Nyomósztály Eszközök
Mi az a hajlítógép mátrixa?
Definíció és fő funkciók
A hajlítógép egy eszköz, amelyet fémlapok hajlítására használnak, amely képes alkatrészeket alakítani előírt formába és méretekké a hajlítógép nyomása alatt.
A hajlító gép mátrixa egy ütő és egy alsó mátrixból áll, amelyek egymással együttműködve vannak a fúratok, alakzatok és szivattyúk készítésére. Az alakításra szolgáló mátrix üres teret (hanyagot) tartalmaz, míg a szivattyúra szolgáló mátrix vágóéllel rendelkezik.
Kezdők számára fontos megérteni, hogy a hajlító gép mátrixának fő célja lehetővé tenni a gépnél a különböző fémtípusok hajlítását különböző szögekre. Ebben a folyamatban egy fémrész lecsúszik két eszköz között: a felső eszköz (ütő) lemen a also eszközre (mátrix), hogy hajlítson a fémrészét.
A hajlító gép mátrixaikat kézzel művelt, hidraulikus és CNC hajlító gép mátrixokra osztják. A hidraulikus hajlító gép mátrixaikat szinkronizációs módszer szerint forgástengelyes szinkronizálásra, gép-hidraulikus szinkronizálásra és elektro-hidraulikus szinkronizálásra osztják. A hidraulikus hajlító gép mátrixaikat mozgás szerint felfelé és lefelé típusokra osztják.
Fontossága a fémlapok hajlításában
Határozza meg a hajlítás formáját és a méretei pontoságát: A forma alakja és mérete közvetlenül meghatározza a hajlítás formáját, például a szöget, a görbület sugara stb., amely közvetlen kapcsolatban van a termék minőségével.
Ellenőrizze a hajlítási folyamatot: Az eszköz rögzítheti a fémes lapot egy adott pozícióban és ellenőrzi a nyomás hatására történő deformációját annak érdekében, hogy karbantartsa a hajlítás egységességét.
Növelje a gyártási hatékonyságot: A forma gyors cseréjével különböző termékek forma váltását néhány milliszekundumban lehet befejezni, ami jelentősen rövidíti a váltási ciklust.
Hosszabbítja az élettartamot: A keményanyagból készült és felületi kezelésre támaszkodó eszközök élettartama többszörösére növekszik.
Csökkenti a gyártási költségeket: A pontossági formák használata növeli a termelékenységet és csökkenti a formafeltételt okozó hulladék arányát.
Konkrét követelmények elérésére: A CNC technológia segítségével a formot bármilyen alakzatba alakítható, hogy megfeleljen egyes konkrét termékek gyártási követelményeinek.
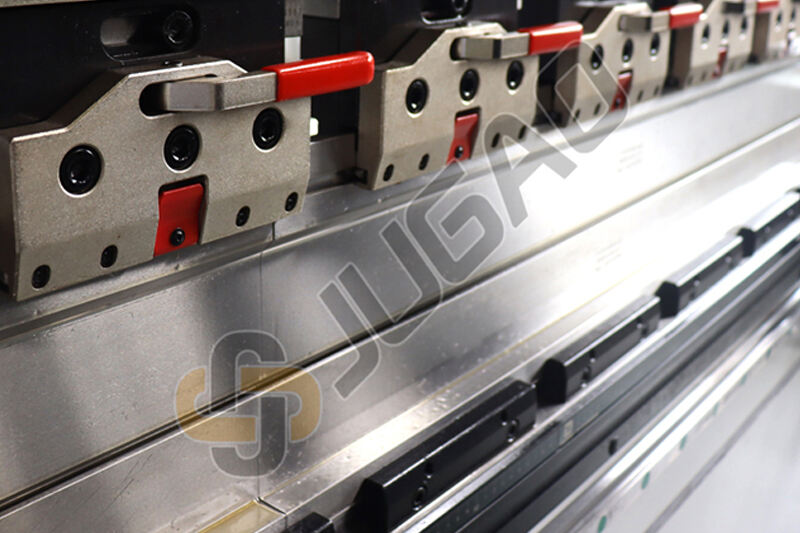
Nyomósztály Eszközgyüjtemények
Tömörítők és Formák
Ők azok a kulcskomponensek, amelyek meghatározzák a hajtott munkatétel alakját, és felszerelve vannak a felső és alsó nyomóvarrákon, hogy irányítsák a fémlap hajtásának területén történő deformációt.
