Przyszłe ścieżki ewolucji innowacji technologicznych w prasach dogięciowych
Spis treści
Rewolucja Automatyzacji: Przekształcanie Paradigmat Produkcji
○ Integracja Inteligentnej Linii Produkcji
○ Postępy w Systemach Sterowania Adaptacyjnego
Cyfrowy Ekosystem: Produkcja Definiowana Oprogramowaniem
○ Technologia Cyfrowego Bliźniaca od Końca do Końca
○ Głęboka Integracja IoT w Przemysle
Zielona Transformacja: Zrównoważone Praktyki Producentów
○ Systemy Zarządzania Energii w Zakresie Cyklu Zamkniętego
○ Innowacje w projektowaniu zgodności środowiskowej
Zbieżność technologiczna: Perspektywa rozwiązań next-gen
Podstawowa analiza techniczna
Rewolucja Automatyzacji: Przekształcanie Paradigmat Produkcji
Integracja inteligentnej linii produkcyjnej
Nowoczesna automatyzacja prasów łamanych ewoluowała od ulepszeń pojedynczych maszyn do pełnej współpracy całej linii. Poprzez integrację robotów kolaboracyjnych o sześciu osiach, systemów obsługi materiałów AGV oraz modułów inteligentnego magazynowania, producenci osiągają działania bez załogi, począwszy od ładowania surowców po sortowanie gotowych produktów. Takie systemy poprawiają ogólną wydajność o ponad 40%, podczas gdy technologia pozycjonowania wizyjnego gwarantuje powtarzalność gięcia w granicach ±0,05 mm, znacząco redukując wahania jakości spowodowane przez intervencje ręczne.
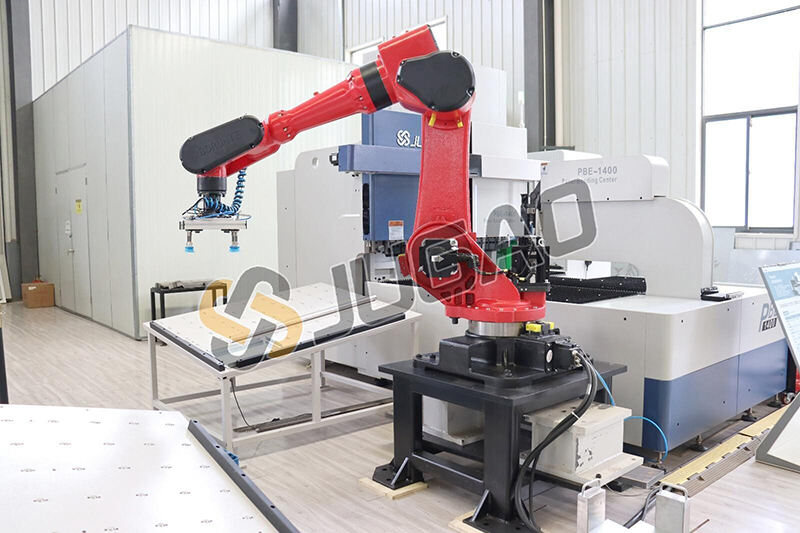
Przełomy w systemach sterowania adaptacyjnego
Systemy sterowania adaptacyjnego napędzane przez algorytmy uczenia głębokiego stają się odniesieniami branżowymi. Dzięki pozyskiwaniu danych w czasie rzeczywistym z czujników ciśnienia, laserowych detektorów zasięgu oraz innych wieloplatformowych wejść, te systemy dynamicznie optymalizują algorytmy kompensacji kąta. Na przykład, podczas obróbki stalí o wysokiej wytrzymałości z istotnymi efektami sprężystego powrotu, system automatycznie dostosowuje otwory matryc, poprawiając dokładność kompensacji z ±0,3° (tradycyjne wartości empiryczne) do ±0,1°. Ta samorozwijająca się logika umożliwia zespołom dostosowywanie się do coraz bardziej skomplikowanych wymagań dotyczących przetwarzania multi-materiałów.
Cyfrowy Ekosystem: Produkcja Definiowana Oprogramowaniem
Technologia cyfrowych bliźniąt od początku do końca
Głęboka integracja oprogramowania CAD/CAM z fizycznym sprzętem spowodowała powstanie platform cyfrowych bliźniąt. Inżynierowie mogą wykonywać pełnoprocessowe weryfikacje – od modelowania 3D, przez symulację procesów po analizę naprężeń – w środowiskach wirtualnych, dokładniej przewidując deformację blach podczas gięcia. Studia przypadku pokazują, że ta technologia skróciła cykle próbnych formowań dla producenta części samochodowych z 15 dni do 72 godzin, przy jednoczesnym zmniejszeniu marnotrawstwa materiału o 22%.
