Factores que afectan á tonelada das máquinas de dobre
Métodos de dobre
Dobremétodos | Influencia na tonelada das máquinas de dobre |
Dobrado ao aire | Requiere máis toneladas que o doblado neumático porque a molla superior toca fondo no molde. O material entra en contacto coa púa da molla superior e coa parede lateral do molde inferior. A tonelaxe é maior, pero non tanto como no imprimado. |
Dobrado por abaixo | Requiere máis toneladas que o doblado ao aire porque a molla superior toca fondo no molde. O material entra en contacto coa púa da molla superior e coa parede lateral do molde. A tonelaxe é maior, pero non tanto como no imprimado. |
Imprimado | Requírese a maior tonelaxe. O puncho e a matriz están en contacto total co material, comprimindo e afinando o material. Empregan forzas moi grandes para facer que o material se axeite á angle da matriz da máquina de dobre. |
Os diferentes métodos de dobre de metal requiren unha tonelaxe diferente. Por exemplo, no dobre no aire, a tonelaxe pode aumentarse ou diminuírse cambiando a abertura da matriz.
O raio de dobre afecta a anchura da abertura da matriz. Neste caso, debe engadírselle o factor de método á fórmula. Cando se usa o dobre inferior e a estampación, a tonelaxe requerida é maior ca no dobre no aire.
Se calculas a tonelaxe para o dobre inferior, tes que multiplicar a tonelaxe por polegada de dobre no aire polo menos por cinco. Se usas estampación, a tonelaxe requerida pode ser incluso maior ca para o dobre inferior.
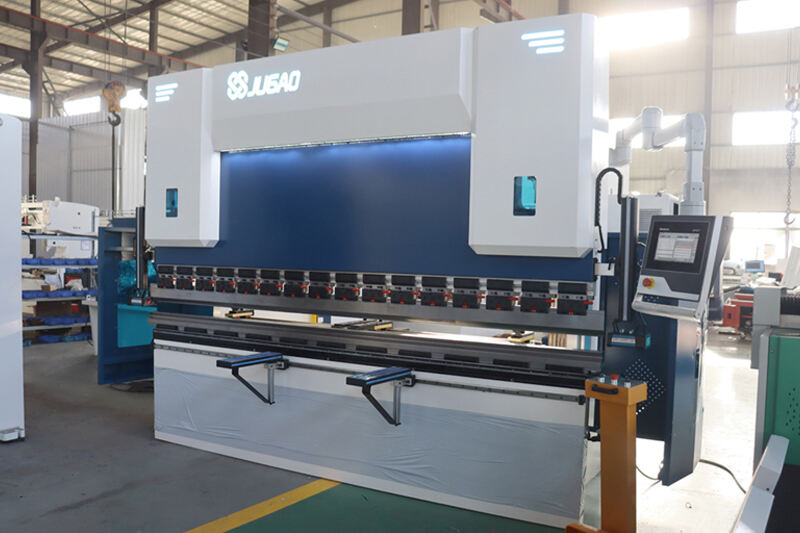
Anchura da matriz
Xa aprendemos que no dobre no ar, a tonelada necesaria diminúe à medida que o tamaño da abertura do contramodelo aumenta e aumenta cando o tamaño da abertura diminúe.
Isto é porque a anchura da abertura do contramodelo determina o radio de dobre interior, e un menor radio de contramodelo require máis toneladas.
No dobre no ar, a relación do contramodelo normalmente é de 8:1, significando que a distancia da abertura do contramodelo é oito veces a espesura do material. Neste caso, a espesura do material é igual ao radio de dobre interior.
Fricción e Velocidade
No dobre no ar, o puncho debe pasar polo orificio inferior do contramodelo para dobrar a chapa metálica. Se a superficie da chapa metálica non está lubrificada, a fricción entre o contramodelo e a chapa metálica aumenta, requirendo máis toneladas para dobral a chapa metálica e reducindo o efecto de resprallido do material.