Formagyűrök
Ezen platformok támogatják és pozicionálják a felső.clipsToBounds és az alsó meghajtókat. Összekapcsolva a nyomás alatti Clipperszel, hogy lehetővé tegye a gyors eszközváltást. Különösen hasznosak a konzisztencia megőrzésében több termelési futam között.
Kanyarítási Segédeszközök
Hogy segítsék az operátorokat gyorsan és kényelmesen befejezni a kanyarítási feladatokat, néhány segédeszköz, például szög mérő eszközök és helyezkedési blokkok néha használni. Ezek az eszközök nagyon fontosak a magas pontosságú alkalmazásokban, ahol még a legkisebb eltérések is befolyásolhatják a végterméket.
Gyors Váltó Rendszerek
Sok modern nyomás alatti kanyarítógép rendelkezik gyors váltó rendszerekkel, amelyek lehetővé teszik az operátorok számára a felső clipper és az alsó meghajtó gyors cseréjét különböző kanyarítási feladatok elvégzéséhez.
Ez a képesség döntően fontos a magas-kötésű, alacsony-termelési környezetekben, ahol gyakran kell eszközváltást végezni a különböző hajlítási feladatok igényeire. Például egy munkahelyi környezetben a gyors váltórendszer lehetővé teszi a különböző projektek közötti gyors átváltást, amely növeli az általános hatékonyságot.
Elhelyezési rúdszárnyalatok
Ezeket az eszközöket a munkaadó pontos pozicionálására és rögzítésére használják a hajlítási folyamat során. Ez elengedhetetlen azonos hajlítás ismételt végrehajtásához.
Hajlító védelmi elemek
A hajlító védelmi elemeket a hajlító szélén telepítik a munkaadó éles sarokainak védelmére, amely meghosszabbítja a hajlító élettartamát. Különösen fontosak, amikor törékeny vagy nagy értékű anyagokat dolgoznak fel.
A záróelemek
A záróelem-összekötő a punch interfészhez gyors telepítést és eltávolítást tesz lehetővé a záróelemek számára. Ez a funkció hasznos olyan környezetekben, ahol a záróelemeket gyorsan kell cserélni a termelési hatékonyság fenntartása érdekében.
A szennyezőanyag-tartalom
Osztályosítsa el egyenletesen a smirgelem sugarát a munkalap keményedésének és égésének csökkentése érdekében.
Záróelem Padok/Modulok
Azokat a tenonzaló támogatására és az eszközszettelépítés segítésére használják. A merevesség nagyon fontos.
Kötélék
A hajlítás mélységének ellenőrzéséhez tartassa állandónak a hajlítási felületek közötti távolságot.
Mérőeszköz elmozdulások
Azokat a hajlított részek eltávolítására használják, és beállítási célokra is alkalmazhatók.
Eszköz-tartók
A feszítőeszközök rögzítik a mátrixot a nyomóra. A modern feszítőeszközök gyakran rendelkeznek gyorscsere mechanizmusokkal, amelyek növelik az termelékenységet a beállítási idő csökkentésével. Például, egy magas-változatos termelési környezetben, a gyorscsere feszítőeszközök lehetővé teszik a művelettörések közötti gyors váltást, minimalizálva az állásidőt.
Ragadó Rendszerek
A ráncolórendszer általánosan szorítógépkészleteket, szorítógép blokkokat és beállítási gömböket használ, hogy megfelelően helyezze el a ráncolókat és a mátrixokat. Biztos szorítás alapvető ahhoz, hogy megakadályozza az eszköz mozgását a ráncolási folyamat során, ami hibákat okozhat. Például, a nagy erősségű acél ráncolásakor egy erős ráncolórendszer biztosítja a mátrix stabilitását magas nyomás alatt.