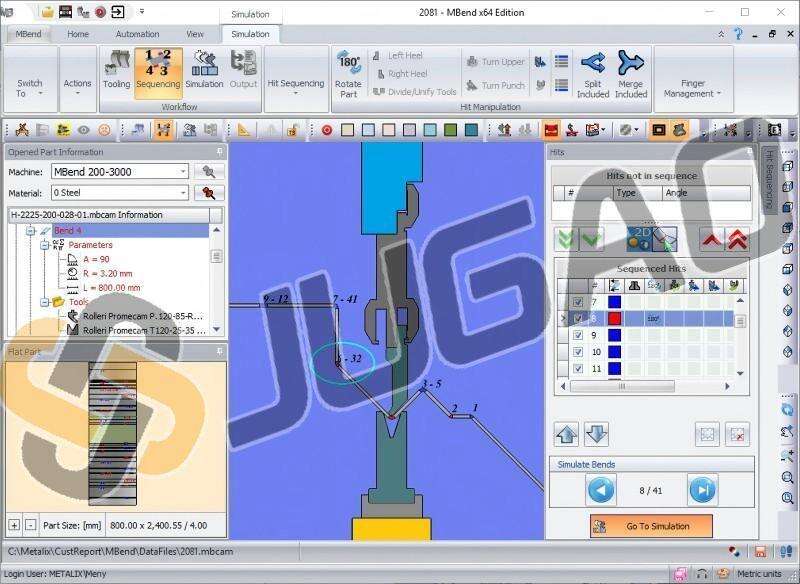
Głęboka Integracja Przemysłowego IoT
Systemy monitoringu zdalnego wspierane przez 5G i architektury obliczeń brzegowych osiągają reaktywność na poziomie milisekund. Wdrażając czujniki analizy drgań oraz moduły monitorowania stanu hydraulicznego oleju, sprzęt może przewidywać awarie kluczowych elementów (np. łożysk silników serwospoja) 14 dni wcześniej. Ponadto, systemy certyfikacji danych procesowych oparte na blockchainie spełniają surowe wymagania dotyczące śledzenia w produkcji lotniczej.
Zielona Transformacja: Zrównoważone Praktyki Producentów
Zamknięte Systemy Zarządzania Energiią
Następne generacje elektrycznych serwomechanizmów do gięcia wykorzystują technologię inwertera dwukierunkowego, aby zwrócić energię hamowania do sieci, co pozwala zmniejszyć zużycie energii o 65% w porównaniu do tradycyjnych modeli hydraulicznych. Dane eksperymentalne wskazują, że systemy hybrydowe z superkondensatorami odzyskują 32% energii bezwładnościowej podczas ciągłego przetwarzania blach nie rdzewiejących o grubości 2 mm, osiągając roczną redukcję emisji węgla o 8,6 ton na maszynę.
Innowacje w projektowaniu zgodnym z normami środowiskowymi
Systemy hydrauliczne o niskim poziomie hałasu zgodne ze standardami ISO 50001 wykorzystują synergę między pompy zmiennymi i akumulatorami, aby zmniejszyć hałas podczas bezczynności z 85dB(A) do 72dB(A). Zastąpienie oleju mineralnego fluidami hydraulicznymi o podstawie biologicznej obniża emisje VOC o 46% w cyklu życia urządzenia, co jest zgodne z regulacjami EU EcoDesign 2025.
Zbieżność technologiczna: Perspektywa rozwiązań next-gen
Hybrydowe układy napędowe elektro-hydrauliczne przekraczają tradycyjne granice: Układy hydrauliczne umożliwiają szybkie karmienie podczas ścięcia wstępтельного, podczas gdy tryby elektryczne serwowe zapewniają precyzję w fazie doboru, osiągając liderujący w branży stosunek efektywności do zużycia energii wynoszący 1:0,78. Ponadto algorytmy optymalizacji procesów napędzane technologią obliczeń kwantowych mają skrócić czas programowania złożonych zakrzywionych zginaniek do kilku minut do 2025 roku.
Podstawowa analiza techniczna
Wymiar techniczny | Innowacyjna wartość |
Automatyzacja | Umożliwia produkcję ciągłą 24/7, redukuje koszty pracy o 57% i zwiększa WSK (Współczynnik Skuteczności Urządzeń) do 89% |
Cyfryzacja | Skraca cykle rozwoju produktów o 40%; bazy danych procesowych podnoszą wydajność szkoleń dla nowych pracowników o 300% |
Zrównoważony rozwój | Obniża całkowite zużycie energii o 52%, odcisk węglowy o 38% i koszty zgodności o 65% |
Podsumowanie
Fala innowacji w technologii pras zginających postępuje wzdłuż trzech osi: inteligencji, cyfryzacji i zrównoważonego rozwoju. W ciągu najbliższych pięciu lat poznawcze prasy zginające z możliwościami samodiagnostyki, platformy współpracy produkcyjnej oparte na chmurze oraz rozwiązania napędzane wodorem o zerowym emisji dwutlenku węgla mogą przedefiniować konkurencję w przemyśle formowania metali. Dla producentów, przyjęcie tych trendów jest nie tylko kluczowe dla wzmożonej konkurencyjności, ale również niezbędną ścieżką w kierunku transformacji w ramach Przemysłu 4.0.