Análisis Integral de la Duración y el Ciclo de Reemplazo de una Prensa Freno
Cuadro de contenido
Factores Principales que Afectan la Duración del Freno de Prensa
1. Diseño y Calidad de Fabricación
2. Frecuencia de Uso
3. Gestión de Mantenimiento Regular
4. Adaptabilidad del Entorno Operativo
Señales Clave para la Reemplazo
1. Aumento de los Costos de Mantenimiento
2. Obsolescencia Tecnológica
3. Declive Continuo del Rendimiento
Preguntas Frecuentes
P1: ¿Cuál es el promedio de vida útil de un freno de prensado?
P2: ¿Cómo extender la vida útil?
P3: ¿Cuándo debe reemplazarse un freno de prensado?
Conclusiones y recomendaciones
Como equipo central en la fabricación de chapas, la vida útil y la estrategia de reemplazo de los frenos de prensado impactan directamente los costos de producción y la eficiencia. Este artículo analiza sistemáticamente los factores que influyen en la vida útil del equipo, el momento de reemplazo y las estrategias de optimización, empoderando a las empresas para implementar una gestión del ciclo de vida científica.
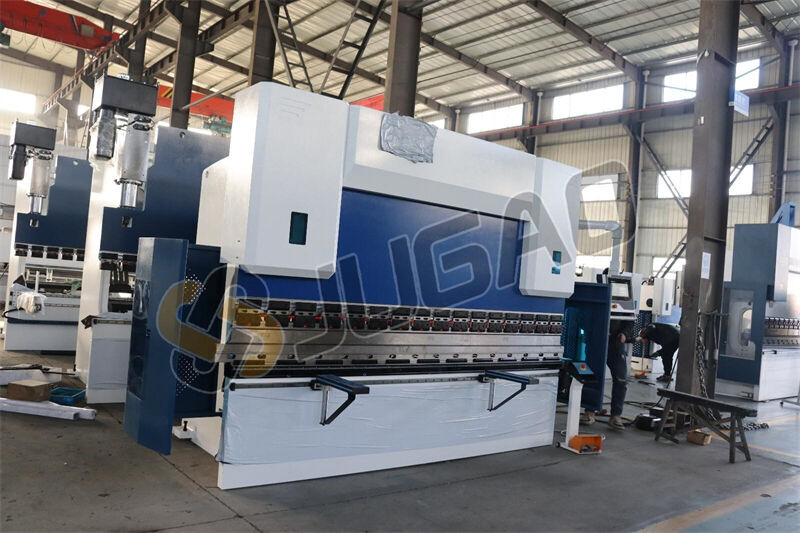
Factores Principales que Afectan la Duración del Freno de Prensa
1. Diseño y Calidad de Fabricación
La base de la longevidad del equipo radica en los procesos de diseño y fabricación:
Materiales y artesanía: Marcos de fundición de alta precisión y rieles guía endurecidos mejoran significativamente la resistencia a la fatiga.
Configuración técnica: Tecnologías avanzadas como motores de servodirección y sistemas de control de bucle cerrado reducen el desgaste a largo plazo.
Selección de marca: Priorice fabricantes certificados por ISO para garantizar fiabilidad.
Estudio de caso: Un freno de plegado con marco de acero completamente soldado mantuvo un 90% de precisión después de 12 años de uso continuo, mientras que un modelo de gama baja necesitó reparaciones mayores al octavo año bajo las mismas condiciones.
2. Frecuencia de Uso
La intensidad de uso y la vida útil exhiben una relación no lineal:
Escenarios de Uso Ligero (<4 horas/día): La vida útil teórica supera los 20 años.
Producción Intensa (operación 24/7): Los componentes principales deben ser evaluados cada 10-15 años.
Puntos Críticos de Desgaste: Enfóquese en las juntas hidráulicas, guías de pistón y contactos eléctricos.