Nyomásalapú vékonyító eszközök típusai
Ráncoló profilok
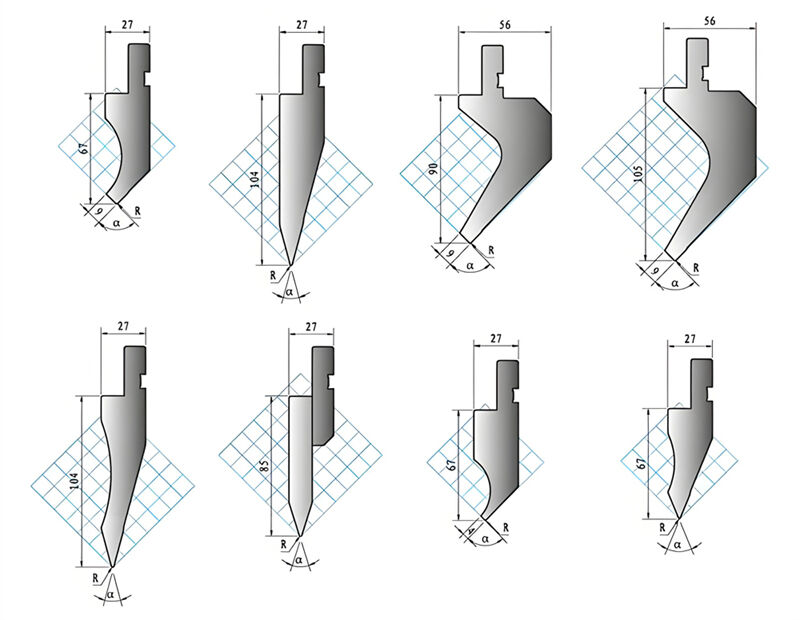
A ráncoló a felső eszköz a nyomó ráncoló berendezésben, és a nyomóráncoló csúszkájára van rögzítve. Erőt alkalmaz a munkaadaton, hogy a ráncoló alakjában történjen a ráncolás. A ráncolók különböző tervekben érhetők el, amelyek különböző lapacsvonal ráncolási igényekre és anyag típusokra vonatkoznak.
Szabványos ráncolók
A szabványos lyukastestek vastag testűek és szűk tippel rendelkeznek, többfelhasznósak és gyakran használnak általános hajlítási feladatokhoz és magas tonnás alkalmazásokhoz. alkalmasak szabványos hajlításokra, például 90 fokos szögek készítésére különféle anyagokon. Például egy szabványos lyukastestet használhatunk jobb szögű hajlításra lágy acél lapra, így több munkaadat esetén is konzisztens eredményt érhetünk el.
Éles szög felső meghajtó
Az éles szögű lyukastest 30-60 fokos szögekhez használatos, vastag testtel és éles tippel rendelkezik. Általában kevesebb, mint 30 fokos hajlításokhoz használják, és képes kezelni szögeket legfeljebb 89 fokig. A lyukastest tippje szöge általában 28° és 34° között van.
Tipikus méretekről
Tengely távolsága: Változik 1" és 1,5" között
Munka magasság: Általában körülbelül 3,75".
Tipp sugar: Változik 1/32" és 1/8" között.
Légyhasú punchok
A légyhasú punchok behúzott profillal rendelkeznek, amely lehetővé teszi a bonyolult hajtásokat anélkül, hogy a munkaadó megzavaródna. A U-profilokra tervezték ezeket a punchokat, amelyek tökéletesek mély dobozok és más bonyolult alakzatokhoz. A légyhasú punchok hosszabb testtel és behúzott területtel rendelkeznek annak érdekében, hogy elkerüljék a munkaadó lábainak ütközését. Például, amikor egy mély U alakú csatornát készítünk fémlapban, a légyhasú punch a szükséges távolságot biztosítja az anyag károsodásának elkerülése érdekében.
Ablakkeret punchok
Ablakkeretű ütők szűk testesek és ferde tippel rendelkeznek, amelyek lehetővé teszik a hajlítást és a sarokok körül való munkavégzést. A tipp belép a hajlító eszközbe. Mindkét oldalon ferde lehet a hajlítás, gyakran ablakkeretek és ajtokeretek készítésére használják, és hatékonyan feldolgozható lapacs a keretgyártáshoz.
Szűk/Szabla Ütők
Az egész hosszúságukon át egyenletes vastagságúak, a szűk ütők geometriája egyenes, nem jár sarokon, ami megfelel az olyan helyzetekben, ahol korlátozott a tér, ideálisak a dobozcsuklók végleges hajlítására, és alkalmasak korlátozott területeken végzett műveletekre.
Sugár Tetejű Ütők
A sugaras tetejű ütő kerek tippel rendelkezik, nem élesélű, tehát tervezése arra vonatkozik, hogy kerek hajlításokat végezzen, és használható standard V-alapú meghatározókkal jelölési műveletekhez és sima görbített profilok létrehozásához. A test általában vastagabb, hogy el tudja viselni a szükséges hajlítási erőket.
Joggle Punches (Z Tools)
A Joggle punch különleges alakú, ami eltolásos hajtást termel, és speciális alkalmazásokban használnak S alakú profilok létrehozására. Ez egy speciális eszköz, általában konkrét személyre szabott munkákhoz használt, két hajtást egyszerre készítve. Vácánnyal végzett profilt bírál, mint a szokványos punch.
