Általános elemzés a nyomósáv élettartamáról és cserévi cyklusról
Tartalom:
Alapvető tényezők a nyomósztömparancs élettartamára
1. Tervezés és gyártási minőség
2. Használati gyakoriság
3. Rendszeres Karbantartás Kezelése
4. Működési Környezet alkalmazkodhatósága
Jellegzetes Jelük a Cserére
1. Növekvő karbantartási költségek
2. Technológiai elavulás
3. Folyamatos teljesítmény-hullámzás
Gyakori kérdések
K1: Mi a nyomószerkezet átlagos élettartama?
K2: Hogy terjeszthető ki az élettartam?
K3: Mikor kell egy nyomószerkezetet cserélni?
Záró és ajánlások
Mint mag alapozó berendezés a lapáttermelésben, a nyomószerkezetek élettartama és cseréje közvetlenül befolyásolja a termelési költségeket és hatékonyságot. A cikk rendszeresen elemzi azokat a tényezőket, amelyek befolyásolják az eszköz élettartamát, a cserélés idejét és a optimalizálási stratégiákat, segítve vállalatokat abban, hogy tudományos lifecycle kezelést valósítsanak meg.
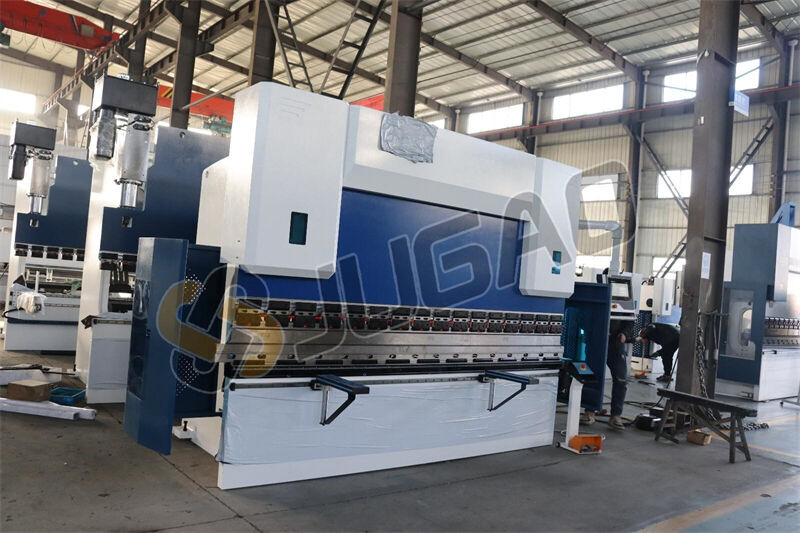
Alapvető tényezők a nyomósztömparancs élettartamára
1. Tervezés és gyártási minőség
A felszerelés hosszú élettartamának alapja a tervezési és gyártási folyamatokban van:
Anyagok és műveszet: Magas pontosságú öntött képkockák és keményített irányítóvonalak jelentősen növelik a rohamellenállást.
Technikai konfiguráció: Haladó technológiák, mint például a szervomotoros hajtások és zárókörös ellenőrző rendszerek csökkentik a hosszú távú摩sélyt.
Választás márkánként: Az ISO-biztosítékos gyártókat adjuk előnyben, hogy megbízhatóságot biztosítson.
Tanulmány: Egy teljesen összesített acélképkockás nyomásalapozó 12 éves folytonos használat után 90%-os pontosságot tartott fenn, míg egy alacsonyabb minőségű modellnek nagy javításokra volt szüksége az 8. évig azonos feltételek között.
2. Használati gyakoriság
A használati intensitás és a szervizétel nemlineáris kapcsolatban áll egymással:
Kevésbé Terhelt Forgatókönyvek (<4 óra/nap): A szervizétel elméletileg 20 évet meghaladja.
Teljes Terhelésű Működés (24/7 működés): A központi komponenseket minden 10-15 éven belül meg kell vizsgálni.
Fontos Lábasállomások: Törekedjen a hidraulikai zárókrán, a ramutalakozóknál és az elektronikai kapcsolatoknál.