Referencia de Datos: Una fábrica de piezas automotrices reportó que el equipo que procesa más de 500,000 ciclos anuales experimentó un triple en la tasa de fallas del sistema hidráulico en comparación con condiciones estándar.
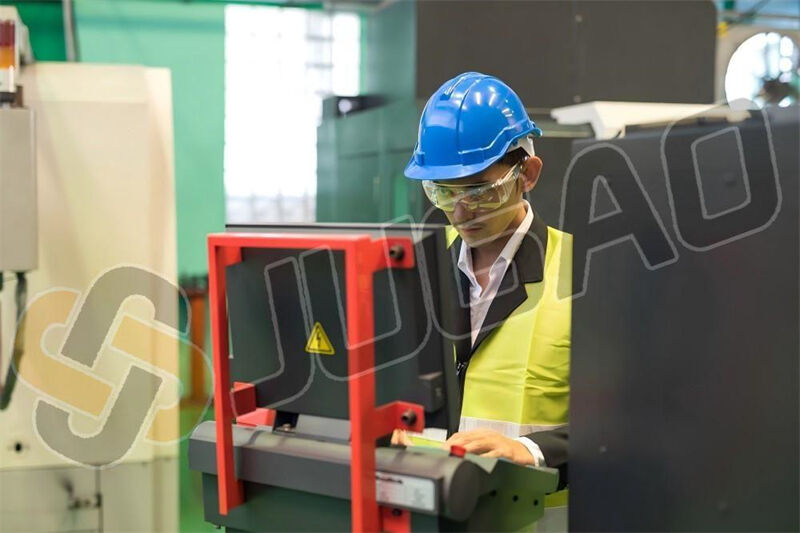
3. Gestión de Mantenimiento Regular
El mantenimiento científico prolonga la vida útil en un 30%-50%:
Mantenimiento diario: Limpiar los residuos de la vía guía; revisar los niveles de aceite hidráulico semanalmente.
Revisión trimestral: Calibrar la precisión del calibrador trasero; inspeccionar la estabilidad de la escala de parrilla.
Revisión anual: Reemplazar los filtros de aceite hidráulico; probar la desviación de par del sistema de sincronización.
Problema de Mantenimiento: Las empresas que se basan únicamente en reparaciones posteriores a fallos alcanzan un <60% de eficacia general del equipo, mientras que los programas de mantenimiento preventivo logran >85%.
4. Adaptabilidad del Entorno Operativo
Los impactos ambientales a menudo se subestiman:
Control de Temperatura/Humedad: Condiciones ideales: 10-35°C, humedad <70%.
Prevención de Polvo: Instale cortinas de aire a presión positiva para reducir la contaminación del gabinete eléctrico.
Estabilidad de la Base: Use plataformas con amortiguadores de vibraciones en entornos de alta vibración para evitar la deformación del marco.
Caso Extremo: Una instalación costera sin tratamiento anti-salpicaduras de sal experimentó una severa corrosión de las tarjetas electrónicas en 3 años.
Señales Clave para la Reemplazo
1. Aumento de los Costos de Mantenimiento
Iniciar análisis de costo-beneficio si los costos anuales de reparación exceden el 30% del valor residual o los costos de una sola reparación mayor superan el 15% del precio del equipo nuevo.
Modelo de Decisión:
Umbral de Reemplazo = (Costo Anual de Mantenimiento + Pérdidas por Tiempo de Inactividad) / Costo Anual de Depreciación del Equipo Nuevo > 1.2
2. Obsolescencia Tecnológica
El equipo heredado enfrenta tres desafíos:
Brecha de Precisión: Modelos mecánicos tradicionales con parada: ±0.1mm repetibilidad frente a modelos CNC: ±0.02mm.
Baja Eficiencia Energética: Las prensas de freno servoeléctricas reducen el consumo de energía en un 40%-60%.