Alsó Mátrix
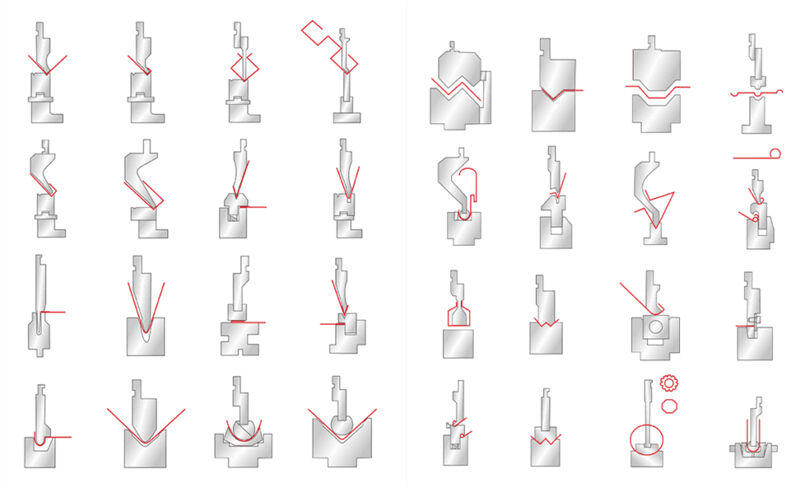
Az alsó mátrix a nyomásalapú mátrix alsó eszköze, és az alapján telepítik a nyomásalapú mátrixon. Amikor a punch lehajtható, biztosítja azt a reakciós erőt, amely szükséges a fémmegalkotásra. A mátrixok különböző alakúak és méretűek lehetnek, hogy különböző típusú hajtásokat hozzanak létre.
V-mátrix
A V-formú mátrix a leggyakoribb típusú mátrax, és érhető el egyesülésben, dupla V és többes V alakzatokban. Jellemzően alakzatos csatornával rendelkezik. Használatos V-formájú törések előállítására a munkaadatokban. A V/csatorna szélessége és mélysége meghatározza a végső töréskutat és ívét. Rendelkezésre áll négyirányú modul részeként könnyű cserélhetőség érdekében.
U-mátrax
A 'U' formájú mátraxok csatornák és mélyebbre törések készítésére használhatók, ideálisak bonyolultabb alakzatok igénylő műveletekhez. Tervezve U- vagy C-formájú törések elkészítésére, ez a mátrax törések készítésére alkalmas 90° és 180° között. Például mély csatornák alkotásához fém lapokban szerkezeti részekhez, a 'U' formájú mátraxok biztosítják az egyenletesiséget és erősséget.
Laposító mákok
A laposítómátraxok felhasználásra kerülnek a törött anyag laposítására, hogy garantáljanak sima és fejlesztett végzetet. Ezek a mátraxok alapvetőek a végtermék professzionális kinézetének eléréséhez, például a lapos fémlapoknak az autótestrészek gyártásához.
Offset nyomók
Az offset nyomók Z alakú vagy offset görbítéshez való alkalmazásra szolgálnak, két szöget hoznak létre egyetlen ütésben. Növelik a pontosságot, mivel a görbüléseket párhuzamossá teszik.
Sugárnyomók
A sugárnyomókat kerek punchokkal együtt használják a sugár alakú görbítések elérésére, amelyek egy sima, ívelt profilhoz vezetnek.
Légyfa alapú nyomók
A lúdhasú alakú mátrix olyan tervezésű, amely elkerüli a munkaadat interferenciáját, lehetővé téve a szoros térben vagy meglévő görbések körül való hajtást. Főként arra használják, hogy eltávolítsák a munkaadaton lévő kiálló éleket vagy flángokat, és alkalmas mély dobozok vagy magas flángú profilok hajtására.
Flángoló Mátrixok
A flángoló mátrixokat használják rácsok vagy élek létrehozására, amelyek javítják a vizuális megjelenést és erősítik a laposfém részek élei.
Csatornaformozó Mátrixok
A csatornaformozó mátrixok egyetlen ütésben alkotnak U alakú csatornákat, ami hatékonyabb, mint a hagyományos V alakú mátrixokkal történő U alakú csatornák kialakítása.
Laposító mákok
A laposító mákokat éles szögű hajtások teljes kijárására használják, és gyakran együtt használják a falatbevonással végzett műveletekkel.
Négyirányú mákok
A négyirányú mákok V alakú csatornát tartalmaznak, amelynek minden oldala más-más méretű egyetlen mákon. A többszörös hajtási mákokat egy műveletben két vagy több hajtás elkészítésére használják, beleértve az offset mákokat is ilyen speciális típusok között.
