Optymalizacja produktywności pras łamanych: Ramy oceny wydajności
W dzisiejszym konkurencyjnym świecie metalurgii produktywność pras gięciowych bezpośrednio wpływa na zyskowność operacyjną i reaktywność wobec rynku. Ten szczegółowy analizę przedstawia systematyczne podejście do oceny i poprawy wydajności pras gięciowych, łącząc metryki techniczne z najlepszymi praktykami operacyjnymi w celu uzyskania mierzalnych popraw w procesach produkcyjnych.
Kluczowe czynniki produktywności dla operacji pras gięciowych
1. Wskaźniki efektywności operacyjnej
Ocena współczesnej wydajności pras gięciowych wymaga monitorowania trzech kluczowych wskaźników:
Analiza Czasu Cyklu: Śledź rzeczywiste cykle gięcia w porównaniu do teoretycznej pojemności maszyny
Stopy Wyników Jakościowych: Pomiar efektywności pierwszego przejścia w stosunku do procentów ponownego przetwarzania
Wzorce Spożycia Energii: Monitoruj zużycie energii na jednostkę produkcyjną
Zaawansowane modele CNC obejmują teraz wbudowane tablice analizy dostarczające w czasie rzeczywistym wyniki OEE (Ogólna Efektywność Urządzeń), co umożliwia podejmowanie decyzji opartych na danych.
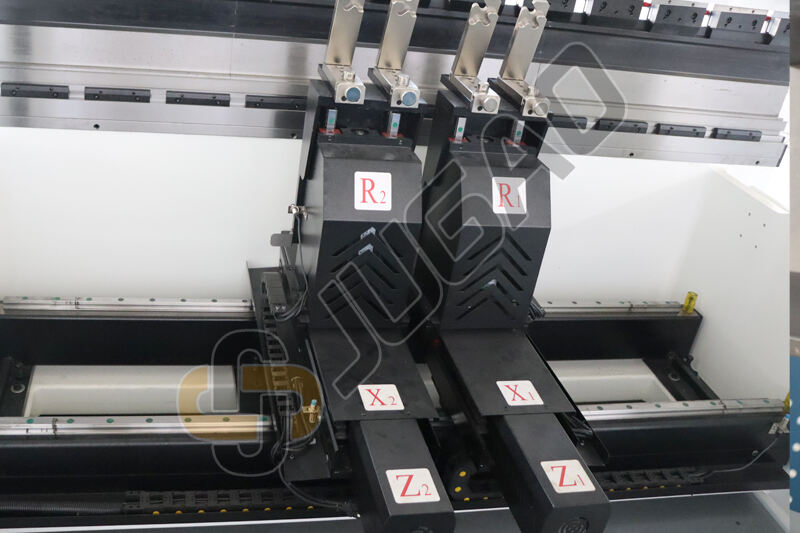
2. Strategie Optymalizacji Przepływów Pracy
Optymalizacja Przepływu Pracy
Zaimplementuj zasady wytwarzania szczupłego, aby eliminować działania nie dodające wartości:
Techniki SMED (Single-Minute Exchange of Die): Zmniejsz zmiany narzędzi do poniżej 10 minut
Mapowanie przepływu materiałów: Przegrupuj układy podłogi produkcyjnej, aby minimalizować odległości obsługi
Cyfrowe śledzenie zadań: Wprowadź systemy MES do monitorowania produkcji w czasie rzeczywistym
Te metody zazwyczaj osiągają poprawę wydajności operacyjnej o 25-40%.