Adatforrás: Egy autószerelői gyár jelentette, hogy az egyéves 500.000 ciklusnál több feldolgozási felszerelés háromszor nagyobb hidraulikai rendszer-sérülési arányt mutatott standard feltételekhez képest.
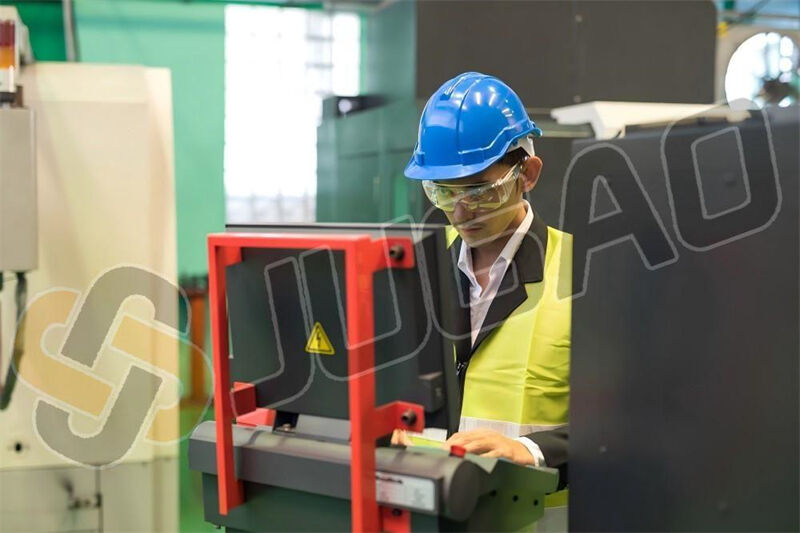
3. Rendszeres Karbantartás Kezelése
A tudományos karbantartás 30%-50%-kal meghosszabbítja az élettartamot:
Naponta: Tisztítsa le a vezérlő csatornát a szemétből; hétente ellenőrizze a hidraulikus olaj szintjét.
Negyedévente: Kalibálja a háttér-gegyű pontosságát; vizsgálja meg a rács skála stabilitását.
Évente: Cserélje ki a hidraulikus olaj szűrőit; tesztelje a szinkronizációs rendszer nyomaték eltéréseit.
Karbantartási csalás: Az egyetlenül hibás utáni javításokra támaszkodó vállalatok <60%-os eszközhatékonyságot érnek el, míg a megelőző karbantartási programok >85%-ot szolgáltatnak.
4. Működési Környezet alkalmazkodhatósága
A környezeti hatások gyakran alul vannak becslve:
Hőmérséklet/Páratartalom-vezérlés: Ideális feltételek: 10-35°C, páratartalom<70%.
Porvédelem: Telepítse a pozitív nyomású levegő-függönyeket az elektromos szekrények kontaminációjának csökkentésére.
Alap Stabilitás: Használja a rezgés-dämpferes platformokat a nagy rezgésű környezetekben a tartomány deformációjának elkerülése érdekében.
Szélsőséges eset: A part menti telephely nélkülíthetett anti-sófüst kezelésben súlyos áramkör-elerosódást tapasztalt 3 év alatt.
Jellegzetes Jelük a Cserére
1. Növekvő karbantartási költségek
Indítson el költség-nyereség elemzést, ha az éves javítási költségek meghaladják a maradékérték 30%-át vagy egyetlen főbb javítás költsége túlmutatja az új berendezés árának 15%-át.
Döntési Modell:
Csere Határérték = (Éves Karbantartási Költség + Állományveszteségek) / Új Berendezés Éves Értékcsökkenési Költsége > 1.2
2. Technológiai elavulás
Az örökbefogadott berendezések három kihívást jelentenek:
Pontossági Különbség: A tradicionális mechanikus megállítási modell: ±0.1mm ismétlődés vs. CNC modell: ±0.02mm.
Alacsony energiahatékonyság: Az új servo nyomókacsák az energiafogyasztást 40%-sal és 60%-kal csökkentik.