Hajtási gép-mákok típusai
Esztélytípus |
Jellemzők |
Alkalmazás |
Előnnyel |
Americantools |
- 30 fokos éles szögek mind a nyomó, mind a meghajtó oldalon. |
-Különféle anyagerjesek és profilok hajlítási műveleteire alkalmas. |
-Állható és megbízható, különféle feladatokra használható. |
Európai pontosságú eszközök |
-Ismeretes a "Promecam" eszköznek. |
-Alkalmas magas pontosságra vonatkozóan igényes hajtás alkalmazásokra. |
-Csökkenti az éles szögek által okozott visszapattantást, javítja a hajlítási pontosságot. |
NewStandard Eszköz |
-Osszefüzi az amerikai és európai jellemzőket. - A páncél és a matrica 45-fokos éles szögű. - Kompatibilis az amerikai és európai hajlítógépekkel. |
-Alkalmazható különféle hajlítási igényekre. - Népszerű olyan termelési környezetekben, amelyek pontoságát és rugalmasságot igényelnek. |
-A gyors eszközcsere növeli a műveleti hatékonyságot. -A versenyképesség és a pontosság egyensúlyát teremtve, széles körű projektekhez alkalmas anélkül, hogy nagyobb módosításokra lenne szükség a gépen. |
VelatonRapid Tooling |
-Általánosan TruPunch rendszerekhez használt - Nagy pontosság, kis tűrőtlenség |
-Főként magas pontosságú nyomtatási feladatokra használják, például precizionkomponensek feldolgozására. -Alkalmazható olyan gyártási igényekre, amelyek pontos és gyakori eszközcsereket igényelnek. |
-Magas pontosság, magas fokú szabványosítás, gyors eszközcserének képesség. -Hosszabb eszközéletkor, magasabb pontosság. -Erős eszközkompatibilitás, alkalmas különféle típusú gépeszközökhez. |
Összegzés
A Wila gyorscsere-eszközrendszer főként olyan helyzetekben használatos, amelyek nagy pontosságot és gyakori eszközcsere-t igényelnek, lehetővé téve a gyors eszközcserét, és alkalmas precíziós komponensek feldolgozására.
Az amerikai formák jellemzői alacsony költség és nagy termelési méret, alkalmasak tömeges termelésre alacsonyabb pontossági követelményekkel.
Az európai formák pontosságot és stabilitást értelmeznek, alkalmasak olyan iparágakban, mint az autóipar, az elektronika és a repülőipar, ahol magas pontossági követelmények vannak.
Az új szabványeszközök rendelkeznek erős kompatibilitással és alkalmazkodással, lehetővé téve a gyors beállításokat és a termelési hatékonyság javítását különféle környezetek között.
Anyagszivárgás választása nyomóhajtású formákhoz
A hajlító formák hatékonysága és élettartama szorosan kapcsolódik a forma erősségéhez és anyagához. A hajlítási folyamat során jelentkező nagy nyomás és súrlódás miatt a forma összetétele és kezelése döntően fontos.
A magas erősség és súrlódásellenes tulajdonságok jelentősége
A hajlítógép eszközei képesek megállni a működés során fellépő nagy nyomást. A magas erősség biztosítja, hogy az eszközök nem térváltoznak vagy törnek, amikor nyomást gyakorolnak.
Továbbá, a súrlódásellenes tulajdonságok kulcsfontosságúak, mivel azok határozzák meg a felhasználó szolgáltatási idejét. A súrlódásellenes eszközök hosszú távon fenntarthatják alakjukat és funkcióikat, így konzisztens hajlítási hatást biztosítanak és csökkentik a rendszeres cserék szükségességét.
Keményített eszközök
Egy módszer a rugalmasság és a hosszú tartóság javítására nyomósztályon keresztül az, hogy merevítjük a formákat. Specifikusanyagok használata nyomósztály-formákhoz népszerű az eleji merevségük miattés az abban rejto lehetőségek miatt további merevítésre.
Például
Krom-molybdén acél: ez az ötvözet híres a durva erőssége és a kölcsönhatóerő ellenállásáért, amely egyensúlyt teremt a nyomósztály erősségének és hosszútartóságának között, biztosítva, hogy a szerszám ki tud tartsa a nehégsavarási műveleteket anélkül, hogy túl korán elnélkülne a kölcsönhatóerőtől.