Pelo contrario, se a superficie da chapa metálica é lixa e lubricada, a fricción entre o molde e a chapa metálica diminúe, reducindo a tonelada necesaria para dobral a chapa metálica. Pero isto aumentará o efecto de resprallido da chapa metálica.
A velocidade de dobre tamén afecta á tonelada necesaria. Conforme a velocidade de dobre aumenta, a tonelada necesaria diminúe. Aumentar a velocidade tamén reduce a fricción entre o molde e a chapa, pero isto tamén incrementa o resprallido da chapa.
Propiedades do Material
Tonelada refírese á forza que a prensa de dobre aplica á chapa metálica. Polo tanto, o intervalo de forzas de dobre depende da espesor e da resistencia ao tracción da chapa metálica que se dobra.
Tipo de material
Un factor é o tipo de material que se dobra. Os materiais con maiores resistencias ao tracción, como o acero inoxidable ou as aleacións de alta resistencia, requiren máis forza para dobralos que os metais mellores, como o aluminio ou o cobre. Por exemplo
Acero inoxidable (grado 316): resistencia ao tracción ~620 MPa; resistencia a yield ~290 MPa.
Cobre: resistencia a tracción ~210 MPa; resistencia a ruptura ~69 MPa.
Os materiais máis suaves, como o aluminio, mostran menos resistencia, o que reduce os requisitos de tonelaxe pero aumenta o potencial de resprallido.
Resistencia a tracción e resistencia a ruptura
Diferentes materiais teñen diferentes resistencias a tracción, o que afecta directamente á forza necesaria para doblar. Por exemplo, o acero inoxidable require normalmente máis tonelaxe que o acero dúxil ou o aluminio.
A resistencia a tracción é o estrés máximo que un material pode soportar baixo unha carga constante. Se este estrés se aplica e mantiñe, o material acabará rompendose. A resistencia a ruptura, polo contrario, é o estrés a partir do cal un material comeza a deformarse plásticamente.
Resistencias típicas de tracción de algúns materiais
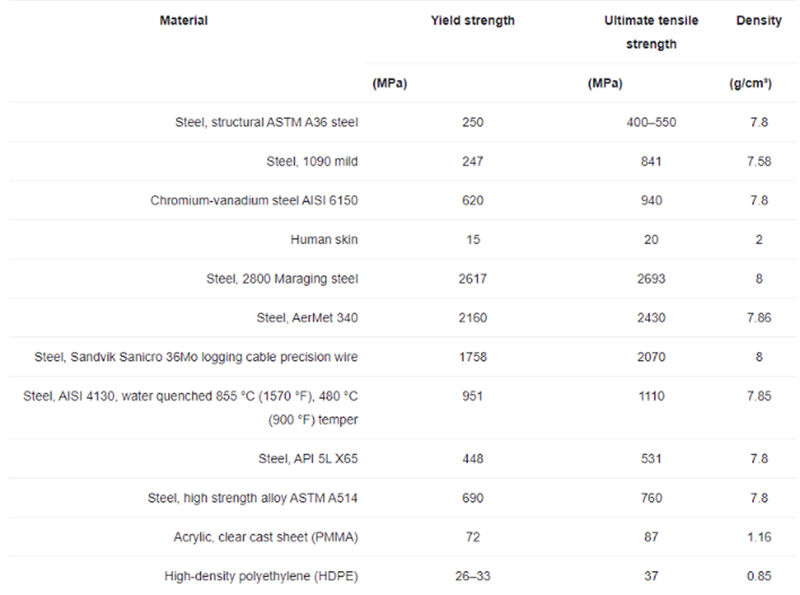
Espesor do material
Outro factor importante é a espesura do metal en chapa. Quanto máis grosa teña o material, máis toneladas se requiren, e viceversa. Os materiais máis groso requiren múltiples veces máis toneladas debido á súa maior resistencia á deformación.
Por exemplo, duplicar a espesura da chapa duplicará tamén a forza necesaria. En termos xerais, máis grosa ten o material, máis toneladas ou forza se requiren para formalo.