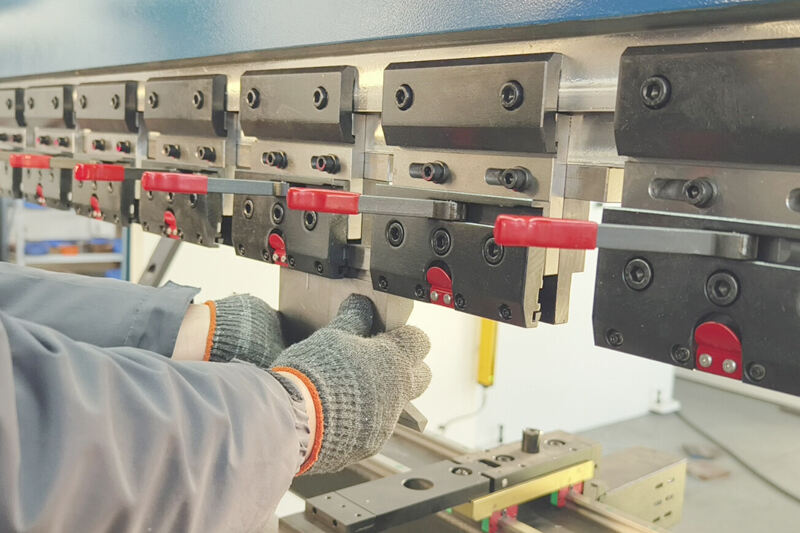
3. Rozwój Kapitału Ludzkiego
Szkolenia operatorów
Stwórz program certyfikacji umiejętności na kilku poziomach, obejmujący:
Podstawowe obsługa maszyn (Poziom 1)
Zaawansowane rozwiązywanie problemów (Poziom 2)
Optymalizacja procesów (Poziom 3)
Szkolenie operatorów w zakresie krzyżowym na wielu maszynach tworzy elastyczność kadry, która może zmniejszyć simplyfikację o do 30% podczas zmiany zmian lub nieobecności.
Zaawansowane techniki poprawy wydajności
1. Systemy konserwacji predykcyjnej
Przejście od planowanego serwisu do monitorowania opartego na stanie:
Analiza drgań dla wyrównania ramięcia
Czujniki jakości cieczy hydraulicznej
Termowizyjne badanie elementów elektrycznych
Te technologie mogą przewidzieć 85% potencjalnych awarii przed tym, jak spowodują nieplanowane wygasnięcia.
2. Integracja Automatyki Inteligentnej
Rozwiązania automatyzacyjne
Oceń możliwości automatyzacji na trzech poziomach:
Podstawowa Automatyzacja: Automatyczne zamienniki narzędzi
Układ Pośredni: Roboticzne obsługa materiałów
Zaawansowane Rozwiązania: Adaptacyjne gięcie sterowane sztuczną inteligencją
Analiza ROI zazwyczaj pokazuje okresy zwrotu inwestycji w przedziale 12-18 miesięcy dla kompleksowych pakietów automatyzacji.
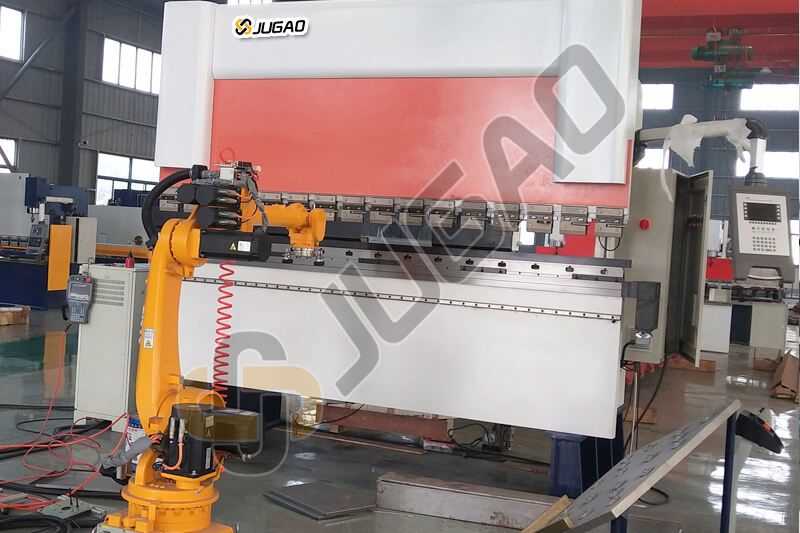
3. Optymalizacja programowania CNC
Zaimplementuj zaawansowane techniki programowania:
Algorytmy zagnieżdżania: Maksymalizacja wykorzystania materiału
Symulacja kolizji: Wirtualne testowanie ciągów zginania
Bazy danych w chmurze: Centralne przechowywanie programów i kontrola wersji
Te metody zazwyczaj redukują czas programowania o 40%, jednocześnie poprawiając niezawodność procesu.