Yasuki acél: a Yasuki acél magas minőségu acél, amelyet általánosanhasználnak specializált eszközök gyártására, hírességét a kiváló merevsége ésdermesztéke miatt kapja. Összetétele éles éleket tart fennt, ami teszi azideális választásnak a pontos és savarási feladatokhoz.
Meleg finomítási eszközök
Az erekedés vagy hőkezelés egy folyamat, amely javítja a fémeszközök tulajdonságait. A fémet irányított melegítési és hűtési ciklusokkivonatkoztatásával megváltoztatja molekuláris szerkezetét, így javítja teljesítményét.
Például
A hőkezelés után a szénvasztanya erőssége és auszerekési ellenállása javul. A hőkezelési folyamat finomítja a vasztanya poroszerkezetét, amely stabilebbá és tartósabbá teszi azt. A szénvasztanya eszközök, miután temperálási kezelést kaptak, kevesebb mértékben rohanhatnak vagy alakváltozást szenvedhetnek, így biztosítva a hosszabb eszközéletet és az egyformányú hajlítási hatást.
Eszközkezelés és telepítés
Egy nyomó gurító működési hatékonysága az eszköz minőségétől függ, de az eszköz kezelésétől és telepítésétől is. A megfelelő kezelés és telepítés fenntarthatja a legjobb teljesítményt, csökkenti az auszerekést és meghosszabítja az eszköz élettartamát. Itt vannak az eszközkezelés és telepítés finomságai:
A formázó geometria jelentősége
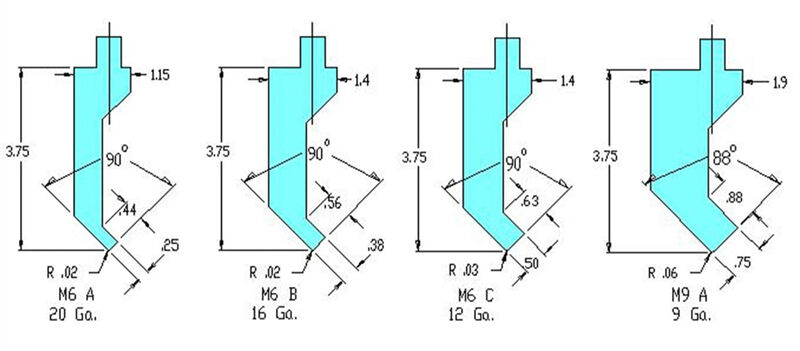
A hajlítási hatás eléréséhez általában bonyolult terveket készítenek a hajlítási mátrixok geometriájára. Minden mátrix alakja, szöge és mérete kulcsfontosságú a hajlítási folyamat pontosságának biztosításához. Ezek az eszközök kezelése és telepítése során,
Győződjön meg arról, hogy a szerszám geometriája konzisztens az elvártnyalábítási művelettel. A hibás geometriájú eszköz használata pontatlan nyomás eredményezni fog, és károsíthatja a géjszerkezetet és a munkafolyamatot.
Szabályosan ellenőrizze a formát a kihasználódásra vagy kárára vonatkozóan. Az idő múlásával a forma geometriai alakja változhat a kihasználódás miatt, ami hatással lesz a nyalábítás minőségére.
A helyes tárolás döntő fontosságú. A szerszámok tárolásakor geometriai alakjuk fenntartása érdekében kerülje a halmozást vagy olyan helyeken való elhelyezést, amelyek deformációhoz vezethetnek.
Szegmentált formák és előnyei
A szegmentált szerszámok olyan eszközök, amelyek sok részre vagy szakaszra osztva vannak. Nemcsak hosszú eszközök, hanem a szegmentált eszközök lehetővé teszik a nyomós áram operátorainak, hogy rövidebb eszközcsempészek kombinációját használják a kívánt hosszúság vagy beállítás eléréséhez. Az előnyök az alábbiak szerint:
Flexibilitás: A szegmensekkel rendelkező eszközök nagyobb versenyképességgel bírnak, a műveleti program konkrét igényeinek megfelelően össze lehet függeszteni a szegmenseket.
Könnyen használható: Rövidebb eszközök használata egyszerűbb, mint a hosszabbaké, könnyebben működhetnek, telepíthetők és javítathatók.
Maur áras csökkentése: Ha egy formából adott komponens kihasználódik vagy megsérül, akkor azt az egyes komponenseket kell cserélni, nem pedig az egész formát.
Költséghatékonyság: A művelettöréses csoportokba történő befektetés hatékonyabb, mint több hosszú eszköz beszerzése különböző műveletekhez, így a hosszú távú költségeket csökkenti.