Lagunas en Funcionalidad: Características inteligentes (p. ej., simulación 3D, cambio automático de herramientas) no son alcanzables mediante retrofitting.
Recomendación de Actualización: Priorice el retrofitting CNC para modelos hidráulicos con más de 10 años de antigüedad.
3. Declive Continuo del Rendimiento
Incluya estas métricas en las evaluaciones de salud del equipo:
Desviación del Ángulo de Plegado: Supera la tolerancia por 2 veces durante tres meses consecutivos.
Retraso en la Respuesta Hidráulica: >0.5 segundos desde la orden hasta el movimiento del émbolo.
Error de Sincronización: Desviación del eje Y1/Y2 >0.05mm.
Herramientas de Diagnóstico: Utilice analizadores de vibración y cámaras de imagen térmica para inspecciones en profundidad.
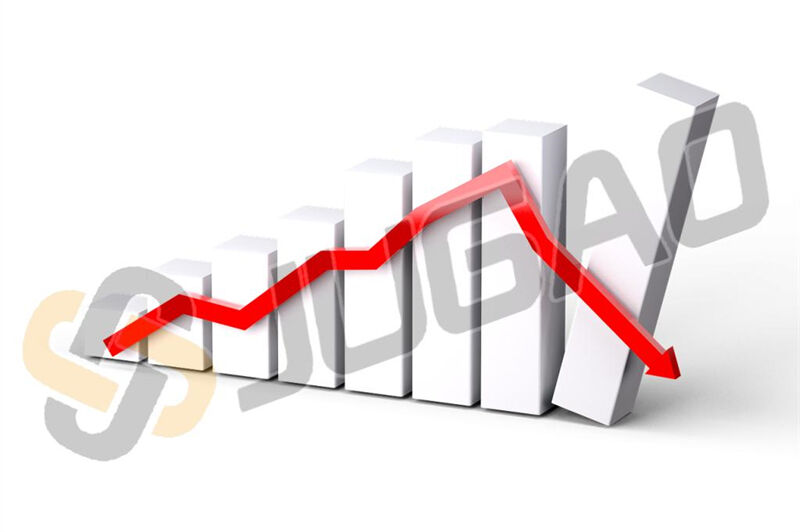
Preguntas Frecuentes
P1: ¿Cuál es el promedio de vida útil de un freno de prensado?
Bajo uso y mantenimiento estandarizados:
Modelos Económicos: 8-12 años
Modelos CNC de Gama Media: 12-18 años
Modelos de Servo de Gama Alta: 15-25 años
P2: ¿Cómo extender la vida útil?
Implementar una estrategia de mantenimiento en tres niveles:
1. Nivel de Operador: Verificaciones de lubricación antes del turno; limpieza del área de trabajo después del turno.
2. Nivel de Técnico: Pruebas mensuales de la curva de presión hidráulica y de aislamiento eléctrico.
3. Nivel Experto: Análisis anual de estrés del marco y actualizaciones de firmware de CNC.
P3: ¿Cuándo debe reemplazarse un freno de prensado?
Iniciar evaluación de reemplazo si:
Componentes críticos (por ejemplo, cilindros principales) se discontinúan sin alternativas.
La eficiencia de procesamiento disminuye un 30% por debajo de los estándares de la industria.
Los sistemas de seguridad no cumplen con los últimos estándares CE/OSHA.
Conclusiones y recomendaciones
La gestión del ciclo de vida de un freno de plegado requiere un sistema de evaluación cuantificado:
1. Mantenga registros de equipos: Registre el historial de mantenimiento, códigos de falla y retrofit.
2. Adopte monitoreo IoT: Seguimiento en tiempo real de la presión, temperatura y vibración.
3. Desarrolle planes de 5 años rodantes: Alinee los tiempos de reemplazo con la planificación de capacidad y tendencias tecnológicas.
Guía de acción: Inspecciones anuales por terceros para generar informes de salud del equipo para decisiones basadas en datos.