมการติดตาม KPI รายเดือนเพื่อรักษาโมเมนตัมของการปรับปรุงอย่างต่อเนื่อง
คำถาม: การลงทุนในระบบอัตโนมัติแบบใดที่ให้ผลตอบแทนเร็วที่สุด?
A: ระบบการเปลี่ยนเครื่องมืออัตโนมัติทั่วไปมักจะมอบผลลัพธ์ด้านประสิทธิภาพการทำงานอย่างรวดเร็วที่สุด โดยมีความซับซ้อนในการใช้งานค่อนข้างต่ำ
แผนที่เชิงกลยุทธ์สำหรับการปรับปรุงอย่างต่อเนื่อง
วางแผนเพิ่มประสิทธิภาพในช่วง 12 เดือน:
เดือนที่ 1-3: การประเมินเบื้องต้นและการระบุจุดคอขวด
เดือนที่ 4-6: การฝึกอบรมผู้ปฏิบัติงานและการนำระบบอัตโนมัติพื้นฐานมาใช้
เดือนที่ 7-9: การเพิ่มประสิทธิภาพกระบวนการขั้นสูงและการบำรุงรักษาเชิงป้องกัน
เดือนที่ 10-12: การผสานระบบเต็มรูปแบบและการตรวจสอบสมรรถนะ
ผู้ผลิตชั้นนำที่ใช้วิธีการเชิงโครงสร้างนี้มักจะประสบความสำเร็จดังนี้:
ปรับปรุงประสิทธิภาพการผลิตได้ 35-50%
ลดของเสียจากวัสดุลง 25%
ลดต้นทุนพลังงานลง 20% ต่อหน่วย
สำหรับองค์กรที่พร้อมจะเปลี่ยนแปลงการดำเนินงานของเครื่องพับโลหะ ความร่วมมือกับผู้ให้บริการเทคโนโลยีอย่าง JUGAO CNC MACHINE ซึ่งเสนอบริการประเมินผลผลิตแบบครบวงจรสามารถเร่งผลลัพธ์ในขณะที่ลดความเสี่ยงในการนำเสนอบนพื้นฐานได้ ผู้ผลิตที่ก้าวหน้าที่สุดในปัจจุบันกำลังรวมการปรับปรุงทางกลไกเหล่านี้เข้ากับเทคโนโลยีดิจิทัลทวินเพื่อจำลองและปรับแต่งกระบวนการก่อนการนำไปใช้งานจริง