Optimalizált munkafolyamat: A szegmensekkel rendelkező eszközök gyorsan újra beállíthatók, így a beállítási idő csökkenni, és növeli a termelékenységet.
A tárgyi eszközök pontosságának jelentősége
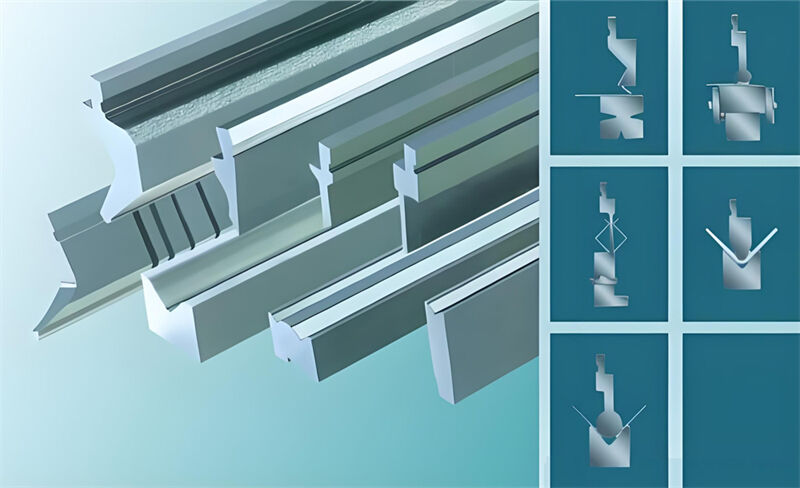
A formapontosságok gyártásban alapvetőek, mivel meghatározzák a termék normális működését, az estétikai tárolók mérvizsgáját vagy más fizikai jellemzőket. A jelentőségük fő oka az alábbi:
Javított összetevő illeszkedése és funkció: Ez a pontosság biztosítja, hogy a részek illeszkedjenek egyéb részekkel, elkerülve az üzemműszaki problémákat és inkompatibilitásokat.
Növeli a végtermék kinézetét: A pontosságok hozzájárulnak a termék estétikájához, például biztosítják, hogy a részek szinten legyenek anélkül, hogy észlelhető szivárgások lennének.
Vegye figyelembe a megfelelő szélességet az eszköz pontosságainál: Az eszköz pontosságait engedélyezheti, miközben fenntartják funkcionáliságukat.
Részcsere lehetősége: A tolleranciák lehetővé teszik egyetlen rész cseréjét, amely megkönnyíti a karbantartást és javítást.
Tollerancia definíciója konzisztencia, pontosság és precizitás érdekében: A tollerancia definíciója lehetővé teszi a termék konzisztenciájának, pontosságának és precizitásának jobb ellenőrzését.
Költségcsökkentés: A tolleranciák előzetes meghatározásával a gyártók csökkenthetik a drága gyártási hibákat és az újrafeldolgozást.
Gyakori kérdések
1. Mi a fő különbség a precizitással alapított és nem precizitással alapított eszközök között?
A precizitással alapított matricák extrémisan szoros tolleranciákon keresztül gyártottak, amelyek biztosítják a magas pontosságot és konzisztenciát a matricák egész készletén keresztül. Ez a szintű pontosság kritikus azokban az alkalmazásokban, amelyek pontos szögeket és ismétlődést igényelnek, mint például a repülőgép- vagy egészségügyi berendezés-gyártás iparágai.
A nem pontos talajos eszközök, bár olcsóbbak, kisebb toleranciával rendelkeznek és általában alkalmasabbak olyan alkalmazásokra, ahol a pontosság nem olyan kritikus. A választás az egyes lehetőségek között a termelési követelményektől függ, a pontos talajos eszközök jobban alkalmasak a magas-pontosságú feladatokra, amelyek konzisztenciát igényelnek.
2. Milyen gyakran kell kalibroálni a nyomósztály eszközeit?
A kalibráció gyakorisága a termelési mennyiségtől, anyagtípus-tól és pontossági követelményektől függ. A magas-pontosságú alkalmazásoknál vagy folyamatos termelési környezetekben heti vagy akár napi kalibráció szükséges, hogy megfelelően biztosítsuk a konzisztens hajtást és minimalizáljuk a potenciális eltéréseket.
Kevesebb terhelésű műveletek esetén havonta vagy negyedévente elég lehet a kalibráció. Egy rendszeres kalibrációs program bevezetése, amely a termelési igényekkel egybevág, segíthet a pontosság fenntartásában és csökkentheti a visszaélési vagy hulladékanyag mennyiségét.