Funkcióhiányok: A smart funkciók (pl. 3D szimuláció, automatikus eszközcsere) nem érhetők el átalakítással.
Frissítési ajánlás: Prioritás a CNC átalakítása az 10 évnél idősebb hidraulikus modelleknek.
3. Folyamatos teljesítmény-hullámzás
Tartalmazd ezeket a mértékeket az eszközök egészségét értékelő elemzésekben:
Kanyarodási szög eltérés: Három folyamatos hónapban a toleranciát kétszer meghaladja.
Hidraulikus válasz késleltetés: >0,5 másodperc a parancs és a rammozgással való várakozás között.
Szinkronizálási hiba: Y1/Y2 tengely eltérés >0,05mm.
Diagnosztikai eszközök: Használja a rezgés-analizátort és a hőmérsékleti kép-kamerát a további vizsgálatokhoz.
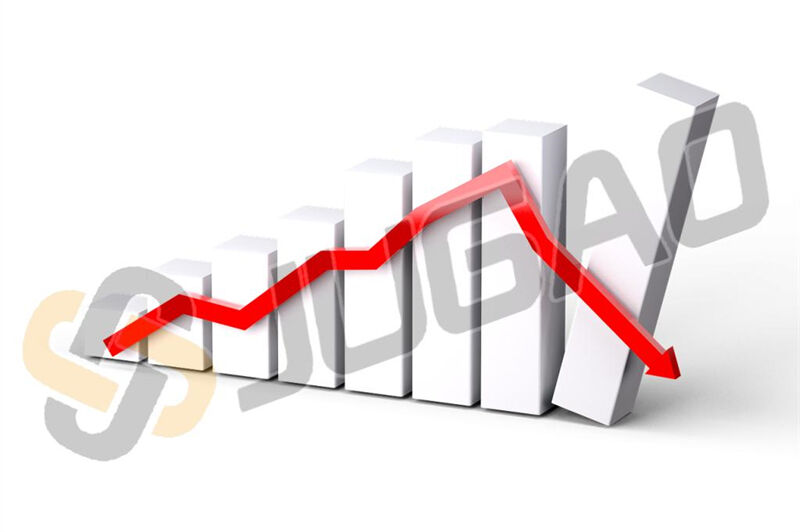
Gyakori kérdések
K1: Mi a nyomószerkezet átlagos élettartama?
Állami használat és karbantartás alatt:
Gazdaságos modellek: 8-12 év
Középső árkategória CNC modellek: 12-18 év
Magas árkategória Servo modellek: 15-25 év
K2: Hogy terjeszthető ki az élettartam?
Háromszintes karbantartási stratégia implementálása:
1. Operátor szint: Előzetes öntóanyag ellenőrzés; utólagos munkaterület takarítás.
2. Műszaki szint: Havi hidraulikai nyomás görbének és elektrikus izoláció tesztelése.
3. Expert Szint: Éves keretstressz elemzés és CNC firmware frissítések.
K3: Mikor kell egy nyomószerkezetet cserélni?
Indítsa el a helyettesítési értékelést, ha:
Kritikus komponensek (pl., fő hengerek) megszűnnek, és nincsenek alternatívák.
A feldolgozási hatékonyság 30%-kal alacsonyabb az ipari szabványoknál.
A biztonsági rendszerek nem felelnek meg a legfrissebb CE/OSHA szabványoknak.
Záró és ajánlások
A nyomószerelés élettartam-kezelése kvantitatív értékelési rendszer igénye:
1. Felszerelési Adatok Karbantartása: Jelentse meg a karbantartási előzményeket, a hibakódot és az átalakításokat.
2. IoT Figyelés Bevezetése: Valós idejű nyomás-, hőmérséklet- és rezgés-mérések.
3. Ötévős Gördülő Tervek kidolgozása: Hangzastrázák igazítása a kapacitás-tervhez és a technológiai trendekhez.
Műveleti Útmutató: Éves harmadik fél által végzett ellenőrzések az adatok alapján történő Felszerelési Egészségjelentések készítéséhez.