Análise Completa do Ciclo de Vida e Sustitución dun Frente de Prensas
Contidos
Factores Principais que Afectan á Vida Útil dun Frente de Prensa
1. Diseño e Calidade da Fabricación
2. Frecuencia de Uso
3. Xestión de Manutencción Regular
4. Adaptabilidade do Entorno Operativo
Señales Clave para a Sustitución
1. Aumento dos Custos de Manutenición
2. Obsolescencia Tecnolóxica
3. Declive Continuo do Rendemento
Preguntas frecuentes
P1: Cal é a vida útil media dun frebrador?
P2: Como se pode alargar a vida útil?
P3: Cando debe substituírse un frebrador?
Conclusión e Recomendacións
Como equipo básico na fabricación de chapa, a vida útil e a estratexia de substitución dos freños de prensa afectan directamente aos custos de produción e á eficiencia. Este artigo analiza sistemáticamente os factores que influen na vida útil do equipo, o momento da substitución e as estratexias de optimización, empoderando as empresas para implementar unha xestión científica do clico de vida.
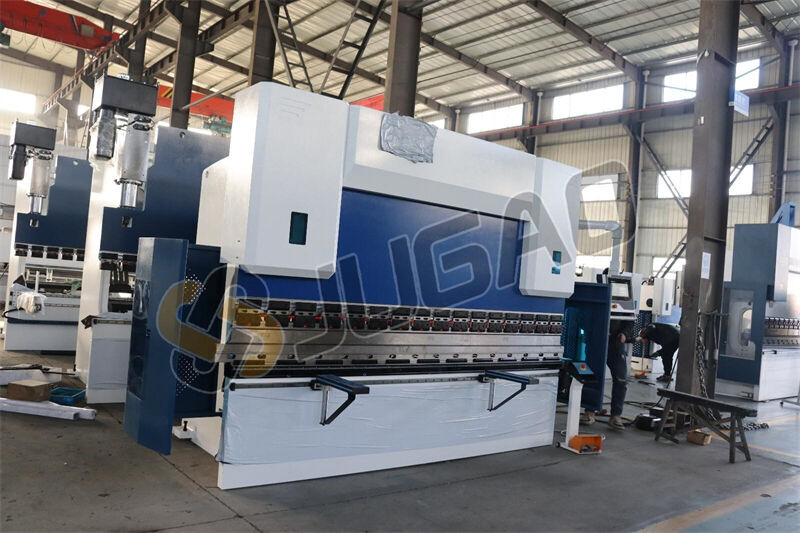
Factores Principais que Afectan á Vida Útil dun Frente de Prensa
1. Diseño e Calidade da Fabricación
A base da lonxevidade do equipo está na deseño e nos procesos de fabricación:
Materiais e Maestría: Moldes de fundición de alta precisión e raíles guía endurecidos incrementan significativamente a resistencia á fatiga.
Configuración Técnica: Tecnoloxías avanzadas como motores de servomecanismo e sistemas de control en bucle pechado reducen o desgaste a longo prazo.
Selección de Marca: Prioriza fabricantes certificados ISO para asegurar fiabilidade.
Estudo de caso: Un frebrador de marco de aco completamente soldado manteve un 90% de precisión despois de 12 anos de uso continuo, mentres que un modelo de baixa calidade requireu reparacións importantes ao cabo do 8º ano baixas as mesmas condicións.
2. Frecuencia de Uso
A intensidade de uso e o tempo de vida útil exhiben unha relación non lineal:
Escenarios de Poca Carga (<4 horas/día): O tempo de vida útil teórico supera os 20 anos.
Producción Intensa (operación 24/7): Os compoñentes principais deben ser avaliados cada 10-15 anos.
Puntos Críticos de Desgaste: Centrarse nas seladas hidráulicas, nas guías do ber e nos contactos eléctricos.
Referencia de datos: Unha fábrica de pezas automóbiles informou que o equipo que procesa máis de 500.000 ciclos anualmente experimentou unha taxa de fallo do sistema hidráulico tres veces maior en comparación coas condicións estándar.
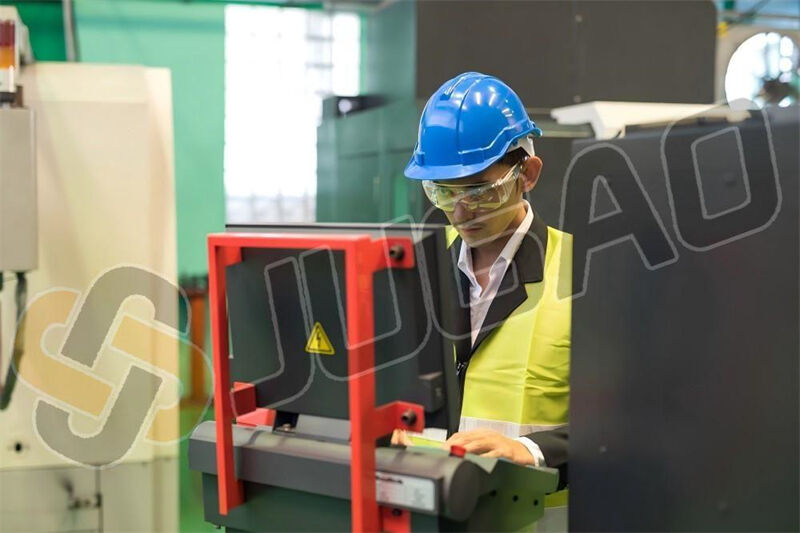
3. Xestión de Manutencción Regular
A manutencción científica aumenta a vida útil entre un 30% e un 50%:
Manutenición diaria: Limpar os resíduos da guía; comprobar os niveis de óleo hidráulico semanalmente.