3. Milyen tényezők hatnak a nyomósztály eszközök élettartamára?
Sok tényező hat az eszköz élettartamára, beleértve a anyag minőségét, az alkalmazás intensitását, a munkaterület anyag merevségét és a karbantartási módszereket. Azok a nyomósztály eszközök, amelyek magas minőségű eszközacélot használnak vagy különleges fedésekkel vannak ellátva, általában hosszabb ideig tartanak, különösen a nagy mennyiségű termelési környezetekben.
Rendszeres tisztítás,光滑润滑 és ellenőrzés megakadályozza a korai kihasználódást, ami jelentősen hosszabbíthatja az eszköz élettartamát. Emellett a túlzott tonnák elkerülése és a javasolt működési irányelvek követése védelmet biztosít az eszköz számára a túlzott terhelés ellen, ami növeli a szerviz élettartamát.
4. Használhatók-e nyomósztály eszközök mindenféle fémre?
Bár a nyomósztály eszközök széles körben használatosak, különböző fémtípusokhoz szükség van egyedi eszközjellemzőkre a legjobb teljesítmény érdekében. Például, a keményebbek fémtípusok, mint például a rostmentes acél vagy a titanium több erőt bonyolnak ki a mátrixon, ezért a magas erősségű vagy karbidfedett mátrixok alkalmasak ezekhez az alkalmazásokhoz.
A lágyabb fémek, mint például az alumínium, kevesebb mátrixerőt igényelnek, de lágyabb mátrixokat vagy nyomókat használhatunk a felületi károsodás elkerülése érdekében. A mátrix és a anyag típusa közötti illesztés optimalizálja a mátrix élettartamát és a hajlítási minőséget, amely növeli a nyomósík művelet teljes efficienciáját.
5. Hogyan választok ki a projektemhez megfelelő nyomósík eszközöket?
Először is, figyelembe kell venni az anyag jellemzőit, beleértve az anyag típusát, húzóerőét és rezsgénységét, hiszen ezek meghatározhatják a konkrét eszközszerelmi igényeket. Különböző anyagok, mint az alumínium, a szén-dús acél és a rostmentes acél, egyedi tulajdonságokkal rendelkeznek, amelyek különböző beállításokat igényelnek.
Ezután értékeljük ki az anyag vastagságát és hosszát. A mátrix nyitása általában 8-szorosa kell legyen az anyag vastagságának. Az anyag hossza meghatározza a szükséges mátrix hosszát. A hajlítási szög és alakzat fontosak. Konkrét hajlítási alakzatok, mint a V-hajlítás vagy a szélcsavarás, megfelelő eszközöket igényelnek. A szükséges hajlítási alakzat ismerete segíthet abban, hogy kiválasszuk a megfelelő mátrixot.
A szerszám profilja és terhelési határértéke szintén döntő. Igazítsd a szerszám profilját a munka típusához, független attól, hogy légibegyenes, aljibegyenes vagy érmibegyenes, és győződj meg arról, hogy a terhelési korlát ne haladja meg a nyomósztály képességeit károsodás elkerülése érdekében.
A matricza kiválasztása konzisztens kell legyen a részvegyszer vastagságával. Használd az „8×2 szabályt”, és szorozd meg a legalacsonyabb vastagságú metál 8-cal annak meghatározására, hogy mi a legkisebb V alakú matrica, amelyre szükség van. A beállítható matriczak hasznosak a több begyeneses projektekhez.
Amikor punchot választasz, add alapul a munka követelményeinek. Vegyük figyelembe a punch típusát, például a standard, lúdhasú, vagy éles-szögű típusok közül, és biztosítsd azt, hogy a punch orr sugara illeszkedjen a pneumatikus formázási sugarértékhez.
A pontosság és kompatibilitás fontos a részegyenesenység eléréséhez. Válasszon magas pontosságú eszközöket, és olyan funkciókat, mint a szakaszos és önmagukban tartó rögzítés kényelmét és biztonságát. Vizsgálja meg az eszköz-opciókat és testreszabást. Bár az általános eszközök alkalmasak a gyakori hajtásokhoz, egyedi specifikációkhoz testreszabott eszközök is szükségesek a formálási hatékonyság javításához.
Végezetül figyeljen a beállításra és működésre. Azok az eszközök, amelyek előtt engednek betöltést, csökkenthetik a beállítási időt. Azok a projektekhez, amelyek gyakori eszközcserét igényelnek, mindegyik nyomóhéj felszereltsége dedikált eszköztárcaval növelheti a hatékonyságot.