Materiais | Espesor (mm) | Radio de curvatura (mm) | Multiplicador de toneladas | Toneladas requeridas (tons/metro) |
Aco suave | 1 | 1 | 1 | 10 |
Aco suave | 2 | 2 | 1 | 40 |
Aco suave | 3 | 3 | 1 | 90 |
Aluminio (5052-H32) | 1 | 1 | 0.45 | 4.5 |
Aluminio (5052-H32) | 2 | 2 | 0.45 | 18 |
Aluminio (5052-H32) | 3 | 3 | 0.45 | 40.5 |
Aco inoxidable (304) | 1 | 1 | 1.45 | 14.5 |
Aco inoxidable (304) | 2 | 2 | 1.45 | 58 |
Aco inoxidable (304) | 3 | 3 | 1.45 | 130.5 |
Aco suave | 2 | 1 | 1 | 60 |
Aco suave | 2 | 3 | 1 | 30 |
Aco inoxidable (304) | 2 | 1 | 1.45 | 87 |
Aco inoxidable (304) | 2 | 3 | 1.45 | 43.5 |
A táboa mostra que
1. À medida que a espesor do material aumenta, a tonelada necesaria para todos os materiais aumenta significativamente. Dobrar a espesor de 1 mm a 2 mm multiplica por catro a tonelada.
2. O aluminio require aproximadamente un 45% máis de tonelaxe que o acero suave da mesma espesor, e o acero inox require aproximadamente un 45% máis de tonelaxe que o acero suave.
3. Reducir o radio de dobre interno mentres se manteña a espesor constante aumenta a tonelaxe necesaria. Medrar o radio de 2 mm a 1 mm aumenta a tonelaxe en un 50%.
4. O multiplicador de tonelaxe varía segundo o tipo de material e a súa resistencia a tracción. Nestes xemplo, é 1.0 para o acero suave, 0.45 para o aluminio 5052-H32, e 1.45 para o acero inox 304.
Rebotexado
Despois de dobrar, os materiais tenderon a rebotar levemente cara á súa forma orixinal. Os materiais de alta resistencia terán máis rebotexado, polo que será necesario axustar a tonelaxe e as ferramentas para conseguir ángulos precisos.
Lonxitude e Ángulo de Flexión
Lonxitude da Curvatura
A lonxitude de flexión da mesa da prensa de frebrar é a lonxitude máxima que unha chapa de metal pode ser doblada. A lonxitude de flexión da prensa de frebrar debe ser ligeiramente maior que o material a doblar.
Se a lonxitude da mesa non é correcta, pode producirse dano no foso ou en outros componentes. Un calculador de carga de flexión pode axudar a determinar a tonelaxe requirente baseándose na espesor do material e en outros factores como a lonxitude de flexión e a lonxitude da abertura V.
Ángulo de Flexión
Canto maior sexa o ángulo, maior será a tonelaxe requirente debido á maior compresión do material no punto de flexión. Por contra, os ángulos máis grandes requiren menos forza pero poden resultar en dobras menos precisas.
Factores de ferramenta
Os puncheiros da prensa de frebrar son tamén un factor a ter en conta. Estes puncheiros tamén teñen limitacións na carga de frebrado. Os puncheiros en V de ángulo recto poden manexar cargas de maior tonelaxe.
Xa que os morros de ángulo afilado teñen un ángulo máis pequeno e están feitos con menos material, como os morros de pescozo de ganso, non están tan predispertos a manexar cargas pesadas.
Ao usar diferentes morros, non debe superarse a súa forza máxima de frebrado. Ademais, o raio do morro e o raio de frebrado tamén afectan aos requisitos de tonelaxe.
Un raio de morro maior pode provocar un aumento na forza de frebrado requirente. De forma similar, canto maior sexa o raio de frebrado, maior será a tonelaxe requirente.
A relación entre a anchura da abertura do morro e a espesura do material é outro factor a considerar. Para materiais máis finos, recoméndase unha razón de morro máis baixa (como 6 a 1).