Revisión trimestral: Calibrar a precisión da ré traseira; inspeccionar a estabilidade da escala de gratinado.
Revisión anual: Cambiar os filtros de óleo hidráulico; probar a desviación de par do sistema de sincronización.
Fosa de manutenção: As empresas que só se basean en reparacións posteriores a fallos alcanzan un <60% de efectividade global do equipo, mentres que os programas de manutenção preventiva xorden >85%.
4. Adaptabilidade do Entorno Operativo
Os impactos ambientais soven ser subestimados:
Control de Temperatura/Humedade: Condicions ideais: 10-35°C, humedade<70%.
Prevención do Polvo: Instale cortinas de aire a presión positiva para reducir a contaminación dos armarios eléctricos.
Estabilidade da Fundación: Use plataformas antivibracións en ambientes con alto nivel de vibración para evitar a deformación da estrutura.
Caso Extremo: Unha instalación costeira sen tratamento anti-salitre experimentou unha corrosión severa das placas base dentro de 3 anos.
Señales Clave para a Sustitución
1. Aumento dos Custos de Manutenición
Inicia un análise de custo-beneficio se os custos anuais de reparación superan o 30% do valor residual ou se os custos dunha reparación maior superan o 15% do prezo do equipo novo.
Modelo de Decisión:
Límite de Substitución = (Custo Anual de Manutenção + Pérdidas por Parada) \/ Custo Anual de Depreciación do Equipamento Novo > 1,2
2. Obsolescencia Tecnolóxica
O equipamento legado enfrente tres desafíos:
Diferenza de Precisión: Modelos tradicionais mecánicos: repetibilidade ±0.1mm frente a modelos CNC: ±0.02mm.
Baixa Eficiencia Enerxética: As novas prensas de servo reducen o consumo de enerxía en un 40%-60%.
Deficiencias Funcionais: As características intelixentes (p.ex., simulación 3D, cambio automático de ferramenta) non son alcanzables mediante retrofitting.
Recomendación de Actualización: Priorizar o retrofitting CNC para modelos hidráulicos con máis de 10 anos.
3. Declive Continuo do Rendemento
Incluín estas métricas nas avaliacións da saúde do equipo:
Desviación do Ángulo de Flexión: Supera a tolerancia en 2x durante tres meses consecutivos.
Retardo na Resposta Hidráulica: >0,5 segundos desde a orde ata o movemento da pera.
Erro de Sincronización: Desviación do eixe Y1/Y2 >0,05mm.
Ferramentas de Diagnóstico: Empregue analizadores de vibración e cámaras de imaxe térmica para inspeccións a fondo.
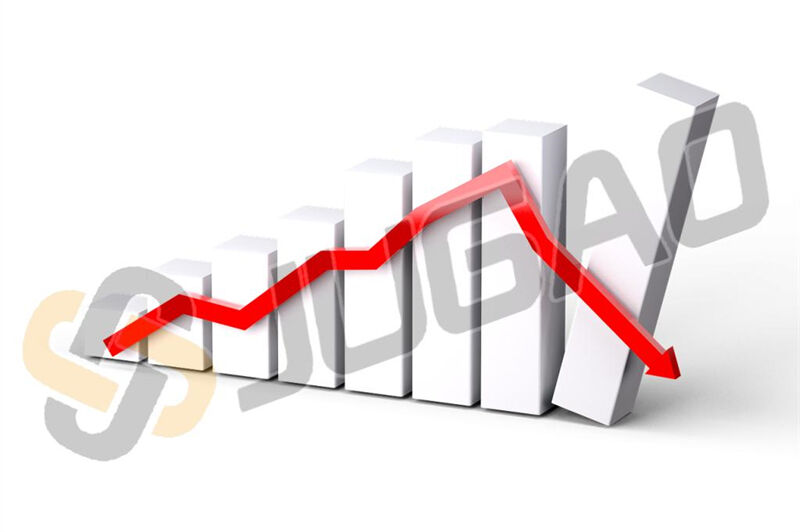
Preguntas frecuentes
P1: Cal é a vida útil media dun frebrador?
Baixo uso e mantemento estandarizado:
Modelos económicos: 8-12 anos
Modelos CNC de gama media: 12-18 anos
Modelos de alta gama con servo: 15-25 anos
P2: Como se pode alargar a vida útil?
Implementar unha estratexia de manutenção en tres niveis:
1. Nivel de operador: Comprobacións de lubrificación antes do turno; limpeza do espazo de traballo despois do turno.
2. Nivel Técnico: Curva de presión hidráulica mensual e probas de isolamento eléctrico.
3. Nivel Experto: Análise anual do estrés do marco e actualizacións de firmware CNC.
P3: Cando debe substituírse un frebrador?
Inicia a avaliación de substitución se:
Componentes críticos (p.ex., cilindros principais) deixan de fabricarse sen alternativas.
A eficiencia de procesamento cae 30% abaixo dos estándares da industria.
Os sistemas de seguridade non cumpren os estándares máis recentes de CE/OSHA.
Conclusión e Recomendacións
A xestión do ciclo de vida do frebrador require un sistema de avaliación cuantificado:
1. Manter Rexistros de Equipamento: Registar o historial de manutenção, códigos de fallo e retrofit.
2. Adoptar Monitorización IoT: Seguimento en tempo real da presión, temperatura e vibración.
3. Desenvolver Planes Rodantes de 5 Anos: Alinear os calendarios de substitución coa planificación da capacidade e as tendencias tecnolóxicas.
Guía de Acción: Inspeccións anuais por terceiros para xerar Informes de Saúde do Equipamento para decisiones baseadas en datos.