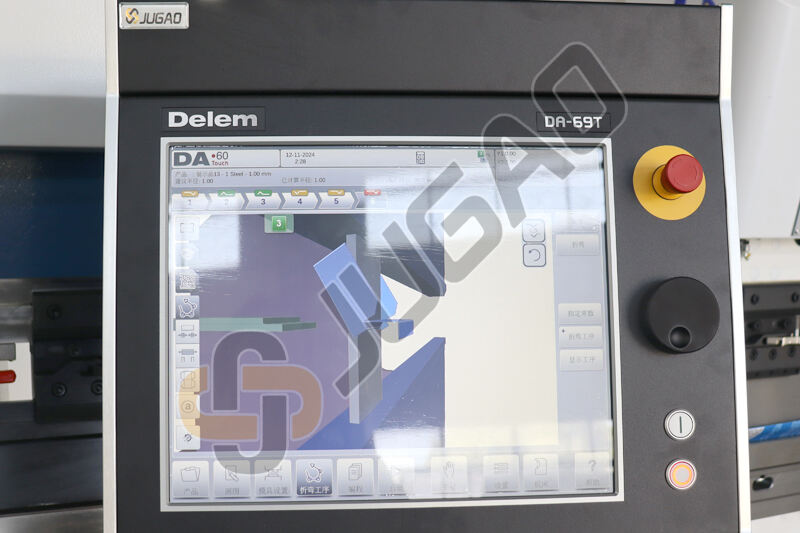
Pytania i odpowiedzi eksperta: Rozwiązywanie wyzwań produkcyjnych pras do zginania
Q: Jaki jest najbardziej istotny pierwszy krok, aby poprawić wydajność pras hamulcowych?
A: Przeprowadź kompleksowe badanie czasu-ruchu, aby zidentyfikować największe ograniczenia wydajności przed wdrożeniem rozwiązań.
Q: Jak często powinniśmy badać wydajność naszych pras hamulcowych?
A: Wykonuj audyty wydajności co kwartał z miesięcznym śledzeniem KPI, aby utrzymać dynamiczny postęp.
Q: W które inwestycje w automatykę otrzymujemy najszybsze zwroty?
A: Systemy automatycznego wymiany narzędzi zazwyczaj przynoszą najbardziej natychmiastowe zyski produkcyjne przy względnie niskiej złożoności implementacji.
Strategiczna mapa drogowa dla ciągłej poprawy
Wypracuj plan wzmocnienia produktywności na 12 miesięcy:
Miesiące 1-3: Ocena punktu wyjścia i identyfikacja garloków
Miesiące 4-6: Szkolenie operatorów i implementacja podstawowej automatyki
Miesiące 7-9: Zaawansowana optymalizacja procesu i pielęgnacja predykcyjna
Miesiące 10-12: Pełna integracja systemu i walidacja wydajności
Wiodące producenci, którzy stosują ten strukturalny podejście, zazwyczaj osiągają:
poprawa przepływności o 35-50%
obniżenie odpadów materiałów o 25%
20% spadku w kosztach energii na jednostkę
Dla organizacji gotowych przekształcać swoje operacje pras CNC, współpraca z dostawcami technologii JUGAO CNC MACHINE, którzy oferują kompleksowe usługi oceny produktywności, może przyspieszyć wyniki jednocześnie minimalizując ryzyka implementacji. Najbardziej postępujące producenti łączą teraz te ulepszenia mechaniczne z technologią cyfrowego bliźnia, aby symulować i optymalizować procesy przed ich fizyczną realizacją.