Materiais máis grosos poden requirer unha razón de morro máis alta (como 10 a 1 ou 12 a 1) para reducir a forza de flexión e manter a aplicación dentro das capacidades da máquina de dobre.
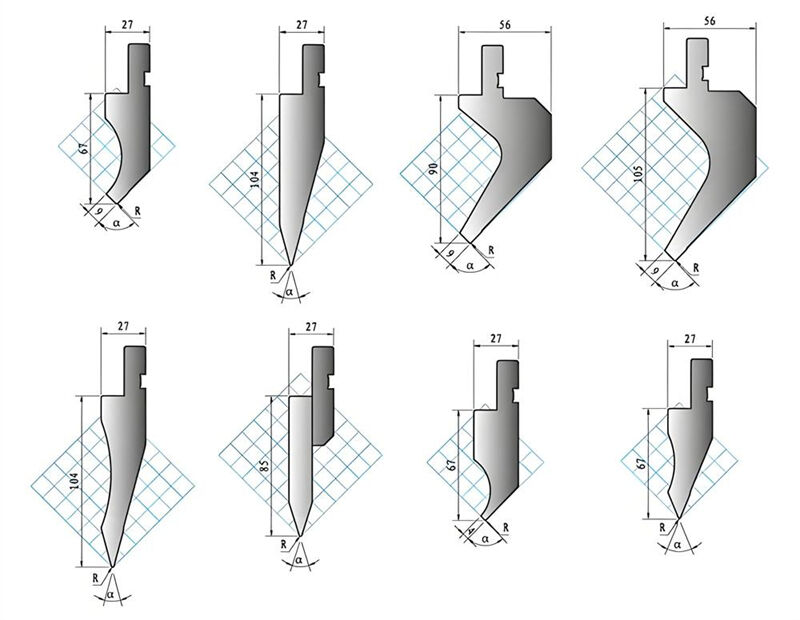
Desgaste a longo prazo das ferramentas
Desgaste gradual:
Co tempo, as operacións repetidas de alta presión fan que as ferramentas perdan súa nitidez e integridade estrutural. Se non se soluciona, este desgaste pode levar a dobras inconsistentes e a unha peor calidade das pezas.
Impacto na vida útil da ferramenta:
Sobrecargar unha ferramenta alóndese da súa capacidade (por exemplo, fresar chapa espesa cunha mullera estreita) pode causar microfíssuras ou un fallo catastrófico durante a súa operación. As inspeccións regulares son esenciais para evitar paradas inesperadas ou riscos de seguridade.
Requisitos de manutenção:
As ferramentas que se sobrecargan requiren manutención máis frecuente ou substitución, aumentando os custos operativos. Os sistemas de monitorización ou software de manutenición predictiva poden axudar a identificar patróns de desgaste antes e optimizar o uso das ferramentas.
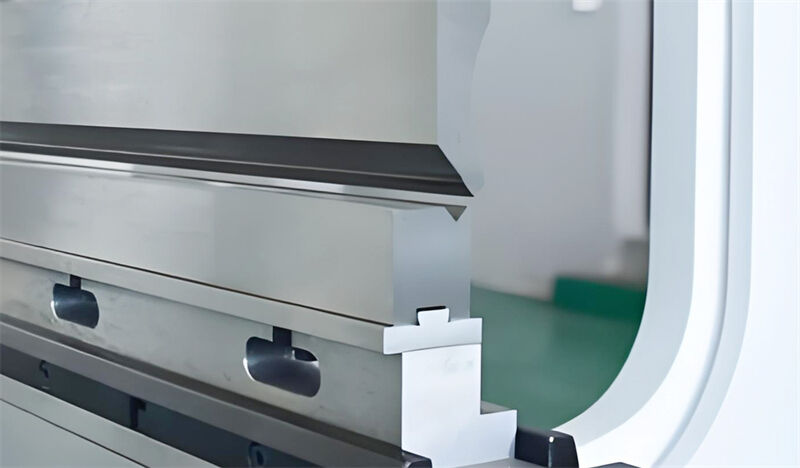